Articles
Name | Author | |
---|---|---|
CASE STUDY: Transavia Netherlands upgrades to the latest MRO IT solution | Gerard de Bruyn, Product Owner of the technical department, Transavia Netherlands | View article |
CASE STUDY: Canadian North took control of its device fleet | Gail Campbell, Senior Manager Maintenance Information Systems, Canadian North | View article |
CASE STUDY: Affinity reaps the benefits of a new IT solution. | Grahaeme Colledge, Technical Director at Affinity Flying Training Services, and Tim Alden, Strategic Partnerships Director at Veryon | View article |
WHITE PAPER: A step into the future for an MRO software solution | Andrew O’Connor, Head of Product Management, Aviation and Paul Lynch, Group Managing Director, Aviation, both at Aspire Software | View article |
WHITE PAPER: AI is Powering Growth of Lifecycle Optimization Tools | Dr Ip-Shing Fan, John Maggiore and Professor Anna Smallwood, all at Cranfield University | View article |
WHITE PAPER: Gains for MRO from digital solutions | Remon Sweers, VP of Products, QOCO systems | View article |
CASE STUDY: Canadian North took control of its device fleet
Author: Gail Campbell, Senior Manager Maintenance Information Systems, Canadian North
Subscribe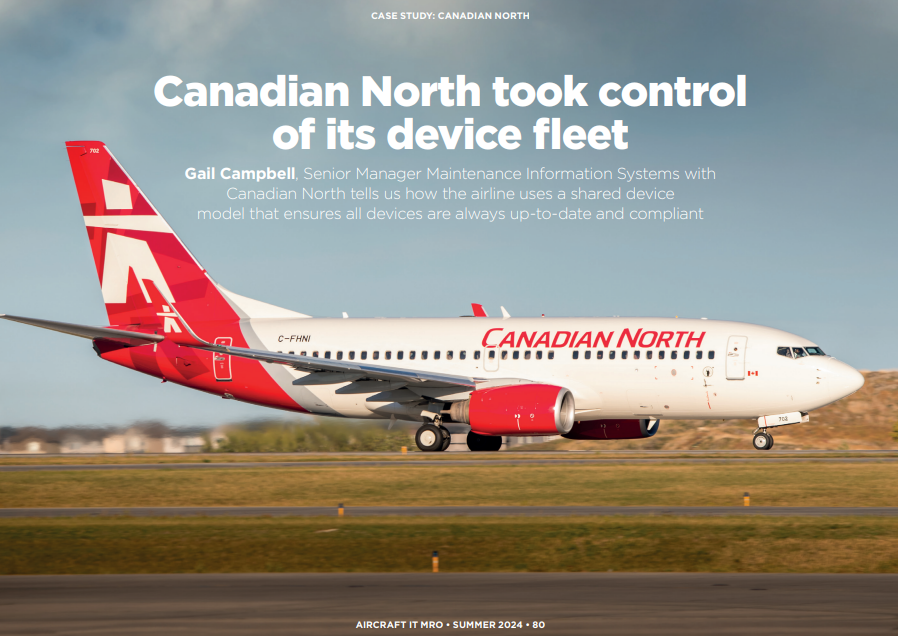
In this case study we going to look at the challenges and inefficiencies that can stem from using outdated paper-based systems as well as difficulties in managing complex workflows in a remote operational environment. We’ll also look at how a shared-device model has been crucial to mitigating common human errors, maintaining security and keeping cost of ownership low. I’ll finally explain how automating content deployment for technical publications, maintenance documentation, applications and operating systems can eliminate bottlenecks and improve your bottom line. But, as this is a case study, we’ll start with a brief introduction to the airline whose case it is, Canadian North.
CANADIAN NORTH
Starting as Bradley Air Services in 1946, the airline commenced operations under the ‘Canadian North’ brand in 1998. Canadian North is wholly Inuit owned and serves the most difficult places in Canada’s North. A mixed fleet of Boeing 737 and ATR aircraft, are all gravel and ice strip equipped for landing in remote locations. And because the airline serves many remote communities, it is a mixed passenger and freight carrier with some aircraft that are combination (combi) types, capable of multiple passenger/cargo configurations.
We face a number of challenges; some are common to the whole aviation sector and some are unique to our particular operations at Canadian North. Common to the sector are time sensitive and ever-changing content on productivity tools and maintaining synchronicity of device fleets in multiple locations. A good example is that working from the same and latest documentation is a requirement of Transport Canada so maintaining synchronicity of technical publications/content is crucial. Particular challenges faced by Canadian North include poor connectivity in some of our northern outposts causing a risk of non-compliance and out-of-date apps. There is also the road to a paperless environment which is a challenge in itself and, of course, regardless of the location, we need to guarantee updates are done and that we have synchronicity of devices. As well as the day-to-day factors such as flight time, maintenance turnaround time and efficiency of maintenance personnel, there is also the total cost of ownership (TCO) of the device inventory to be considered and the challenge of securing physical access by engineering staff to all devices.
THE JOURNEY TO MOBILITY AND ELECTRONIC RECORDS
Before mobility Canadian North was 100 per cent paper based, people would manually key entries into desktop computers. Then they would get transcribed and sometimes entries would be duplicated in the process. We realized there was a problem when not everyone had the means for maintenance technicians to record their work, i.e. access to an iPad. With eMRO from TRAX, see more below, Canadian North was able to transition to e-mobility. Now, with e-mobility, maintenance technician contractors are able to complete their own entries.
In 2013, we implemented TRAX then, in 2023, we moved from TRAX legacy to eMRO. The reason for telling you about that is because, when we moved from TRAX legacy to eMRO we wanted everything to go digital. As I’ve already mentioned we were, at the time, very paper orientated. When we created the business plan for eMRO, we made a mistake and forgot that we do our own HMV (Heavy Maintenance Visits) as well as our own MRO work with our normal line maintenance. We have a lot of contractors that come to work with us whenever we get a lot of aircraft in for HMV and LMV and we have two locations where we do this. Our thinking was moving towards an electronic solution but we forgot that our contractors are also going to need the eMobility app to work on eMRO and so, at the very last minute we realized we had no means of getting iPads for all of the contractors that come in on a part-time basis but we didn’t want to buy an iPad for each of them to use. We buy iPads for all of our employees, and they get to keep them but we didn’t want the contractors to be taking our iPads home because of the security issues associated with that. However, with such a large number of devices needed in the business, the next challenge that we faced was how to keep track of them and make sure that they were all fully up-to-date at all times with the latest documentation and regulatory compliance.
SHARED DEVICE MANAGEMENT AND UPDATING
To deal with this challenge and at the very last minute, we reached out to M3, having heard about their solution. Before going live with eMRO, we wanted to know how we could implement the iPad for contractors but not have those devices taken off the premises. M3 came in and showed us their solution which is a Kiosk, that can either be portable or at a fixed location. We decided to put fixed Kiosks in our main HMV bases in Ottawa and Edmonton and M3 came in to Canadian North to set-up the Kiosks and it has been plain sailing since we implemented them.
Because Canadian North is, as the name suggests, an airline that serves northern bases and destinations, we face a lot of challenges of paperwork coming in from the northern bases. In winter time, flights get cancelled all the time and sometimes, even when we get the paperwork, we can’t read it. It’s always been a challenge and so going mobile and paperless across the business was our biggest goal at the time of writing. M3 has helped us with the implementation of the latest Kiosks at our centers. I’m now looking to push that out to all of our remote stations like Yellow Knife and others for the employees, as opposed to us having to buy every new employee a new iPad, and then keep up with it because they lose their life after some three years. When the paperwork and agreement had been completed, M3 came in, set up the Kiosks, and put a guy on site who set-up the entire system.
Now, the contractor comes in, and they get a badge for the location where they’ll be working. Then, when working, they swipe the badge at the Kiosk which automatically opens and the iPad is there for them with whatever we have put on the Kiosk for the MDM part of it. So, if we choose that we don’t want the contractor to see something, that item won’t be loaded on the Kiosk. We started with a pilot plan because what this has proven to me now is that we keep the MDM (Mobile Device Management) right on the Kiosk and make any changes to it. Currently with our employee iPads, the ones that we bought, we’re using Meraki MDM from Cisco. The challenge of doing it with Meraki is that, if I push out a change to all of the iPads, but a user is on a three-week rotation, when he gets back, he doesn’t get that updated information. That’s because he has to go into the iPad and actually get the load itself because his iPad was turned off. It has helped us by going to M3 because, as soon as they check in and take an iPad out of the Kiosk, it’s always loaded with the latest documents, applications, everything. Potentially, with the ones that we’re doing manually, they don’t get the load right away if they’re not in work at the time, so they may be using outdated information. It’s a similar problem as it was with the paperwork; if they don’t read that there’s an update to a particular manual, they’ll be using outdated information and that is not acceptable. With the M3 solution, there is a nice easy dashboard for us to use; you go in, you update it, it pushes the updated items out and, if the iPad is plugged in to the Kiosk, it gets the update. If the iPad happens to be checked out with a user, once they plug it in to the Kiosk, the entire system is totally wiped and then reloads everything that you want. There is just the one MDM that pushes everything out whereas previously, with the old system, it had been dependent on access to the iPad to upload updates with the risk that users could still have been using outdated information.
BENEFITS OF A SHARED DEVICE SOLUTION
Using a shared device solution offers the airline a number of benefits. It keeps the cost-of-ownership low and saves admin/configuration time for end users with iPads that are always ready to use. It also allows partners (contractors) access to iPads, decreasing the duplication of entries. The M3 Kiosks also solve a number of inefficiencies with one solution. Digitized workflows and paperless operations eliminate error-prone paperwork: M3 Solutions replaced manual data entry and handwritten records with digital forms and checklists, significantly reducing the potential for transcription errors. Streamlined workflows mean that contractors have access to maintenance information and tech pubs on their iPads directly on the wing. With centralized data, all maintenance records are stored securely in a single digital platform, reducing the risk of data loss or damage.
In figure 1 you can see what the Kiosk looks like.
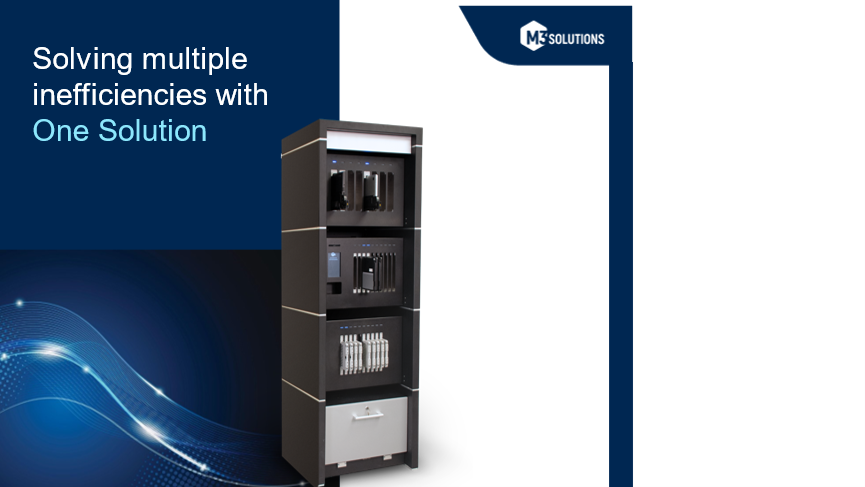
Figure 1
This is all part of Canadian North’s transition to going electronic with eMRO and with the iPads we’re going to look at other applications. I’m just giving you the scenario within eMRO, but we also use Comply365 and a lot of different applications. We are not just going to use these Kiosks for eMRO; we’ll be using them for all employees for ither applications and might potentially use it in the flight Ops context and set-up Kiosks for that. What the Kiosk will do is it will save us a lot of money by moving from buying an individual iPad for each employee to everybody sharing a fleet of iPads. It’s so simple for employees to get an iPad; they walk in to work, check out an iPad loaded with the material they need for their job (whatever their profile is set up to use, that information will be on the device) and, when they’ve finished, check it back in. End users can focus on their job responsibilities instead of spending time maintaining their device and we have complete asset management across the organization. Spare devices are not required for the event of equipment failure, low battery, updates not maintained, or forgotten/lost devices.
In each site at Ottawa and Edmonton, there is a Kiosk with 20 slots and another one with ten slots, giving us 30 slots for iPads in each of those two bases. We started with M3 because of the HMV and the contractor usage, making sure that they have the capability to do their electronic sign-off.
We also have eLearning on our iPads to ensure that everybody always has the training they need and we give each of our contractors an email for communication during their shift. How it’s set-up is that, when they sign on to the iPad, it will prompt them to put in their specific user details. They can then sign on to their company email just by logging in. All of that is pre-set on their iPads for them to use every day.
SUMMARY AND CONCLUSION
Using the shared device model not only delivers cost savings for the company but it also makes sure that all of the necessary information is uploaded and up-to-date. At the time of writing, there were a couple of people that had to go in to Meraki, whenever an employee left or an employee started or a contractor, they had to go in to Meraki, de-activate one profile, add a new profile, set-up the iPad, meet with the person to hand over the iPad and make sure that they were all set-up. Now, with the Kiosk centers, we simply give new employees or contractors their activation code and swipe card. They can then go to the Kiosk and swipe their card or they can use a PIN code. It takes away a lot of the administration side of things.
Prior to this project, we used to have the Gen 7, 8 and 9 iPads and we recently found that the gigabyte capacity that we had bought was not as much as we had expected. So, we changed all of our Gen 7 to 9 devices for Gen 10 iPads which are what we gave to employees and we’re up to 64 gigabytes on those so that they could use them with all the downloads. Using the Kiosk, it wipes the information every night so the Gen 7-9 devices now work OK because everything is wiped; so, if they’ve taken pictures to upload into task control or somewhere, that all gets wiped out and it’s like a brand-new iPad when the next person comes in to sign it in in the morning.
That has been our experience in Canadian North where the M3 device management solution has not only simplified the running and use of our iPad fleet but is also paving the way for future mobile and digital developments.
Comments (0)
There are currently no comments about this article.
To post a comment, please login or subscribe.