Articles
Name | Author | |
---|---|---|
Case Study: Automating Humans back into Aviation – Robotic Process Automation | Albert Almendro, Aircraft Structures Engineer & AMOS Administrator, Vueling | View article |
Reaching new Heights: Maintenance Planning | Mark Martin, Director Commercial Aviation Product Line, IFS A&D | View article |
Case Study: Thomas Cook eTechLog (ETL / ELB) | Rich O”Mara, ETL & Big Leap Project Leader, Thomas Cook Group Airlines | View article |
Big Data: Racing to platform maturity | Yann Cambier, Senior Manager, ICF | View article |
Case Study: Automating Humans back into Aviation – Robotic Process Automation
Author: Albert Almendro, Aircraft Structures Engineer & AMOS Administrator, Vueling
SubscribeAutomating Humans back into aviation
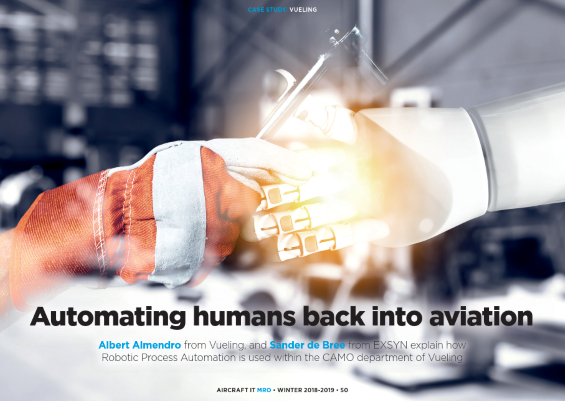
Albert Almendro from Vueling, and Sander de Bree from EXSYN explain how Robotic Process Automation is used within the CAMO department of Vueling
This article is about using robotic processes in the maintenance and engineering and CAMO environment, it uses the experience of Vueling, a Spanish low-cost airline, and their processes to illustrate the concept and its implementation. So, for context, let’s first share with you a brief profile of Vueling.
ABOUT VUELING
In July 2004 Vueling commenced operations with two Airbus A320’s on four routes. Today, the carrier (now part of the IAG group) serves more than 150 destinations with a fleet of 115 aircraft and 3,000 flight personnel. Vueling is a low cost airline with its home base at EL Prat airport in Barcelona. Paris Charles de Gaulle, Madrid Barajas, Sevilla, Brussels Airport and Amsterdam Airport Schiphol are also used as hubs. The airline operates direct flights from Barcelona to 155 destinations in Europe, Africa and the Middle East and carries over 16 million passengers every year. It is the largest airline in Spain by fleet size and number of destinations. The 115 aircraft in the Vueling fleet today include A319, A320, and A321 types as well as the A320 NEO – the first of 47 on order entered service in July 2018.
THE INITIAL SITUATION
Vueling was facing a challenge with the printing of workpackages from AMOS frontend that need to be delivered to the MRO at the end of the day. Every single item in the maintenance forecast is one execution of the process and thus the daily creation of workpackages weighed heavy on the daily workload in what was a quite complex process (figure 1).
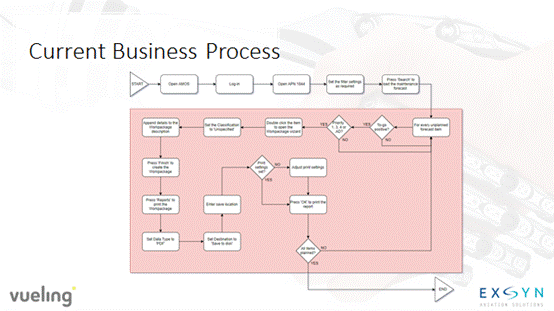
Figure 1
In fact, three or four employees were engaged on these tasks with two to three hours each day spent on printing workpackages alone – there were about 120 workpackages a day to be handled. The task is necessary for daily operation, but is repetitive, monotonous and time-consuming. Additionally, the department did not have the resources to always fully cover the workload, thus increasing pressure on the engineers. It meant that the task had to be planned up to seven days ahead and, more importantly for the business, it meant that those employees involved with this task were skipping non-mandatory forecast items in order to free up the time they needed for printing workpackages. That, of course, was bad for the business.
THE SOLUTION
In order to address the issue that was facing Vueling, EXSYN recommended and Vueling agreed to a solution that introduced Robotic Process Automation (RPA) to take over routine elements in their processes, such as printing workpackages, it was also intended to introduce greater consistency and accuracy, and reduce mistakes or omissions caused by human error.
In general, RPA is a technology that allows the user to create a software ‘robot’. This robot mimics the actions a human employee would do and does so in the same user interface of the system. Think of data entry into an ERP system, archiving of files or downloading data. These automated actions can even string up to a full end-to-end business process. Robots are trained for their tasks with the same instructions that are used for human employee counterparts and every robot also has its own workstation. Instead of a physical station, it is a virtual one. In these virtual environments they ‘read’ the screen electronically.
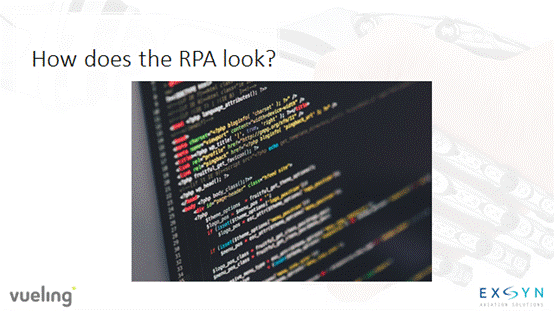
One of the biggest strengths of RPA is the low requirement for change in an organization. Software robots literally mimic the actions that human employees perform and do so in the front-end that human employees use. Organizations can adapt RPA without the need to change their (IT) infrastructure too much. Additionally, RPA saves organizations from engaging in the risky and time-consuming endeavor of redesigning the existing systems or even developing a new system.
By implementing RPA, the business hires a digital workforce. The robot workforce can take care of mundane and repetitive tasks or assist employees in their day to day work. Implementing them, organizations can achieve cost-reductions of up to 40%, realize improvements in service provision, achieve ROI (return on investment) within one year and enjoy other benefits.
There are two main automation types: attended automation and unattended automation. Attended automation is automation that is initiated by the human employee and visually runs on the desktop. Unattended automation on the other hand is automation that is triggered by an electronical input and it is executed on a virtual environment.
Why Robotics
For the workpackage situation EXSYN has developed a software robot that has automated the downloading, printing and planning of workpackages. As the initial situation at Vueling illustrates, within an airline there are many tasks of a repetitive/routine-based nature. These tasks take up valuable time; they decrease workforce motivation and increase the risk for human induced errors. Applying Robotic Process Automation (RPA) increases the efficiency of an airline, makes airlines more competitive and it can reduce or even take away human induced errors. By exploring the possibilities to automate such tasks, airlines can relocate man hours to value creating processes that require creativity and will boost the overall motivation of the workers.
But, as well as benefits from using robots, there are also challenges which have to form part of any thinking about robots and whether to use them (figure 2).
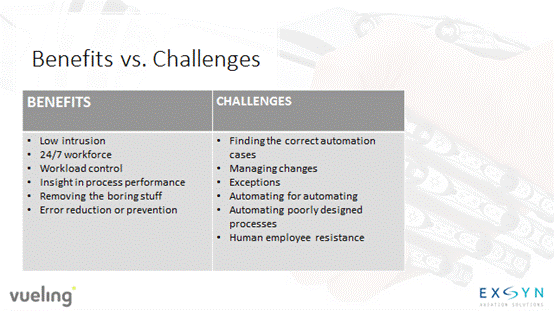
Figure 2
The benefits of automation have already been alluded to with low intrusion in the process, a 24/7 ‘workforce’, the removal of boring routines from human staff (thus making them available for more creative inputs to the business) and a reduction or elimination of the inaccuracies that will be caused by human error. There’s also better workload control and a clearer insight into process performance.
As far as challenges go, it’s important that automation is applied in the appropriate cases (see ‘Scoring’ below) and that any changes required are properly managed. There will always be exceptions and there is little point in automating for automating’s sake; there must be benefits to be gained. If a process is poorly designed then automating it will simply make it poorly designed but automated: arguably worse than a poorly designed process conducted manually.
THE APPROACH TO AN AUTOMATED SOLUTION
As a first step, EXSYN undertook an initial process analysis with Vueling’s planning department process expert to understand the current business process as set out in figure 1 above. This was a five step job and, at each step, there was an identified objective plus an expected output.
5 Steps to understand the challenge
The first step (figure 3.1) was to gather information which entailed mapping the different areas in the organization and their processes in order to generate a process landscape.
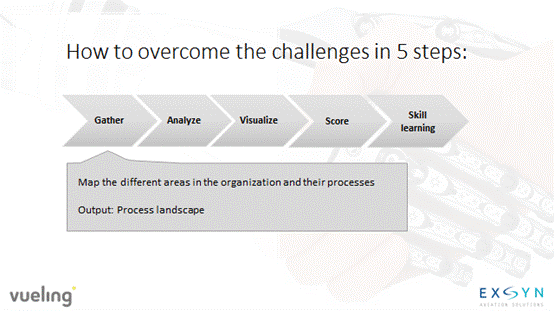
Figure 3.1
As a next step (figure 3.2, and with process information gathered on volume, time investment, rule-based, exceptions, human errors, process changes, input/output, system & application and risks) was to analyze that information…
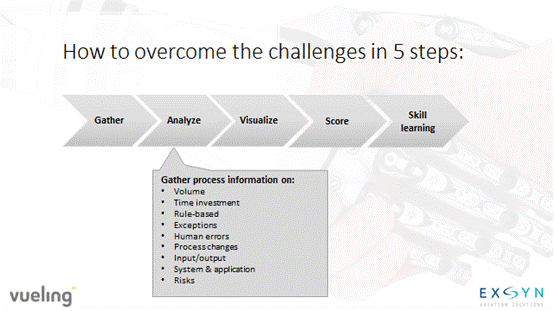
Figure 3.2
… and establish flowchart documents (figure 3.3) in order to be able to visualize the process as flowcharts such as figure 1 above.
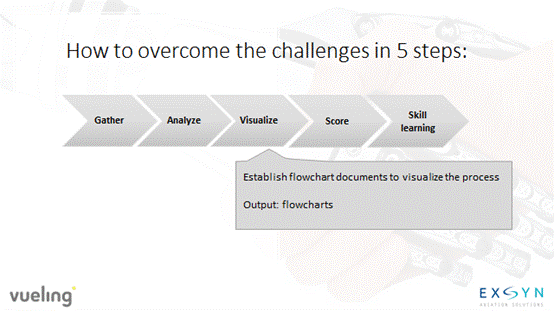
Figure 3.3
Next step was to rate the processes (figure 3.4) based on pre-defined factors to assess their suitability for the application of RPA and based on a scoring model developed by EXSYN. This resulted in a listing of process candidates for RPA.
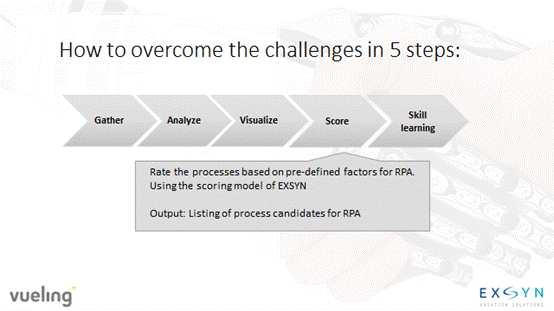
Figure 3.4
The final step was to code the RPA bot, i.e. ‘educate’ it, to perform the processes that were deemed suitable for it: in other words, to create a robotized process (figure 3.5).
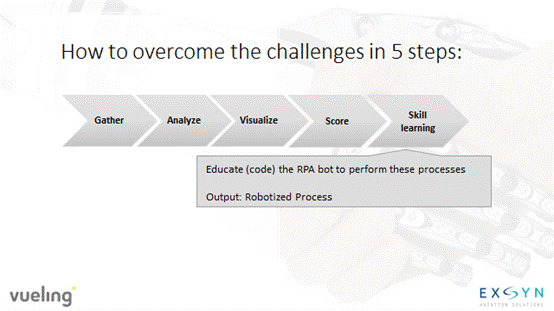
Figure 3.5
Scoring model
As part of that route to understanding, the process was scored in order to be able to be clear where the real bottlenecks were and indicate whether a step in the process was suitable for an RPA to do it. In fact there were two levels of scoring. The first was a technical score (figure 4.1) to assess the feasibility of a task being transferred to RPA, while the second was a value rating (figure 4.2) to assess whether, technical score notwithstanding, a step in the process was worth the investment cost of using an RPA. In both cases, weightings were given to different aspects of a job to determine the efficacy and/or value for money of a job being assigned to RPA.
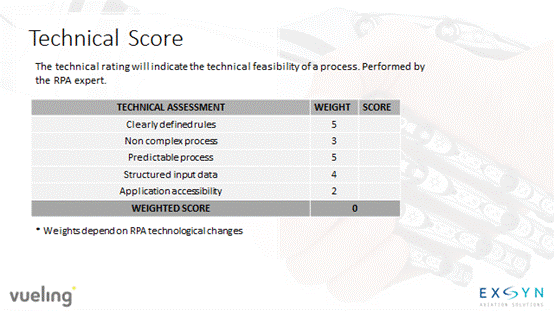
Figure 4.1
The technical scoring looked at aspects such as, are there clearly defined rules as to how this job is performed, how complex and predictable is the process, how structured is input data and the degree of application accessibility. Robots work best when given simple tasks with clear rules to follow and input data arriving in a predictable and consistent form.
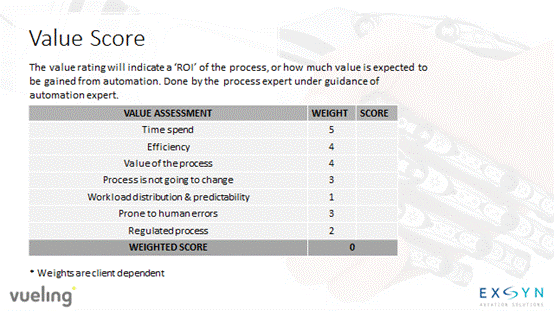
Figure 4.2
Value scoring indicates the potential ROI of the process – how much value is expected to be gained from automation.
Added together, in the case of Vueling, the combined scores indicated that workpackage was the best candidate process for the first application of RPA (figure 4.3).

Figure 4.3
The rest of the process
Following scoring, an automation skeleton was developed as the basis on which the new process, including its automated elements, could be built. The opportunity was also taken to see what improvements in business rules might be implemented as part of the transition to a new process plus some changes to enhance the process’s reliability.
As with any implementation, the new process with its software robots was tested away from the day-to-day operation in a test environment to ensure that it would do all the things that Vueling had previously done but would do them better and do a few more things besides. That completed, it just remained to create new documentation appropriate for the new process.
There were, though, a couple of challenges to be overcome. During the time that this was underway, Vueling upgraded from AMOS v10.90 to v11.30 and, of course, the new process had to take account of that upgrade in the system it was designed to serve. Fortunately, EXSYN has experience in AMOS implementations and upgrades and so was able to ensure that everything worked here. Also, AMOS is not controllable through UI (user interface) objects and so allowance had to made for that.
All that said, when the new process was implemented, AvBot Mk. 1 ‘joined’ the Vueling workforce to contribute at a key point on the new business process (figure 5) which, as can be seen, is a lot clearer and more straightforward than the old process.
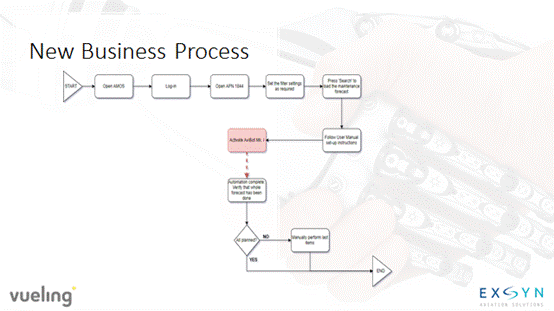
Figure 5
It has also had a big impact on the business with €4,500 worth of aviation engineer man hours saved in the first six weeks of the new process. There is also now only a need for one employee to monitor the process and automation has enabled a 15 day buffer to be built in so that it will be easier to plan around unforeseen events. Very importantly, the new process and its robot have meant that there are no more cases of human error causing items to be missed. Figure 6 shows the changes in stark numbers and they are impressive.
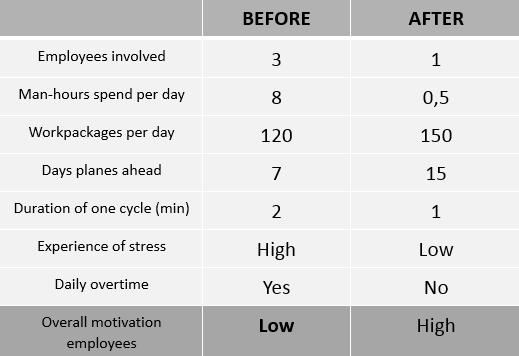
Figure 6
THE BENEFITS THAT ROBOTIC PROCESS AUTOMATION CAN DELIVER
RPA has provided the CAMO and maintenance organization at Vueling with the ability to robotize processes and, in doing that, they have achieved a number of benefits but without the need for disruptive change. The new process RPA mimics user interaction with other systems and so is not a disruptive element and, because the robot requires no sleep or breaks, it has created a 24/7 ‘workforce’. RPA has significantly reduced human error in the process and has also reduced cost as the human input is just one person now as opposed to the three or four who were needed before. But, perhaps, most importantly of all, the introduction of RPA to these routine tasks has freed up the humans in the organization to undertake more creative tasks instead of the repetitive tasks that they previously had to do. This benefits the workers involved who now are able to engage with more interesting jobs but it also benefits the airline which now gets the full benefit of a motivated and creative workforce. This is truly using automation to get humans back into aviation.
Contributor’s Details
Albert Almendro
Albert Almendro is a graduated Aeronautical engineer specialising in Aircraft engineering. After completing his final thesis, Albert joined Ryanair as a Technical Services graduate engineer. In 2014, he joined Vueling as a Senior Airworthiness engineer and was involved in the coordination of the data-migration of the Vueling fleet from SAP into AMOS software. He is currently working as an Aircraft Structures Engineer and AMOS Administrator.
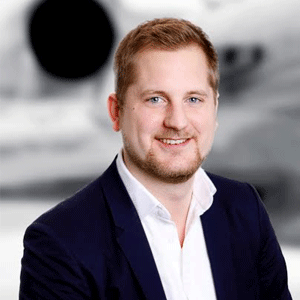
Sander de Bree is founder and CEO of EXSYN Aviation Solutions; focusing on aircraft data management solutions for aviation and heavily specialized in the field of IT systems for aircraft maintenance. Next to implementing the overall strategy he oversees all operational activities and R&D projects within the company. Sander holds a degree in aeronautical engineering with a specialization in aviation regulations and has a background in business administration. He holds a EASA certification on human factors, and IR part-m and IR part145
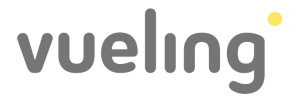
Vueling is a low cost airline with a fleet of 115 aircraft and 3,000 flight personnel. The airline performs direct flights from Barcelona to 155 destinations in Europe, Africa and the Middle East and carries over 16 million passengers every year. The fleet includes A319, A320, and A321 types as well as the A320 NEO – the first of 47 on order entered service in July 2018.
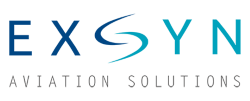
EXSYN provides aviation IT solutions with one important mission: to develop reliable, simple, and user-friendly software solutions and digital technology so that the aviation industry benefits more from digital possibilities. EXSYN’ s aviation solution platform focuses on data processing, data analytics, data storage as well as related consulting services for Airline Maintenance & Engineering departments. The firm has a broad expertise and a thorough understanding of all the high safety levels to provide clients with a service meeting the required standards and within the timeframe demanded.
Comments (0)
There are currently no comments about this article.
To post a comment, please login or subscribe.