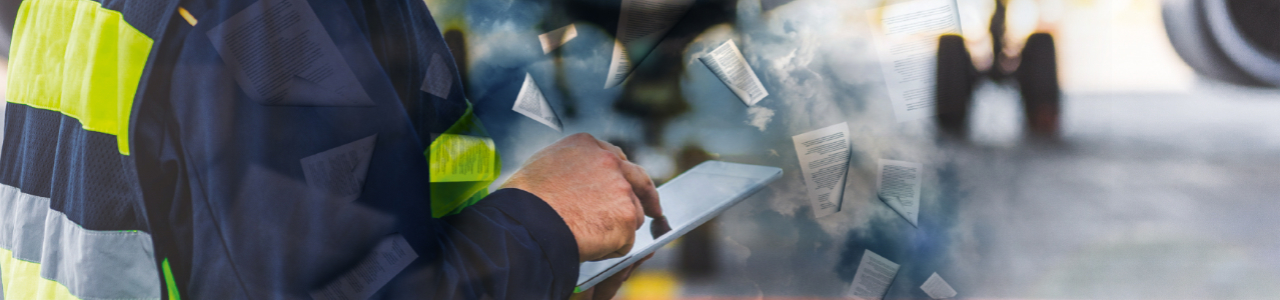
Copa Airlines “Goes Live” with IDMR Solutions InForm
Copa Airlines “Goes Live” with IDMR Solutions InForm
Leading Latin American commercial airline, Copa Airlines, has implemented IDMR Solutions’ Software for the edition, revision and distribution of its company-wide manuals.
IDMR, a New York based software company, is a global leader in technical documentation management solutions (DMS) designed exclusively for fleet operators, MRO providers and OEM organizations. Its integrated suite of applications has proven success in increasing operational performance and decreasing operational cost while insuring airworthiness, safety and regulatory compliance at multiple airlines.
Copa Airlines completed IDMR’s InForm implementation on schedule and went live on September 1st 2016. The carrier deployed an integrated suite of applications managing its manuals shifting to a 100% digital and paperless solutions.
“IDMR is a valued partner to our business,” said Itzy Valdes, Centralized Manuals Manager at Copa. “A pioneer in the industry, IDMR, helps to ensure that our technology investment evolves with our business.”
COPA implemented IDMR’s PDE, an enterprise content management solution. Keeping track of its versioning, harmonizing its manuals edition, and facilitating Authority’s reviews, COPA is using cutting-edge technologies to materialize its digital and mobile revolution. Being fully integrated in Copa’s IT, IDMR InLib solution allows employees with their single corporate logon to access documentation anytime, anywhere, from any type of terminal (desktop, tablet, phone) on any type of operating system.
IDMR’s comprehensive and integrated solution (from the edition to the approval workflow through the required revision cycles, from the distribution to the mobile access) is highly adaptable and drastically improved productivity assuring respect of deadline and facilitating collaboration between authorities and the air carrier.
“Copa is a valued customer and we appreciate the opportunity to support the company as it continues its growth path and fly passengers in very dynamic markets,” said Israel Revivo, CEO/President, IDMR Solutions. “IDMR is committed to continuing to provide airlines with the latest solutions to enable them going paperless, with the delivery of custom-built solutions that are highly scalable, adaptable and can easily integrate with other enterprise applications. By putting in place the next-generation solutions, Copa captures the best practices and functionality inherent to these applications while benefiting from our past and ongoing experience as well as important investment in research and development”, added IDMR’s CEO.
SpiceJet takes off with AMOS
SpiceJet takes off with AMOS
At a glance
– Expansion of the AMOS footprint in India
– Efficient ramp up for a swift start to the project
– 600 new AMOS users
– Impressive fleet increase plans
Swiss-AS welcomes another low cost carrier
Swiss-AS today announced a new business relationship with SpiceJet, one of India’s leading low cost airlines, regarding the Swiss Aircraft Maintenance & Engineering System AMOS. AMOS will be rolled out and used by over 600 employees in the Technical department of the airline. Some members of the SpiceJet technical department staff are already familiar with AMOS, which helped the airline not only during the evaluation phase, but will also be beneficial in the future implementation process.
“India has become a strategic market for us and, with SpiceJet on board, we are proud to continue this Indian story of success,” stated Ronald Schaeuffele, CEO of Swiss-AS.
AMOS will support the SpiceJet growth strategy
SpiceJet is excited to start the AMOS project and the airline foresees a short implementation period to benefit from best practice processes with the introduction of this software. The underlying strategy to introduce AMOS aligns perfectly with the expected fleet growth at SpiceJet to support efficiency gains and improved cost control measures. SpiceJet will double the current fleet with the 55 B737 MAX aircraft on order. For the carrier, implementing a new MRO software during this challenging phase will bring efficiency benefits and allow the existing and new aircraft to be directly monitored and maintained in AMOS. Experience has proven, via the numerous low cost carriers already members of the AMOS customer community, that expansive fleet growth projects have been successfully and economically managed using optimized fleet management processes.
Aero One® 4.8 : Advanced employees and tools management
Aero One® 4.8 : Advanced employees and tools management
The Aero One 4.8 release includes some major changes in the execution module. Management of resources has been largely improved as well as tools management. Discover below what’s on the agenda !
We are very proud and pleased to release the 4.8 version of Aero One® with quite major improvements to facilitate and optimize your maintenance execution.
First, we have added a bunch of features to manage effectively human resources affected to work orders. It starts with enhanced layouts of the work order and task list : you can now directly access to relevant logistic information through a ‘Details’ tab. This includes required qualifications for maintenance operations through ‘Qualification’ sub tab. Easy and straightforward.
Also, Aero One® is getting one step further with employee assignment and qualification controls : These features ensure that you indeed have the staff for the job, but also, the qualified one. You really just have to follow Aero One®’s warnings !
Of course, we have worked hard to make these features as intuitive as possible with a layout that shouldn’t bother your habits ! It is most likely that you will be able to use those features without referring to the ‘How-To’…
Besides, it’s easy to edit and print the list of operations assigned to your employees, Aero One® will filter automatically work by employee !
Second major improvement, is the ability to manage tools with different levels of administration depending on your requirements: from simple tools to complex tools that are tracked in your stocks, you will get all the necessary to have an efficient combination between tasks, human resources, spares and tools.
Basically, tools can be assigned to task list in order to plan availabilities, and when task lists are added to work orders, Aero One® will automatically display availabilities of the tools : A tools status cockpit makes it really straightforward. Just open the tools status transaction, and read the lights !
Of course, you can define required tools for any work order under going, the ‘tools’ tab is easy to use and allows correlating a tool to an operation.
Assigning/issuing a tool for a specific work order / operation can be done easily through the logistic cockpit, as you would do for any parts to issue for maintenance.
Traceability and efficiency are on the program !
Finally, we also added other nice touches to this release, download and have a look our 4.8 Release Note to see what’s new !
As per the Aero One®’s team work in progress, we should deliver a new release (4.9) somewhere in Q1 2017 with, among other features, penalties management for aircraft and equipment counters. Stay tuned.
Marshall Aerospace signs new OASES contract with Commsoft and opts for Private Cloud service
Marshall Aerospace signs new OASES contract with Commsoft and opts for Private Cloud service
16th December 2016
A world leader in aviation engineering and maintenance software, Commsoft is delighted to announce that Marshall of Cambridge Aerospace Limited, part of the Marshall Aerospace and Defence Group, has signed a new, extended contract to use the industry-leading OASES product for its growing CAMO activities.
An OASES user since 2008, Marshall plans to use the OASES system to support an on-going CAMO operation in the Middle East.
Marshall is working hard to secure further CAMO contracts and sees a potential for OASES to be used in support of these programmes.
A ‘best-of-breed’ MRO IT system, OASES offers an industry-leading technical sophistication whilst being intuitively user-friendly. To allow for scalability, OASES is structured in a modular format and, for this new contract, Marshall has selected the Core, Airworthiness and Planning modules.
OASES can either be installed on a local server or accessed via the internet through Commsoft’s Private Cloud hosting service, avoiding the need to install any additional hardware. As part of its new contract, Marshall has migrated to the new cloud environment.
Nick Godwin, Commsoft Managing Director, commented: “It is always gratifying when a long-standing client opts to renew its contract and continue as part of the worldwide community of OASES users. So we’re particularly pleased that a member company of the UK’s largest independent aerospace and defence group has demonstrated its continuing support of the system. It’s a further validation of the technological, operational and commercial benefits that OASES can deliver.”
Designed by software engineers who understand aviation maintenance and operations, OASES is continually being developed – with the active participation of its users – to ensure it remains fully up-to-date with technological progress and fully responsive to the ever evolving needs of both airlines and MROs.
Over 110 aviation organisations in no less than 45 different countries are supported by Commsoft’s OASES, including national carriers, 3rd party maintainers, regional carriers, leasing companies, cargo specialists, charter operators and specialist rotable stockists across the USA, Europe, the Middle East, Asia, Africa and Australasia.
DAC International and Esterline Avionics Systems Extend Their Distribution Agreement
DAC International and Esterline Avionics Systems Extend Their Distribution Agreement
AUSTIN, Texas, December 15, 2016
DAC INTERNATIONAL INC. (DAC), a subsidiary of Aero Precision Holdings LP, announced today that it has extended their agreement for the distribution of the Esterline CMA-6800 Display. Esterline Avionics Systems is a major supplier of cockpit avionics systems and advanced displays to the aerospace market, including airframe manufacturers, airlines, military agencies and government customers around the world.
“We are extremely pleased to continue our relationship with Esterline.” said DAC International’s President Cisco Hernandez. “We believe the CMA-6800 offers our customers a simple replacement solution for the aging ED-800’s currently in the field today, while lowering operating costs and further extending the life of their existing cockpits.”
DAC distributes the CMA-6800 Product line in aftermarket pursuits. DAC currently holds a AML STC that includes the Hawker 800/800xp/1000, Bombardier’s Challenger 601-3A/3R, Dash 8-100/200/300 and its 415 Superscooper, Cessna Citation 650, Dassault Falcon 900, Fokker 50 and the Gulfstream III. In addition the S76 STC is expected in late December to early January 2017 time period.
The CMA-6800 Electronic Display System was designed to replace the aging Honeywell ED-800 Cathode Ray Tube (CRT) displays. DAC partnered with Peregrine to complete the engineering, test and certification activity required for this STC.
In addition to the certification listed, DAC has received European Aviation Safety Agency (EASA) approval and ANAC Approvals.
SESAR JU RISE Project Wraps Up With Tremendous Success
SESAR JU RISE Project Wraps Up With Tremendous Success
December 14, 2016
NAVBLUE and its SEJAR partners are proud to announce the successful completion of the RISE Project (RNP Implementation Synchronised in Europe). Together, with SESAR Joint Undertaking (SJU), we have laid the ground work for the deployment of performance-based navigation (PBN) procedures at eight airports located in southern Europe.
The two-year RISE project aimed at improving airport access and enhancing safety of operations by removing the circle-to-land approaches, without relying on the ground navigation infrastructure, lowering the weather minima and allowing shorter tracks resulting in track mile savings and continuous descent operations.
The project, co-financed by SJU, was managed by NAVBLUE, in collaboration with four air navigation service providers (ANSPs) – DCAC, NAV Portugal, DSNA, HCAA –three airline operators – Air France, Novair and TAP Portugal, and numerous participant airlines including Aegean, EasyJet, Emirates and Air Corsica. These partners conducted over 500 flight trials, demonstrating 43 PBN procedures, such as required navigation performance (RNP) approaches with authorisation required (AR), RNP approaches, visual RNAV approaches, and RNP1 to instrument landing system (ILS) procedures (RNAV (RNP), RNAV (GNSS), RNAV Visual, RNP1 to ILS).
Paul-Franck Bijou, Chief Commercial Officer, NAVBLUE, remarked: “This project represented how industry partners can collaborate closely, each bringing their own expertise, to make substantial ecological and financial gains in the aviation industry benefitting all today and in the long term.”
For each airport, the project included design of the PBN procedures, validation on a full flight simulator, training of air traffic controllers and real flight demonstrations and supported extensively through the active participation of the four ANSPs.
Florian Guillermet, Executive Director of the SESAR Joint Undertaking remarked: “The RISE project represented an excellent opportunity to demonstrate more widely the significant efficiency, safety and environmental benefits that are possible with PBN procedures. I am very pleased that we were successful in improving access to regional airports, which is critical for better mobility and connectivity in Europe.”
Through questionnaires completed by Air Traffic Controllers (ATC) and flight crews and through flight data recordings, the project received very positive feedback and has been deemed to be a tremendous success that is bringing to the industry numerous safety enhancements, environmental benefits through reduced fuel consumption and noise disturbances while also providing greater airport accessibility.
IFS acquires Mxi Technologies Ltd
IFS acquires Mxi Technologies Ltd
December 13th 2016 – IFS, the global enterprise applications company, has today signed an agreement with the owners of Mxi Technologies Ltd (“Mxi”) to acquire the company.
Mxi is the leading provider of integrated and intelligent maintenance management software solutions for the global aviation industry. Mxi serves defence and commercial operators, third-party Maintenance, Repair and Overhaul (MRO) companies, and Original Equipment Manufacturers (OEMs) with software, support and services. Headquartered in Ottawa, Canada, Mxi is a global organisation with more than 265 employees.
Mxi’s Maintenix software suite is uniquely designed to help aviation organisations maximise the revenue potential of their aviation assets through standard, lean, and predictive maintenance. Mxi’s global footprint of customers ranges from emerging and mid-sized organisations to the largest global aviation enterprises, many of whom have multi-site deployments that scale to several thousand users. The company’s blue chip customer base includes: Southwest Airlines, Air France, KLM, Qantas, China Airlines, LATAM, Icelandair, NetJets, Boeing, BAE Systems, Saab, Pratt & Whitney, and several of the world’s air forces.
Alastair Sorbie, IFS President & CEO, said, “With the acquisition of Mxi, IFS becomes a world leading provider of aviation maintenance software solutions to defence and commercial aviation operators, MROs, and OEMs. We will continue to invest in and market both the Maintenix and IFS Applications solutions for customers who want a point solution, but we also believe that an end-to-end integrated solution will be attractive to many companies in the sector. The deep aviation maintenance expertise of Mxi combined with IFS uniquely positions us to help new and existing customers achieve operational excellence. This acquisition is in line with IFS’s growth strategy and ambition to become the world’s leading provider of enterprise applications to global customers in asset, service, and product-centric verticals.”
Diogenis Papiomytis, Director of Aerospace & Defence at industry analyst Frost & Sullivan, commented, “The acquisition of Mxi Technologies by IFS makes strong commercial sense, as the two companies have complementary capabilities and products targeting commercial and military aviation organisations.” Papiomytis added: “The global scale of IFS operations, as well as its innovative culture, extensive business development, and R&D resources will allow Mxi to grow its business and implement large scale projects without compromising on customer service or product development timeframes. Furthermore, the Maintenix product and Mxi’s growing aviation and defence customer base will add substantial value to the IFS product portfolio and assist in expanding its reach beyond the already strong IFS aviation & defence credentials.”
North Cariboo Air Adopts RAAS
North Cariboo Air Adopts RAAS
Calgary, Alberta, Canada – After a detailed systems evaluation process, North Cariboo Air has selected RAAS to replace the incumbent legacy system for complete management of aircraft maintenance processes including technical records, quality assurance, reliability, material management, procurement and expense tracking.
North Cariboo Air is an established charter airline who operate a mixed fleet of 20+ aircraft ranging in size from 9 to 100 seats, primarily serving the Canadian Oil and Gas sector. The heightened regulatory and data management requirements associated with larger aircraft types spurred an initiative at North Cariboo Air intended to identify an aviation maintenance management software suite that would streamline workflow, introduce inter-systems integration potentials, aid strategic decision support and ultimately help reduce expense across the entire enterprise.
North Cariboo Air Director of Maintenance, Bill Stupak, says, “Our decision to move to RAAS is part of a greater North Cariboo Air objective to increase information exchange across departments and meanwhile decrease ongoing expense. The AIS implementation team have created an implementation project plan that will directly replace our existing maintenance management suite while retaining established work flows, and concurrently add the facilities necessary to allow North Cariboo to achieve the higher degree of inter-system data integration we require to provide the highest level of service to our customers and support our team efficiently.”
AIS Director of Operations and CEO, Eric Hansen, comments, “North Cariboo Air have ever-changing fleet requirements and operational missions. As their business changes so do their business systems requirements, and AIS is very happy to have been identified as a solution provider that will add value to the North Cariboo Air organization.”
AVTECH Enters into an Agreement with Icelandair to provide Advanced Data to Cockpit
AVTECH Enters into an Agreement with Icelandair to provide Advanced Data to Cockpit
2016-11-07
AVTECH Sweden AB, with processing and sending advanced information in real-time to the cockpit and aircraft systems as one of its core businesses, today announces that it has entered an agreement with Icelandair ehf, to setup and support their advanced ACARS data transmissions during a limited 3-month time period.
Icelandair, Iceland’s leading airline, is in a project to increase flight efficiency and reduce flight crew workload trialing a real-time upload of information to its aircraft via data link. AVTECH will support the final live testing stage of this project.
“It is a pleasure to support one of Europe’s most well-known airlines in this important task, says Sören Skog Key account manager. ACARS communication, a ground based communication network used by airliners all over the world, plays an increasing role in air-to ground communication to modern aircraft.“, says Sören Skog, Key Account Manager.
“AVTECH’s long experience with advanced ACARS data integration made it possible to support Icelandair in this project. We look forward to further applying our technologies in this field to client applications in the future”, says David Rytter, CTO.
This time limited project is of minor financial importance but an important showcase of AVTECHs capabilities in this area.
For more information, please contact
Sören Skog, Key Account Manager, +46 (0) 8 544 104 80
David Rytter, Chief Technical Officer, +46 (0) 8 544 104 80
Middle East Propulsion Company (Mepc) Selects Ifs Applications for Engine Mro Support
Middle East Propulsion Company (Mepc) Selects Ifs Applications for Engine Mro Support
IFS Applications will support engine Maintenance, Repair and Overhaul (MRO) at MEPC’s facility in Riyadh, Kingdom of Saudi Arabia, which services aircraft engines for the Royal Saudi Air Force
IFS, the global enterprise applications company, announces that Middle East Propulsion Company (MEPC) has selected IFS Applications™ to help manage key operations at its Riyadh facility such as MRO, finance, supply chain, document management, HR, and payroll.
In 2012, MEPC opened its state-of-the-art, 194,000 square-foot MRO facility in Riyadh, close to the city’s King Khalid International Airport. MEPC is the sole military engine shop in the Kingdom of Saudi Arabia and provides MRO support for the Pratt & Whitney F100 engines powering the Boeing F-15 fighter aircraft operated by the RSAF.
The IFS solution will allow MEPC to execute all aspects of its MRO operations, from hangar entry to exit – with integrated support for finance and HR. End-to-end visibility will extend across personal areas of responsibility, ensuring focus is kept on what is strategically important. Business intelligence is built into IFS Applications, enabling operators to analyse key performance indicators using predictive analytics to show the full impact of processes on overall MRO performance, as well as the effect a decision has on operations in real time.
“Rather than continuing to use a combination of different business systems, we required a single, integrated solution to manage our complete business operations at the critically important Riyadh facility,” said Abdullah Al Omari, Chief Executive Officer at MEPC. “The 360-degree visibility provided by IFS Applications allows us to maximise maintenance efficiency and react quickly to potential performance issues, which is important in the fast-paced military support environment.”
Luis Ortega, Managing Director for Middle East, Africa & South Asia at IFS added, “The selection of IFS Applications to support the MEPC facility, which is integral to military operations in the Kingdom of Saudi Arabia, demonstrates the strength of the engine MRO capability in IFS Applications. The RSAF is one of the most advanced fighting forces in the world, and we are delighted to be supporting MEPC with our market-leading engine MRO solution to keep its aircraft available and operational around the clock.”