Articles
Name | Author | |
---|---|---|
Be ready for GDPR | Sander de Bree, Founder and CEO of EXSYN Aviation Solutions | View article |
A new way of looking at and managing pre-maintenance data Part 2 | Steve Sayers, Director of Technical Publications, FLYdocs | View article |
Paper to Data — Data to Dollars Part 2 | Rob Saunders, Consultant, Aircraft IT | View article |
New technologies and Blockchain | Mathieu Gimenez, Innovator at the MRO Lab Singapore, Air France Industries KLM Engineering & Maintenance (AFI KLM E&M) | View article |
Digital twins, AI, mobile apps and drones | Mark Martin, Director, Operator Edition Product Line, Aviation & Defense Business Unit, IFS | View article |
A new way of looking at and managing pre-maintenance data Part 2
Author: Steve Sayers, Director of Technical Publications, FLYdocs
SubscribeA new way of looking at and managing pre-maintenance data Part 2
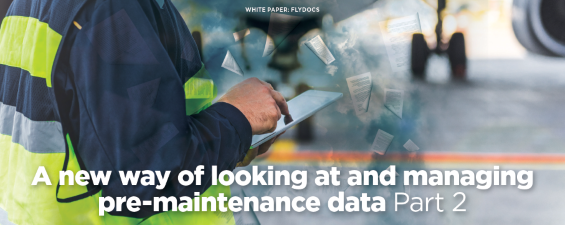
Every airline or aircraft operator needs maintenance data for their aircraft; however, when the data comes from different sources and is presented in different formats, this process becomes unnecessarily complicated. Steve Sayers, Director of Technical Publications, FLYdocs
In part 1 of this article, we considered pre-maintenance data: what it is, how it’s used, and how it’s organized and categorized. We also looked at some of the problems of digitized maintenance data, the difficulties of having to use different systems to access/use pre-maintenance data supplied from the OEMs and briefly suggested how that might be overcome using a digital document management solution like FLYdocs. In this second part of the article, we’ll look more carefully into the problems of incompatibility between systems, where and how airlines and operators are already managing that data, where and why they cannot do so and some ideas as to how this could be resolved.
THE OPPORTUNITY TO IMPROVE MANAGEMENT AND CONTROL OF PRE-MAINTENANCE DATA
This is really about management and control of the data outside of the OEM’s environment, i.e. within the airline or operator’s location and systems. However, there are different requirements with regards to how long data is held. A good example is from the operator’s point of view; in some situations, there is a regulatory requirement to keep 36 months of pre-maintenance data archived. This does not refer to post maintenance data; as stated previously, this has to be kept for the life of the aircraft.
For example, Boeing and Airbus operate different revision schedules. Boeing data is revised monthly and quarterly (depending on fleet type), and Airbus revise four times a year. This means airlines and operators are constantly managing new revisions of data and having to maintain extra IT capacity solely to archive all this data.
Some of the reasons for the 36-month archive are below:
- As part of the investigation process following an aircraft incident, the relevant AAIB (Air Accident Investigation Board) would need to review all maintenance work, servicing and repairs that have been carried out on the aircraft. This investigation could go back to the last heavy maintenance check that the aircraft underwent, which could have been 36 months prior (some aircraft undergo heavy maintenance checks every three years).
- Also, at the lease return of an aircraft, the airline or operator must be able to show the versions of certain manuals that were used to carry out specific maintenance tasks or servicing requirements. This is particularly relevant when reviewing the damage/repair status of the aircraft. In some circumstances, if a permanent repair has been applied to an aircraft, it stays for the life of the aircraft, so access to older versions of SRMs are required. These repairs could have been applied several years earlier to a much older version of SRM.
- The OEMs can provide specific earlier revisions of requested data but at a cost to the airline. Therefore, the obligation is on the airline or operator to keep and manage their own archives.
Having all previous OEM versions of data (by fleet type) available and managed offline would make the returns process for airlines and operators, (particularly mixed fleet operations), much easier and reduce the costs and timelines of having to rely on the OEMs for support.
The data archive service is an opportunity that we are reviewing at FLYdocs and which could be offered as a subscription service offering in which:
- The airline or operator subscribes to a full revision managed database of all relevant manuals – archived, managed and controlled offline by FLYdocs.
- Alternatively, the airline or operator has the ability to upload and manage their own database/archive within the FLYdocs system.
Both options could provide a relevant revision management process that would synchronise version uploads in-line with the OEMs revision schedules and auto archive the old revisions, and in turn notify the users that new versions of data are available. Access to the old archived data would be controlled.
CURRENT BLOCKS TO OBTAINING/STORING/USING PRE-MAINTENANCE DATA
The real block for any independent solution provider would be getting access to OEM data. It is, in one sense, understandable because the OEMs do not want their data to be available to companies or third parties who do not own or operate aircraft, lessors of course being the exception.
OEM data is only available through an annual subscription process and is a good revenue opportunity for them. Also, it is their proprietary data, i.e. it’s the OEM’s design data, which they understandably are not going to provide as a free of cost (FOC) option and that they also take every precaution to safeguard.
Airlines and operators do have the ability to allocate ‘third party access’ to their pre-maintenance data through the OEM applications, as long as all parties have signed into the relevant third party data access contracts. These data access contracts provide ‘read only’ access, and any amendments and/or updates would have to be initiated by the pre-maintenance data owner.
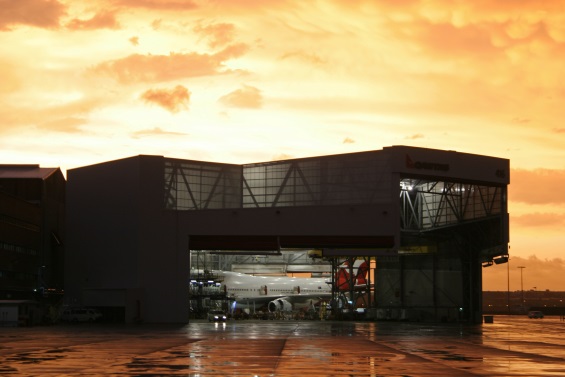
PROCESS CHANGES THAT UNIFIED PRE-MAINTENANCE DATA WOULD REQUIRE OR BRING ABOUT
Looking first at the OEM data; they have processes that airlines and operators have to follow, i.e. the specific platforms the data has to be accessed from and the actual data download/transfer processes. But looking at pre-maintenance data created in-house by the airlines and operators (see Part 1 of this article), there are opportunities. Again, I will refer to FLYdocs here as a potential answer because I am familiar with the embedded existing workflows and the data management processes within the system, and the way they work. The FLYdocs workflows could be used to cover the multiple processes required to enable airlines/operators to not only create and access their own data, but also potentially be used to view and access all pre-maintenance data (even OEM generated). This would be a real step forward.
The biggest opportunity and potentially the best area to start, would be the internal documentation that all airlines create. Nearly all internally created documentation has to pass through several phases of checking and authorisation before final release. In some cases, this documentation is only required for a specific amount of time, i.e. has to be reviewed within a certain time frame from the point of creation to see if it is still relevant and/or current. The time intervals for reviewing can be internally set.
In most cases the process of creating, reviewing and authorising, as well as the further requirement of a date review for relevance and effectiveness, is probably handled through multiple systems or databases and can be very time consuming. There will always be a requirement for this type of temporary documentation, whether it is tackling an airline/operator requirement or if it is addressing errors or ambiguity within OEM created manuals or documents. An example could be a missing or incorrect step within an AMM (Aircraft Maintenance Manual) maintenance procedure. Even though the OEMs test and prove their documentation, there are still occurrences of the above situation arising. In this case the airline would raise a Tech Request or a Service Request with the relevant OEM, which, if agreed, might result in a manual change at some point in the future. Typically changes like these can take six to nine months or longer to be fully implemented into the pre-maintenance data sets. In the meantime, the airline or operator issues a document often called a TB (Technical Bulletin or Temporary Bulletin) under their Part 21 approval, which allows them to create this type of document to provide engineers with the relevant information until the OEM update is available.
From an airline or operator’s point of view, all their internal documentation and data that is created for pre-maintenance and subsequently linked to post maintenance records can all be created, authorised, accessed, managed and controlled through the workflow processes that are currently within systems like FLYdocs, for instance; where automation and robust workflows could remove the requirement of multiple other systems.
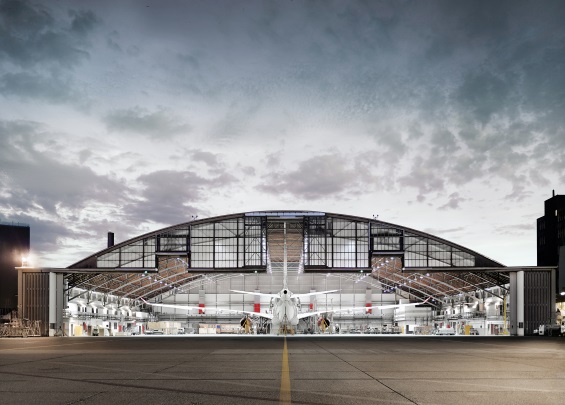
CONCLUSION
Although OEMs work to the relevant ATA chapters and principles, e.g. S1000D authoring standards, they present this information in different formats and in different ways. To be able to display and access numerous documents in a standardised format and having hyperlinks from the pre-maintenance to the post maintenance (relevant records) would be of real benefit; a benefit that modern digital documentation systems can provide. For multi-fleet airlines and operators, (which most of them are today), it is frustrating having to ‘dip’ in and out of different OEM systems and databases that present and format the same data in different ways.
The digital age and the use of digital data and documentation has provided the aviation industry with opportunities that only a few years ago were not achievable. Now, as mobile technology becomes something we use every day, new opportunities arise. It’s a very exciting time to be involved in the industry as there’s currently no end in sight to where the digital story will go, or to what is going to happen next. In the past, it’s sometimes taken a while for the technology to catch up but now there is an opportunity to give people the data they want at the point where they want it; an ethos that drives and motivate us at FLYdocs.
Contributor’s Details
Steve Sayers
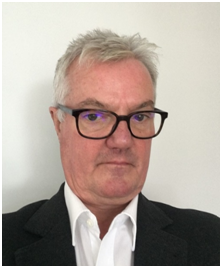
Before joining FLYdocs in 2017 as Director of Technical Publications, Steve’s career spanned 35 years in aviation; 24 years within production of military aircraft with BAE Systems followed by 11 years in commercial aviation with Virgin Atlantic Airways, where he held the role of Information Services Manager. In his current role, Steve is responsible for identifying and developing opportunities to enhance the capability of FLYdocs, for example, by creating, managing and controlling pre-maintenance data and documentation and to provide FLYdocs’ clients with a seamless end to end process for all their documentation needs and requirements.
FLYdocs
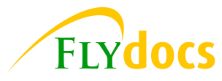
Comments (0)
There are currently no comments about this article.
To post a comment, please login or subscribe.