Articles
Name | Author | |
---|---|---|
WHITE PAPER: New Technology Focus – Extending Digital Twins to Digital Financial Twins | Sriram Haran, CEO; Varun Prakash Anbumani, Senior Solution Architect and Vamsi Krishna, Data Scientist, all at KeepFlying | View article |
CASE STUDY: An ERP system that has grown with Airbus New Zealand | Peter Buscke, Production Engineer, Airbus New Zealand shares Airbus’s experience with Ramco in New Zealand | View article |
CASE STUDY: A digital game-changer for JAL Engineering Co. | Atsushi Kita, Senior Director, Maintenance Planning Group, JAL Engineering Co. | View article |
CASE STUDY: A digital game-changer for JAL Engineering Co.
Author: Atsushi Kita, Senior Director, Maintenance Planning Group, JAL Engineering Co.
Subscribe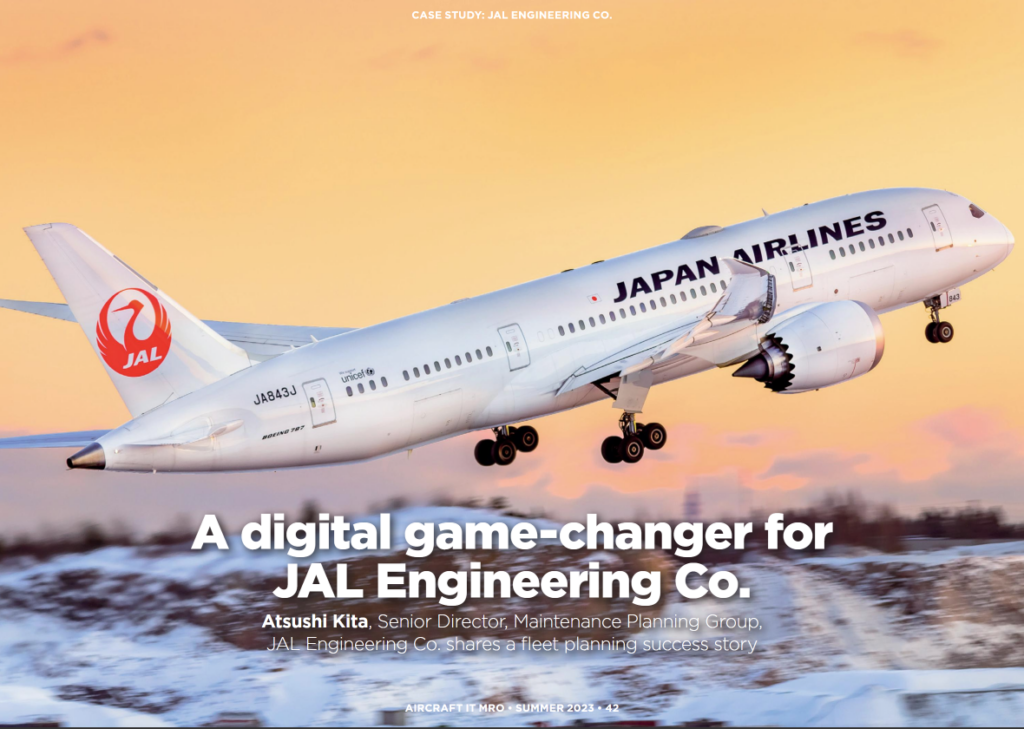
Atsushi Kita, Senior Director, Maintenance Planning Group, JAL Engineering Co. shares a fleet planning success story.
In this article, I’m going to share with you our experience using IFS Fleet Planner in JAL Engineering (JALEC). We’ll look at what it does and, importantly, at what benefits JAL Engineering has gained from using the new system. But let’s start by telling you something about JAL Engineering, the maintenance department of Japan Airlines (JAL).
JAL ENGINEERING CO., LTD. (JALEC)
Established in 2009, JALEC is 100 percent owned by Japan Airlines and has 4,000 engineers and mechanics with bases at Haneda (HND) and Narita (NRT) airports, Tokyo, as well as Itami (ITM) airport in Osaka. JALEC has certifications in 17 countries and regions and is responsible for the fleet management, engineering and quality management of 200 aircraft for four operators (JAL, J-AIR, ZIPAIR and Spring Japan) in the JAL group, as their airline maintenance department. Also, JALEC is responsible, as an MRO, to provide services for the aircraft of more than 50 customers to-date – other airlines and the military in Japan. Those services include line maintenance, base maintenance, engine shop, component shop and training. JALEC’s annual revenue is about U.S. $1 billion.
Zero-Zero-Hyaku, 0-0-100
For Japan Airlines, Zero-Zero-Hyaku, 0-0-100, is a key objective today (figure 1). We shared the idea and what inspired it with readers in the March-April 2020 issue of AircraftIT MRO.
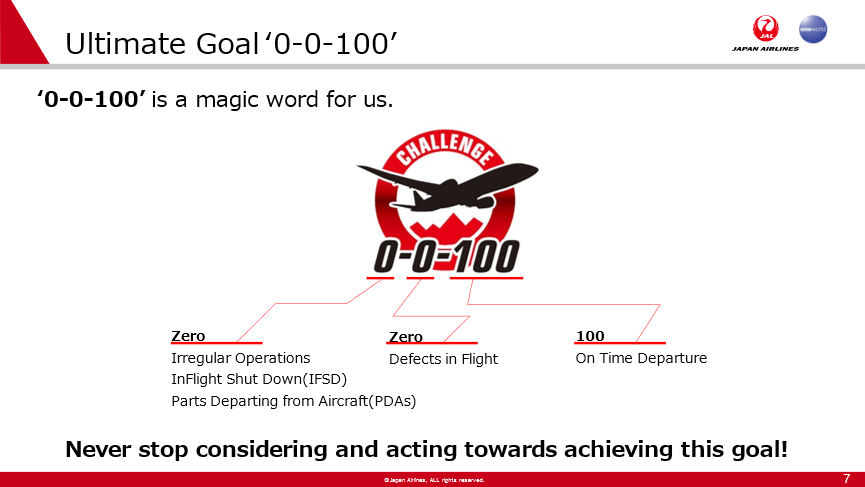
Figure 1
As the figure says, it’s a magic word for JAL but it’s difficult to understand. The numbers 0-0-100 have a meaning. The first Zero means that there should be no irregular operations, no inflight engine shut downs (IFSD) and no parts departing from the aircraft (PDAs). The second Zero means that there should be no defects in flight and the 100, in Japanese Hyaku, means that there should be 100 percent on-time departures by every aircraft. These are very stringent targets that JAL has set for its operations and which JALEC must support. Some might regard this as impossible, but we simply see it as a powerful challenge. It means that we never stop considering and acting towards the achievement of this goal.
As part of that, we monitor our progress and Figure 2 shows our performance against that target and the ultimate goal of 0-0-100.
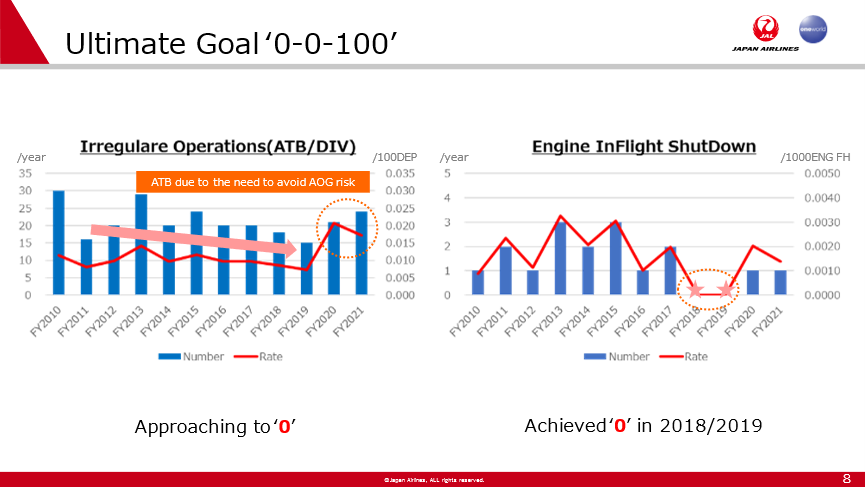
Figure 2
In 2020 and 2021, COVID ensured that travel conditions were far from typical but it can be seen that, prior to the pandemic, there was a downward trend in irregular operations and engine inflight shutdowns. With regards to inflight shutdowns, JAL has approximately 200 aircraft which means that there are 400 engines to be operated every day. But, in 2018/19, JAL never had to shut down an engine in flight; they achieved that part of the Zero-Zero-Hyaku objective at that time. Also, for irregular operations, the rate is decreasing and approaching zero.
We should also consider the defect in flight rate (figure 3)
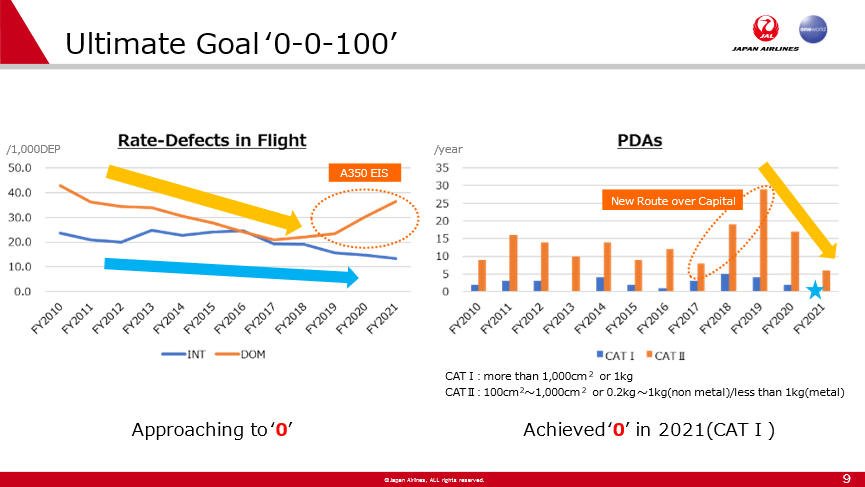
Figure 3
In 2019, JAL introduced the Airbus A350 EIS and, from then, the rate of defects in flight has been increasing. However, most of the fleet are not A350, as there are only about 16 of the aircraft in the fleet. Notwithstanding, the rate of defects in flight is steadily falling and approaching zero. Finally, parts departing from the aircraft (PDA) which is now decreasing every year, were increasing between 2017 and 2019, just prior to when the Tokyo Olympics were anticipated to have been held. The government was very focused on the PDA program because they opened a new route over Tokyo which generated an increase in PDAs but, since 2020, they have been decreasing.
How to achieve 0-0-100
This objective is a policy that shows us a direction but doesn’t offer a reason for the maintenance department. If you want to improve safety, you have to invest in aircraft, components and other materials which are very expensive which means, in turn, that you need to make a profit -a virtuous circle. However, if you cannot make a profit, you cannot invest and, therefore, cannot improve safety, a vicious circle. To achieve 0-0-100, we have to stabilize operations, improve efficiency and, to do that, we have to increase revenue while reducing costs. That was JALEC’s motivation to introduce IFS Fleet Planner throughout our maintenance operation.
IFS FLEET PLANNER
This is a Cloud-based software, a semi-automatic planning engine for the long-term base maintenance schedule. In figure 4 is a snapshot of IFS Fleet Planner.
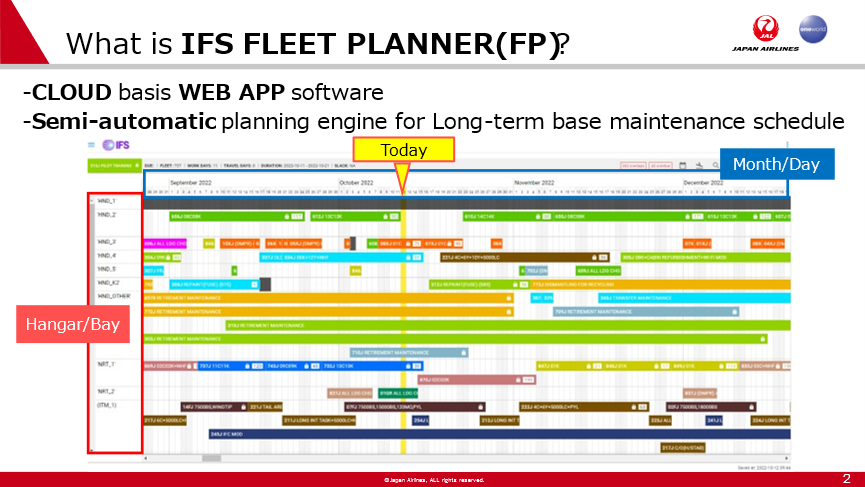
Figure 4
The horizontal axis, the blue edged box at the top, shows the time frame while the vertical axis, red edged box on the left, shows the hangars and bays, the places where we can undertake heavy maintenance. It shows that JAL Engineering has a hangar base in Haneda (HND) with six bays and two bays at Narita (NRT) There is also a bay at Osaka (ITM) and there are outsource maintenance facilities outside of Japan.
Overall, IFS Fleet Planner’s usability is very good and it is a simple step to introduce it into your process because it is a Cloud system. It’s also easy to use, easy to see and it’s easy to share information as well as to expand your business scope. Only an ID and Password are required to use the system which can be used anytime, anywhere in the world. As for infrastructure needed, there is no need to link with any other maintenance information system (MIS) and no need for a server or in-house system; all that is needed is a PC. Importantly in these budget aware times, the system can be implemented and used for a reasonable cost.
Given that we had been looking for a system like this for more than six years, IFS Fleet Planner has completed a part of our objective to achieve JAL’s ultimate goal of Zero-Zero-Hyaku, 0-0-100 – see below. We have found the system to be supportive of our business, to be stable and to be profitable. In terms of airline operations, IFS Fleet Planner is a contributor to fleet strategies, risk management and revenue management. For MRO operations, it is a contributor to the stability and efficiency of the operation, risk management and flexibility.
JALEC ADOPTS IFS FLEET PLANNER
So, let’s move on to examine the case study of JAL Engineering and IFS Fleet Planner. In the JALEC operation, we gained four key advantages from adopting Fleet Planner. Our view is that the first advantage is multiple simulations, followed by yield management for maintenance, then there is innovative planning and finally, workload mitigation. Let’s look more closely at each of those.
Multiple simulation
To complete your mission in a maintenance operation you have to be able to deal with uncertain circumstances (figure 5.1). These might include volcano explosions, earthquakes, health crises such as COVID-19, lightning or war; these are what we mean by uncertain circumstances that could impact unplanned maintenance. To prepare for these situations we need to make alternative plans – plans B, C or D – which will be essential to realizing our objectives. You cannot rely on just the primary Plan A, but IFS Fleet Planner enables users to simulate various plans by changing parameters.
In figure 5.1 you can see a primary plan or Plan A which is the optimized plan.
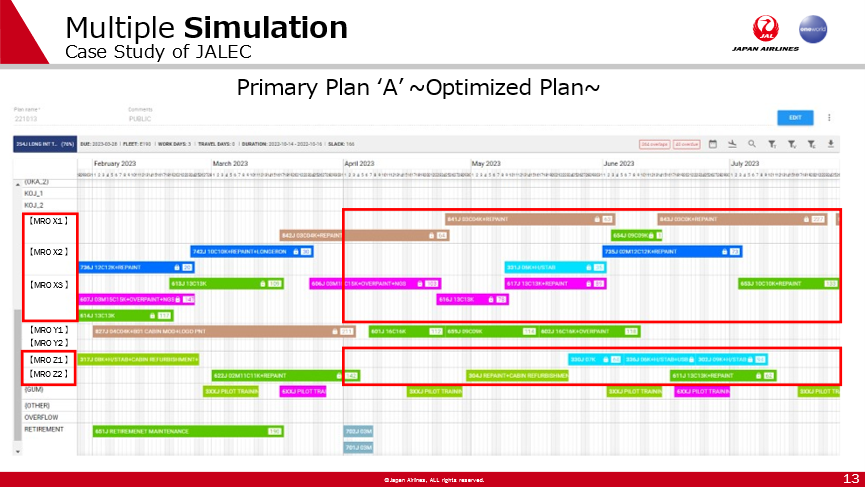
Figure 5.1
This is a snapshot of JALEC’s actual operation. MRO X1, X2 and X3 means that those tasks are outsourced to certain MROs but we have to consider what if there was some risk in outsourcing to this country’s operation, hence the red box around those tasks. If some problem, such as a resurgent health problem, was to occur in the area, we might need to suspend outsourcing to those MROs; so, we need to have alternative plans. We can do this with Fleet Planner by quickly changing the parameters (figure 5.2).
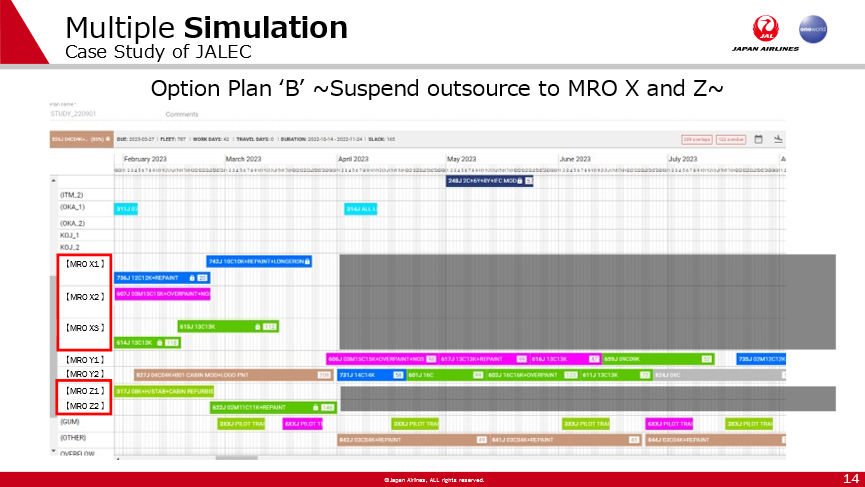
Figure 5.2
Although this is just a simulation, it shows what can be done in a short time with Fleet Planner by changing the parameters. We can make a Plan B for if we had to suspend outsourcing to these MROs in which case, we’d have to change other plans for heavy maintenance. IFS Fleet Planner will make those other plans: also, we can introduce other parameters to easily make a Plan C or Plan D. That gives us the option to choose an appropriate plan depending on the situation. It is possible to confirm various data and the feasibility of a plan with outputs from multiple simulations which also helps to establish strategies and manage costs. This helps us to maintain a stable and efficient operation while avoiding risks which is one huge advantage to be gained from using Fleet Planner.
Yield management
Yield is calculated as the planned time from the last maintenance event divided by the maximum required interval (figure 6.1)
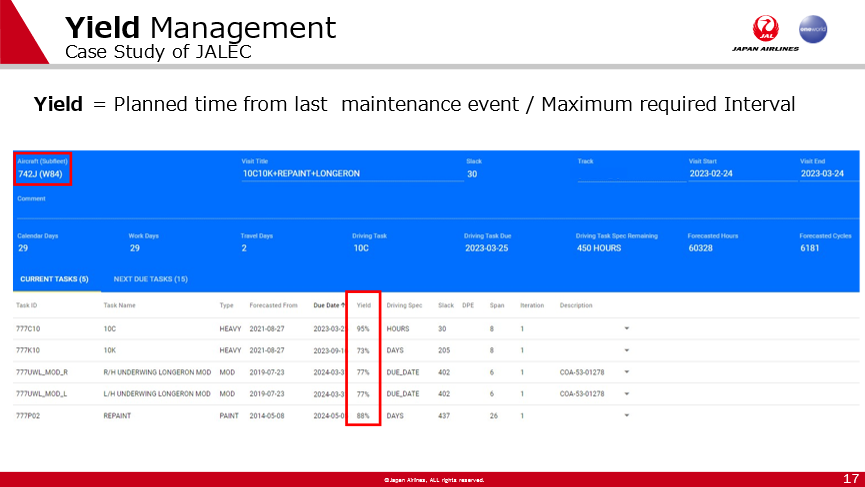
Figure 6.1
IFS Fleet Planner can build a work package with multiple heavy maintenance tasks. Figure 5.1 shows an aircraft, 742J, with the visit title reflecting the package of maintenance work to be undertaken by HAECO in China. Fleet Planner can show that this 10C package is yielding 95 percent and 10K package is yielding 73 percent. So, JALEC monitors and controls this yield as a KPI (Key Performance Indicator) in our operation.
Figure 6.2 shows actual data from JALEC’s operations.
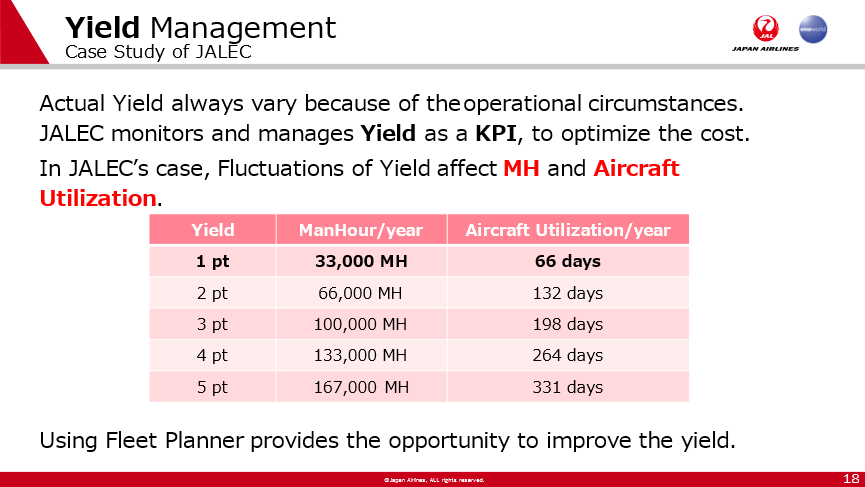
Figure 6.2
The actual yield will always vary because of operational circumstances, which was especially the case during the COVID-19 period. So, at JALEC, we monitor and manage yield as a KPI in order to optimize the cost in all cases. In the case of JALEC, fluctuations of the yield (center column of figure 5.1) mean that if we can increase the yield from, say, 95 percent to 96 percent, i.e., by one point, that makes it possible to release 33,000 man-hours for work that needs to be done in the year because maintenance cover is extended. That means that the aircraft can be utilized 66 more days in the year. So, if you increase this yield by more points, as shown in figure 6.2, you can utilize aircraft in the fleet more through the year and reduce the total amount of work that needs to be done. This is a very big advantage of using IFS Fleet Planner to manage the yield of the maintenance work. Of course, it depends on how to use Fleet Planner as we need to manage and adjust the plan based on this KPI, but if you use Fleet Planner as we do, it will generate more opportunities to gain man-hours and increase the utilization of the aircraft.
Innovative planning
This is very easy to understand. IFS Fleet Planner is a Cloud-based system so that it can be used anytime, anywhere in the world. It’s easy to share information between team members. My team at JALEC have built a Pit-Board in the office to share various data including the Fleet Planner and other operational data such as weather analyses.
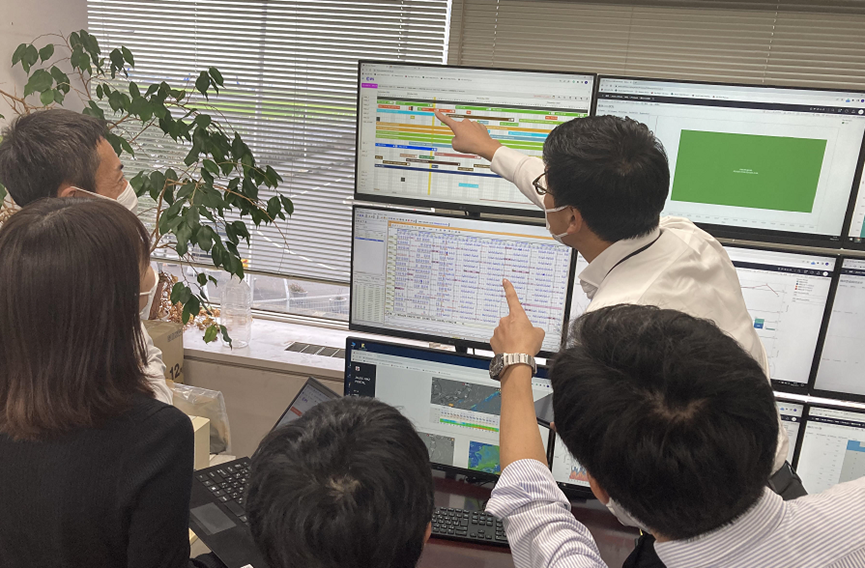
Any time that they get together in front of the Pit-Board, the team can share ideas and maybe get together in a Scrum. This is in line with a Japanese expression that two heads are better than one so five heads must be incredible! The Pit-Board brings innovation to your plan.
Workload mitigation
Another one that’s easy to understand. Before we introduced IFS Fleet Planner, we made the heavy maintenance plan using Excel spreadsheets. That was time-consuming as a manual process with significant risks for human error. Any coloring to identify different tasks had to also be done manually and, if someone wanted to share information, they’d have to send an email with an attached file. It added to workloads and was a headache.
After introducing Fleet Planner, one person is able to complete the same volume of work for the 200 aircraft, where previously it would have needed two. Not only that, but also, the business quality is improving, is more flexible and is taking less time. We can get information quickly and, if anyone is working from home, it’s easy to share with colleagues in real-time. It means that everybody is healthier and is happy.
IN CONCLUSION
The introduction of IFS Fleet Planner has empowered our people to be more innovative and the robust plans produced by our innovative planners gives us confidence to manage the operation. Having a stable operation contributes to our passengers’ experience, improves how we work with customers and empowers us to continue to evolve. In other words, IFS Fleet Planner provides us with a route to realize that 0-0-100 target.
At the time of writing, IFS is developing additional parameters which JALEC has requested to further improve the capability available within our existing solution. We are increasingly realizing the potential that fleet planning engineers can gain from IFS Fleet Planner.
Contributor’s Details
Atsushi Kita
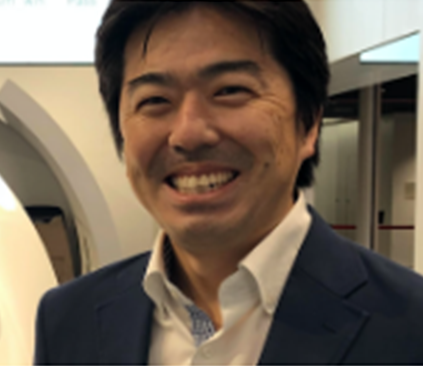
Atsushi Kita has worked in JAL/JALEC for twenty years, now mainly for maintenance planning and corporate strategies. He has supported customers as Director of Sales and Marketing of JALEC. Also, he has represented JALEC at ‘ATEC’, an association which is comprised of Japanese aviation companies, to develop and improve Japanese regulations working with the Japanese authority.
JAL Engineering Co. (JALEC)
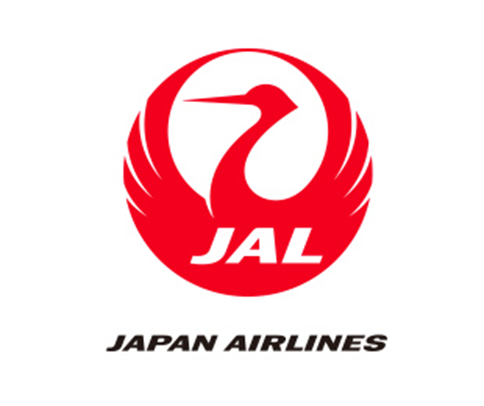
JALEC is an MRO business 100 percent owned by Japan Airlines with 4,000 engineers and mechanics working across three main bases. The business has certifications in 17 countries and regions and is responsible for managing 200 aircraft for four operators in the JAL group, as their airline maintenance department. Also, JALEC provides MRO services for fifty customers include, line maintenance, base maintenance, engine shop, component shop and training.
IFS
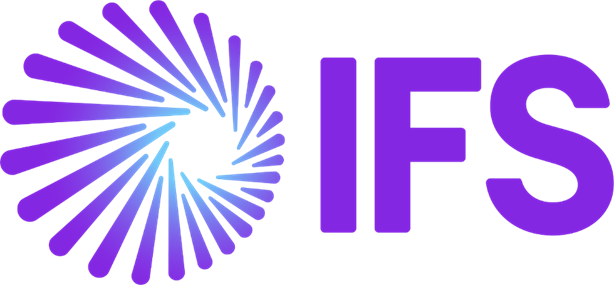
IFS is a provider of software solutions for global aerospace & defense (A&D), whose solutions support a complete spectrum of maintenance management capabilities from heavy MRO to line maintenance. IFS’s innovative enterprise solutions empower A&D organizations to quickly adapt and manage change whilst delivering bottom-line value, increasing efficiencies and cost savings, and safeguarding compliance. IFS customers include BAE Systems, Lockheed Martin, General Dynamics, SAAB, GE Aviation, Pratt & Whitney, HAL, Emirates, LATAM, Qantas, China Airlines, Air France-KLM, and Southwest Airlines.
Comments (0)
There are currently no comments about this article.
To post a comment, please login or subscribe.