Articles
Name | Author |
---|
Aircraft Performance Monitoring at Wizz Air
Author: Jaime Romero Waldhorn, Fuel Efficiency Manager, Wizz Air
SubscribeJaime Romero Waldhorn, Fuel Efficiency Manager at Wizz Air shares Wizz Air’s experience of using an advanced aircraft performance monitoring solution to increase efficiency.
Many fuel efficiency initiatives are dependent on the accuracy of flight planning and Flight Management System predictions. The accuracy of these systems depends on aircraft performance deterioration level which indicates by how much actual aircraft fuel consumption differs from its baseline model at any given point in time.
Every aircraft has different in-flight performance. Differences originate mainly from engine deterioration, but also from maintenance quality, installation of performance improvement packages or just the manufacturer’s production quality. Accurate monitoring and application of performance deterioration factors enable these differences to be turned into emission savings.
To understand how it works, let’s start with some facts. For each aircraft type, manufacturers publish associated performance models. These models play a fundamental role in Flight Planning and Flight Path optimization. They are being used in:
- Flight Planning System:
- Calculation of OFP (Operational Flight Plan) fuel figures;
- Calculation of the lowest cost trajectory.
- Flight Management System:
- Calculation of economic speed
- Calculation of Optimum Flight Level;
- Calculation of FMS descent path (for Airbus aircraft known as IDLE factor);
- Calculation of FMS fuel figures (EFOB).
Performance models are built for each given aircraft type. As every aircraft in the fleet burns a different amount of fuel, we need a way to represent the performance of each tail. This is done through the use of Aircraft Performance Monitoring (APM), by biasing aircraft performance model using actual observations. As a result, Flight Planning and FMS predictions are more precise. Increased precision translates directly into emission savings. Regarding OFP fuel figures, savings are also indirect as more accurate fuel figures translates into less overburns – less flights in which actual fuel burn was higher than planned. This increases pilots’ trust in planned fuel figures and thus they tend to take less extra fuel on board. Summing up, safe overburns (underburns) are key in the reduction of captain’s discretionary fuel.
APM output is also used in Aircraft Information Management Systems for the purpose of supporting tail-assignment. Until 2019 Wizz Air Flight Operations followed a legacy APM process, which required significant manual workload and in which precision was far from ideal. We spent most of the time preparing and processing the data, with not much time left for analyzing trends and results and the impact they had for our operations.
Another drawback was that the updating of performance factors took place every month or quarter depending on standard deviation of results. Such lengthy intervals result in fuel penalties related to planning too much fuel until the new performance factor is available (for example fuel burn of the aircraft might significantly decrease due to engine change). As a result, in order to cater with cases where large differences in deterioration occurred, there was no other way than to apply a rounding-up policy. Otherwise, aircraft could fly for extended periods with a too low performance factor.
In 2019 Wizz Air established a long-term cooperation with StorkJet, which supports airlines in aircraft performance monitoring and fuel efficiency optimization. Their solution named ‘AdvancedAPM’ resolves the issues described above and fits much better into Wizz Air’s vision. . With help of Advanced-APM, Wizz Air performance monitoring process is now:
- Fully automatic, requiring only analytical workload on Flight Ops side;
- Precise, with daily resolution and low scatter of the results;
- Independent from aircraft and engine manufacturers;
- Includes all flight phases;
- Much more advanced – including over 60 charts related to aircraft performance and diagnostics aspects;
- Includes IDLE factor.
Instead of obsolete ACMS reports, AdvancedAPM uses wireless QAR (Quick Access Recorder) data which records ~20x more flight data at higher precision and frequency. A proof-of-concept performed on historical data indicated significant improvements in monitoring precision. Increased resolution and level of precision connected with diagnostics data enabled us to more accurately identify what was the root cause of performance deterioration. In some cases, maintenance actions were performed, recovering some of aircraft performance.
Example below (Figure 1) presents total deterioration (blue line), airframe deterioration (orange line) and both engines deterioration (green line) over time. In SEP 2019 Wizz Air performed both engine changes, which resulted in decreasing engine deterioration from 2% to 0.7% and total deterioration from 3.5% to 2.4%. With daily resolution we are able to see change in performance just after maintenance action.
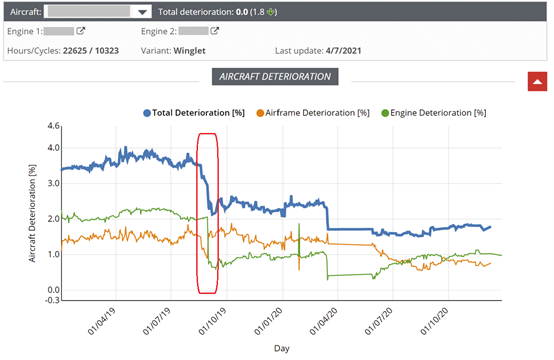
On another example (Figure 2) we can see that total deterioration (blue line) increased from 2,7% to 3,6%.
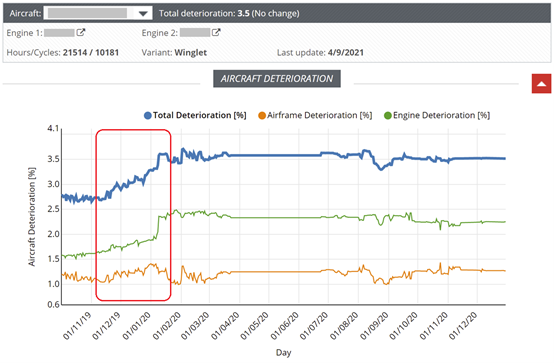
Looking into details, it turned out that the increased degradation was caused by sudden jump in engine 2 deterioration (figure 3).
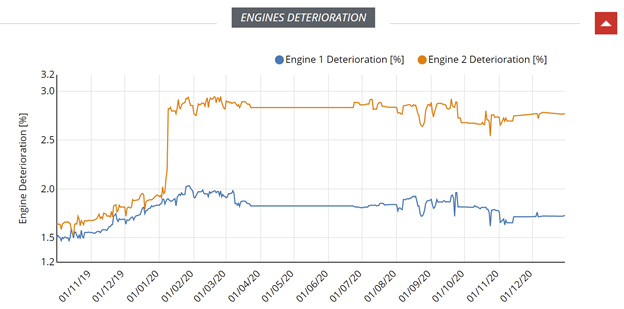
AdvancedAPM also offers a diagnostics module, which is helpful in independent monitoring of engine performance after shop visit or other maintenance actions. The example below (Figures 4 and 5) shows one of PW-1127GA shop visits. The correlation between EGT (Exhaust Gas Temperature) and Engine deterioration is clearly visible.
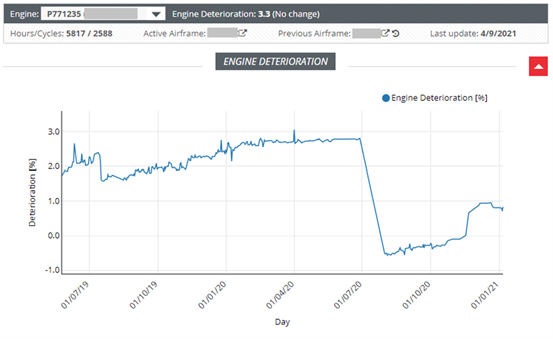
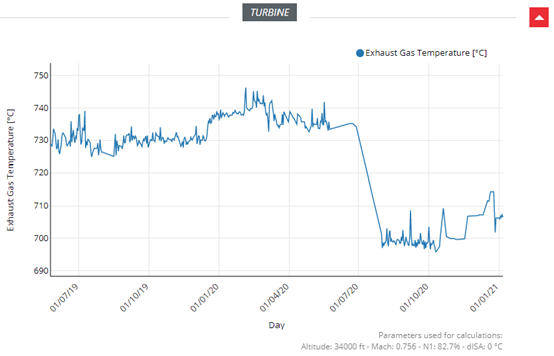
Such changes are immediately picked up by AdvancedAPM. With automatic alerting, Wizz Air can immediately react to increased degradation and work on corrective actions. The software gives us the possibility to monitor over 60 engine and airframe parameters related to aircraft performance (deflection of ailerons, spoiler, elevator, divergence of N1 or TAT/CAS and much more).
Wizz Air also applies advancedAPM IDLE Factors for accurate computation of the FMS descent profiles. The aim of the IDLE factor is to adjust the FMS performance model such that actual descent can be performed at IDLE thrust from Top of Descent until final approach. IDLE factors are especially important on descents to low congestion airports.
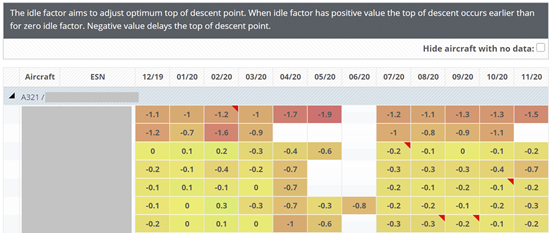
What is more, StorkJet provided Wizz Air with a study describing Descent Profile Optimization which clearly indicated saving potential and all the correlations that might have impact on savings.
Summing up, actual aircraft performance is the key in flight path optimization, reduction of overburns and proper fleet assignment. With AdvancedAPM Wizz Air’s analytical team can focus on data analysis instead of data processing. All of that results in fuel savings and reduction of CO2 emissions.
Contributor’s Details
Jaime Romero Wald
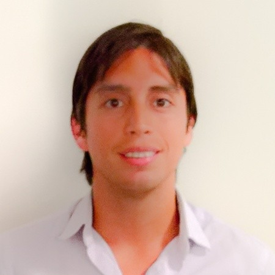
Jaime Romero Waldhorn, Fuel Efficiency Manager at Wizz Air. He has a master’s degree in Traffic and Transport from the TU Darmstadt in Germany and over eight years of experience in the airline industry. Since 2018 he has been part of Wizz Air and starting in 2020, he joined the Flight Operations team, being in charge of introducing and monitoring fuel efficiency initiatives.
Wizz Air
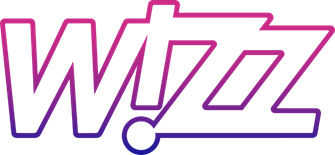
Wizz Air is a European ultra-low-cost (ULC) airline with its head office in Budapest. The airline serves many cities across Europe, as well as some destinations in North Africa and the Middle East. With over 130 aircraft across several types from the Airbus A320 family, it currently serves 70 destinations in 44 countries.
StorkJet
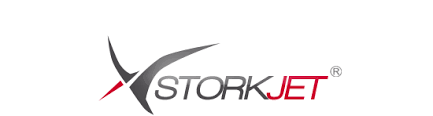
StorkJet is the expert in aircraft performance and fuel efficiency based on real flight data, supporting airlines through revealing new saving potentials and optimizing flight operations. Airlines use StorkJet’s software to track over 30 fuel initiatives, monitor the performance of each aircraft in the fleet and engage pilots to be more eco-friendly.
Comments (0)
There are currently no comments about this article.
To post a comment, please login or subscribe.