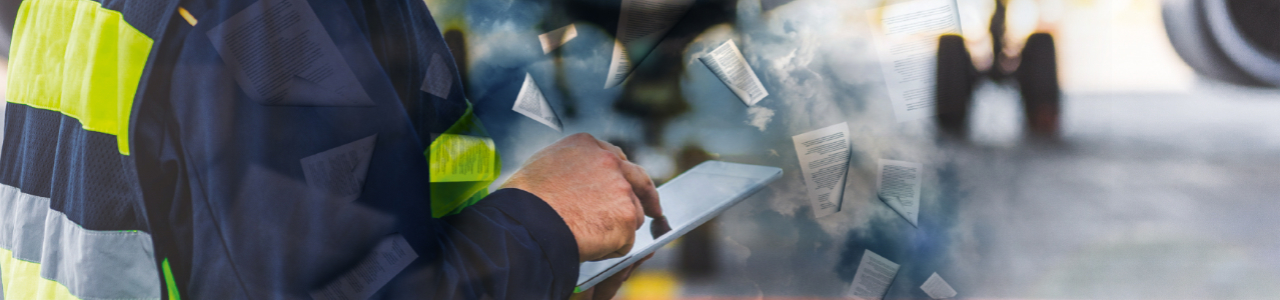
DELTA TO EQUIP 11,000 PILOTS WITH MICROSOFT SURFACE 2 TABLET DEVICES
ATLANTA and REDMOND, Wash., Sept. 30, 2013 /PRNewswire/ — Delta Air Lines (NYSE:DAL) is equipping its 11,000 pilots with the Microsoft Surface 2 tablet, which will be used initially as an electronic flight bag to replace heavy paper-based flight kits containing navigational charts and aircraft operating and reference manuals. Device rollout to pilots flying the Boeing 757 and Boeing 767 fleets will start later this year and all Delta cockpits are projected to be paperless by the end of 2014.
Please click here for a video:
http://origin-qps.onstreammedia.com/origin/multivu_archive/PRNA/ENR/FX-MM88288-20130930-01.mp4
The Surface 2 will run on the Windows RT 8.1 platform and provide flight crews easy access to essential tools and the most up-to-date flight-related resources, including navigational charts, reference documents and checklists while saving the airline $13 million per year in fuel and associated costs.
“Delta’s electronic flight bag running on Surface 2 continues the technological strides Delta has been making to give our crews the best tools to keep them flying safely and efficiently,” said Capt. Steve Dickson, Delta’s senior vice president – Flight Operations. “This intuitive device puts key information at our pilots’ fingertips right when they need it. By eliminating paper, we’ll reduce clutter and minimize time spent looking for flight information, allowing our pilots the opportunity to develop greater situational awareness in the air and on the ground.”
Electronic flight bag to support real-time access to resources
Delta’s electronic flight bag will leverage Jeppesen’s industry-leading FliteDeck Pro application built specifically for the Windows platform. The interactive software gives flight crews quicker and more efficient access to key, real-time information and resources such as dynamic charts and navigation utilities that help them better manage the safe operation of their aircraft.
“Delivering digital flight information through FliteDeck Pro on the Surface tablet platform will increase situational awareness and improve operational efficiency for Delta Air Lines,” said Tim Huegel, director, Jeppesen Aviation Portfolio Management. “This EFB integration program highlights a successful collaboration between Delta, Microsoft and Jeppesen and we congratulate Delta on the digital transformation of their flight deck operations.”
With the Windows RT 8.1 operating system, pilots will be able to open two applications side-by-side, offering, for example, the opportunity to assess weather information alongside proposed flight paths. The Live Tile user interface in Windows 8.1 can feed up-to-the-minute information to crew members while the Surface 2’s true high-resolution 1080p touchscreen display adds detail to maps and other resources.
Delta expects to receive approval from the FAA to use the tablets during all phases of flight next year, a process that follows an extensive period of testing on board Boeing 757 and Boeing 767 aircraft. Approvals for all subsequent fleet types are expected by the end of 2014. The Surface tablets fully integrate handheld technology in the flight deck, streamlining organization of necessary materials and ensuring continuity of information accessed by pilots while giving them the latest tools to drive operational and cost improvements. The reduction of paper in the cockpit also reduces clutter and allows pilots to spend more time focusing on flying the aircraft as they will benefit from an intuitive user interface that features functions to find information faster, without having to hunt for appropriate manuals in flight bags or page through paper documents.
“The integration of the electronic flight bag is part of Delta’s broader move to upgrade flight deck equipment, deploy technology enhancements and take advantage of airspace modernization efforts,” said Dickson. “With these improvements, we’re able to reduce the airline’s environmental impact while providing a great deal of flexibility to continue to add mobile technology solutions into our flying operations.”
Maximizing efficiencies for environmental benefit
Rolling out the Surface 2 tablets across the entire fleet and eliminating paper in the cockpit means the carrier will remove traditional 38-pound pilot flight bags maintained on board aircraft for each pilot. That critical weight reduction is expected to reduce fuel usage by an estimated 1.2 million gallons per year which translates to a 26-million-pound reduction in carbon emissions — the equivalent of taking more than 2,300 passenger cars off the road. Additionally, the tablet will cut the airline’s paper usage by 7.5 million sheets annually and save an estimated 900 trees each year.
In the coming years, Delta plans to expand the functionality of the EFB equipment and increase the efficiency of the operation by providing pilots with electronic dispatch and flight release information, access to real-time weather forecasts, up-to-the-minute operational information and dynamic communication with aircraft technicians on the ground.
“We set out to make Surface the most productive tablet, so we couldn’t be more excited to help Delta pilots be more productive and help the environment,” said Brian Hall, Surface general manager at Microsoft. “This announcement demonstrates Delta’s absolute commitment to bringing the best in technology innovation into their flight operations. The full HD Surface screen and ten-hour battery life will be perfect for flights where Delta pilots will get seamless real-time data and visualization in a variety of lighting conditions. And then they can be productive off the plane with Microsoft Office and our click-in keyboard. We look forward to seeing how Delta amazes us with its Surfaces.”
The move to a paperless cockpit follows Delta’s industry-leading launch of handheld devices for its 19,000 flight attendants that runs on Windows Phone-based software. Delta flight attendants began using the Nokia Lumia 820 in August and are able to access customer and flight information while using Dynamics for Retail technology for easy onboard customer purchases.
About Microsoft
Founded in 1975, Microsoft (Nasdaq “MSFT”) is the worldwide leader in software, services and solutions that help people and businesses realize their full potential.
More information about how organizations are turning to Microsoft technology is available on the Microsoft Customer Spotlight newsroom.
About Delta
Delta Air Lines serves more than 160 million customers each year. Delta was named by Fortune magazine as the most admired airline worldwide in its 2013 World’s Most Admired Companies airline industry list, topping the list for the second time in three years. With an industry-leading global network, Delta and theDelta Connection carriers offer service to 317 destinations in 57 countries on six continents. Headquartered inAtlanta, Delta employs nearly 80,000 employees worldwide and operates a mainline fleet of more than 700 aircraft. The airline is a founding member of the SkyTeam global alliance and participates in the industry’s leading trans-Atlantic joint venture with Air France-KLM and Alitalia. Including its worldwide alliance partners, Delta offers customers more than 15,000 daily flights, with hubs in Amsterdam, Atlanta, Cincinnati,Detroit, Minneapolis-St. Paul, New York-LaGuardia, New York-JFK, Paris-Charles de Gaulle, Salt Lake City and Tokyo-Narita. Delta is investing more than $3 billion in airport facilities and global products, services and technology to enhance the customer experience in the air and on the ground. Additional information is available on delta.com, Twitter @Delta, Google.com/+Delta and Facebook.com/delta.
Cathay Pacific Airways selects ULTRAMAIN efbTechLogs for industry-first cross-fleet ELB Implementation
Hong Kong-based, Cathay Pacific Airways, has begun an implementation of efbTechLogs™ Electronic Logbook (ELB) software developed by Ultramain Systems. ELB software is new technology that replaces the long-standing paper-based aircraft technical log. Cathay Pacific will implement the Ultramain ELB on its Class 3 Electronic Flight Bag (EFB) installation to a common standard across all its aircraft types comprising 170 aircraft. The ELB software operates on Electronic Flight Bag hardware, which itself constitutes new technology, and is classified by aviation authorities from least to most integrated with the aircraft: Class 1, 2, or 3 EFB respectively.
“The majority of airlines are still using paper-based aircraft technical logs, so the use of ELB software is in its infancy,” says Tim Spears, Vice President of Ultramain and head of Ultramain’s Onboard Systems division. “When you look at airlines actually operating Electronic Logbooks, the majority are flying with efbTechLogsprovided by Ultramain Systems. Cathay Pacific Airways is set to be the first industry operator with a common Electronic Logbook across all fleet types.”
“Replacement of paper with the real-time capture of structured maintenance information through an Electronic Logbook will dramatically improve the efficiency of processes in Line Maintenance operations,” says Rob Saunders, Cathay’s Head of Engineering Cost Management and Business Improvement. “Working closely with HAECO, our MRO partner, we have looked much further than just replacing the paper. To realize the benefits, we needed a proven ELB solution integrated with our M&E system.
Mark McCausland, President of Ultramain Systems, says, “efbTechLogs operates on Class 1 (mobile devices), as well as Class 2 and 3 EFB, and has been in continuous approved use on Class 3 EFB since 2008.efbTechLogs has a great deal of experience incorporated into the software and has been installed by more operators than all other ELB offerings combined.” McCausland said, “No other ELB has the cross-fleet and cross-manufacturer capabilities that efbTechLogs has.”
Christopher Gibbs, Director of Engineering for Cathay Pacific, said, “Similar ELB software that spans all of our fleet types is essential in managing an e-enabled fleet. Commonality of software makes sense on many levels, from training to ground systems integration. e-Operations can provide incremental benefits for individual aircraft, but we see a significantly stronger business case for full fleet enablement.
ARCONICS DELIVERS 787 EFB DOCUMENT MANAGEMENT FOR THOMSON AIRWAYS
Thomson Airways is the world’s largest leisure airline, offering flights from the UK and Ireland to destinations across Europe, Africa, Asia and the Americas. Thomson Airways became the first UK airline to take delivery of the Boeing 787, receiving the first aircraft in May 2013. They turned to Arconics to help them manage the documentation for the new fleet.
The Challenge
In addition to the new Class 3’s on the B787, Thomson Airways uses a range of Class 1 and 2 EFBs on other fleets. Producing manuals that can be viewed easily and reliably across devices is difficult and time-consuming. Thomson Airways was using an authoring system based on a standard XML editor. The system had serious problems including a high training requirement, an internal IT burden caused by locally installed editing software and recurring problems with overall reliability.
The impending arrival of the new B787 fleet led to a search for a new authoring and distribution system. Phil Ganewski, Manager of Flight Support, led a comprehensive evaluation of 8 different vendors across a wide range of functional and business categories. The evaluation was comprehensive, with particular attention paid to:
- Authoring
- Workflows, groups, and user management
- Security and Auditing
- Publishing outputs – HTML, PDF, XML, Class 1, 2 & 3.
- Importing and editing Boeing FTID
- Overall architecture
- Availability of EFB software
- Training, ease of use, and vendor support
According to Phil “We needed a solution that was completely web-based. We have busy people across the organization including Fleet Managers, Technical Pilots and Subject Matter Experts who update the manuals, but authoring is not their main job. By definition, authoring is done when the time is available. They can go for months without using the system, so ease-of-use was a major concern. We did a comprehensive due diligence exercise and the Arconics AeroDocs system had green ticks across the board.”
The Solution
Arconics worked closely with Thomson Airways to define the requirements for a customized solution that would meet Thomson’s needs for authoring and delivery to Class 1, 2 and 3 EFBs, including the EDB on the Boeing Class 3 EFB on the 787 fleet.
The deployment was not without challenges. The Class 1 EFBs were tightly locked down, which required some additional work to roll out the system. The authors had to be trained on the new Arconics authoring system, which took about half a day, supplemented by some remote support as they began working with the system.
“We had some unique requirements, but Arconics gave us the help and support we needed. Sometimes they had a solution figured out before we had finished describing the problem. It was also very helpful that the software was so easy to use. There was nothing that could have been done better during the implementation” said Phil.
The Outcome
AeroDocs was deployed in time to support the B787’s first flight. Now over 40 people across Thomson are using AeroDocs to edit Boeing and Thomson Airways manuals including FCOM, MEL, and Ops Manual Parts A, B and D, and other flight ops manuals and handbooks. Overall document publishing coordination and administration of the system is handled by a single employee.
The system is helping Thomson Airways meet its goal of a paperless cockpit, which will generate savings of several hundred thousand pounds per year.
More significantly, using AeroDocs has helped standardize manuals and the revision process across the organisation. The AeroDocs manual viewer delivers a better user experience for the pilots, who can now navigate and search the manuals more easily, improving safety. The UK Civil Aviation Authority are also connected to the AeroDocs system, allowing them to review and approve changes online.
Thomson Airways is now enabling AeroDocs across all their fleets and all devices, including Class 1 and 2 EFBs on the 737, 757 and 767 fleets, and to pilots’ own devices and laptops.
Phil concluded “I’ve worked with a lot of companies, but few are as good as Arconics. The team are highly knowledgeable, the work gets done, and if there’s a problem, I know I’ll get the support I need.”
For more information about Arconics please go to www.arconics.com or email info@arconics.com.
Norwegian Air Shuttle selects future-proof tablet based EFB solution from Scandinavian Avionics.
Billund, Denmark, 25. September 2013: The SA Group headquarters, Scandinavian Avionics has signed an agreement with Norwegian Air Shuttle to replace the existing Electronic Flight Bag solution in their fleet of Boeing 737 aircraft with the new future-proof tablet based solution from Scandinavian Avionics.
Only a few months ago, Scandinavian Avionics announced its launch project for their proprietary new tablet based EFB solution. Today, the Norwegian airline, Norwegian Air Shuttle has signed a contract to equip their entire fleet of Boeing 737 aircraft with the new flexible and cost-effective tablet based EFB solution. Scandinavian Avionics will provide all equipment, certification package (EASA STC) and installation support for the project.
The solution consists of 2 ruggedized 10.1” Panasonic tablets, Scandinavian Avionics’ Data Integration Center (DIC-600) for aircraft interface and server capability and a separate communication module (ERC-400) that eases the certification process and future-proofs the operator’s future communication demands. Both the interface unit and the communication module have been designed and certified in-house by Scandinavian Avionics.
The solution stands out in the market because it redefines the traditional EFB architectural concept by moving focus from the actual EFB display in the cockpit to the flexible infrastructure in the aircraft.
Michael R. Truelsen, President at Scandinavian Avionics, explains:
“As opposed to other EFB solutions with expensive hardware and high certification costs, we have developed a future-proof concept that enables the aircraft operator to use a commercial windows based tablet as the EFB display. The development within commercial tablets is running way faster than the traditional EFB hardware and with our solution the operator can continuously upgrade the EFB display to the most current model at low certification costs.”
John-Christian Paulshus, Head of Business Development Operational It Solutions at Norwegian Air Shuttle says:
“We prefer not to invest in proprietary EFB solutions; but to invest in more open infrastructure that will support today’s and future EFB devices. We strongly believe in rather short-cycled devices in cockpit while maintaining a flexible infrastructure in the avionics compartment for many years. We have been looking for a replacement EFB solution that will provide Norwegian with the best price performance available – in line with our overall business concept with modern equipment – and we have now found the solution for the future.”
An electronic flight bag solution benefits any airline or aircraft operator by reducing weight on board and by saving time on updating the physical charts in the flight bag as well as gaining operational benefits with connectivity.
Ole-Christian Melhus, Deputy Director Flight Operations at Norwegian Air Shuttle comments:
“As an experienced paperless operator, we are confident that the flexibility achieved by the new hardware solution provided by Scandinavian Avionics, will exceed the operational benefits targeted for effectiveness and operational control. Aircraft connectivity together with existing and future infrastructure flexibility, are key elements in the selected solution. Streamlining our operation in all aspects are important in our daily processes, both today and for our continuous expansion, we stand confident that this will be a solution and investment for the long term future.”
Michael R. Truelsen concludes:
“We believe strongly in our EFB concept, and the fact that airlines are now starting to change course and exchange traditional EFB systems with new future-proof solutions as ours, is a sign that we are on the right track.”
The initial certification and installation has been accomplished for new delivery aircraft and retrofits are currently proceeding according to Norwegian Air Shuttle’s high paced plan for the current Boeing 737 fleet.
****
Scandinavian Avionics A/S – Member of The SA Group
Scandinavian Avionics A/S is the headquarters of The SA Group – an experienced avionics organization with divisions in Sweden, Norway, Greece, Malaysia, Bahrain and India and a customer base geographically spread over all of Europe, Africa, CIS and the Middle- and Far East.
Based on a number of relevant approvals, Scandinavian Avionics – The SA Group provides complete turn-key avionics solutions, including avionics logistics and parts support, maintenance (MRO), certification, design & engineering, installation, product development, training and consultancy services with the primary business platforms being larger helicopters, corporate aircraft, regional airliners and defense electronics.
Since the founding in 1978, core values like quality, reliability and flexibility have been deeply rooted in the organization and are the main causes for the excellent reputation among aircraft operators around the world today.
For more information please visit www.scanav.com
Norwegian Air Shuttle (Norwegian)
Norwegian Air Shuttle ASA, commercially branded “Norwegian”, is a public low-cost airline noted on the Oslo Stock Exchange.
The company is the second largest airline in Scandinavia and the third largest low-cost airline in Europe. It has a route portfolio that stretches across Europe into North Africa and the Middle East, as well as Thailand and the US. With competitive prices and customer friendly solutions and service, the company has experienced significant growth in recent years. 17.7 million passengers flew with the airline in 2012. Norwegian operates 382 routes to 121 destinations and has approximately 2,500 employees.
For more information please visit www.norwegian.com
navAero receives STC for Class 2 Tablet EFB System on Q400
SUNDSVALL, SWEDEN, September 25, 2013 — navAero announces the achievement of FAA Supplemental Type Certification (FAA STC ST03170NY) on the Bombardier DHC-8-400 Series for the installation of a Class 2 Tablet Electronic Flight Bag provisions for the navAero Tablet EFB System that includes the navAero Universal Aircraft Interface Device (UAID). Provisions include pilot/first officer cockpit mounts that feature electrical connectivity for device charging and data connectivity.
The navAero Tablet EFB System consists of a modular, proprietary designed “Smart” Mount tablet holder that securely contains that tablet device and meets all appropriate DO-160 requirements. The holder is integrally equipped with the navAero Power/Data Interface (PDi) module that converts 28VDC aircraft power to that which is appropriate for charging the tablet device. The PDi module also feeds aircraft data (ARINC 429, 717, Discretes) from the navAero Universal Aircraft Interface Device (UAID) to the tablet for use in various software applications along with capability for WiFi and cellular connectivity. The UAID also provides built-in capabilities for QAR functionality.
The STC was executed by navAero in cooperation with Delta Engineering and DECA Aviation Engineering Limited for navAero customer, WestJet Encore. The navAero EFB system uses an architecture that consists of dual cross-connected tablet devices with Ethernet connectivity to the navAero UAID. It allows for multiple variations of tablets to be hosted to achieve maximum flexibility and upgradeability. As deployed, the system achieves WestJet Encore goal for the deployment of their Integrated Communications and Application System (ICAS).
Simone Giordano, navAero Executive Vice President Sales and Marketing, stated: “This achievement shows that our Class 2 Tablet EFB System meets all the regulatory requirements to be a highly integrated part of a modern airline, providing end-to-end connectivity from aircraft to operations. navAero has taken this design approach for tablet EFB deployments and has commercialized derivations to accommodate iPad devices as well as various types of Windows/Andriod-OS tablet devices.”
Giordano continued, “navAero has always been on the leading edge of providing customer-focused EFB solutions. As a product line extension to our widely accepted and deployed aircraft-dedicated Class 2 tBag™C22 Electronic Flight Bag System, our Tablet EFB System provides a certified platform for airline operators who desire a mounted, powered and ‘data connected’ tablet solution for their fleets. Whether they are aircraft-dedicated systems or tablet-based deployments, we have certifications and hardware solutions that allow customers to achieve their program objectives.”
Aircraft installations for WestJet Encore are currently in-progress. Installation kits for the Bombardier Q400 are available for immediate delivery.
About navAero
navAero, Inc. is the world leader in developing and commercializing cost effective electronic flight bag products. Currently navAero offers FAA & EASA STC installations on the following aircraft series: Airbus A300/310, A318/319/320/321, A330, A340, B727, B737, B747, B757, B767, MD82/83/87, ERJ-135, E-170, BAe-146 / Avro-RJ70/85/100, CL601/604, DHC-8-402. For further information, visit the navAero website at www.navAero.com.
About DECA
DECA is Canada’s premier aviation services provider with a foundation built on the diversity of their capabilities, platform experience, programs, customers and the experience of their people. For further information, visit the DECA Aviation Engineering Limited website at www.deca-aviation.com.
About Delta Engineering
Delta Engineering has provided the aviation industry with certification, engineering and manufacturing services for nearly 15 years. Delta Engineering holds a FAA Repair Stations (Part 145), Organization Delegation Authorization (ODA), Production Certification (PC), Part Manufacturing Authorization (PMA) and Minor Change Approval authorization. Their ODA include ODA-STC, ODA-PC and ODA-PMA with inspection and engineering unit member. For further information, visit the Delta Engineering website at www.delta-engineering.com.
Press Contact:
Simone Giordano
navAero, Ab
+46 60 66 41 00
simone.giordano@navaero.com
Lufthansa Targets Operational Efficiency With New EFB Tool
Lufthansa Targets Operational Efficiency With New EFB Tool
Carrier to explore cost savings potential of on-board flight profile optimization with software by specialist provider PACE
BERLIN, 25 September 2013 – Lufthansa is the launch customer for a new EFB tool which will help pilots actively manage the operational efficiency of their flights. The software will use live aircraft and weather data to determine in real time the most cost-efficient flight trajectory for the remaining route to destination. Making full use of the EFB’s computational power and of high-fidelity performance data, the software is set to achieve significantly more accurate results than current on-board technology.
With the most cost-efficient, or ECON, trajectory as a reference, the software is able to pinpoint the available cost savings potential for every instant of the flight and display it to pilots in easy-to-read charts, giving concise information about fuel burn, overall cost and delay; the latter provides additional support for managing on-time performance.
The Pacelab Flight Profile Optimizer is currently being developed by Berlin-based software provider PACE, who specializes in operational efficiency management solutions for airlines. In fact, the present collaboration with Lufthansa follows the successful implementation of a similar project with the carrier’s regional subsidiary Lufthansa CityLine.
A first prototype of the software is planned for late 2013; initially, it will be deployed on Class 2 EFBs on the carrier’s intercontinental fleet for a large-scale evaluation, to become part of the standard installation if the savings projected in a preliminary study are realized.
“In Lufthansa, we have found the perfect launch customer for the Pacelab Flight Profile Optimizer,” says Dr. Oliver Kranz, PACE Managing Partner and head of the company’s airline division. “Lufthansa is a recognized innovation leader, and we are very fortunate to be able to draw on their vast operational know-how in the development of our software.”
NOTE TO EDITORS
About PACE Aerospace Engineering and Information Technology GmbH
PACE, with offices in Germany and the US, develops and distributes intelligent software solutions for aircraft and engine manufacturers, airlines, MRO providers and leasing companies supporting the entire life-cycle of the aircraft, from marketing and design to customization and flight operations.
Major areas of application are conceptual aircraft and aircraft systems design, cabin configuration, performance analysis and the management of fuel and operational efficiency in flight operations.
Customers include Airbus, Air Berlin, ASDL, Boeing, Bombardier, COMAC, Embraer, Emirates, Etihad, Eurocopter, Eurowings, GE Aviation, Irkut, Lufthansa CityLine, MDA, Rolls-Royce, Superjet International, Sukhoi and Swiss International Air Lines.
More information about PACE is available online at www.pace.de.
Contact:
PACE
Aerospace Engineering & Information Technology GmbH
Rotherstr. 20
10245 Berlin
Press department
Anja Kittner
+ 49 30 293 62 412
press@pacelab.com
www.pacelab.com
Aloha Air Cargo chooses TRAX!
Trax is proud to announce the newest addition to the family. Aloha Air Cargo has chosen to sign with Trax and move forward with the best MRO ERP Software available.
Trax software will help Aloha Air Cargo with their daily ground, flight, and maintenance operations across numerous locations within Hawaii, and as they expand to the West Coast. Trax MRO ERP software will ensure their maintenance and engineering work and records are kept in impeccable shape. This will help Aloha develop further efficiencies to organize purchasing, inventory control and procurement, and project management among IT functions within the company, providing much needed scalability as they grow in the coming years.
Jose Almeida, President and CEO of TRAX USA Corp., states, “We are excited to be part of the growth of Aloha Air Cargo, and it is with great excitement that we welcome them to the TRAX Family.”
Aloha Air Cargo will be implementing X1, the latest version of TRAX Maintenance. This version includes over 20 modules to cater to virtually every aspect of aircraft maintenance. TRAX Maintenance will be able to assist Aloha Air Cargo in various ways – from Material Management and Finance to Technical Records and Reliability, Aloha Air Cargo will now have aircraft, inventory, and maintenance activity information integrated into a single system.
About Aloha Air Cargo
Headquartered in Honolulu, Aloha Air Cargo delivers fast, economical and reliable transport of goods between the Hawaiian Islands of Oahu, Maui, Kauai and the Island of Hawaii. It became an independent cargo operator after the closure of Aloha Airlines passenger services in May 2008. Aloha Tech Ops is a division of Aloha Air Cargo and provides maintenance and engineering services to airlines in the State of Hawaii.
Aloha Air Cargo is owned by Seattle-based Saltchuk, which has been doing business in Hawaii since 2000 when it acquired Young Brothers/Hawaiian Tug & Barge. Committed to the welfare of Hawaii and strengthening the local economy, the company also acquired Hawaii Fuel Network, Maui Petroleum and Minit Stop Stores in 2006. For more information on Aloha Air Cargo please call toll free 888-94-ALOHA (25642), or visit www.AlohaAirCargo.com.
About TRAX
TRAX USA Corp., with offices in the United States, Japan and United Kingdom, is the number one seller of aircraft maintenance software globally. TRAX Maintenance solution has been developed – with Airlines and for Airlines – to provide the most comprehensive and advanced MRO ERP software solution available today. For more information about TRAX, please visit www.trax.aero
For further information about TRAX Maintenance or media related inquiries call +1.305.662.7400 or e-mail sales@trax.aero
Boeing Launches New Maintenance Apps for iPad
LONDON, Sept. 24, 2013 /PRNewswire/ — Boeing [NYSE: BA] has made performing routine maintenance and diagnosing aircraft issues faster and easier for airline technicians with a suite of new mobile applications for iPad. With the apps, technicians will have immediate access to manuals, part numbers and other critical information to resolve maintenance issues plane-side and collaborate with co-workers located elsewhere. As a result, airlines can enhance real-time regulatory compliance, reduce flight delays and reduce operational costs.
Boeing worked with several airlines for more than a year on the prototype, incorporating their input to optimize the user interface and maximize utility for line mechanics. Technicians will have instant access to critical information, including the maintenance history of an aircraft, when they need it most. The application suite includes Toolbox Mobile Library, Toolbox Mobile Parts and Maintenance Turn Time.
“Mobile technology is an important aspect of our digital airline strategy, which is to harness the power of information, technology and analytics to create insights that give our customers the Boeing Edge: a competitive advantage in the marketplace,” said John Maggiore, director of Fleet and Maintenance Solutions, Boeing Digital Aviation. “Data-driven optimization across flight operations, airspace and maintenance operations is saving aircraft operators millions of dollars in operating costs today. This is an exciting new chapter of that journey.”
Features of the new maintenance apps include:
- A Toolbox Mobile Library, which will provide technicians access to maintenance documents for instant reference and use, wherever and whenever needed.
- Hyperlinks between multiple manuals and airline-created content that will expedite access to critical documents so that users can easily search for documents and information about parts and fault histories.
- A Toolbox Mobile Parts app which enables technicians to instantly retrieve information about part availability, including the airline’s most current inventory information.
- Maintenance Turn Time, which gives technicians a secure connection to collaborate with their colleagues when troubleshooting a maintenance issue. A technician can take a photo of a damaged part, upload it for others to see and annotate and then share information about maintenance issues with their peers in real time. Maintenance Turn Time is available for the iPad, iPhone and a web browser.
- The ability to update reference manuals with one tap on the iPad screen. Alaska Airlines technicians estimate that using the apps on a 0.69-pound iPad mini to access critical information will save 4,000 pieces of paper a day.
“We are very excited about the launch of these new products,” said Maggiore. “They are a great addition to the Boeing portfolio and will deliver even more value to our customers when used in conjunction with capabilities such as Electronic Logbook, Airplane Health Management and Maintenance Performance Toolbox.”
About the Boeing Edge
Boeing offers a comprehensive portfolio of commercial aviation services, collectively known as the Boeing Edge, bringing value and advantages to customers and the industry. Boeing Digital Aviation is the business unit that delivers the Boeing Edge through integrated offerings in software, applications, information solutions and advanced training to drive optimized performance, efficiency and safety across customer operations. Boeing provides a competitive edge by solving real operational problems, enabling better decisions, maximizing efficiency and improving environmental performance — creating intelligent information solutions across the aviation ecosystem.
Contact:
Elizabeth Holleman
Digital Aviation Communications
(206) 601-1217
elizabeth.a.holleman@boeing.com
Photos and caption are available here: http://boeing.mediaroom.com
SOURCE Boeing
euroAtlantic Airways EFB solution extends to full Boeing fleet
euroAtlantic Airways EFB solution extends to full Boeing fleet
Portuguese airline continues successful use of Navtech iCharts
September 24, 2013 (TORONTO) – Navtech Inc., a leader in flight operations software and services, is pleased to congratulate customer, euroAtlantic Airways, for their extended Class 2 Type B EFB approval from EASA (European Aviation Safety Agency). This is one of the first EASA certifications for an airline operating an all Boeing aircraft fleet and utilizing Apple iPad hardware. The non-scheduled international airline, operating in diverse routes in the US, Canada, Caribbean, Central and South Americas, Africa, Middle East and beyond, will operate Navtech iCharts via iPads across their entire fleet. euroAtlantic Airways is also a subscriber to Navtech’s Navigation Data for the GE US and Honeywell FMS.
“We are always pleased to be a part of innovative technology solutions that give our customers cost savings, enhanced safety and overall increased operational efficiency,” said Mr. Heath Bowden, Product Director – Charts & EFB at Navtech. “euroAtlantic has had great success in removing paper from their cockpits.”
euroAtlantic Airways was a new customer to Navtech in 2012, signing two agreements for services within six months and becoming an ally for Navtech. “We have a very good, professional relationship with Navtech and we are happy to help bring them more attention through our story,” said euroAtlantic Airways Chief Pilot, Mario Alvim. “We are very pleased with our Navtech solution.”
Navtech iCharts is an application that brings Navtech electronic charts to your iPad. This allows the iPad to be used as a Class 1 EFB, or with regulatory and operational approval, as a Class 2 Type B device. Navtech has worked with customers, like euroAtlantic Airways, to achieve operational approval of the iPad as a Class 2 device. Navtech’s family of state-of-the-art aeronautical charts products have been developed using research from Human Factor Specialists and by gathering data from, and working closely with pilots who have years of experience using aeronautical charts. Each chart includes enhanced symbology and communication features. Navtech’s electronic chart viewing application, Navtech eCharts, has been used by Navtech’s customers for over ten years. Continued product enhancements will form the infrastructure for Navtech to easily support all Classes of EFB and all devices from tablets to installed avionics.
For more information, visit www.navtech.aero.
About Navtech, Inc.
Navtech, Inc. is a leading global provider of flight operations solutions, serving more than 350 airlines and aviation services customers. Navtech’s product suite includes aeronautical charts, navigation data solutions, flight planning, aircraft performance software (take-off/landing, weight and balance), and crew planning solutions. Many of Navtech’s products can be configured as part of an EFB solution, including take-off data calculation, weight and balance, and aeronautical charts. These products, supported by Navtech’s ISO: 9001 certification, directly support millions of flights each year and help Navtech customers maximize efficiency, reduce costs, ensure compliance with complex national and international safety regulations, and effectively deliver their services.
Navtech is an international company with offices just outside of Toronto in Waterloo, Ontario – Canada’s Technology Center – and in Stockholm, London, and Ahmedabad, India, and is further supported by satellite offices around the world. Its home on the web www.navtech.aero is the first and only site for viewing the Navtech Aviation Poster Collection, a collection of hundreds of posters and other ephemera that capture the history of aviation through the arresting graphic design of the day.
About euroAtlantic Airways
euroAtlantic was founded by Tomaz Metello, CEO and major shareholder, and is also partially owned by the largest Portuguese leisure corporation, Pestana Hotels & Resorts. euroAtlantic airways is a Portuguese registered non-scheduled International Airline, operating in the most diverse routes in North Atlantic (USA and Canada), Caribbean, Central and South Americas, Africa, Middle East, Pacific, Australia and Oceania.
Founded as Air Zarco on 25th August, 1993, the company first adopted the trade name Air Madeira until 17th May, 2000, date when the memorandum of association was altered by deed, and the current name of euroAtlantic airways – transportes aéreos s.a. was adopted. Since the outset of its operation, euroAtlantic guarantees insurance cover with Leader insure Catlin France. euroAtlantic is FAA (FAR129) and EASA certified, euroAtlantic is registered as an IOSA Operator under the IATA Operational Safety Audit Program. Our maintenance organization is approved under EASA Part 145 to perform line maintenance on B757, B737, B767 & B777 airplanes (Certificate of approval) and our CAMO has Sub Part I privileges to B737NG, B767 and B777 aircraft types (Certificate of approval – part M).
euroAtlantic Airways Class 2 Type B iPad EFB solution showing Navtech iCharts
Vanilla Air goes for AMOS
Vanilla Air, previously called AirAsia Japan, is a Japanese low cost carrier, operating from Narita Airport in Tokyo. The airline is wholly owned by ANA.
Swiss-AS is very pleased to announce that Vanilla Air has again decided in favour of AMOS and will, although being separated from the AirAsia Group, continue to manage its maintenance with AMOS.