So that’s why mechanics need mobility but what about the other side of the coin, what can mechanics do on tablets? For this, Blair highlighted a pretty good list of functions and benefits, explaining mechanics can get to their manuals using ‘My tasks’ Even if they’re sitting in a fast-food restaurant, the tablet will ring indicating that they have an assignment and at what gate. On arrival at the specified gate, the tablet indicates exactly what has to be done to the airplane as well as what has been done in the past. The tablet can also acknowledge when the mechanic is at the plane and tell Ops group that he’s there. He can even use the tablet to delay the boarding procedure if the floor boards have to be pulled and, at the end of the job, he can use the tablet to close the maintenance task and go to the next plane. In short, using tablets keeps mechanics moving directly from one plane to the next so they don’t lose time going back and forth getting assignments and information to perform tasks.
Blair added that AA has 1,200 CMMs (component maintenance manuals) digitized and online so mechanics can hook into information for multiple fleets live plus there are offline capabilities.
But over and above the functions and benefits, Blair wanted to add, “We’ve come pretty close to perfecting how you’d want a mechanic to use tablets both on- and offline. If tech pubs have changed just one word, or one chapter, or the whole book we can update the manual as appropriate. The tablets also carry ‘out of service’ information; facilitate the chasing of parts and hold OSP (oil servicing program) information which is ‘very cool’. And whereas, in the old days, some had to use work cards and calculators which introduced errors; now this is managed with automation – the mechanic adds two pints of oil to an engine and it automatically does the calculation to say if it’s good or bad; mechanics really like this.”
%20image%204_sm.jpg)
CHALLENGES FOR THE TABLET PROGRAM
Having established why mechanics would want tablets and what those devices could do for them, we also wanted to know whether there had been any challenges and what did the airline learn in the rollout?
Blair’s response was that the biggest challenge is connectivity and he explained, “We’ve worked through a lot of connectivity issues. Bearing in mind that we’re in some fifty countries around the world, we have found that international connectivity with tablets is a whole other ballgame than for domestic tablets. As a result, we have become experts at buying tablets outside the country and putting local cellular cards on the devices. Mechanics in Norita will be running theirs on GoGoMo whereas in the US it’s totally different. We run Sprint and Verizon and AT&T tablets but haven’t found one solution that works perfectly all around. We’re constantly moving things around and trying different options, first getting good service from one provider, then another provider works better.”
All of American’s tablets are Wi-Fi and cellular capable because mechanics can go from a concrete break room under a terminal where Wi-Fi works and not cellular, then go outside where cellular works better. And then again, sometimes around a Boeing 777 cockpit, you just lose signal. All of this experience drove the airline to adopt supporting offline capabilities.
HOW THE PROGRAM WORKS %20image%202_SM.png)
Given the range of these challenges and the size of American, we wondered how the airline goes about device selection. Blair explained that his team had worked closely with AA’s IT group and gave some employees a choice of Samsung or iPad. There is no Windows option yet “because we’re waiting for the Windows cellular program to be worked out”. But broadly the airline accepts that people just prefer one device over the other. American has 1,722 tablets currently deployed around the world of which 1,600 are Samsung tablets and 100 are Apple iPads, running side-by-side. They started two and a half years ago with Samsung because at that time the IT organization was struggling with infrastructure security issues around iPad. Now the airline is using both and Blair doesn’t mind which is used as long as they do the job. He adds, “Anyway, we’re running HTML 5 apps, which means they’ll run on most devices: we’re system agnostic and we’re tablet neutral.”
User engagement has been the most important aspect of the whole project at American Airlines. As Blair puts it, “It’s not about my idea or management’s idea; we take seriously every suggestion from a mechanic and we do our best to give them what they want.” What mechanics like most about tablets is the speed with which IT can deliver solutions: so AA didn’t sit around and wait for the perfect solution before deploying tablets. Blair’s team worked with Flatirons Solutions and, although the original solution was clunky, they did a deal that in six months’ time the airline wanted certain usability requirements such as a really nice user experience in which mechanics could use dropdown boxes (mechanics don’t like typing), could touch things and could zoom. And how did that work out? “True to their word,” Blair confirmed, “within six months Flatirons Solutions delivered a solution and the mechanics loved it.”
Getting information to the mechanics’ fingertips is now so much easier for AA than it was two years ago. The airline has moved from a paper world, where you wonder if the information was revised and if you’re in the right revision (and it could take a week to get there), to today’s environment when the same process takes minutes. It’s also only minutes from tech pubs publishing something before every mechanic around the world has it. If the mechanic is working offline, the program knows that there has been a revision and the mechanic must synch up before opening it. “The regulators love that there is built-in protection so that our mechanics do not use the wrong information.” says Blair, adding, “Mechanics are giving us their input and we went from five applications to more than two dozen in less than a year. We’re on version 9 or 10 this year alone and we’re pushing out revisions every 30-45 days. Mechanics like the speed; they like that we’re paying attention to them.”
THE BENEFITS AND ‘WHERE NEXT’
Before moving on to the Q&A Blair wanted to summarize the benefits and look to the future to see where the project is going. “AA has leadership that says it makes sense to keep the mechanic on the airplane, rather than in the break room, with everything they need [on the tablet] to fix the airplane.” he explained. “We’re going to get more into aircraft health management (airman web) and getting information from the aircraft in a mechanic-friendly view. OEM systems are good if you’re sitting at a desk. But we need stuff that works on a tablet, that lets mechanics take fault isolation codes and get into the AMM [aircraft maintenance manual] and have every engineering order he could ever want. We’re working towards that right now.”
%20image%203_sm.png)
KEY QUESTIONS ABOUT SPECIFIC ISSUES
Aircraft IT: Did you face any roadblocks from the FAA?
BLAIR GREGG: We took a different approach, taking Flatirons Solutions representatives with us to the FAA when we sat down with the CMO [certificate management office] and explained to them how the tablet would stop mechanics from having unrevised data. We showed them what mechanics would see in the tablet and what they’d be able to do: we got their buy-in and they were appreciative of us sharing it with them. Most importantly, the [publishing] process has been tightened up. We know exactly what revision of which manuals is on every one of those 1,700 tablets. The Flatirons Solutions software has a dashboard that tells us if manuals have been revised or not and we can send mechanics notifications if they haven’t [acknowledged receipt].
Aircraft IT: When you provide Wi-Fi, is it corporate American Airlines Wi-Fi? Do you use public Wi-Fi?
BLAIR GREGG: AA builds out Wi-Fi for other systems for other parts of the company like moving baggage around; and we take advantage of airport Wi-Fi. If you fly into Dallas, you get free Wi-Fi. Airports use different cellular companies and we use this as well. [Also] all of our tablets have cellular paid by the company, which is a requirement for mechanics to do their jobs.
Aircraft IT: Are the tablets issued as a corporate tool or a personal device?
BLAIR GREGG: We initially started treating tablets as a [corporate] tool: [however] mechanics were hesitant to check them out – they were concerned that ‘Big Brother’ was watching them. [And] mechanics treat tools well when the tools are their tools. We have 1,700 tablets out there today and in two and a half years, only two tablets have been destroyed. One was dropped and run over by a truck. The other was thrown against a wall and broke. (The employee bought a new one). They are amazingly rugged. Tablets are $300; the radios that mechanics carry are $600 and Toughbooks are $4200. So if you only broke two in two years, that’s pretty good.
We put our Samsung devices in an OtterBox case. When we did the math, we thought they’d break a lot more than they have. We are not worried about Skydrol: we keep these tablets at the flight line. These are mechanics working live flights so chances are they aren’t going to drop it in a bucket.
Aircraft IT: Do you worry about theft?
BLAIR GREGG: We initially started watching with GPS to see about loss but mechanics are treating them like their own tools. GPS will drain battery life so we backed off. If someone misplaces a tablet, we go on to our mobile device management and see where it’s sitting and the mechanics goes and picks it up. We have recovered every tablet that has been misplaced.
Aircraft IT: Do you have a hardware refresh rate, such as a 3-year cycle?
BLAIR GREGG: Yes, we use a three year cycle. We thought battery life would be shorter but we think we’ll get three years out of them.
Aircraft IT: When a mechanic leaves the company, how do you treat that?
BLAIR GREGG: We issue the tablets and mechanics return them to us when they leave.
Aircraft IT: You said earlier that American ‘gave some employees a choice of Samsung or iPad.’ How does that work?
BLAIR GREGG: Currently our iPads are only with the management team and aren’t with our mechanics yet.
Aircraft IT: Can you shed some light on the return on investment for the hardware and software?
BLAIR GREGG: We’ve looked at it in a couple of ways. Previously we had Panasonic Toughbooks. Now we can buy more devices with a less expensive tablet. We did not have to do a financial justification beyond knowing we’ll save at least 10 minutes by keeping the mechanic on the airplane versus having to go get data.
We weren’t able to finish our analysis because we changed our requirements with the FAA. Mechanics are now required to reference the six-digit reference [number], so we changed the game. We now have ‘delayed minutes’ that correspond with the six-digit reference that previously they didn’t have to record. Part of our strategy was to get the devices out there and get [mechanics] using the tablets before they had to start using the six-digit reference. We know fundamentally that the tablets help when they sign the logbook.
Aircraft IT: You said you issue tablets to technicians.
BLAIR GREGG: Yes, they take the devices home.
Aircraft IT: Around task cards, do you use electronic sign off or paper?
BLAIR GREGG: We are still paper based. The merger [with US Airways] will… change this but today we are still using paper.
Aircraft IT: What lessons have been learned regarding acceptance by the technicians?
BLAIR GREGG: We found that we were doing really well with our tablets until the day the pilot showed up with his iPad. We went from feeling really good to being really envious. Pilots could get to the internet and we couldn’t. We had to change. This is the number one thing that changed with mechanics wanting to use tablets… when we gave them unlocked tablets to surf the internet. We made it clear what the parameters are for use and we’ve had no issues. If you want to know what changed it, give them the internet. In line maintenance, it’s a really great day when the mechanic is sitting down because the plane is flying. But when an airplane needs attention, we want our mechanics to fix it fast.
Aircraft IT: On the security piece, what does access look like?
BLAIR GREGG: American Airlines has a single access system. We have to know our employee number and password. Those are the only things we need to do anything. Where it gets trickier is going to MyBoeingFleet or AirbusWorld from the tablet, if we’re not synchronized then you may have to know another password. Single sign-on is the thing mechanics like.
Our time was up and we parted thanking Blair Gregg for taking the time to share, with Aircraft IT readers, American Airlines’ experience with the introduction of tablets and mobility for mechanics.
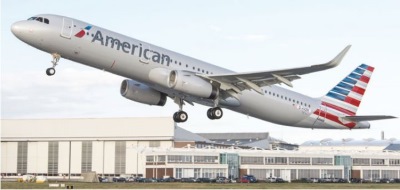

Author
BLAIR GREGG
MANAGING DIRECTOR OF TECHNICAL STRATEGY FOR MAINTENANCE & ENGINEERING, AMERICAN AIRLINES
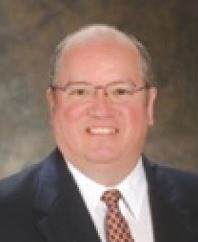
Blair Gregg is currently the Managing Director of Technical Systems Strategy for Maintenance & Engineering at American Airlines. In this role he is responsible for technical systems enhancement opportunities that will measurably impact M&E performance in dependability, reliability, productivity and cost control.
Blair joined American in 2007 as the General Manager of the Alliance Fort Worth Maintenance Base. Most recently he was the Director of Line Maintenance for the Southwest Division.
Prior to joining American, he spent 20 years with American Eagle Airlines in Fort Worth. His most recent position was Vice President of Aircraft Maintenance. Also, while at American Eagle, he progressed through several positions including Director of Inventory Control, Managing Director Abilene Operations, and Vice President Base Maintenance.
To post a comment, please login or subscribe.