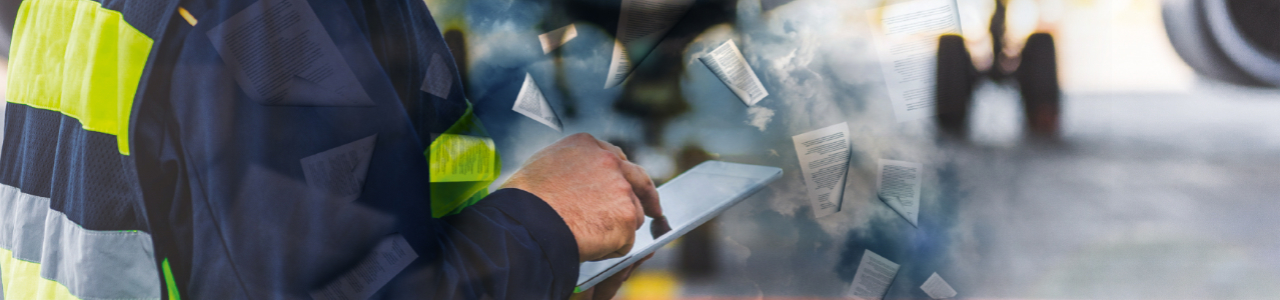
TAROM Airlines Implements Honeywell Forge Flight Efficiency to Reach Fuel and CO2 Goals
Romania’s largest airline, TAROM, is approaching its 70th year in the skies. As the company sought to expand their flight-efficiency program to keep their emissions goals and fuel savings on target, they turned to Honeywell Forge Flight Efficiency. Being the largest airline in Romania based on international flights and destinations as well as a consistently growing and expanding company, flight efficiency is an ongoing challenge when working towards sustainable air travel. In addition, as a SkyTeam alliance member, TAROM has sustainability commitments for achieving maximum CO2 reduction.
The Romanian flag carrier owns one of the youngest fleets in Europe, but even with relatively new aircraft, reducing fuel burn and CO2 emissions is always a concern. The company knew there was more they could do.
The company built their Fuel Efficiency Improvement initiative around the framework proposed by IATA for a successful fuel management program. One important feature of this model is “management by numbers” using a Define-Measure-Analyze-Improve-Control (DMAIC) process. Their strategy was in place, but TAROM lacked a system that could consolidate and analyze their internal data, allowing them to make data-driven decisions about flight planning and fuel loading. TAROM sought out the Honeywell Forge Flight Efficiency team for advice and solutions.
Honeywell Forge Flight Efficiency brings together flight variables into a single platform for a comprehensive look at fleet and environmental data. The tool can be used to discover and monitor savings opportunities by fleet, tail, airport, city pair and more. It’s a one-stop-shop for insights and can be leveraged to rally stakeholders company-wide and engage them in efficiency initiatives. The platform instantly unlocks value, enabling airlines to make improvements in targeted areas.
“The scope of our fuel management initiative is beyond a plain ‘cut the costs’ operation. It is a change management endeavor focused on fleet renewal, improving operational efficiency, promoting and using sustainable aviation fuels, and carbon offsetting,” said Dragos Preda, Fuel Efficiency Improvement Manager at TAROM.
“By choosing Honeywell Forge Flight Efficiency we have solid indications TAROM will reach an efficiency level beyond our initial goals.”
Dragos Preda, FEI Manager for TAROM
In addition to the benefits gained through the Honeywell Forge Flight Efficiency portal, Preda commented on the value of his relationship with the product team, adding “Honeywell Forge Flight Efficiency is managed by a highly-supportive team, and I appreciate how passionate they are, openly discussing and sharing their fuel management knowledge.”
Prior to implementing Honeywell Forge Flight Efficiency, the airline was able to monitor general fuel consumption figures and reveal generic trends using simple tools. However, TAROM soon realized that mining for insights behind those generic trends was not possible. Much of the data came from single sources, making it unreliable and even inaccurate in some cases.
“The level of aviation fuel efficiency we need can’t be reached without a tool specifically designed for fuel management,” Preda said. “Honeywell Forge Flight Efficiency intakes, processes and cross-references many distinct data sources to provide a detailed and accurate image of our fuel situation. It is one of the best tools that explicitly targets fuel management and is reliable.”
Being one of the first Honeywell Forge deployments in Romaina, TAROM is fully confident in the solution’s capabilities. In just a few months since implementation, Preda commented that he believed the system has the potential to increase operational fuel savings by about 3%. Preda said, “By choosing Honeywell Forge Flight Efficiency we have promising indications TAROM will reach an efficiency level beyond our initial goals.”
Lufthansa German Airlines and Lufthansa Cargo live with AMOS
At a glance
- Tier-one project finalised with successful go-live
- 3’500 new users and approx. 300 additional aircraft now managed in AMOS
- Almost all Lufthansa Group aircraft are now managed in AMOS
- Multi-CAMO setup
Tier one project successfully completed
Swiss AviationSoftware Ltd. is proud to announce the successful cut-over to AMOS M&E system at Lufthansa German Airlines and Lufthansa Cargo.
The “big-bang” go-live took place on May 14th and 15th and marked the ultimate finalisation of an implementation unique in Swiss-AS history in terms of size and complexity: 3’500 users, 150 new processes, a multitude of individual legacy IT systems being replaced and close to 300 aircraft ranging over seven aircraft-types including the A320s with up to 30 years of history.
Both airlines have fully adopted AMOS for their whole active fleets in a multi-CAMO setup – two completely separated CAMOs (LHA + LCAG) plus one SCAMT service provider working in one AMOS environment – all approved by the German aviation authority.
The global pandemic had a significant impact on the AMOS implementation as all projects at Lufthansa had been put on hold in 2020. Fortunately, the airlines’ Management then decided to continue the AMOS rollout as one of few strategic projects: “AMOS Restart” was born and came with an adjusted scope and limited manpower. Nevertheless, the project team managed to bring the project back to speed and successfully completed it. The airline embraced the opportunity to emerge stronger and more resilient from the crisis.
Ambitious expected benefits
The introduction of AMOS marks the end of a multitude of individual IT legacy systems for both airlines and provides a future-proof core platform to further digitalize the group’s Technical Fleet Management (TFM). The project was initiated with the objective to realize the following benefits:
- Simplify and modernize the IT landscape including system integrations;
- Significantly reduce the annual software/hardware costs;
- Increase efficiency of the CAMO organization leading to sustainable cost reductions;
- Make compliance with airworthiness laws and regulations simple;
- Substantially reduce MRO spending through improved data quality and insight;
- Benefit from industry best practice AMOS build-in processes to enhance efficiency across Technical Operations;
- Align processes to TFM group standards to realize further group-wide efficiency improvements.
“Implementing AMOS as our M&E software was a strategic project for Lufthansa and Lufthansa Cargo. We now have a solid platform to continue our digital push towards more increased mobility, leaner processes and easier data integration across our multiple systems.
This project was one of few selected by the Board to continue despite the turbulent period caused by the pandemic. Today, that decision pays off in full,” says Thomas Spriesterbach, VP Technical Fleet Management Lufthansa, Accountable Manager Part 145, “and we are happy to be partnered with Swiss-AS, not only as supplier of AMOS, but especially for their staff’s expertise and professionalism throughout the project.”
A new organization, new processes and advanced integrations
Historically Lufthansa Airlines had outsourced the CAMO and Line Maintenance activities to Lufthansa Technik. In parallel to the AMOS implementation, these activities have been insourced along with the integration of approx. 2’500 staff and many of the legacy IT systems, used to manage these activities.
The legacy IT systems were basically home-grown and highly customized. To eventually achieve go-live with AMOS, it was required to create a complete new Technical Fleet Management organization inside the Lufthansa Group, adjust processes to existing group standards that follow the AMOS build-in industry best practices processes and convince the users that the rich functional scope and configurability of AMOS matches the customized legacy system features.
The AMOS implementation was flanked by the group-wide Technical Fleet Management (TFM) initiative that focusses on the standardisation and harmonisation of the technical business processes among the Lufthansa Group members in order to boost the performance of the individual Tech Ops departments and to allow an easy exchange of aircraft and other assets within the group.
The AMOS centric IT eco system includes advanced interfaces to around 15 major external software sources, such as Flight Operations Systems, Digital Archiving Solution, Crew Briefing Systems, Warehouse Management and Transport/Logistics Management Systems etc.
One of the most advanced integrations connects AMOS with the customer’s main pool provider Lufthansa Technik, through an advanced bi-directional integration to support a highly automated material supply chain process.
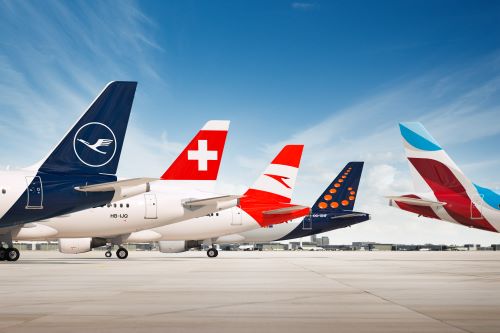
Leveraging existing AMOS experience in the Lufthansa Group
AMOS has been used for more than 20 years within the Lufthansa Group; therefore, Lufthansa German Airlines and Lufthansa Cargo were in the lucky position to profit from the extensive experience of the other group members (Swiss International Air Lines, Austrian Airlines, Eurowings, Brussels Airlines and Lufthansa CityLine). With their extensive AMOS knowledge, colleagues from the sister airlines supported the implementation as key users in areas such as training, user acceptance testing, process definition and data transfer, while further cementing the collaboration within the Lufthansa Group.
From the IT perspective, Swiss-AS in partnership with Reist Telecom (Zurich) hosts the airlines’ AMOS servers and offers in this context its proven AMOS Operation Service (AOS) package. Swiss-AS is already performing hosting, AMOS application server and database administration for other Lufthansa Group members, which convinced Lufthansa German Airlines and Lufthansa Cargo to also entrust these crucial tasks to Swiss-AS.
“Congratulations to Lufthansa German Airlines and Lufthansa Cargo for this successful cut-over to AMOS which has the potential to lift the group-wide cooperation in M&E to a whole new level. We are extremely proud that AMOS is now the backbone MRO software solution for the Lufthansa Group,” states Ronald Scherer, CEO of Swiss-AS. “My thanks to all those who have been involved in this challenging project and have contributed to its great success, while, of course, including the customers’ project teams into this statement.“
A big-bang implementation with unparalleled dimensions
From the beginning the project was designed around the hypothesis of a big-bang go-live with approx. 300 aircraft across all stations. This approach will eventually allow to exploit expected benefits faster and avoid the complexity of running multiple systems in parallel for an extended time.
The data transfer project had been immensely complex and challenging due to:
- 30 years of historical data
- more than 15 legacy systems involved
- a diverse fleet consisting of 7 different aircraft-types
- approx. 300 aircraft
In total 60 million records had to be transferred into AMOS. This major task of legacy data cleansing, mapping, extraction, transfer and validation had been mastered by a mixed project team of Lufthansa Group and Swiss-AS.
Regarding the training, not less than 3’500 new users have been educated on AMOS and the new procedures that came along with it. The airlines applied a mix of train-the-trainer and e-learning for the end users, while the most complex topics such as engineering or planning were led by experienced Swiss-AS trainers, onsite or remotely.
For the cut-over a duration of 48 hours had been scheduled. During that time Swiss-AS had allocated around 40 employees onsite at Frankfurt, Munich and Hamburg to support the users during the switch-over and the post-go-live stabilisation period. In addition, the Swiss-AS headquarters was on standby for any challenges that might occur during such event.
Foundation laid for further group-wide Technical Operations digitalization
With the successful implementation, AMOS is now the leading CAMO and Part-145 software in the Lufthansa Group – fully integrated into and interfacing with the surrounding IT system landscape, based upon the TFM Group standard compliance processes.
The roll-out of AMOS at Lufthansa German Airlines and Lufthansa Cargo will provide the base to further digitize processes in the Lufthansa Group by leveraging AMOS’ advanced integration capabilities. True digitalization can only be achieved by looking at the value streams holistically and beyond single systems or companies. AMOS with its comprehensive portfolio of APIs offers unparalleled possibilities to ensure digital data flows end-to-end. In addition, Technical Operations data across all Lufthansa Group airlines will now be generated by AMOS. This will significantly improve and simplify data management and eventually allow the group to unlock the potential of its data.
“I have a lot of respect for the dedication and determination shown by Lufthansa Airlines and Lufthansa Cargo colleagues in working untiringly towards the objective of implementing AMOS and eventually exploiting the clearly identified benefits – ‘Where there’s a will, there’s a way’, states Fabiano Faccoli, COO of Swiss-AS. While Swiss-AS previously gained experience with large implementations, this implementation clearly sets the bar higher. It enabled us to further grow our capabilities and expertise in managing tier-one customers. A go-live is the end of one chapter, but as well the beginning of a new chapter in a software’s life cycle. Swiss-AS is now very much looking forward to kicking off the next set of digitalization projects with Lufthansa German Airlines and Lufthansa Cargo and together set benchmarks in the industry.”
About Lufthansa German Airlines
Lufthansa, the biggest airline within the Lufthansa Group, is one of the world’s largest and most prestigious airlines in existence. In the 2021 business year, the airline welcomed around 23.5 million passengers on board its flights. With its hubs in Frankfurt/Main and Munich, Lufthansa employs more than 35,700 people. As an industry innovator, Lufthansa has long been committed to environmental care and sustainability, operating one of the most technologically-advanced and fuel-efficient fleet in the world. Lufthansa’s flagship A350-900 is currently the world’s most modern and environmentally-friendly long-haul aircraft. It uses 25 percent less kerosene, produces 25 percent fewer emissions and is significantly quieter on take-off than comparable types of aircraft. In order to accelerate fleet modernization, the procurement of state-of-the-art A350-900 and 787-9 long-haul aircraft further increased the efficiency of the fleet on a continual basis. These aircraft will reduce CO₂ emissions by up to 30 percent compared with their immediate predecessors, thus making an important contribution to the further development of the airline’s long-haul fleet and to a more sustainable flying experience overall. Lufthansa as of 31. December 2021 flies to183 destinations in 71 countries on 4 continents. In the 2021 business year, the airline welcomed around 23.5 million passengers on board its flights.
About Lufthansa Cargo
With a turnover of 3.8 billion euros and a transport performance of 7.2 billion freight ton kilometers in 2021, Lufthansa Cargo is one of the world’s leading companies in the transport of airfreight. The company currently employs around 4,200 people worldwide. Lufthansa Cargo’s focus is on the airport-to-airport business. The route network covers around 300 destinations in more than 100 countries, using both freighter aircraft and cargo capacity from passenger aircraft operated by Lufthansa, Austrian Airlines, Brussels Airlines, Eurowings Discover and SunExpress, as well as trucks. The majority of the cargo business is handled via Frankfurt Airport. Lufthansa Cargo is pursuing the goal of becoming the world’s most sustainable cargo airline. To achieve this, the company relies on state-of-the-art technologies and continuous investments in the area of sustainability. In 2021, important milestones were reached, such as the fleet modernization to an all-B777F fleet and the introduction of completely CO2-neutral freight transport for all customers. In 2022, Lufthansa Cargo plans to successively equip its fleet with Sharkskin technology and expand its Sustainable Aviation Fuel program to further reduce CO2 emissions. Lufthansa Cargo is a wholly owned subsidiary of Deutsche Lufthansa AG and the specialist for the logistics business of the Lufthansa Group.
About Swiss AviationSoftware and AMOS
AMOS is a comprehensive, fully-integrated MRO software solution being developed and distributed by Swiss AviationSoftware. Swiss-AS, a 100% subsidiary of Swiss International Air Lines has more than 200 customers worldwide and belongs to the industry-leading MRO software providers. Our loyal customer base includes pure operators of all sizes, major low-cost, regional and flag carriers, large airline groups and MRO providers. In the Americas and in Asia, AMOS is distributed through a partnership with Lufthansa Systems. For more information, please contact us via marketing@swiss-as.com.
Berry Aviation signs up for Rusada’s ENVISION
SAN MARCOS, TEXAS: Leading private services operator Berry Aviation, has selected Rusada’s ENVISION software to manage its Airworthiness and Maintenance activities.
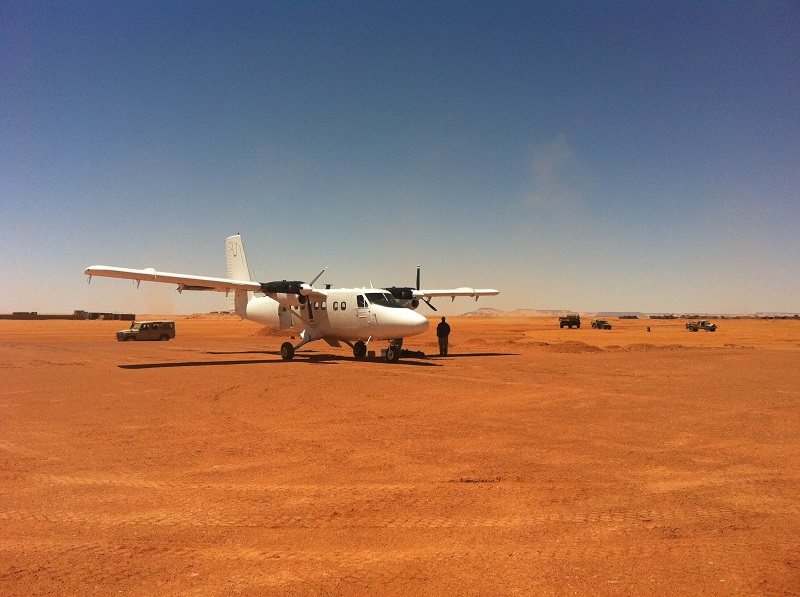
Berry Aviation, based in San Marcos Texas, provide specialty passenger, cargo, and medevac services to the U.S. Department of Defense, as well as cargo flights for civilian organisations, and third-party MRO services. They operate a mixed fleet of over 20 aircraft consisting of De Havilland DHC-6, De Havilland DHC-8-200, Embraer 120, Fairchild Swearingen Metro III, King Air 350, and Cessna 206.
As well as serving all branches of the U.S. military, Berry Aviation’s customers also include Fortune 500 companies, NCAA athletic teams, NASCAR teams, and other Part 135 and 121 carriers.
Berry Aviation have signed up for six of ENVISION’s modules, including Fleet Management, Base Maintenance, and Inventory Management, along with Rusada’s ENVISION Tasks and ENVISION Stock mobile applications.
The solution will be implemented by Rusada’s North American Client Services teams, with work on the project having already begun.
“Due to the growth we’ve experienced over recent years, we were looking for a solution that could better handle the operations and maintenance of a more diverse and larger fleet. ENVISION stood out for us because of its use of modern technologies, and its user-friendly interface. In particular, we were very impressed with its quick and easy forecasting of maintenance activities, as well as its ability to efficiently handle component MRO.
“Even in these early stages of the implementation process we are already beginning to see the benefits Rusada’s software will bring our business and our customers.”
Steve Jenkinson, Director Flight Dispatch Operations at Berry Aviation
Julian Stourton, CEO at Rusada said:
“The services that Berry Aviation provide are incredibly complex in nature, which in turn leads to a complex maintenance environment. Managing such a diverse fleet is tricky enough as it is, but if you don’t have an intelligent software solution to assist you, then the task becomes almost impossible.
“ENVISION has been tried and tested in complex operations around the world, so I am more than confident it can deliver the performance and oversight that Berry are seeking.”
About Rusada
Rusada is a leading provider of aviation software with over 35 years of experience in the industry. Its ENVISION software manages over 2,000 fixed and rotary wing aircraft for 150 operators, maintainers, and manufacturers in 45+ countries. With its headquarters in Switzerland and offices in the USA, UK, UAE, India, Singapore, and Australia, Rusada provides global support for a global industry.
Specialising in the management of airworthiness, maintenance, and flight operations, ENVISION is developed solely for aviation. Its modern, web-based platform features a suite of integrated modules, enhanced by a series of native mobile apps. ENVISION’s easy-to-use interface provides users with clear, actionable information, enabling processes to be carried out quickly and efficiently, and all without the need for paper or spreadsheets.
Media Contact
Chris Prior
Marketing Manager
+44 (0) 1295 231619
Vistara partners with Ultramain ELB for paperless operations; becomes first Indian airline to introduce e-tech logbook
Delhi, 25 July 2022: Vistara, India’s finest full-service carrier, today became the first Indian airline to introduce an e-tech logbook solution and go paperless in its operations in association with ULTRAMAIN ELB.
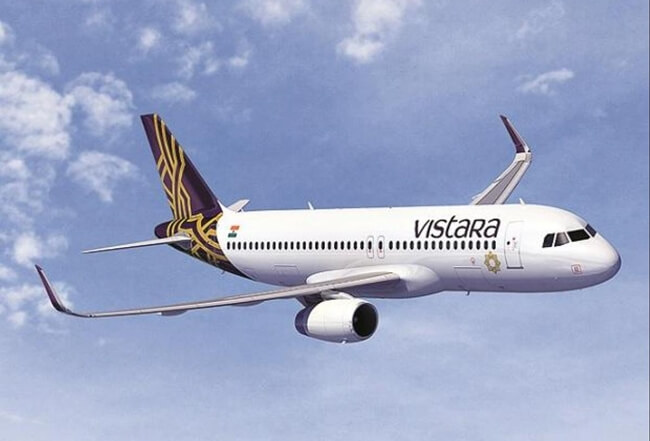
ULTRAMAIN ELB will fully replace aircraft paper technical log, cabin log, journey log, damage log, and fueling log providing a validated electronic Certificate of Release to Service (e-CRS) on flights operated by Vistara. Currently in the airborne proving stage, the ELB application will be used by Flight Crew, Cabin Crew, and Engineers on iOS devices to provide integrated workflows with Vistara’s maintenance and operational systems. The airline is seeking necessary approvals from relevant authorities before fully integrating this solution across its operations. Once implemented, ULTRAMAIN ELB will enable accurate, real-time global operational visibility of the Vistara fleet resulting in more efficient maintenance, higher dispatch reliability, and increased aircraft utilization.
“As Vistara marches on its Digital Transformational journey, the focus on digital data capture, integration and automation will continue. ULTRAMAIN ELB will help digitize our aircraft paper logs and improve operational effectiveness.” said Vinod Bhat, Chief Information Officer, Vistara.
“Vistara remains committed towards constantly improving operational efficiency across processes through automation and we’ve been investing in right technologies to achieve this goal. We are delighted to partner with Ultramain Systems, which will provide the first Electronic Logbook to seek operational approval to operate a fully electronic Technical and Cabin Logbook in India. ULTRAMAIN ELB will be integrated with various live processes like AMOS, ACARS, and ARMS for seamless operations. This application, with its completeness and ease of use, is one step towards building enterprise application integration while also focussing on sustainable operations.”, said Sisira Kanta Dash, Senior Vice President – Engineering & Maintenance, Vistara.
“We are pleased to welcome Vistara to the ULTRAMAIN ELB family. As well as our well proven defect management functions. Vistara will be using ELB’s refuel / defuel functions, which enable real time capture of refueling documentation using Ultramain’s e-Signature capabilities. This is another important step towards the automation of Line Maintenance Operations” said Mark McCausland – President and CEO of Ultramain Systems.
Ultramain Systems provides SIMPLE MOBILE PAPERLESS Aviation Maintenance software products and professional services to airlines worldwide. ULTRAMAIN® ELB™ – the market leading electronic logbook software has been replacing paper-based processes while offering comprehensive functionality and innovative features to help make airlines processes seamless.
Vistara is India’s highest-rated airline on Skytrax and TripAdvisor, and it has been the winner of several ‘Best Airline’ awards, besides being lauded for cabin cleanliness and safety standards. In a short span of seven years since starting operations, Vistara has raised the bar for operations and service standards in the Indian aviation industry to become the country’s most loved airline and has recently crossed the mark of flying 35 million passengers.
***
About Vistara (TATA SIA Airlines Limited): TATA SIA Airlines Limited, known by the brand name Vistara, is a 51:49 joint venture between Tata Sons Private Limited and Singapore Airlines Limited (SIA). Vistara brings together Tata’s and SIA’s legendary hospitality and renowned service excellence to offer the finest full-service flying experience in India. Vistara commenced its commercial operations on January 9, 2015, with an aim to set new standards in the aviation industry in India and it today connects destinations across India and abroad. The airline has a fleet of 53 aircraft, including 41 Airbus A320, five Airbus A321neo, five Boeing 737-800NG and two Boeing 787-9 Dreamliner aircraft and has flown more than 35 million customers since starting operations.
For more information about Vistara, visit www.airvistara.com
MEDIA CONTACTS:
Rashmi Soni VP & Head of Corporate Communications rashmi.soni@airvistara.com | Abhilash Pushpan External Communications Manager abhilash.pushpan@airvistara.com | Smriti Jain AvianWe smriti@avianwe.com +91 9953181096 |
Swiss-AS’ eTLB brings AMOS to the flight deck
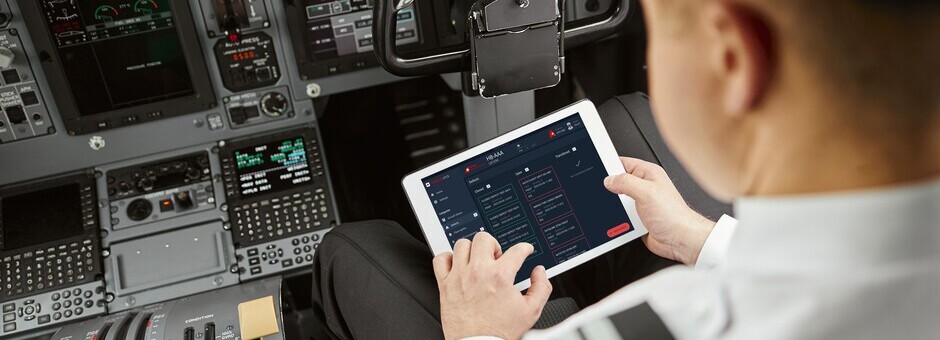
At a glance
- Swiss-AS has launched the development of its eTLB
- Swiss-AS offers a unique product suite for pilots, cabin crew and maintenance staff
- A joint development effort including members of the AMOS airline community
An eTLB tightly integrated with AMOS…
At the end of 2020 Swiss-AS announced within the AMOS customer community the extension of its product portfolio by launching the development of its own eTLB.
With the Swiss-AS eTLB, tightly integrated with AMOS, our customers will have a unique opportunity to improve the collaboration between pilots, cabin crew and mechanics. With the seamless integration of the Swiss-AS eTLB with AMOS and AMOSmobile/EXEC, customers benefit from a product suite that becomes the one source of truth for cockpit, cabin and maintenance staff. Each airline will profit from streamlined end-to-end processes across AMOSdesktop, AMOSmobile and the eTLB, providing increased data access and consistency across departments.
… to better achieve the usual benefits expected from an eTLB
With an intuitive user experience and an elegant user interface, the Swiss-AS eTLB provides flying crew, maintenance staff, administrators and authorities the right level of information and functions required in the respective context.
Swiss-AS eTLB main functions:
- Pilot in command: reporting defects in an intuitive way, selecting them from a pre-existing list and being able to add any additional relevant information for the maintenance staff and goes beyond a defect report.
- Cabin: being able to report a cabin defect in a simple way; if needed, a highlighted picture can be added in order to enhance the Flight Crew – Cabin Crew communication.
- Maintenance: being able to report defects, close defects and perform line maintenance related tasks, such as daily checks, from its own working environment.
- Admin: being able to manage users and roles, workflows and configuration directly in AMOS, roll-out updates and configuration through their Mobile Device Management.
- Authorities: in analogy to the paper TechLog, the authorities need to consult and access the continuous airworthiness of the aircraft associated with the specific eTLB. They can consult every page but are not able to edit any detail.
The implementation of the Swiss-AS eTLB ultimately leads to an end-to-end process optimisation and cost reduction, since the Swiss-AS eTLB helps optimising aircraft turnaround times, providing aircraft availability status in real time, and increasing data access and consistency for flying crew.
Simple implementation and platform independence for additional cost optimisation
At the early stages of its development project, Swiss-AS decided for a Type-A EFB application running on a portable EFB. This strategic choice simplifies the aviation authorities’ approval process for our customers, while avoiding, once implemented, the continuous certification process of each new release of the application. Moreover, Swiss-AS is currently closely working with EASA to obtain an NTO letter to even more ease the adoption of the Swiss-AS eTLB by its customers and their authorities.
Additionally, the Swiss-AS eTLB runs on several operating systems to leverage already deployed hardware in the cockpit and / or provide airlines the possibility to select the most cost efficient hardware for particular contexts.
A joint development effort including the AMOS airline customer community
Swiss-AS collaborates closely with customers to specify the product scope, as performed previously for the development of various AMOS features. This tradition is extended and even enhanced for the Swiss-AS eTLB project, which involves requirement gathering from cockpit crew, cabin crew and maintenance staff.
Over the past months, Swiss-AS had the privilege to onboard several AMOS customers to the eTLB development partners group, such as EL AL ISRAEL AIRLINES, Luxair and Cebu Air. Since the project kick-off in September 2021, both Swiss-AS and customer project team members attended numerous workshops to define key features to be used by pilots, cabin crew and maintenance users.
We consider this customer-centric scope definition and validation process to be a highly constructive and successful model to facilitate the delivery of a mature and functionally advanced product.
Thanks to this strategic partnership with AMOS airline customers of several types and sizes, Swiss-AS will deliver its eTLB solution in Q4 2023.
“EL AL considers the eTLB as an integral part along with AMOSmobile/EXEC to enable paperless throughout our maintenance. Having it as part of AMOS is a huge advantage with hope for a smooth integration. We are delighted to have the opportunity to take an active role in the development phase of the product, influencing and shaping the tool and providing a good learning experience.”
Danny Laredo, Paperless Project Manager, Maintenance & Engineering Division at EL AL ISREAL AIRLINES.
For more information and regular updates, please visit swiss-as.com/amos-mro/etlb
Leading Taiwan-Based Aircraft Maintenance, Repair and Overhaul Service Provider, Air Asia Company Limited Goes Live with Ramco Aviation
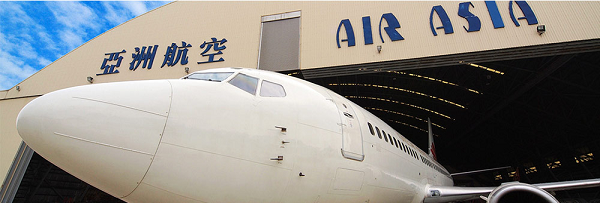
Tainan City, TAIWAN / Chennai, INDIA – July 12, 2022 – Global aviation software provider Ramco Systems announced that it has successfully gone live at Air Asia Company Limited (AACL), Taiwan’s first privately-owned aircraft maintenance company catering to aircraft maintenance of commercial aircraft, helicopters, military and a designated ‘Government owned contractor operated facility’ (GOCO), with its Aviation M&E MRO Suite V5.9, thereby automating and digitally transforming AACL’s business processes.
With modules for Production Planning, Commercials, Maintenance Execution and Supply Chain Management, Ramco’s one stop solution, Ramco Aviation Suite V5.9 replaced AACL’s existing legacy system for proposal management, production Planning, heavy maintenance process for commercial aircraft, and interfaces with AACL’s inventory management solution. As a result, AACL has now recorded a 15% reduction in its production planning process. In addition, Ramco’s next-gen innovations like its Mechanic Anywhere mobile app and real-time Dashboards together with the digital transformation initiatives for Task Card Management, Electronic Signoffs, enable the company to streamline communication between its departments, analyze manhour consumptions, track opportunity details, progress of work packages and report non-routine tasks on the go.
Eric Y.C. Tsai, Director of Commercial Aircraft Planning, Air Asia Company Limited, commented, “With a primary goal to achieve paperless operations and support green environmental protection, and with a vision to become a world-class and professional aircraft Maintenance, Repair and Overhaul (MRO) service provider, we found a perfect technology partner and a best-in-class Aviation software provider in Ramco Systems. Ramco’s rich domain expertise along with the able team members at AACL and Ramco ensured to turnaround this project during the pandemic. Ramco’s Digital Task card feature has been helping us achieve our goal. We are confident that these will be signed off by the Civil Aviation Authority (CAA) and Federal Aviation Administration (FAA), as well.”
Manoj Kumar Singh, Chief Customer Officer – Aviation, Aerospace & Defense, Ramco Systems, said, “With the growing aviation industry, organizations today are being mindful of choosing innovative solutions that are not only helping them improve efficiency, but are also helping them achieve green initiatives. Ramco’s Task Card Digitization is a step towards sustainability in aviation. Equipped with the latest technology stacks around artificial intelligence and machine learning, Ramco Aviation Suite has been helping companies embrace paperless operations and embark on digital transformation. We are happy to support Air Asia Company Limited in their endeavor and help them scale to greater heights.”
Ramco Aviation, Aerospace & Defense is trusted by 24,000+ users to manage 4,000+ aircraft globally. Accessible on cloud and mobile, Ramco Aviation & Defense Software continues to innovate with ‘Anywhere Apps’, significantly reducing transaction time both during aircraft-on-ground (AOG) conditions and critical aircraft turnarounds. Ramco is changing the paradigm of enterprise software with Artificial Intelligence based solutions, powered by cool new features such as digital task cards, offline capability, chatbots, mail bots, HUBs and cognitive solutions. With 80+ Aviation organizations onboard, Ramco is the solution of choice for top heli-operators, leading defense companies, space launch vehicles, UAS/Drones, eVTOL and multiple MROs around the world.
About Air Asia Company Limited (AACL):
Air Asia Company Limited (AACL) was established in 1955 by first funder Gen. Claire Chennault, a former U.S. volunteer aviation commander who was well known by famous “Flying Tiger” during World War II. AACL has been the first private-owned aircraft maintenance company in Taiwan.
Gen. Claire Chennault’s successful experience in management and leadership turned AACL into a world-class and professional aircraft Maintenance, Repair and Overhaul (MRO) service provider.
In 1994, AACL officially become a subsidiary of Taiwan Aerospace Corporation (TAC) as the only Taiwan-based professional MRO with rich experiences, standard facilities and equipment, and well-skilled workforces and competitive prices in servicing both commercial and military aircraft in the Asia Pacific region.
AirExplore signs-up for the EFBOne Cross-Platform solution
IFS, the Copenhagen based EFB Software Platform SaaS provider, announces that it has signed a contract with AirExplore based in Bratislava, Slovakia, to implement the EFBOne from IFS.
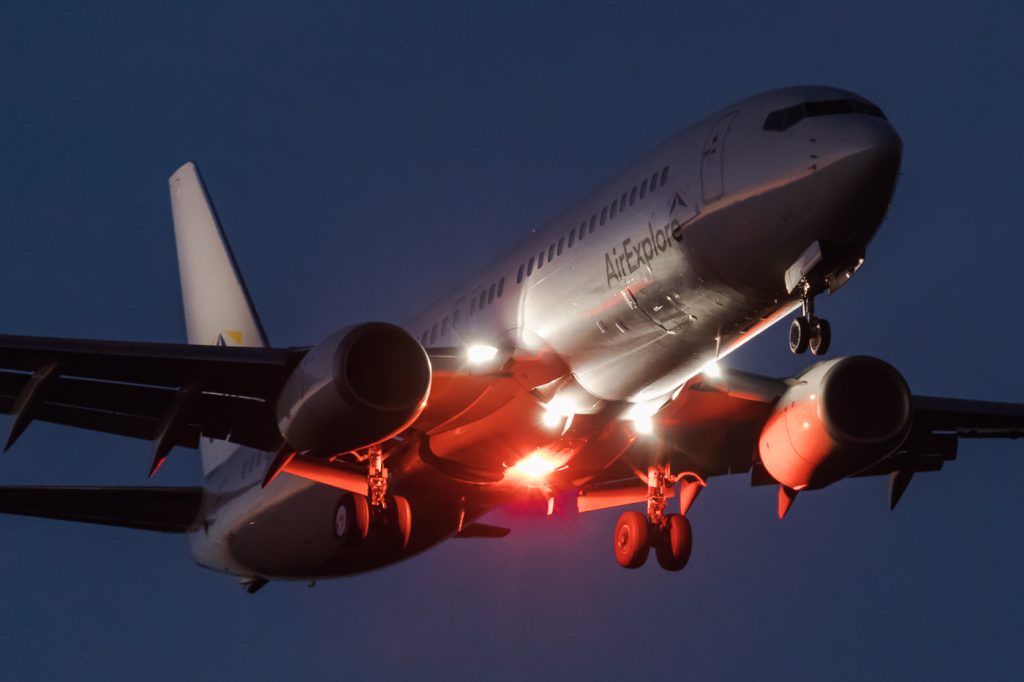
AirExplore operates a modern fleet of 8 Boeing B737-800 aircraft. The AirExplore core business is to provide the ultimate and most flexible ACMI solution to airline clients worldwide using modern aircraft, experienced crew, skilled maintenance, and comprehensive insurance. The implementation of EFBOne will take place during Q3/Q4-2022.
“Being an ACMI operator we selected this solution because it copes with our current and future demanding operational requirements. The EFBOne will be a cornerstone in our operational set-up and its flexibility secures that we can meet our long term EFB strategy goals. The effective and yet flexible architecture of this EFB software solution gives AirExplore the opportunity to bring even more automation into its processes to reduce the workload and increase operational flexibility for flight crews as well as for ground personnel”, Mr. Pavol Klein, Flight Operations Director ofAirExplore said.
The EFBOne solution to be provided will include full Pre-flight reporting with Fuel Planning, In-flight reporting with Electronic Flight Planning module integrated with AirExplore’s NAV Flight Services Flight Planning system output, Post-flight reporting integrated with AirExplore’s LEON Scheduling & Crew planning system, as well as seamless integration of the Jeppesen MFD Pro Chart Viewer application and Boeing OPT Performance app will provide the crew with a uniform and interconnected workflow. The solution includes the comprehensive EFBOne Back-Office System which powers the EFB Platform, centralizes all data flows and controls data import/export to back-end systems and manages status of all individual and aircraft deployed EFB units.
“IFS is honoured to be selected by AirExplore for this EFB software platform project and is looking forward to finalizing the implementation together with AirExplore during Q3/Q4-2022. By selecting EFBOne AirExplore will get a centralized business intelligence tool and a highly customized application solution which can cover all present and future requirements. The choice indicates that IFS offers the right combination of product solutions, advanced technology, seamless integration and the highest cost/benefit levels in the market” says Sandra Daukste, EFB Relationship Manager of IFS.
ABOUT
AirExplore specializes in ACMI/Wet lease operations and is capable of setting up remote operational bases with short notice for their aircraft worldwide. Using own maintenance organization and highly experienced and friendly crew, AirExplore is able to satisfy any customer’s requirements. For more information visit www.airexplore.sk/en
ABOUT
IFS is an innovative and experienced SaaS supplier of iOS and Windows based EFB Software Platform solutions aimed at commercial aircraft operators. The company was founded in 2005 and has 15 years of operational experience providing in-cockpit solutions to airline operators, cargo operators, business jet fleet operators and military users. The EFBOne software solution defines a new standard for high quality modular EFB architecture. It was built to achieve complete data integration to any back-end software systems used by the operator while offering a unique degree of customization options that reflects each operator’s preferences for modules and work-flow contents all set-up to match each airline’s standard operating procedures. For more information visit www.ifs.aero
NAVBLUE opens new site in Gdansk, Poland for Data and Software Production
- New site in well-known aerospace hub
- Focus on Aero Data & Software Production
To expand its global presence NAVBLUE, Airbus’ subsidiary for Flight Operations solutions, announces the opening of a new site in Gdansk, Poland, a recognized aerospace and software hub in Europe.
The office in Gdansk, which will open officially by end of Q3 2022, will specialize in Aero Data and Software Production, leveraging a local talent ecosystem, to develop, produce and deliver continued state of the art flight ops products and solutions that drive airlines’ operational efficiency and support sustainable aviation.
With this opening, NAVBLUE continues its expansion worldwide, now with 4 sites in Europe (France, UK, Poland and Sweden) and offices in Canada, USA, Thailand, and Singapore.
“With our new office in Poland we are reinforcing the NAVBLUE network in Europe and throughout the world. We are happy to open in Gdansk with its recognized talent in software development. It will also facilitate working relations with other teams based in Europe, Asia and America. Our aim is to become an employer of choice in the area, as a high performing and attractive company, and we encourage potential candidates to start applying from now.”
Fabrice HAMEL, CEO of NAVBLUE
For more information on working for NAVBLUE in Poland, please click here.
About NAVBLUE: NAVBLUE is an Airbus Services company, wholly owned by Airbus, and dedicated to Flight Operations & Air Traffic Management Solutions. NAVBLUE provides products and services, and supports both civil and military environments, on the ground and onboard any aircraft and offers expertise in a range of areas, including digital cockpit operations, Operations Control Centre (OCC) systems, Flight Ops Engineering, Performance Based Navigation (PBN) and Air Traffic Management (ATM). NAVBLUE employs 465 employees spread across the world, with offices in Canada, France, Singapore, Sweden, Thailand, UK and US and representatives in several other countries across the globe.
More info at: www.navblue.aero.