Articles
Name | Author |
---|
Case Study: British Airways – Our most important journey yet
Author: Capt. Spencer Norton, Manager Flight Efficiency & Evaluation, British Airways
SubscribeCapt. Spencer Norton, Manager Flight Efficiency & Evaluation, British Airways shares how British Airways put fuel efficiency processes and their fuel efficiency management solution to a live test.
The pressing need to protect and restore our planet has never been more urgent. We’re at a crossroads and the decisions we make today could lead to a brighter future for our planet. Flying is freedom: it connects us with places and people, it makes the world a smaller place but this can come at a cost to the environment. That’s why, at British Airways, we’ve embarked on a flight path to net zero.
Our customers and shareholders demand that we become more sustainable. However, most important is our industry; every reader will be linked to the industry and we all have to do something to improve sustainability, if we want air travel to survive and grow.
PLANNING FOR A NET ZERO CARBON FUTURE
IATA has put forward some strategies to become net zero by 2050 (figure 1).
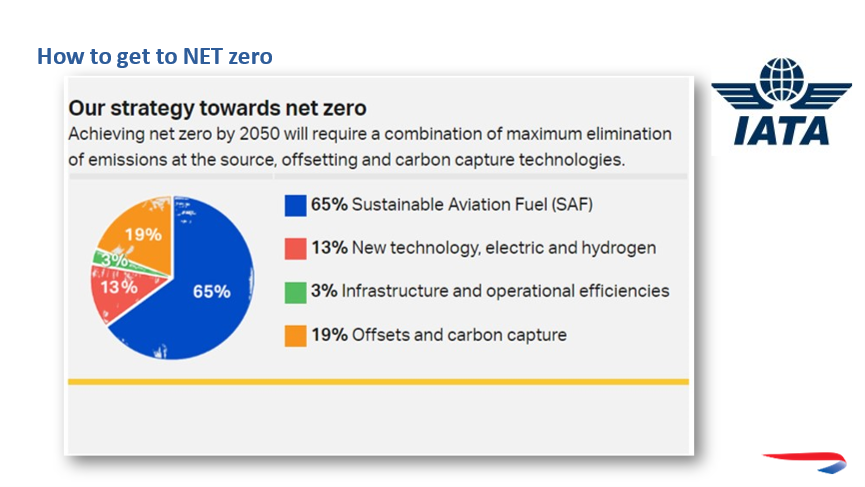
British Airways had already set this objective before IATA and our plan to become net zero by 2050 stands on three main pillars (figure 2).
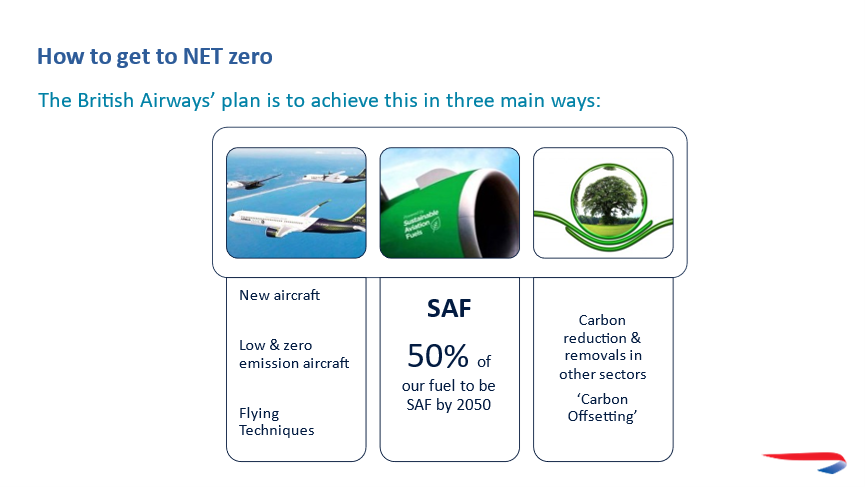
The first pillar is through new aircraft; low and zero emission aircraft and flying techniques. The second pillar is for fifty percent of British Airways’ fuel to be Sustainable Aviation Fuel (SAF) by 2050: We are also looking at hydrogen powered aircraft. If governments can underwrite the supply of SAF then airlines can buy more which will make it more cost effective. The third pillar is for carbon reduction and removal from other sectors with some carbon offsetting.
New Aircraft
British Airways has replaced its Boeing 747s and 767s with a suite of new aircraft including the Airbus 350-1000, Boeing 787-8 -9 and -10 and the Airbus A320/321 neo replacing some of ceos in the fleet (figure 3).
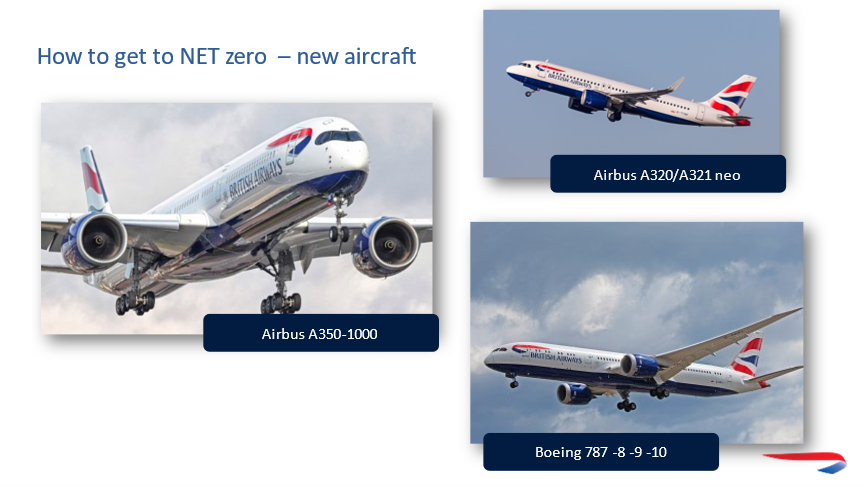
The A350-1000, for example, is 40% more efficient than the Boeing 747 with the same payload and passenger capacity. We’re also looking at and investing in hydrogen propulsion systems, so IAG, British Airways’ parent company, through the Hangar 51 program, has invested in ZEROAVIA which is looking at hydrogen propulsion systems on new aircraft. We’re also looking carefully at Airbus and how they’re progressing with the Airbus ZEROe concept which they believe can be in production by 2034 – an ambitious target.
Flying techniques
If we look at flying techniques, our concept is quite simple: We need to plan as efficiently as possible; we need to fly as efficiently as possible and, most important of all, we need to review effectively (figure 4).
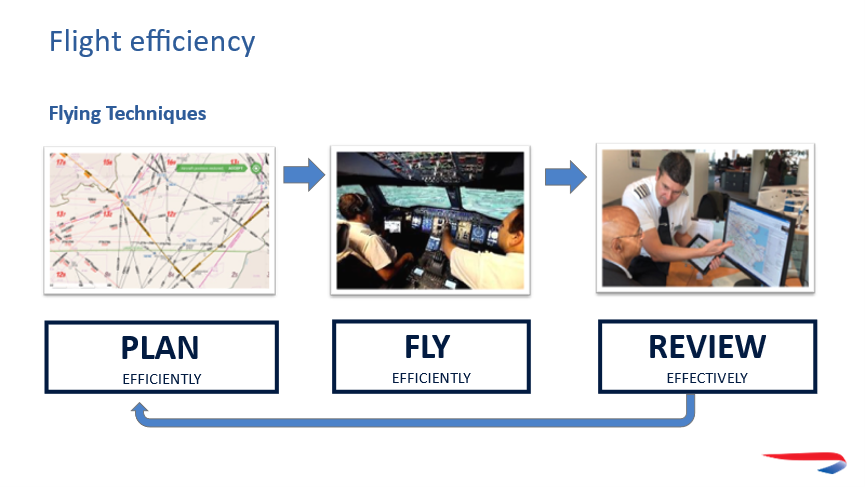
What you can see in figure 4 is a feedback loop going all the way through the system and constantly looking at how we can best optimize our planning and flying techniques while constantly reviewing them.
Sustainable Aviation Fuel
Looking at Sustainable Aviation Fuel, British Airways has committed to at least ten percent SAF by 2030 and we’d hope to get beyond that. The first batch of SAF came from Phillips 66 Ltd.; we’ve also invested in LanzaTech in the US and Velocys in Humberside in the UK. As already mentioned, the final target is to use 50% Sustainable Aviation Fuel by 2050. There isn’t a lot available at the moment which is why that target seem quite far of but, hopefully, it will be possible to bring that forward.
Offsetting and Carbon capture
At British Airways, we’re looking at robust carbon reductions and removals in other sectors of the industry; offsetting all CO2 emissions on all BA flights within the UK; and getting credible opportunities for customers to offset their emissions through varied carbon reduction projects. Plus, again through the IAG Hangar 51 program, looking into breakthrough carbon capture technology.
THE PERFECT FLIGHT
In September 2021, I operated something called the Perfect Flight, the first BA Commercial flight to operate using SAF. We looked at a suite of fuel efficiency initiatives and, crucially, we also looked at airspace modernization. A similar perfect flight was carried out in 2010 and most of the efficiency initiatives that we looked at for that flight, became standard operating procedures for British Airways from then on. Here is a short video about the Perfect Flight.
The question is, how do we calculate some of the savings that you saw in that video. We use the Honeywell Forge tool to help us do so. Here are some of those savings in greater detail and step by step.
ON THE GROUND
As the video explained, the aircraft for the Perfect Flight was connected to fixed electrical ground power and pre-conditioned air; the APU (Auxiliary Power Unit) was switched off five minutes before the standard time of departure which all saved about 30kgs of fuel compared to what we do on a normal standard flight. The pushback was done by an electric Mototok tug, and it was all done with 100% renewable energy (figure 5.1).
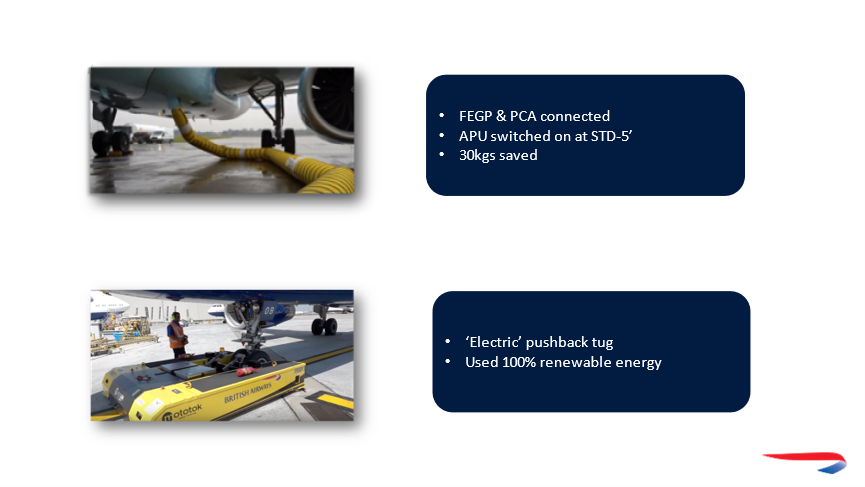
Engine start was delayed and, of course, only one engine was started, but the delay saved about another 10kgs of fuel: also, for this exercise, we used the most fuel-efficient flap 1+F rather than flap 3 and that saves about 24kgs of fuel on an Airbus 320neo (figure 5.2).
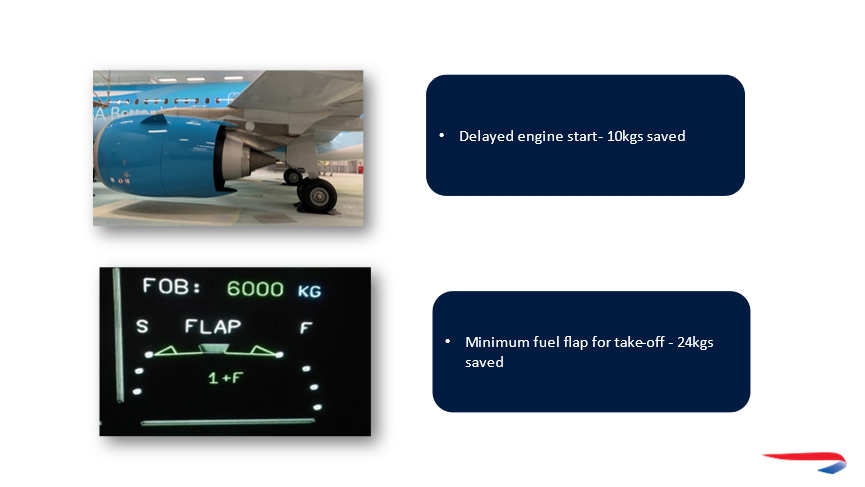
If you look at our routing out to the runway, Heathrow were on Easterlies that day and you can see the green line on figure 5.3 to get us on to 09R to depart; we did an intersection departure, got a target take-off time (TTOT) via Air Traffic Control and the red marking that you can see on the chart is the area where we did reduced engine taxi.
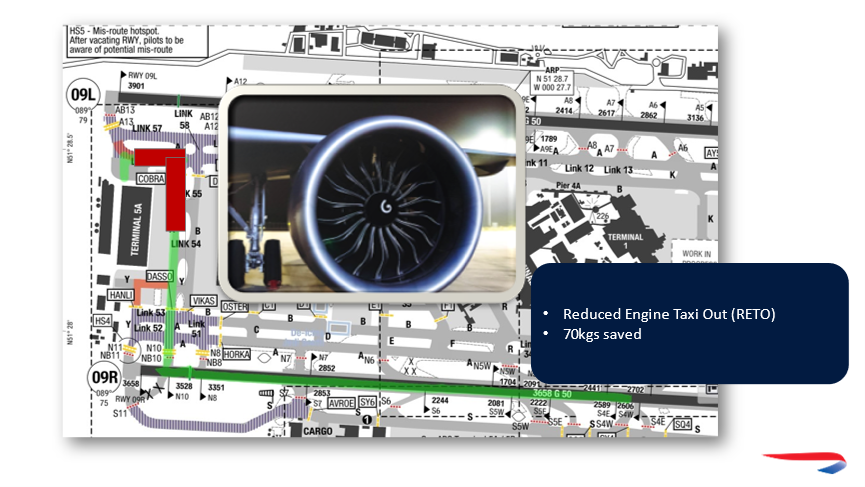
70kgs might seem like a lot but that saving was only for that Reduced Engine Taxi Out (RETO). We did have a problem with the tug on the day and, if we’d had both engines running, it would have been double that number so that 70kgs is embedded into the savings we had there with the issue that we had with the tug on the push-back. You can see where we did the reduced engine taxi and then when we started the other engine to line-up on to the runway ready for take-off.
If we look at the Honeywell Forge tool (figure 5.4) to see that data, then you can see where we started the first engine and then where we started the second engine as well, and that emulates what you saw in the diagram previously.
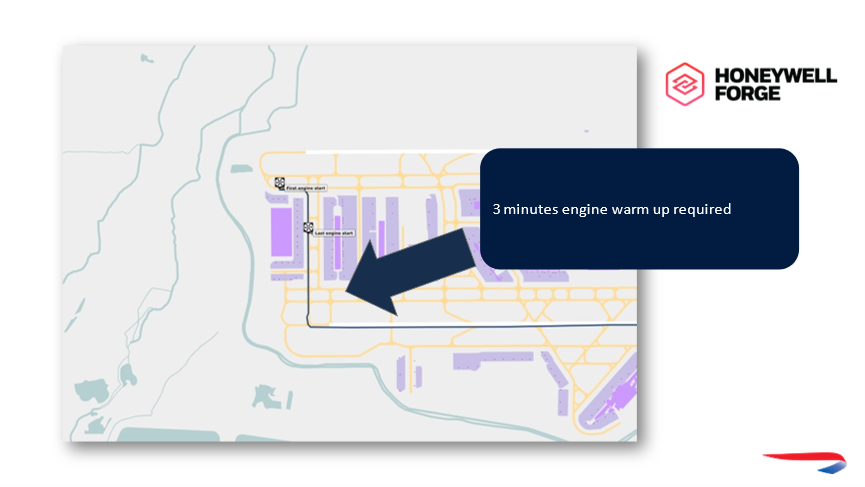
There’s a three-minute warm-up time required for the Leap engines on the NEO.
We completed a Packs off take-off (figure 5.5) which generated a further 6kgs saving; plus we did a Reduced Acceleration Altitude and NADP2 noise reduction procedure at a thousand feet: about 10kgs of fuel was saved by using those procedures.
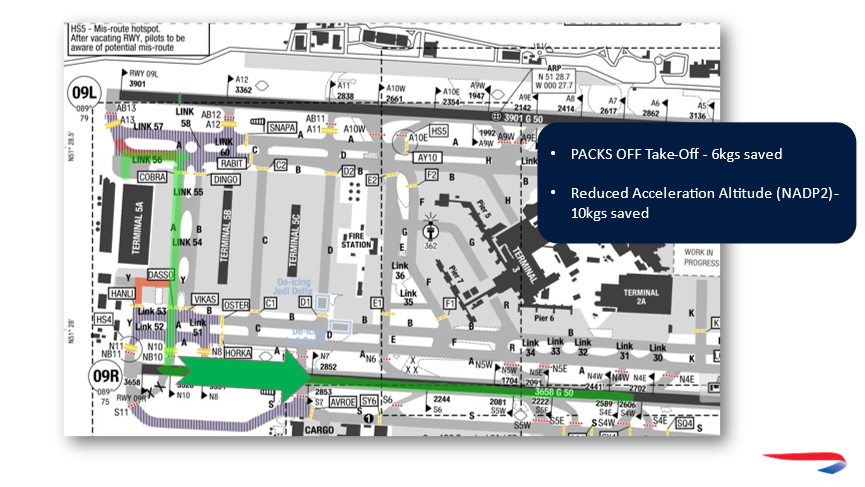
IN THE AIR
On the departure itself we flew the ULTIB Standard Instrument Departure (SID) up to Glasgow (figure 6.1)
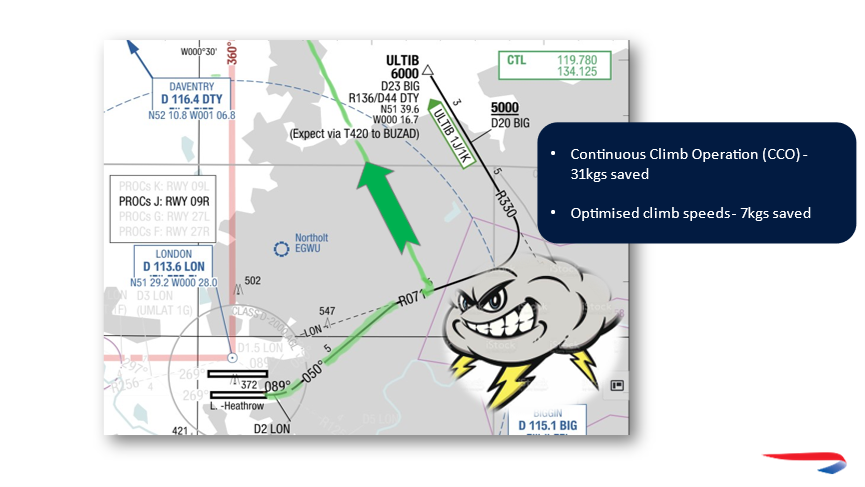
You can see that there was a Thunderstorm in the bottom right-hand corner and so Air traffic Control gave us an early left turn which did save some fuel with continuous climb. As was explained in the video, we flew some optimized climb speeds which saved around 7kgs of fuel in the climb phase.
Looking at the profile again using the Honeywell Forge Fuel Efficiency Tool (figure 6.2), again, the blue line was our actual climb profile, the grey line was our planned climb profile and you can see that we got to top of climb a lot earlier than we had planned on the flight plan.
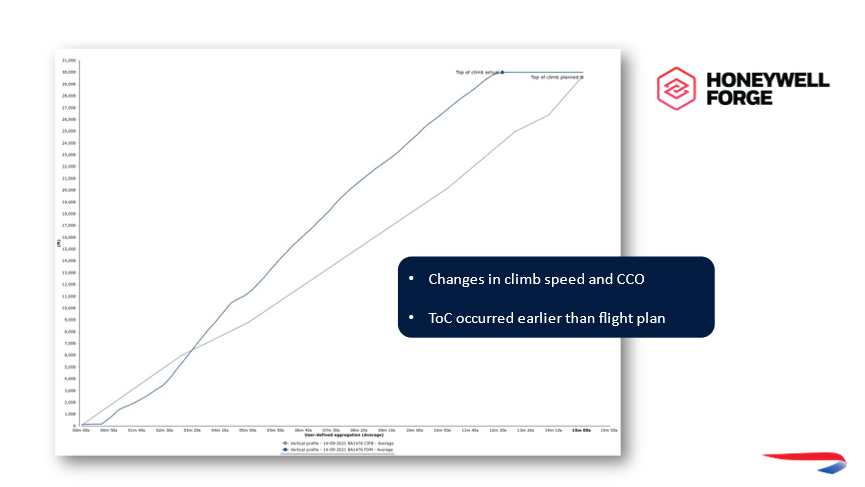
If we look at the lateral routing for the flight (figure 6.3), this is very much like Free Route Airspace (FRA); you can see a much more direct line than what we had planned in the flight planning system to get us up to Glasgow.
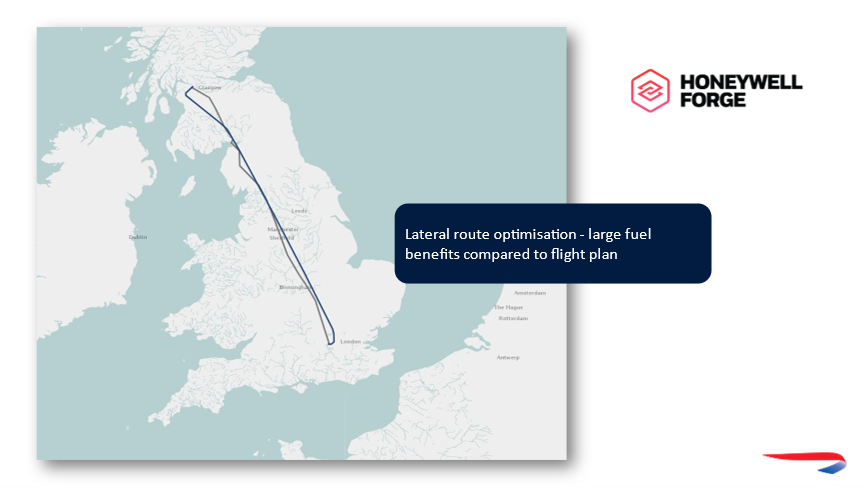
There were some large fuel benefits resulting from the lateral routing.
I spent a lot of time in the simulator doing research on the arrival into Glasgow, trying to make it as optimal as possible. We didn’t know what runway would be in use on the day, so had to consider both an arrival on runway 05 and runway 23 (figure 6.4).
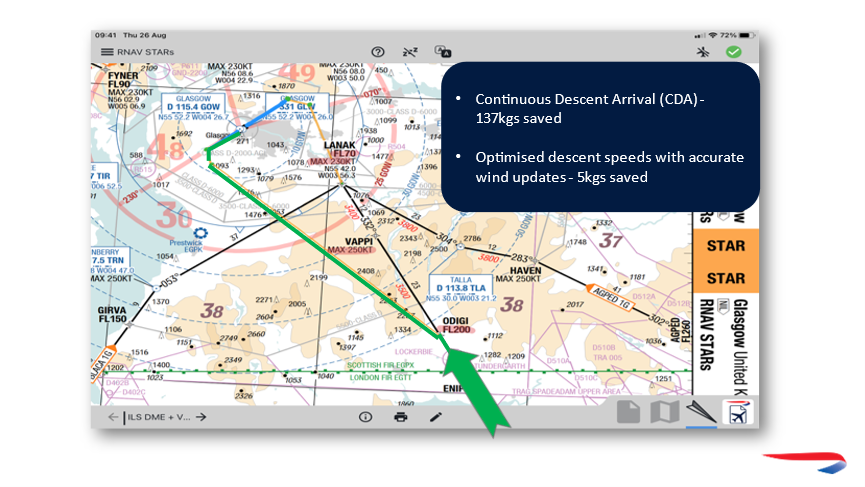
In constructing my own efficient routing, we consulted with Air Traffic Control (NATs) and so they knew where I wanted to go. The green line is the routing that was actually flown which broke away from the actual STAR approach and then made a direct routing onto the Easterly approach into Glasgow and, with a continuous descent, that saved around 137kgs of fuel. We had our optimized winds given to us on the descent as well with about 5kgs of fuel saved for the wind updates there. (Our wind updates were using the NAVLINK product from NAV Flight Services).
The routing that I created in the simulator is in figure 6.5 and you can see two waypoints; PINE5 and PINE0: These don’t normally exist on a routing into Glasgow but by constructing these and by putting a speed reduction in, I was able to fly the descent fully ‘Managed’ coupled with a continuous descent around the corner onto the ILS of runway 05.
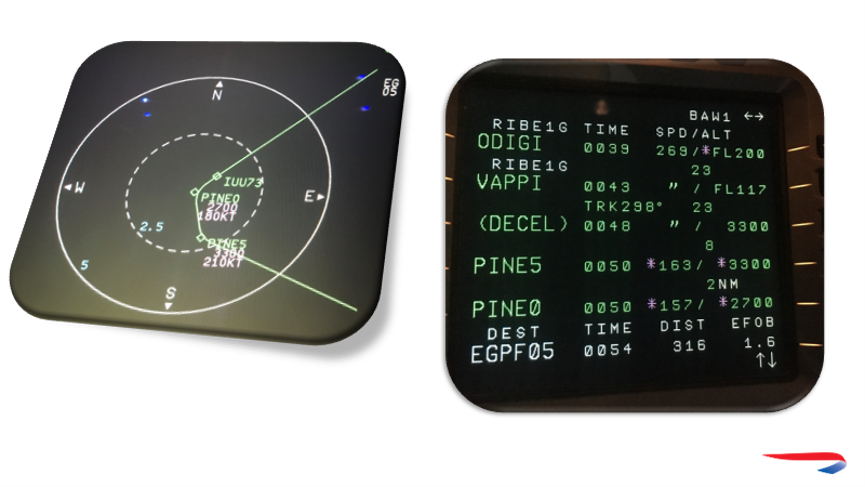
If we look at it in the Honeywell tool (figure 6.6), it can be seen that there was a slight levelling off near the bottom of the descent where we had to reduce vertical speed on occasions when Glasgow Air Traffic Control had a couple of traffic conflicts that were going to go beneath us, so to ensure that we didn’t do any level-offs, we had to reduce the rate of descent to ensure a CDO into Glasgow.
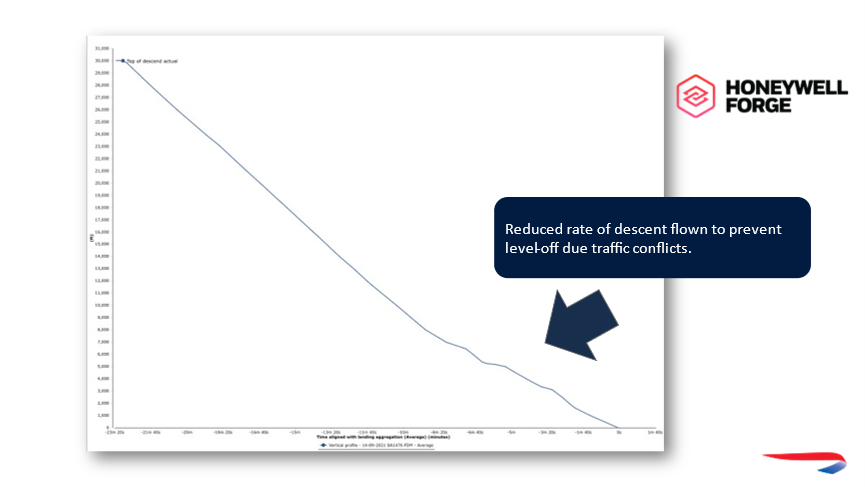
BACK TO THE GROUND
Looking at our landing (figures 7.1 and 7.2) we landed on runway 05 all the way to A1. We’d done a low power, low drag approach; delayed lowering the landing gear until as late as possible whilst ensuring the stable approach criteria at 1,000 ft was met, a Flap3 landing, reduced engine taxi-in and then single engine taxi without APU (SETWA), so we didn’t start the APU at all on arrival. .
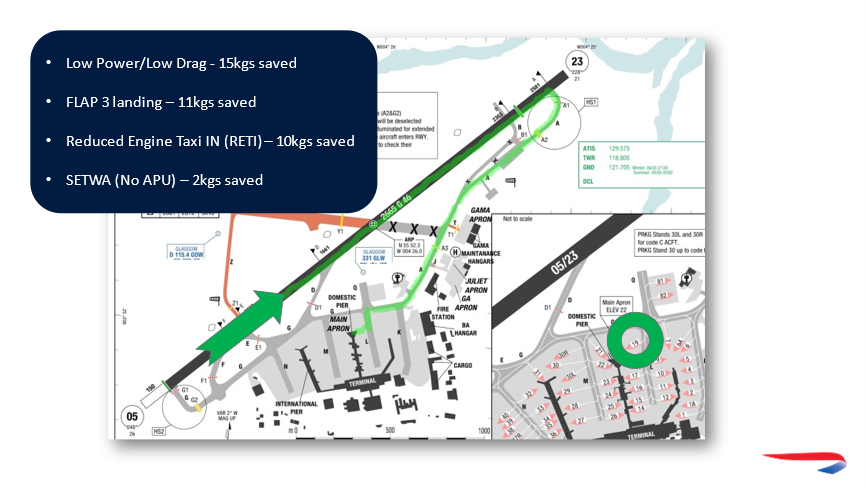
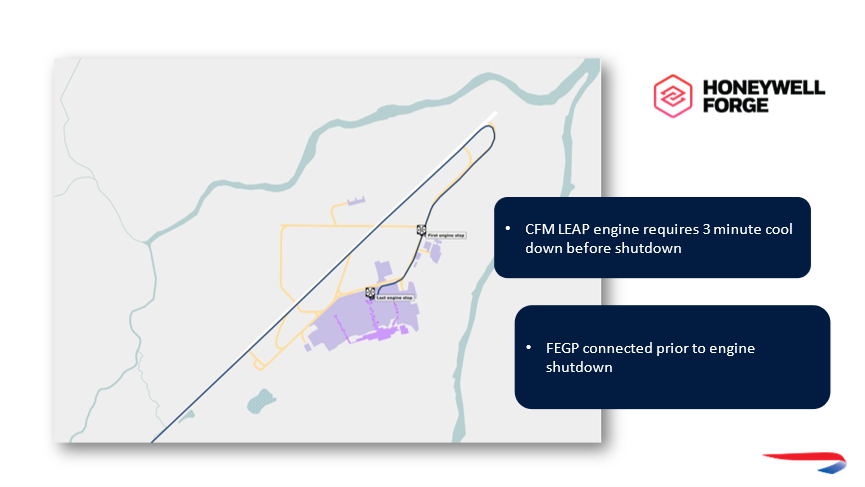
The Leap engine requires three minutes to cool down before shutdown and, again, in the Honeywell tool (figure 7.2) you can see where we shutdown that engine and then had final engine shutdown. The fixed electrical ground power (FEGP) was connected to the aircraft without any APU starting at all.
THE RESULTS AND USING THE NEW FUEL EFFICIENCY TOOL
Most important of all, we saved 371kgs of fuel on the Perfect Flight and that resulted in just under 1200kgs of CO2 saved. If we look at this in a benefits context, we achieved 16% more efficiency than a normal A320neo doing that flight or compared with a A320ceo, that was a 35% efficiency benefit.
I wanted to put it into context what a tonne of CO2 looks like so the photograph is a picture of what a tonne of CO2 actually looks like in terms of volume.
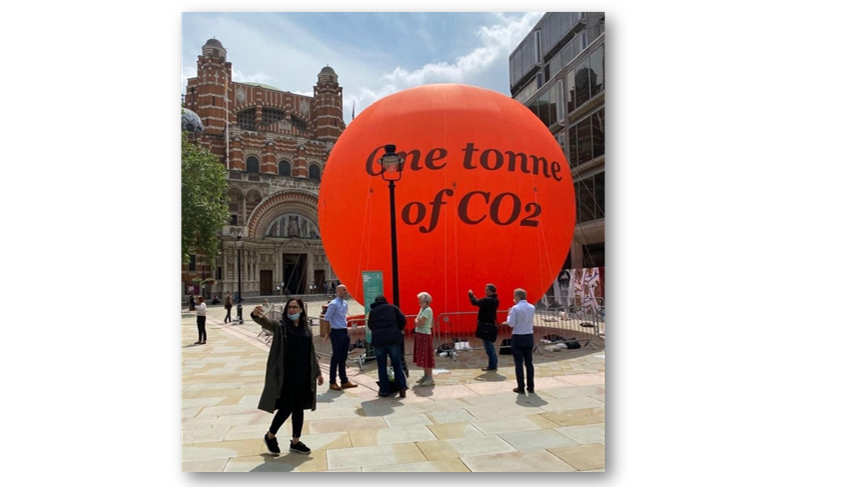
Finally, I just want to explain how we communicate some of these things and the feedback with our pilots. Figure 8.1 shows the new pilot dashboard showing the Discretionary Fuel statistics on the A320 fleet.
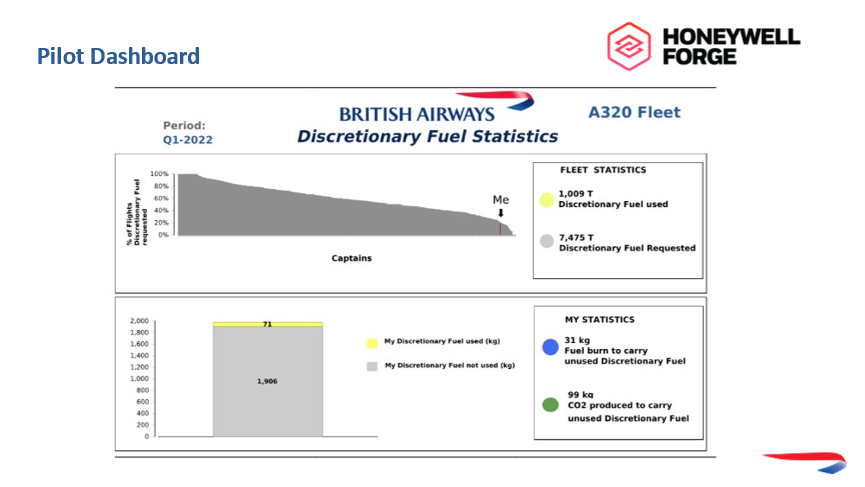
The grey graph at top left shows all the Captains on the A320 fleet anonymized. The ‘Me’ represents where the individual whose dashboard this is sits in terms of how often the carry Discretionary Fuel as a percentage. It shows where they are vis-à-vis their peers on the fleet. The right side of that graph shows the fleet statistics, the Discretionary Fuel requested by the fleet and the discretionary fuel that was actually required: there’s always quite a big difference there and usually shows that only 5% of flights require some Discretionary Fuel. This makes sense, as we use the 95th percentile in our Statistical Contingency Fuel on most of our flights.
The chart underneath shows the individual what Discretionary Fuel they loaded and what Discretionary Fuel they actually required. And then, to the right of that, the CO2 impact of what they did. Every Captain gets this report sent to them every quarter.
We do the same thing with Reduced Engine Taxi Out (RETO) as in figure 8.2 showing the same information with how often the Captain in question does RETO.
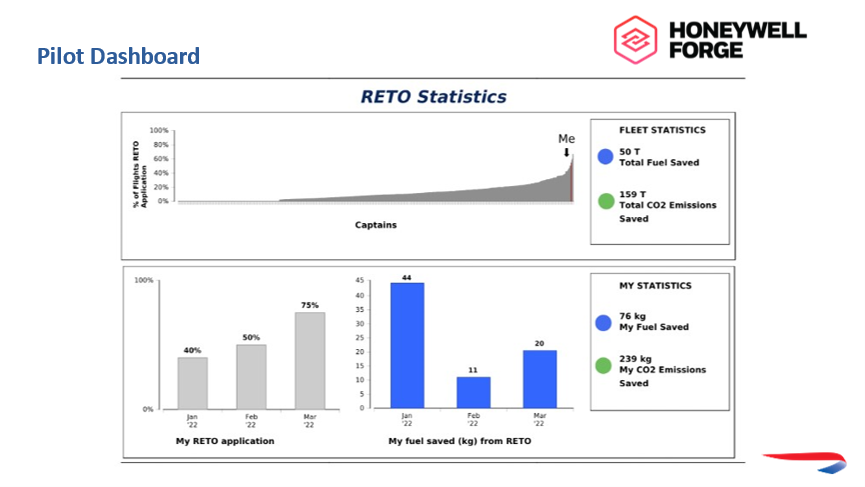
It shows what the fleet has saved by doing RETO and breaks down at the bottom the application rates and the fue (CO2)l saved in the relevant months of that period. A similar report is produced and sent to Captains for Reduced Engine Taxi In (RETI) which looks exactly the same (figure 8.3).
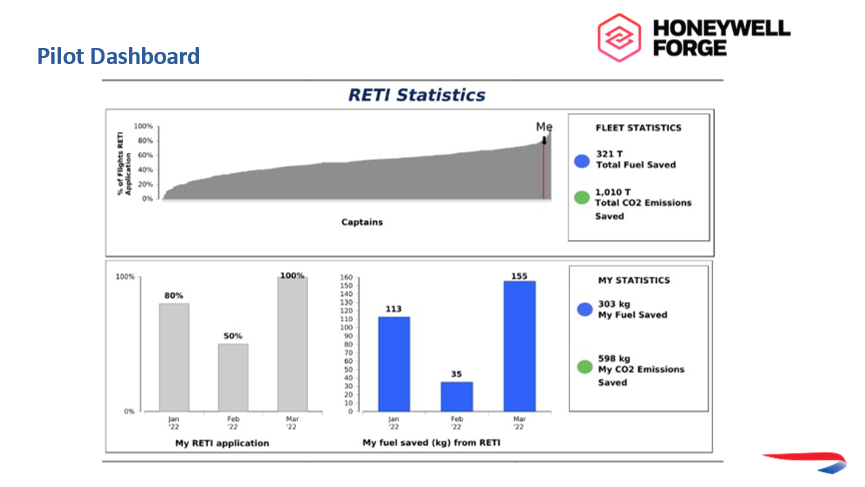
I hope that this article has given readers a good oversight of what was achieved by British Airways with the Perfect Flight and how we captured that data using the Honeywell Forge Fuel Efficiency Tool, which in turn, helps us on our most important journey yet.
Contributor’s Details
Captain Spencer Norton
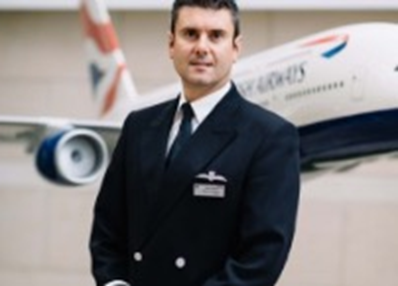
Spencer is a Training Captain on the Airbus A320 and, in his role as Manager – Flight Efficiency & Evaluation, he is responsible for fuel efficiency for all fleets and works closely with aircraft manufacturers providing expertise and recommendations on airspace modernisation and efficiency improvements. He was part of the Rule Making Group at EASA, writing the new EASA Fuel Scheme and chairs the IAG Flight Efficiency & Sustainability group and the Oneworld Fuel Efficiency group.
British Airways
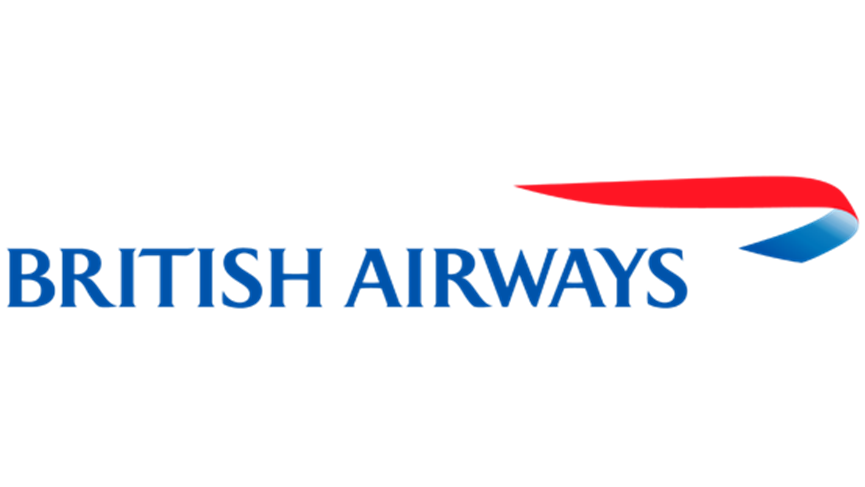
British Airways is the UK’s Flag carrier and a global airline, bringing people, places and diverse cultures closer together for more than 100 years. The fleet of more than 255 aircraft includes Airbus A319/320/321, A350 and A380 types as well as Boeing 777-300 and -200 and 787 types, plus Embraer 190. It is the second largest fleet in the UK. British Airways is a truly global business and has a stated mission to be carbon zero by 2050.
Honeywell Forge

Honeywell Aerospace products and services are found on virtually every commercial, aircraft in the world delivering improved fuel-efficiency, more direct and on-time flights, safer and more comfortable travel, and better flight planning. Honeywell Forge is an enterprise performance management solution for digital transformation of operations. It includes a mix of software products and enabling services that help companies use operational data to drive insights that improve processes, enhance productivity, support sustainability initiatives, and empower workers.
Comments (0)
There are currently no comments about this article.
To post a comment, please login or subscribe.