Articles
Name | Author | |
---|---|---|
Case Study: MATMen – In-House Solution for Supply Chain Optimization | Petr Barton, Inventory Manager, Travel Service a.s. | View article |
Case Study: A digital future for Air Evac | Tammie Bethel, Records Specialist, Air Evac | View article |
Case Study: Achieving a Continuous Compliance Culture at Southwest Airlines | Don Tilden, Director of Central Publications, Southwest Airlines and John Zawlocki, Fleet Solution Manager, Flatirons Solutions | View article |
Case Study: Achieving a Continuous Compliance Culture at Southwest Airlines
Author: Don Tilden, Director of Central Publications, Southwest Airlines and John Zawlocki, Fleet Solution Manager, Flatirons Solutions
SubscribeAchieving a Continuous Compliance Culture at Southwest Airlines
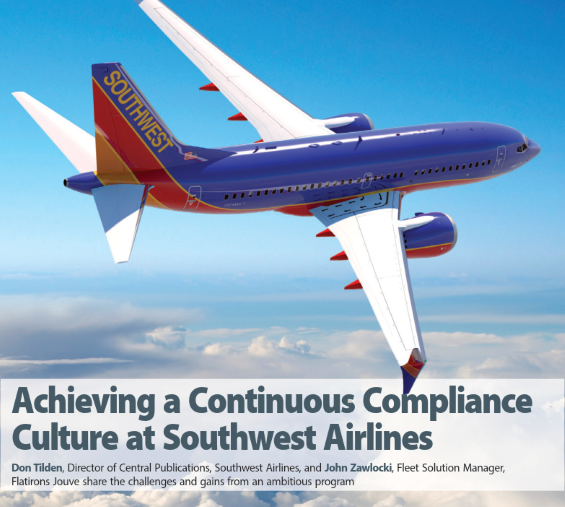
Don Tilden, Director of Central Publications, Southwest Airlines and John Zawlocki, Fleet Solution Manager, Flatirons Solutions share the challenges and gains from an ambitious program
THE EVOLUTION OF SAFETY
Before diving into the main article, we thought that readers would find it useful to look at the evolution of safety and the challenges of compliance management.
How drivers and perceptions of safety have changed
As safety has become an increasingly important element in aviation, it has been through three primary distinct, but not exclusive eras (Figure 1).
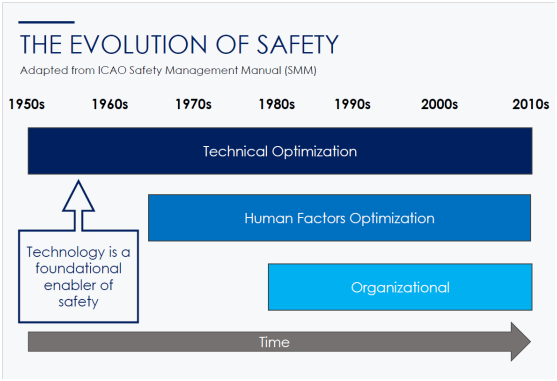
Figure 1
The technical era in the early period of aviation focused on the machine and its operation in a reactive process based on failures and accident analyses, learning lessons after the event and making improvements accordingly. Those analyses drove considerable improvements in technology and were the basis of many much-needed regulations to enhance safety.
As safety continued to improve, the focus shifted to the human factors optimization based on the study of the interface between man and the machine; also focusing on causes and preventative measures to avoid human factor errors. Certainly a lot of time and effort was put into that. But despite that considerable investment, human performance continued to play a key role in accidents.
To address this, focus shifted to the roles that organizations played in the safety process. The consequent organizational era, much of which will be the basis for this article, specifically looked at and considered the impact of the organizational culture, its policies, and their effect on safety. As an outcome, many processes today require proactive collection of data to monitor known safety risks as well as stay ahead of and identify potential risks.
The challenges of compliance management
As regulations have evolved and operators are faced with considerable compliance requirements, responsibilities and challenges have also arisen. Among those are the vast number of regulations from multiple agencies and sources. Regulations get translated into company policy which, in turn, is authored and put into procedures which then become content for multiple manuals, linked together so that, when one changes, it affects a policy or procedure in another location (Figure 2).
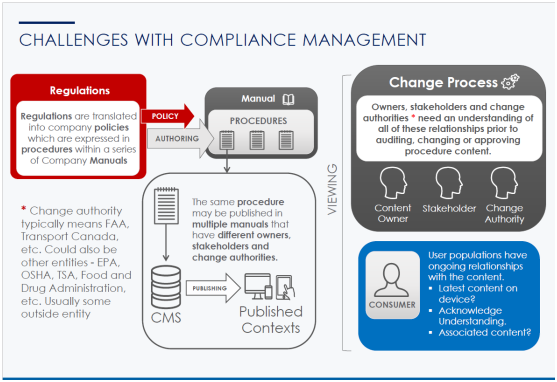
Figure 2
The greatest challenge for manual owners, stakeholders, and regulators is the need for a clear picture of all these relationships prior to auditing, changing, or approving the content in order to avoid any potential non-compliance issues.
With hundreds of documents, manuals, and stakeholders in the organization as well as regulatory bodies, the process can seem daunting. To help us understand how these challenges can be overcome, we’d like to share an overview of how a culture of continuous compliance has been developed at Southwest Airlines.
ACHIEVING CONTINUOUS COMPLIANCE AT SOUTHWEST AIRLINES
Setting the scene
To start, we thought some context would be useful. The Central Publications department publishes all the manuals that Southwest Airlines authors, concerned not only with the technical content, but also with the interfaces. In early 2009, Southwest brought together the various writers generating manuals in their different ‘silos’ into a single department. They were all ‘put in a room’ under unified leadership and the airline charged them with creating standards and consistency across the manual series as well as focusing on the bigger picture of regulations with the continuous compliance culture in mind. The objective was to make Southwest’s manuals the vehicle with which the airline runs its regulatory compliance. There are three things that matter about the manuals:
- They are referred to by the users to do their job;
- They’re also used as training aids;
- More important, they are the vehicle through which the airline is inspected.
It’s not acceptable to have a hodge-podge of answers to regulatory questions: somewhere in the manuals it has to overtly be a part of the context, something that has changed at Southwest over the last eight years.
Tagging the correct answer to the right question
Placing tags in a manual is just as important as editing the words and graphics. Tagging any element as the answer to a regulatory question is an authoring act and is just as important as changing words in a flying procedure. It’s important to be able to say that ‘for this regulatory question; this statement is the answer.’ Southwest takes this very seriously in the authoring process.
Finally, and the reason for this article, is that for Southwest Airlines compliance is not about inspection, nor is it about the FAA quarterly surveillance schedule; it is about being compliant all the time. At any given moment, a user should be able to go into a manual with the confidence that those manuals are fully compliant, and that all regulations are met. That’s not the same as ensuring that every employee is doing the right thing by all the manuals, that’s a line management responsibility; the task of Central Publications is to make sure that those manuals are always right up-to-date and correct.
Along with every airline in the United States, Southwest is required to have a Safety Management System (SMS) at the very heart of any operational change that might introduce a hazard – instituting a new system, investigating a new procedure, installing new software… whatever it is, the airline must be sure that it’s not going to impact adversely on safety, add a new hazard, or require mitigation. Southwest uses the manual system to ensure that when that process of checking out and making sure that any change is not introducing a new hazard is complete, the manual authoring system is used to make sure that the facts have been documented including that there are no new hazards.
Southwest Airlines also tags the procedures and the controls so that compliance documents can be produced from the manuals and the airline doesn’t need a secondary piece of software to perform audits. The answers to people’s compliance questions are pulled directly from the manuals.
The manual is paramount
The rule at Southwest Airlines is, ‘If it isn’t written in the manual, it doesn’t exist’. Someone’s own cheat sheet for a particular job is no good: it isn’t documentation and it doesn’t work for regulatory compliance. Many years ago, that was an issue for Southwest: everybody knew what to do but it wasn’t written down in a form that would satisfy a regulatory inspection. So that had to be addressed, which lead to the rule above.
Content doesn’t need to be in every manual, and Southwest has instituted more rigorous processes around some handbooks, but they still have regimentation, and they still exist with version control as part of the manual system. So, to extend our rule: ‘If it doesn’t exist in a manual, it doesn’t exist because it can’t be inspected.’
ADDRESSING SMS REQUIREMENTS – USE OF TAGS
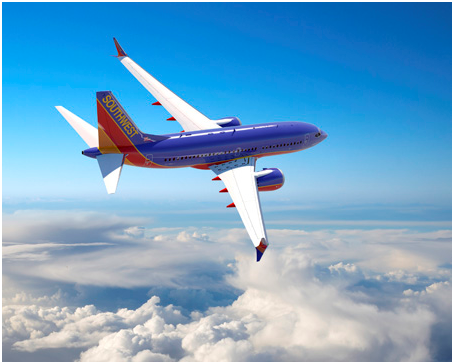
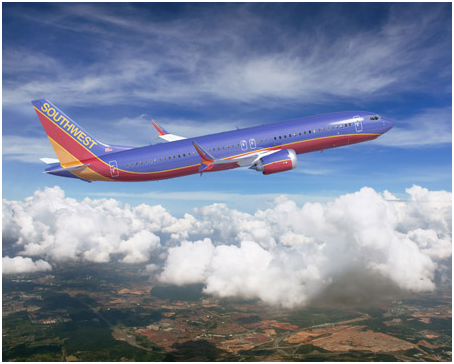
All risk has to be assessed these days for any new implementation. Whether that’s a new piece of software, a new tool, or, as in the case of Southwest, a new airplane: the airline will be introducing the Boeing 737 MAX very soon. Southwest has examined possible hazards and the residual level of risk in order to put controls in place within the new or modified systems. Some are engineered controls; some are procedural, such as checklists. The bottom line is that Southwest leadership, front-line employees, and the FAA need look no further than the manuals to verify compliance.
A shared understanding
As we have alluded to already, Southwest Airlines has a system that controls the authoring process which is the last step in change leadership. The process ensures that the department that owns the procedure really owns the change; that it has been properly coordinated across the different departments; and that the change has been made everywhere required across the manual system. By example, if the way in which an aircraft is moved from the hangar back into service is changed, everyone involved – from engineering to flight operations to ground operations – needs to know about that change. Even though the words for each of them do not have to be exactly the same, they must not contradict each other. Southwest has made this a key action; that different people involved in a procedure get together and agree on language so as to stay in sync. It seems small, but it’s been a pretty big achievement.
Follow up
Another thing that SMS requires is that any revisions or changes must be taken up the leadership chain when there’s a hazard identified so that the accountable executive actually gets to see the change and is really aware of what is going on with the alteration and where the residual risk is. SMS also requires that the business periodically returns to the case to ensure that everything that should happen really is happening; also, after some months, to confirm whether, with the benefit of experience, the change was the right thing to do and whether it is having the intended effect in the system.
Document everything
Finally, it’s important to make sure that everything is completely documented; not only the fact that certain words in the manual have changed but also ‘how did we get here; what research did we do; what is the risk associated with the change; and how was it determined that any new controls will work as intended?’ That’s what a continuous compliance culture is: looking at the current state, where you want to be, and how you are going to get there. You aren’t done until it is all fully documented so that it’s possible to go back and make adjustments.
One of the ways that Southwest documents change with the help of Flatirons is by inserting mark-up using a drop-down (see right side of Figure 3) that the airline’s authors use to tag various elements in the manuals. It’s that straightforward and it must be done at the same time as a part of authoring, not after the fact, but as an integral part of the authoring process.
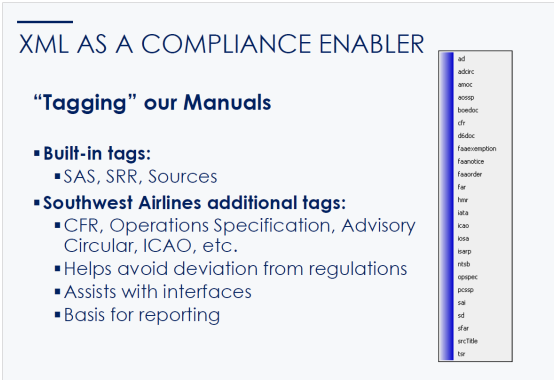
Figure 3
So the new SAS (Safety Assurance System) questions and answers will be a part of the mark-up, there are some examples below, but Southwest has also done a lot with additional tags to meet a variety of needs. Also, specific regulatory references have to be marked so that users can search for them. Any of the tags in Figure 3 can also be reported on. So, if someone is interested in how Southwest meets the requirements of any regulation, it’s possible to go into the system and search on those aspects of that regulation.
It furthermore assists with interfaces; if the user wants to see, for example, across manuals how to deal with the training of crew members, they can search for that tagged content across the manuals. The system not only assists with interfaces but is also the basis of Southwest’s reporting. And that’s what is at the very heart of this article: at any given moment we want to be able to produce a report directly from our manuals that shows we are compliant. Southwest has many different tags used throughout the manuals system, including some that are visible to end users all the time. And then there are other cases when the airline doesn’t want the tags to be shown to avoid cluttering the manual with information that users don’t need in order to properly perform their jobs.
Making things clear
There are times when someone is performing a leadership function and they need to know that a procedure is a safety control and a regulatory requirement; Southwest uses a check-mark to indicate a control in their manuals. Control mark-up can be shown in the output, whether HTML or PDF.
Safety Management System (SMS) reporting is essential now that Southwest is completing the process of being certified and the FAA is validating the content in the manuals. Reports are produced for the FAA, particularly for 14 CFR Part 5 and, additionally, Southwest is converting SAI tags to SAS tags. The system is being used for SMS reporting so that when the FAA asks how requirements are being met, it’s possible to easily pull up the reports because the manuals have been properly tagged.
SOME EXAMPLES FROM SOUTWEST AIRLINES
Training Flight Crew
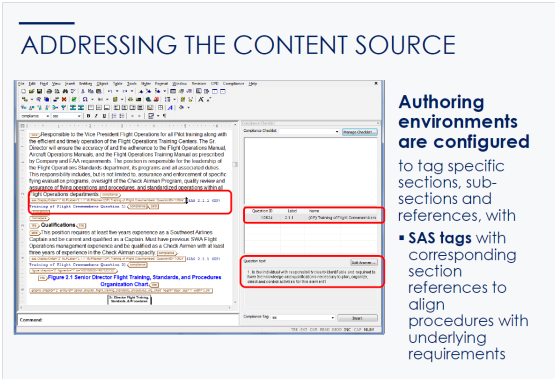
Figure 4
Figure 4 is an example of how Southwest answers the question concerning the training of flight crew members, specifically, ‘is the individual responsible for the training required to have the knowledge and qualifications?’ Not only does the tagging help when producing a report, but it is also tied to that person’s job description so that Southwest will never hire a person to fill that role who doesn’t meet the requirements of the regulation.
Training Cabin Crew
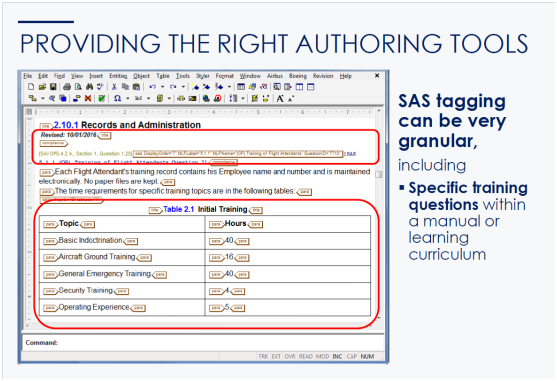
Figure 5
Figure 5 is another example that illustrates how granular tagging can be with a question that deals with how specific training requirements are met.
Records Retention
Another big requirement at Southwest is records retention (Figure 6).
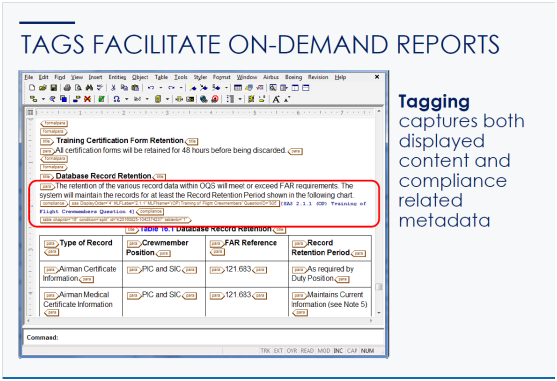
Figure 6
There are some flight papers that must be kept for 30 or 90 days and there are other training requirements that must be kept as long as that crew member is in the airline. So, throughout Southwest Airlines’ manuals, record retention requirements are tagged to make reporting possible.
Where this is all leading to is the fact that an on-demand report can be produced concerning any of the given topics mentioned above. This helps the airline promote the compliance culture because the manual that’s in front of the person shows regulatory compliance standards.
CONTINUOUS COMPLIANCE
Our next illustration in Figure 7 offers an example of what continuous compliance looks like using the example of ‘Training of Flight Crew Members’.
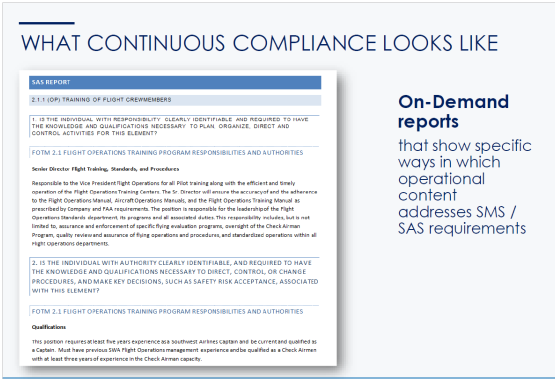
Figure 7
This reporting addresses questions that will often arise during an inspection, such as: ‘How do you train your flight crew members?’ and ‘Do you meet all the requirements of the regulations?’
However, all of this tagging doesn’t mean anything unless you can report on it. Even at a very small level, let’s say we’re going to make a change to a piece of content that affects a question. It’s possible to pull the report on it before we ever start changing and ask, ‘what is it that the manual says now?’ Then, after the change has been made, the report can be pulled again to ask, ‘what is it that we’ve done, and are we still compliant with the regulation?’
As mentioned above, Southwest treats tagging as the means to make sure that they have the proper answer at their fingertips.
Here’s an example (Figure 8) of a question that has lots of different answers.
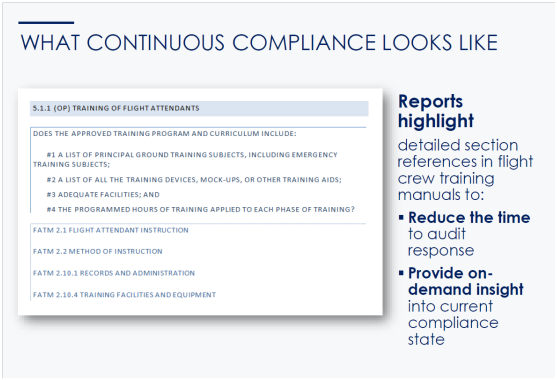
Figure 8
Sometimes an answer is as simple as ‘it’s a single question so we’ll find a single answer in a single paragraph.’ But this is a question that talks about lists of training subjects, how they’re done; you also have to show all your training devices or locations and certifications. This is an example of a question that has lots of different sections that answer those questions. It leads users down the path that, if they wish to change a question that deals with the curriculum, it is necessary to first look at the four individual references in the same manual to make sure that they properly and completely answer the question. In the past, sometimes people fooled themselves, they would find the first answer and, even though it might not have been a perfect answer, they’d stop inspecting themselves and stop reading. Nowadays it is realized that we have to positively search the manuals and make sure that we don’t have contradicting references and that the references used have answered the question completely so that, if someone goes back in to change it later, it will be possible to effect that change in all the different places to avoid elements of different answers from different time periods. Readers will know that different manuals can get to look as if different authors wrote them over time; you’ll find certain sections have been written with a particular voice and a certain completeness. Another manual might be written completely differently from a regulatory perspective and it’s been cut and pasted from a regulation. It’s important to make sure that all those different sections agree with each other and this is a method to do that.
IN CONCLUSION
One important point that we’ve touched on here has been the variety of different regulations with which airlines must comply. Compliance reporting visibility means addressing multiple regulated business dimensions from wages and labor, to financial regulations, to food safety, alcohol, security, EPA, environmental, flight operations… all these things have to be factored in.
At the heart of a continuous compliance culture are dedicated professionals, such as the team at Southwest Airlines, aided by technology that can minimize the human factor risk as the evolution of safety continues. The days of managing via spreadsheets and the like are ineffective with traps just waiting for the unwary. By using technology to minimize the possibility of human error, replacing that human input with trackable tagging, it’s possible to improve efficiency by retaining tags from revision to revision. If the question exists, it can be tagged in various manuals so that, as a manual evolves, as it is revised, that tag stays with it unless the user decides to change it or if there’s a significant departure from that.
One of the more exciting things is using alerts to notify stakeholders; so, if a chief pilot has concerns about three or four sections in a manual, there will be an automatic alert through the workflow system that tells users that someone is attempting to change a procedure in manual A that affects that stakeholder’s use of manual B, C, or D. Approval authority is built directly into the workflow system so that only certain people can approve changes to particular elements of content.
The important message is that the solution at Southwest offers peace of mind that the airline will be in a constant state of compliance. At short notice, the airline is able to generate reporting that gives assurance both to the leadership in the business and the regulators that the airline is in compliance with a particular requirement. The hope is to reduce airlines’ overall exposure to compliance issues now and in the future.
Contributor’s Details
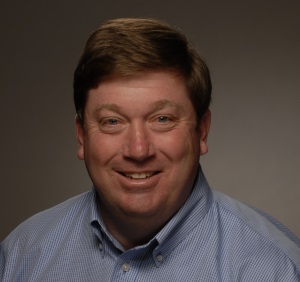
Don Tilden
Don is the Director of Central Publications at Southwest Airlines. His department edits and publishes all company-authored manuals and is responsible for electronic distribution of more than 100 manuals and documents. He started his career in the US Air Force authoring Manuals for the EC-130H, then served as a Senior Research Associate and Lecturer at Embry-Riddle Aeronautical University before Northwest Airlines and Champion Air. Don holds a Master of Science in Aeronautics as well as undergraduate degrees in Aeronautics, Communications, and Human Resource Management.
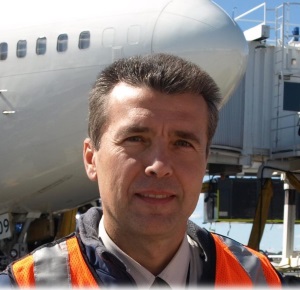
John Zawlocki
John Zawlocki is the Solution Manager responsible for guiding the evolution of the Flatirons Fleet Solution. John’s responsibilities include close coordination with customers, prospects, technology partners, and aviation leaders to define the solution’s investment priorities and long-term roadmap. Prior to joining Flatirons, John held key positions in Engineering, Reliability, and Design at companies like Delta Air Lines, Northwest Airlines, and Northrop Grumman. John is passionate about the business of aviation.

Southwest Airlines
Southwest Airlines Co. is the world’s largest low-cost carrier, headquartered in Dallas, Texas. As of December 2016, Southwest Airlines had scheduled services to 101 destinations in the United States and eight additional countries. Southwest is the largest operator of the Boeing 737 worldwide, with over 700 in service, each averaging six flights per day.
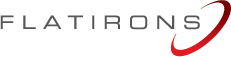
Flatirons Solutions
Flatirons Solutions provides consulting, technology, and outsourcing for content lifecycle management. Its customer engagements help organizations efficiently deliver the right information, at the right time, to the right people by leveraging structured content and digital media — Turning Content into Knowledge®.
Comments (0)
There are currently no comments about this article.
To post a comment, please login or subscribe.