Articles
Name | Author | |
---|---|---|
Case Study: A five year success story together | Dinendra, Deputy Continuing Airworthiness Manager -IT-MRO, Air India | View article |
Column: How I See IT – The death of an icon | Paul Saunders, Solution Manager, Flatirons Solutions | View article |
IATA Paperless Aircraft Maintenance Initiative | Iryna Khomenko, Manager Operational Efficiency, IATA | View article |
Case Study: Endeavor Air: Managing Legacy MRO Systems | Chris Oot, Tech Ops Systems Support Business Manager, and Robert Gatzke, Aircraft Maintenance Programs, Endeavor Air | View article |
Case Study: A five year success story together
Author: Dinendra, Deputy Continuing Airworthiness Manager -IT-MRO, Air India
SubscribeA five year success story together
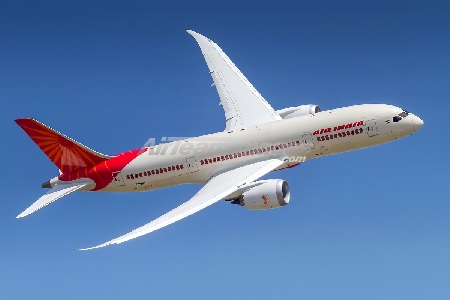
Dinendra B Kadam Deputy Continuing Airworthiness Manager -IT-MRO for Air India offers a case study of how Air India worked with its software vendor to make the most of its MRO IT solution
It’s always a good idea when a software vendor and an airline work together: this article is a success story about Air India and Ramco; working together to generate a great outcome. It’s also about overcoming many problems around mergers and forming a new organization.
ABOUT AIR INDIA
Air India Limited is a Government owned company comprising four airlines formed at different times: from Air India formed in 1932, through Indian Airlines, Alliance Air and, most recently, AIX, formed in 2005. They were all independent airlines owned by the government serving different markets… Air India (international services), Indian Airlines (domestic services), Alliance Air (using smaller aircraft on regional sectors) and AIX (Air India Express) serving the burgeoning low-cost carrier market on both international and domestic sectors. In 2007, all of these airlines were operating under EASA Part M and Part 145 and the government decided that, as a developing economy, the airlines that it owned should undertake all maintenance within India and avoid too many foreign currency transactions.
BUSINESS NEEDS
At the time, all FOUR airlines had their overhaul shops and maintenance facilities at different locations with a mixture of Heavy Maintenance, Line Maintenance, Engine and Component Shops around the country…
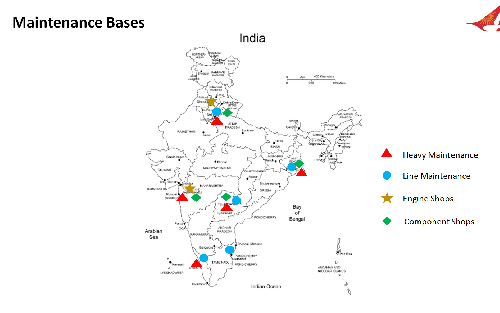
… to serve their various fleets which totaled 133 aircraft (96 of which had an average age of just 6.5 years). Altogether the four airlines were operating about 470 flights per day (including use of the B747-400 aircraft as Prime Ministerial and Presidential transport when needed) with more than 30,000 employees.
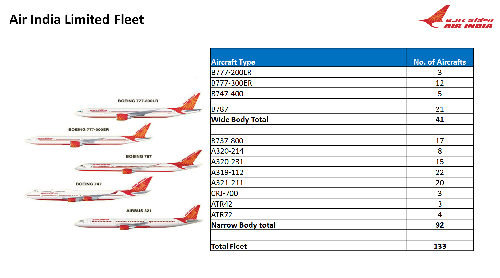
There were facilities in India to repair more than six engine models. Line maintenance was carried out internally wherever possible but, in some cases, outsourced on overseas sectors. The four airlines could undertake heavy maintenance ‘C’ Check, ‘D’ Check in-house.
In 2007, Air India and Indian Airlines were merged as far as operations were concerned, Alliance Air continued with separate operations using smaller aircraft and Air India Express similarly remained a low-fare airline. However, the MRO-engineering functions of all four airlines were merged into a single company ‘Air India Engineering Services Limited’ (AIESL).

IT SYSTEMS
At the same time, management considered replacing the existing maintenance and engineering MRO IT solutions following the merger of the engineering functions of all four airlines. The country was divided into four regions (North, South, East and West) plus a central location in Hyderabad. For the MRO solution, the main objectives were to create a single harmonized platform across all the companies and locations; to increase aircraft availability and utilization; to achieve better and more accurate inventory planning with reduced costs; manage faster rectification of snags for a reduction in TAT (turn-around times); and have increased visibility of parts through all stages of the supply chain.
Harmonizing the processes had to take account of the fact that the culture in each of the companies was different. For instance, whereas Air India was a centralized business, Indian Airlines had been decentralized over four regions. The fleets were also different with Air India using mainly wide body Boeings on its international services while Indian Airlines used mainly narrow body Airbus aircraft for its domestic services. When it came to approvals, Air India had delegated financial power to individuals while Indian Airlines worked through a committee structure. And, finally, on the critical matter of processes; in Air India they were mainly IT driven whereas Indian Airlines had a mixture of IT and manual driven processes.
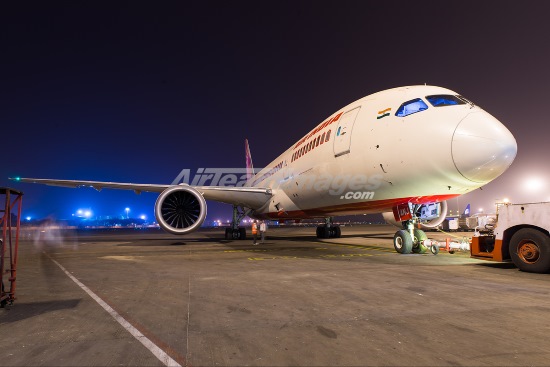
SELECTION PROCESS AND MILESTONES
Once management had decided to introduce new software we started to compile our requirements and to list the shortcomings of the existing system as well as invite ideas from the shop-floor on new requirements. We then undertook a market survey of available solutions including feedback from other airlines and MROs because not only was Air India maintaining its own fleet but was also maintaining engines and aircraft, and conducting line maintenance for the aircraft of other international airlines. Our next step was to draft specifications for what we wanted prior to issuing the RFP (request for proposal). When the proposals were in, we evaluated them all against our technical specification and, for technically acceptable bids, we then considered the commercial aspects of what was on offer.
The next task was to establish a Software Selection Team and, in this, the company demonstrated the seriousness with which it regarded this project with three Board members sitting on the steering committee which comprised:-
- Director- Engineering – Airframe;
- Director- Engineering – Engine & Components;
- Director- Finance;
- Executive Director –IT;
- Executive Director – Materials.
In the working group, as well as the overall project manager, there were expert members from all of the engineering areas that would be impacted by the software change:-
- Project Manager;
- Experts from…
- Quality;
- Maintenance;
- Engine;
- Component;
- Contracts;
- Training;
- Material planning;
- Material Procurement;
- IT;
- Tech Services;
- Production Planning.
Software selection steps
We identified more than thirty vendors of which nine met our technical requirements and, after our commercial evaluation process, three were shortlisted. Those three were invited to make detailed demonstrations of their solutions after which we selected one vendor, Ramco Aviation Solution. Having made our final selection in October 2010, the project was started in December 2010 and we gave ourselves eighteen months to implement the new solution.
SOLUTION SCOPE AND INTERFACES
In January 2011 we started with the business process stories for all four airlines. This was a crucial step because, with representatives from four companies’ engineering, materials and finance functions as well as Ramco, we had to select just one business process that would be acceptable to all four companies. Our MRO IT provider played a very important role in this, demonstrating their application and explaining their clients’ processes which we were comparing with our processes. Finally, after a month, we settled on a single and what we thought was the best aviation standard process. After that, we conducted a classroom pilot project at which the selected process was demonstrated for acceptance and sign off by all four companies.
IMPLEMENTATION CHALLENGES
By April 2011, we had completed the solution definition and started with the User Champion training at multiple locations. This was crucial for a successful change management while moving from disparate systems to one integrated solution.
At the same time, we conducted a country wide executive training program covering system administration and data migration to ensure Air India’s entire Boeing fleet was able to go-live before end of May 2012. Just six months later, on 26th November 2012, the Airbus fleet also went live.
With the Air India Solution Scope (see below) some of the modules, in orange, were not selected by us because we already had solutions which were operational for these modules or were in the process of implementation.
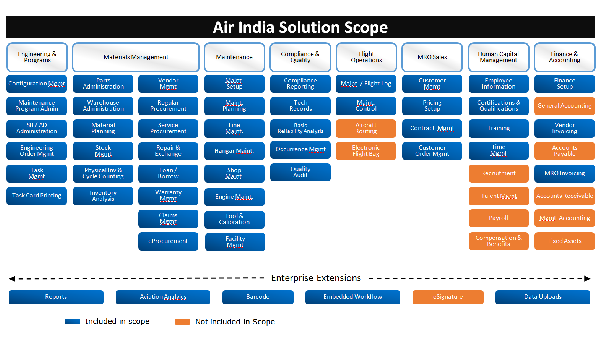
The Ramco solution covered our analytics requirements such as maintenance cost analysis, inventory service level analysis, shop TAT, procurement TAT and customer profitability among others. We also had to manage integration and replacement of existing systems.
Integration
Integration with other systems including Sabre for flight times and routing information; SAP for financials; ESIS for SPEC2000 procurement, Softlink for exports and imports customs clearance and IDMR for technical documentation. Ramco’s MRO suite replaced legacy systems such as Maxi Merlin and Oasis.
Challenges in implementing Ramco
We had to address a number of challenges. Permission from the Regulator required us to convince them that four existing systems could be merged into one solution; it was a difficult task but we needed their permission before starting the project. We took the people with best knowledge of the old systems and the people we had trained on the new system to form the change management team who went to each group to explain what was happening today, what was going to change (and how) and what benefit they would derive from implementing the new system. Data conversion was another challenge with some records in the old systems still on paper, as we have already seen: and then there was the challenge of data migration in which the templates provided by Ramco were a great help. IT infrastructure and meeting the target dates was a further challenge. We also made a parallel decision on company stationery which was to use only A4 size white paper; no more colored paper, no more pre-printed stationery. And we had to manage cutting off the old system which was another challenge because some people, even after change management, were not ready to move to the new system; so we had to draw a line for the change-over. And then, as at the beginning, we had to prove to the regulator the authenticity of the system: our regulator has required a control of two internal audits every year and one external audit every two years.
Overcoming challenges
Challenges were not only in implementing the solution but also extended to rationalizing the human and physical resources in the business. After implementing this solution we have 320 mechanics being trained on the Boeing 787, we have undertaken cross-planning and, with Ramco’s aid, we have started facing the line maintenance challenges. We handle a lot of aircraft for other customers, not only for Air India, so the main challenge was to be cost effective and to have a satisfied customer. In this we were helped through the integration with Sabre: every line maintenance planner or those in charge of the shifts started getting on-screen tasks for and defects on aircraft that would be arriving in the next eight hours, plus the maintenance due on those aircraft. As a result he was in a position to allocate manpower and material. The new system incorporated the skills and qualifications of technicians and mechanics in the system. That also helped our 145 system.
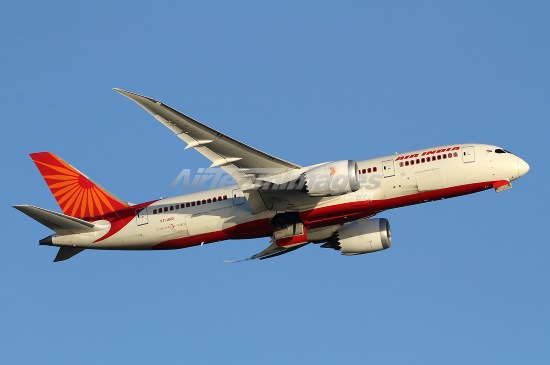
KEY BENEFITS
- Built in process validations ensure that an error free data is maintained in the system.
- Easy visibility of parts and components across fleet types.
- Complete tracking of components across various stores locations, on-wing, vendor repair, shop maintenance, etc. Therefore, easy float reconciliation
- Parts have been distinctly classified into Components, Expendables, Consumables, Raw Materials, Tools and Kits. Components have further been classified into Repairable and Rotable.
- Automated Material Transfers between warehouses based on Ware house Matrix settings & Reorder points
- Seamlessly integrated Engineering, Materials & Finance, enables demand fulfilment and accurate Cost tracking
- Controlled Scrapping Process resulting in efficient Float Management
- Flight Hours and Cycles of aircraft and its components is now readily available as system automatically calculates the same based on actual flying of aircraft thru Journey Logs which is interfaced with their Flight Operations System
- Contract Management System takes care of MRO related work. All the terms & conditions of the contract are defined in the system e.g.: material cost, labour rate, exchange cost, , fixed price / T& M based costing, etc.
- Streamlined Purchase process with reduced lead time using Spec 2000 transmissions for 100+ OEMS/vendors & periodic upload of ATA 200 Vendor Price Catalogue.
- Faster resolution of Receiving Quarantine items and reduction in Overall Procurement TAT.
- Better Part Master Control wrapped with Alternates/ RSPL Information.
- Effective Work Load balancing between the Material Planners & Buyers based BUYER groups and automated multi-level authorizations.
- Simplified Export/Imports management with Customs filing.
Apart from the benefits mentioned above after implementation of the IT MRO system, walls that had previously existed between the group companies were broken and we could utilize resources across the whole merged business.
FUTURE ROAD MAP
- Integration with HUMS
- Reliability Data – SPEC 2000
- Mobility Implementation
- Maintenance and Warehouse Operations
- Digital DFP
- Intelligent Decision making System
- LSAP (Loadable Software Aircraft Parts) Implementation
Contributor’s Details
Dinendra B Kadam
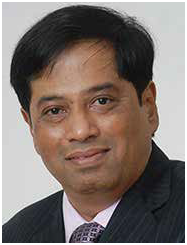
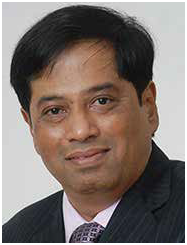
Dinendra is a Deputy Continuing Airworthiness Manager -IT-MRO for Air India. He is a Post Holder approved by D.G.C.A-India and is accountable for the IT-MRO system for the Airline as well the MRO. He has an experience of 28 years in the Continuing Airworthiness Management Organization.
Air India
Air India is the flag carrier airline of India and is owned by Air India Limited, a Government of India enterprise and operates a fleet of Airbus and Boeing aircraft serving domestic and international destinations. Air India became the 27th member of Star Alliance on 11 July 2014 and uses ATR and CRJ aircraft plus the Airbus A319-320 family and Boeing 787 aircraft for selected domestic routes while long distance services use the Boeing 777-300ER, 747 and 787 aircraft.
Comments (0)
There are currently no comments about this article.
To post a comment, please login or subscribe.