Articles
Name | Author | |
---|---|---|
What IT can do: The OEM perspective | Henrik Ollus, Customer Success Manager, QOCO Systems | View article |
Case Study: A lifelong digital maintenance record for aviation assets, Part 2 | Karl Steeves, CEO, TrustFlight | View article |
Case Study: Digital Transformation at Etihad Airways Technical | Eric Bogner, Manager Strategic Partnership and Performance, Etihad Airways and Arish Sayed, Manager Projects – Technical, Etihad Airways | View article |
Case Study: Enter Air’s post-pandemic upgrades are supported by a flexible MRO IT solution | Konrad Dymowski, Enter Air | View article |
Case Study: Digital Transformation at Etihad Airways Technical
Author: Eric Bogner, Manager Strategic Partnership and Performance, Etihad Airways and Arish Sayed, Manager Projects – Technical, Etihad Airways
Subscribe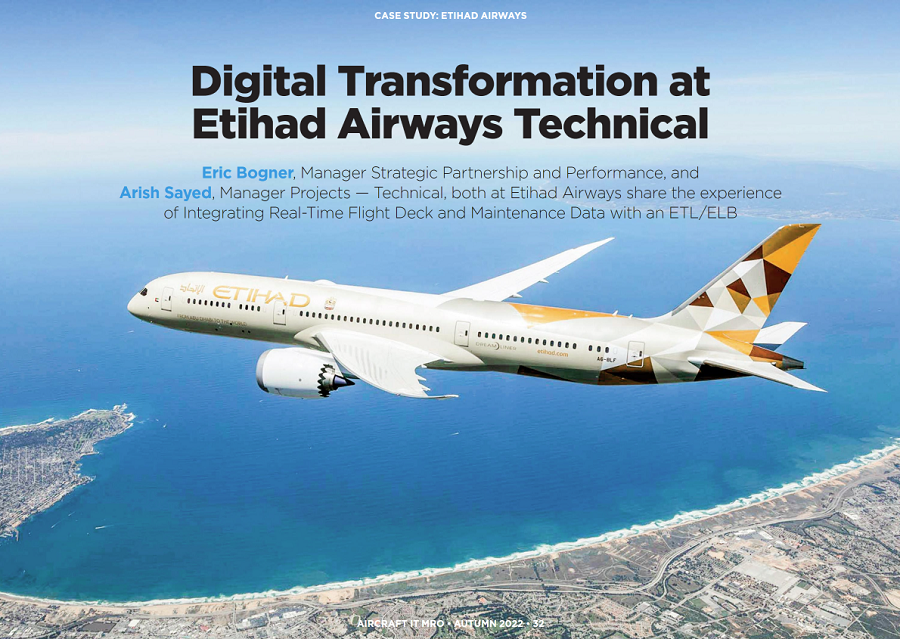
Eric Bogner, Manager Strategic Partnership and Performance, and Arish Sayed, Manager Projects – Technical, both at Etihad Airways share the experience of Integrating Real-Time Flight Deck and Maintenance Data with an ETL/ELB.
The COVID-19 epidemic was both an unprecedented and unpredictable crisis which drove the airline sector to adapt to some incredibly fast changes. In this article, we’ll try to share with readers how Etihad managed to get through that time and used a digital transformation to turn the crisis into an opportunity. But we’ll first tell you a little about Etihad Airways.
ETIHAD AIRWAYS
As the national carrier for the UAE, Etihad Airways was launched in 2003 and so might now be considered a mature business. But, in many ways, Etihad Airways today is quite different from what the airline was even ten years ago. We are now in the process of implementing a five-year transformation plan and have adopted a revised strategy positioning the airline as a mid-sized carrier with a focus on being commercially sustainable and on delivering high levels of customer satisfaction.
There are more than 12,000 employees which will grow as the business grows. Those people are drawn from 139 nationalities, a real cultural mix and an impressive example of people from different cultures working together. Etihad Airways currently flies to 71 destinations across 47 countries. There are currently 71 aircraft in the fleet: 15 Airbus A320 and A321; 5 Airbus A350 with a brand-new cabin; there are also 12 Boeing 777, five of which are freighters; and 39 Boeing 787, a very efficient aircraft that was very useful during the pandemic to keep operating with reduced costs. Across the fleet, the average age of aircraft is 5.7 years, quite young and it’s nice to have aircraft that are really efficient and which allow the airline to reduce its carbon footprint.
STRATEGIC THEMES AND PRIORITIES
We have identified at Etihad Airways a number of Strategic themes and priorities; first for the whole airline (figure 1).
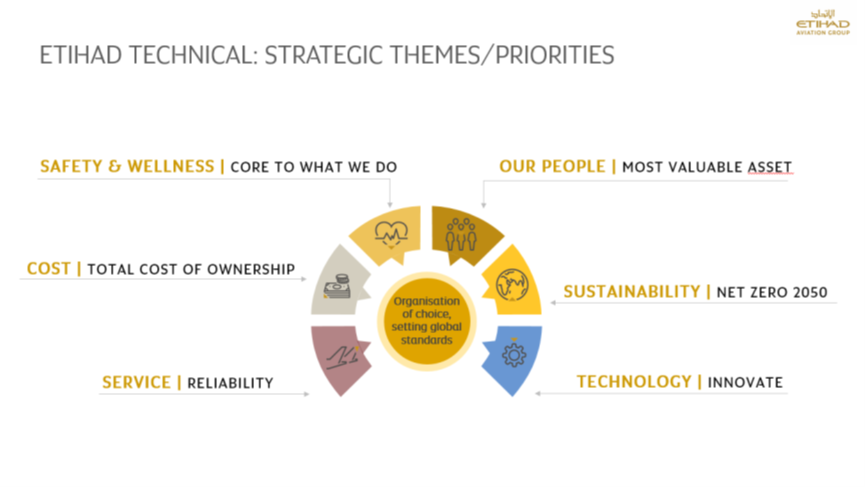
First and foremost is always Safety and Wellness which are core to what Etihad does and the number one priority. We live and breathe safety and every decision must be viewed in that light. During the pandemic, Etihad deployed a wellness program to provide passengers with the confidence that if they were travelling with Etihad, they could feel comfortable to be on board and that everything would be done to eliminate any sense of threat or stress coming fromCOVID-19: it was a really successful initiative. There is also a strong focus on our people who are considered the airline’s most valuable asset. Etihad invests in them and develops them to improve their skills and to develop the business.
With costs, it’s important the we make the right decision for the right reason so we have good control over costs, including total cost of ownership. Sustainability is a subject that gets regularly aired in the sector because everybody wants to be sustainable. Etihad has already taken a leading position with a number of eco-flights which readers might have read about; involving new technologies with a young and efficient fleet really helped to reduce the airline’s carbon footprint. There have already been some great successes and it is something that Etihad wants to continue to pursue with the objective to be net zero by 2050.
Of course, service is key; Etihad wishes to provide the best service to customers. Customer satisfaction, as already mentioned, is at the heart of our work. Finally, technology; like everybody, Etihad seeks to innovate but we want the technology to enable the outcome, it should not itself be the outcome, should not be the final result. What we do with the technology is the important thing.
Drilling further down, there are also strategic priorities and a digitization vision for the technical division (figure 2).
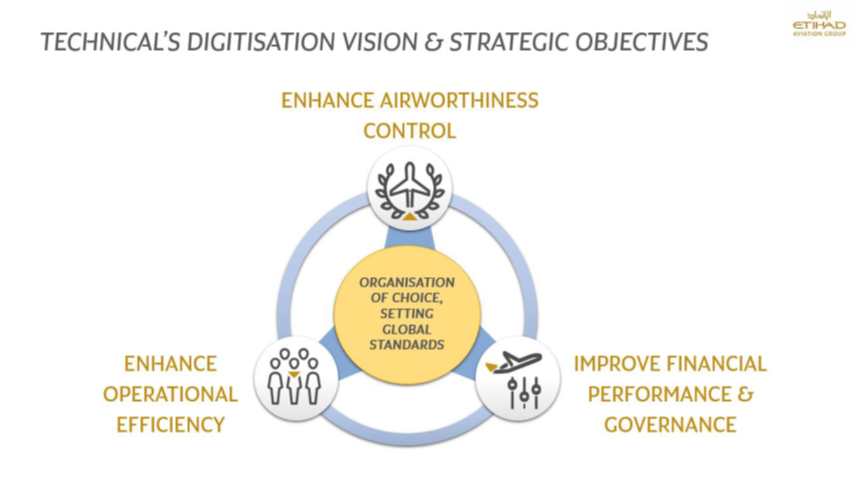
Those objectives have been refined to three pillars. First to enhance airworthiness control, then to improve financial performance and governance and, finally, to enhance operational efficiency. These three pillars will be used to achieve Etihad’s target or vision which is to be an organization of choice, setting global standards. This statement is the same as that which guides the executive team.
A FIVE-YEAR VISION
In 2018, we started with a new management team and a five-year vision (figure 3).
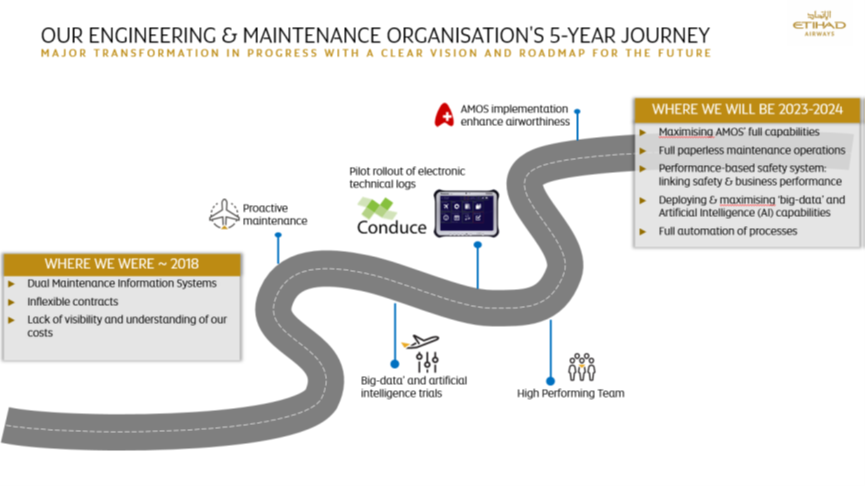
We knew where we were and where we wanted to be in five years, and had a clear roadmap. We initially identified that Etihad is using a dual maintenance information system which proved to be really inefficient. There were inflexible contracts with also a lack of visibility or understanding on costs; there was definitely room for improvement. In the five-year plan, we wanted to maximize the use of AMOS, our MRO system from Swiss Aviation Software, to exploit its full capabilities – we knew that we hadn’t made full use of the system. There was also an objective to become fully paperless and to link Etihad’s safety performance to the business’s performance and to be able to visualize this type of information. It was not always possible to make the best-informed decision based on the data generated from our systems. Another objective was to use automation for processes where that could not only be successfully achieved but could also be achieved quickly – a worthwhile investment.
There was a good vision with a fantastic plan, and Etihad had already started some initiatives but then COVID-19 came. Although some great starts had been made, everything had to then be re-imagined. Etihad Airways was already using AMOS and we knew that we wanted to improve our performance with the system (see above) whether that was going over to a full AMOS solution or adding to the information system. So, for this data migration exercise we transferred 60 million parameters from the old MRO system to AMOS in just one day. We had also already tested some systems linked to the maintenance, using some systems for big data to give us some confidence in the technology, plus we also identified something important which was our champions in the team who would be the high performing people to drive this change.
THE ETECHLOG8 PROJECT
One of the major projects implemented was the eTechLog8 (ETL/ELB) which we had to deploy at the worst possible time. On 23 March 2020, all of the passenger fleet was grounded. Nonetheless, the eTechLog8 project was deployed during the pandemic, over a few years (figure 4) and is now live across the whole fleet.
We’ll cover both the journey to implementation of the eTechLog8 and what Etihad sees as the approach as well as the key elements and the results achieved with this implementation. It reflects what we see as our core digital transformation values.
Let’s start with the key milestones of the project (figure 4).
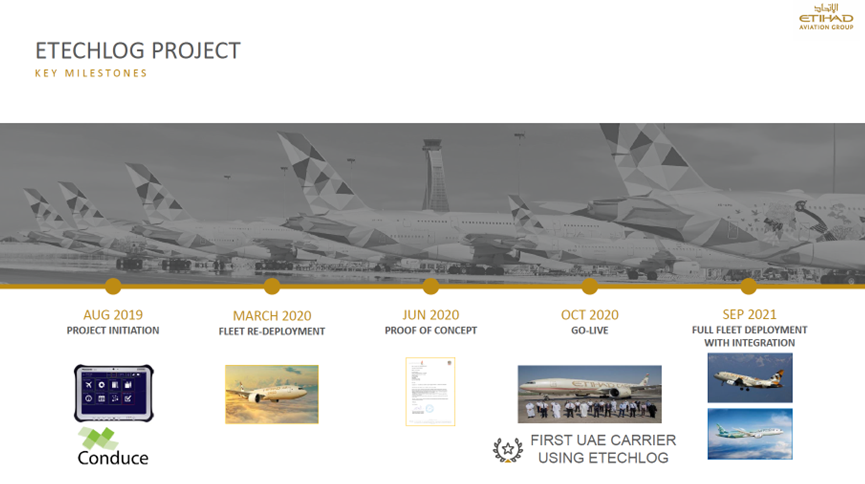
The project started with a mandate in August 2019 when Etihad Airways decided that we wanted to transform our log book system. The first thing we did was to select what we felt was the best partner with the best solution for Etihad’s needs. This was Conduce’s eTechLog88 solution. We partnered with Conduce to ensure that the airline had the right solution to support this ambition going forward. We also teamed up with our authorities early in this phase to ensure that they also took part in this journey of transformation because, at that time there was no operator in the UAE with an approved electronic techlog.
Things ran well for the first six months while we tried to make sure that the project phase was running as smoothly and as quickly as possible until, as already mentioned, COVID-19 hit the sector. That put a lot of pressure on the business without a single passenger aircraft flying. The project team with management decided that they had to take a critical decision to move backwards or forwards. The decision was taken to move forwards. The eTechLog8 project was re-deployed on the only fleet in operation, the freighters. Within three months we were able to transform the project onto the triple seven freighter fleet and approached the authority to give the go-ahead for a proof of concept, which they approved. That meant that Etihad was able to run the electronic log book and the paper log book in parallel. In a further three months, the go-live was agreed with the authority to go ahead and deploy the ETL/ELB on the Etihad Airways fleet. that made Etihad the first airline in the UAE to deploy an electronic techlog solution on their fleet.
Since then, a point was reached in September 2021 where it was possible to deploy the electronic log system across the whole fleet along with integration with the MIS and archiving systems. That was the journey and milestones but readers will want to know how it was done, how it was achieved and the approach taken to get there (figure 5).
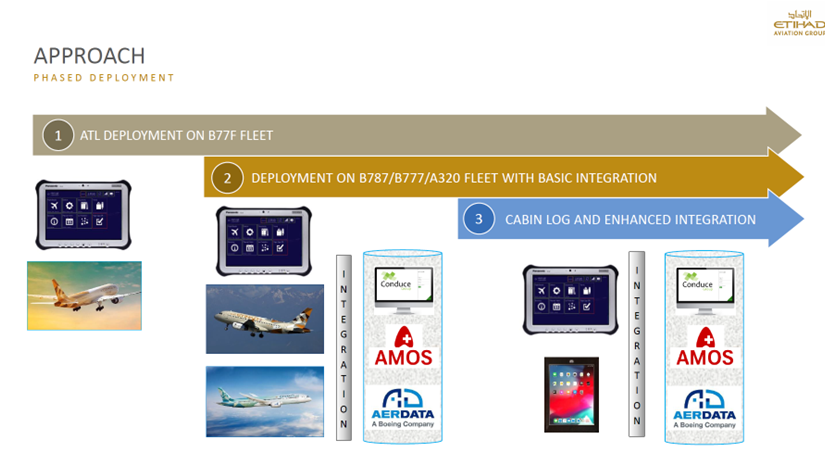
The first step was to make sure that the project was not too complex: we didn’t want to identify a lot of deliverables without being able to deliver, so the project was broken down into three key phases.
The first one was to keep it simple: remove the paper techlog, deploy the electronic techlog. That was done on the only fleet that was operating at the time, the B777 freighters, and the team made sure that they were able to sustain and satisfy the authorities that it would be possible to be completely competent on the electronic log system.
The next and the biggest phase was to deploy the electronic tech log or to expand it to the remaining aircraft in the fleet, B787s, B777s and the A320s. We also decided to go ahead fully with the integration with the MIS system and the archiving system. Today, the Etihad Airways fleet operates with these systems completely integrated.
A further phase which is also a continuing phase is to develop the cabin log solution so that Etihad is able to realize all the benefits of the digitization platform of the electronic solution plus develop enhanced integration with the existing platforms at Etihad Airways as well as looking for new platforms.
How we achieved that was with a lot of focus on two areas: the key elements of the project itself. One is the things that need to done to make sure that the projects is successful; and two is who will do the project.
We identified the very important elements of an electronic tech log deployment or implementation, the first being management of change. This change was no less than the whole organization getting involved in the new system, and that’s never easy. People do not accept change very well. We had to focus and make sure that we covered every element of this change process. We had to look at the existing documentation and procedures because a new platform, a new landscape meant there would be changes to procedures and processes. The device had to be configured to make sure that it gave the airline what it needed and that we changed where the device was giving more. The biggest challenge was training the bulk of the organization; pilots, engineers, outstations… and that was a massive exercise and undertaking.
We went on to build up the integration with the MIS system, a lot of testing was involved with new versions and old versions; there was a lot of development on that area. The final phase was coordinating a deployment plan which was not only about an electronic log system that was coming in but also about making sure that we had the right resources, that the aircraft were on the ground on time for the deployment with all the other departments prepared for possible impact through the deployment having issues. It was a massive exercise to make sure that everything went smoothly and that had to be done with a very competent team (figure 6).
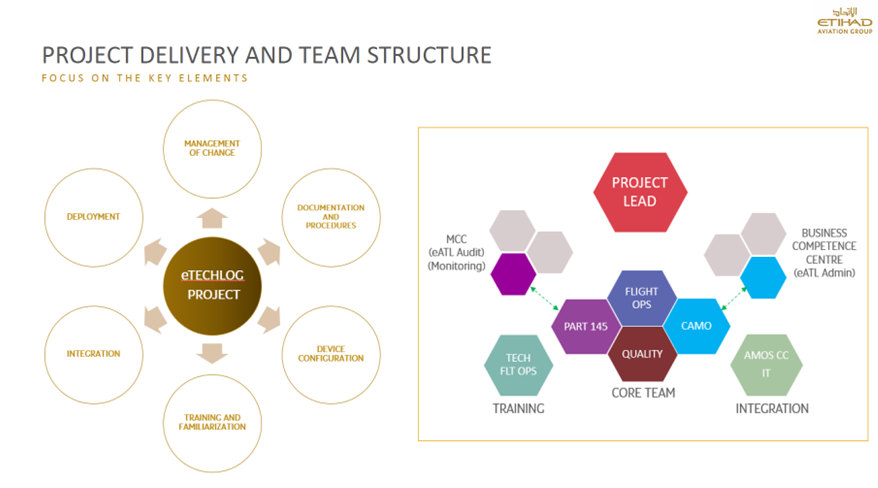
On the right side, you’ll see that the team that wasn’t only eTechLog8 specialized. We assembled a team from within the organization; our Part 145, our flight operations, our CAMO and our quality; we also made sure that the MCC (Maintenance Control Center) and the Business Centers were fully equipped to support this project. The Training Department along with the IT and the AMOS departments were supporting the project to ensure that it was all implemented together.
It wasn’t only about having the people from those departments, they were staff who had no previous project experience but we approached it with the same philosophy of investing in our people, making sure that they are able to stand up and deliver where it mattered most. All of the focus elements and the teams put together made sure that the project was linearly progressive to avoid having any department or any core area left behind. The project was able to deliver on all fronts and in all departments together at the time of deployment.
POST DEPLOYMENT
Operational data from the post-deployment period showed a success story. eTechLog8 has been deployed on 74 tails in the active fleet plus it covered some parked aircraft (figure 7).
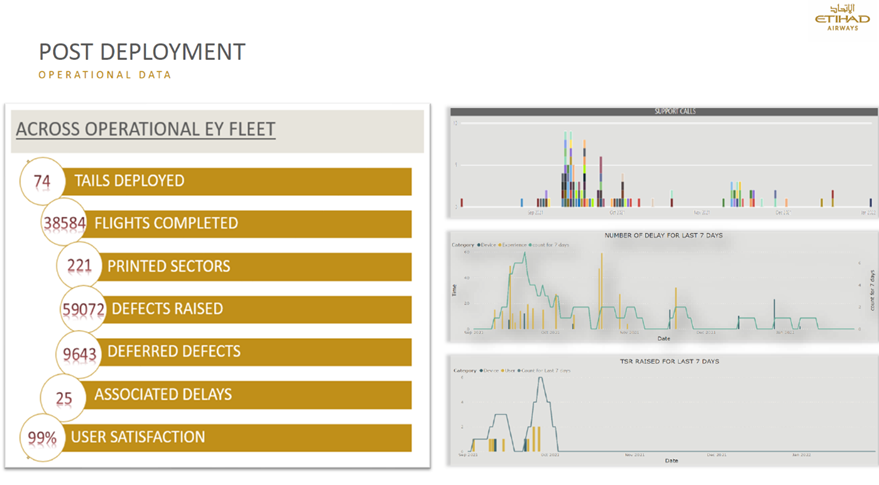
Over 38,000 flights had been completed in eTechLog8 at the time of writing; it’s still running and the 221 printed sectors refer to having a back-up system in case there were any transmission failures and which were able to be used without any delay to the aircraft. More than 59,000 defects have been raised through the system with nearly 10,000 deferred defects running (closing and opening). It was not a smooth run to start with and there were a significant number of delays that related either to a limited knowledge or user interface or just clarifications. However, we made sure that we addressed these delays, there was a supporting system to ensure that delays were immediately addressed and rectified or supported. As a result, user satisfaction, measured through a user survey, was 99 percent either relatively happy or very happy with the new system.
The post deployment statistics are on the right of the figure, statistics that Etihad wanted to use to measure how much of a challenge this deployment would be. The MCC received supporting calls and you will see a big spike at the beginning when the system was first deployed and there were a huge number of calls coming in to the MCC which had been prepared to make sure that they would be able to address most of the regular queries. As the deployment went through and stabilized, the number of calls reduced. Then, with a second phase of deployment, there was another increase in calls with another set of queries and the stabilization again.
Initially there was a spike in delays which, again, were related to user experience or lack of user knowledge and them calling up the MCC (see above). Most delays were less than 15 minutes and reportable delays were less than ten minutes but we wanted to still measure every single delay and find out what the reasons for the delays were. Similarly, reportable events, whether it was the device or the process, were monitored so that, right after the initial spike there was a drop. All this data was then presented back to the authority to make sure that they could see the confidence in Etihad being in control of the whole process. It wasn’t that there were no issues, there were issues but the team was transparent and knew that we were able to advise and bring solutions to the process and to the issues in good time and to take corrective action.
BENEFITS FROM DIGITIZATION
In figure 8, we’ve illustrated what is quite normal for any project but it is a matter of how the change is presented and what an electronic and digitized solution brings to the environment.
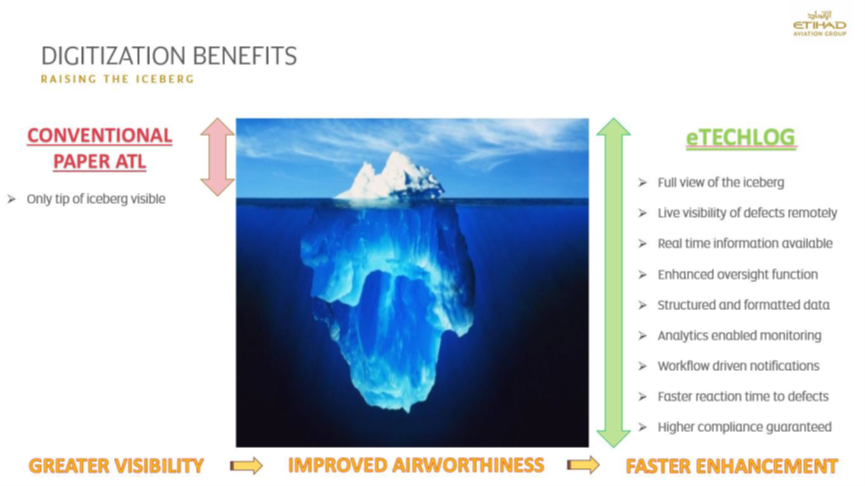
The paper tech log is just a conventional system and the information it records is only the tip of the iceberg. Whatever happens on the paper tech log doesn’t come back in for a long time which means one cannot see everything that’s running behind the scenes. But, with the electronic tech log it is possible to get better visibility of the whole iceberg with: a full view of the iceberg; live visibility of defects remotely – real time information for enhance oversight; structured and formatted data for righting issues with engineers; and analytics enabled monitoring which was put into an analytical tool to show the data was being correctly processed. There were also workflow driven notifications with data driving any notifications, any warnings needed somewhere for someone to action immediately. The result was faster reaction times and higher compliance guaranteed.
In a nutshell, the eTechLog8, the digitization, the transformation brings greater visibility leading to improved airworthiness while pushing Etihad to get faster enhancements across the organization. Overall, figure 8 is a key slide for take-aways because it really shows what the eTechLog8 will create. It will create a lot of problems because the increased visibility will suddenly raise a lot of previously hidden issues but such problems are not linked to the eTechLog8, they were already there but not visible. Nevertheless, it is something that people in the organization need to be alerted to at the outset of the project.
Also, for those who are interested in starting to use eTechLog8 technology, this article does not say whether you should or should not go for this technology; it’s more about asking yourself, how long do you want to stay with a conventional paper ATL which only shows the tip of the iceberg, how long do you want to stay in that situation?
KEY AREAS AND CRITICAL SUCCESS FACTORS
Etihad identifies critical success factors for all projects undertaken (figure 9).
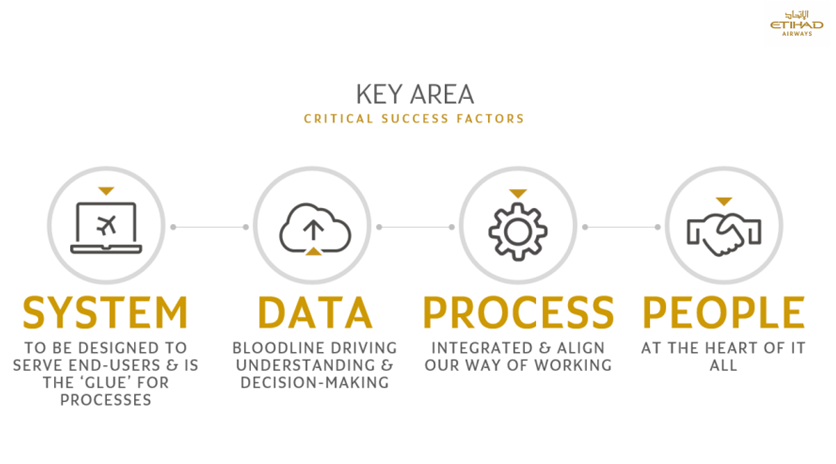
First is the system which we can compare to the body because it is a critical element and needs to be a good fit for your own airline. Data is something really important. There must be clean data plus you need to know how to use that data. The process needs to be aligned with the system and the process will feed the data to the system. Finally, the people who are the ones who will drive the change, will be able to use the system, provide good data, and leverage the potential of having this data. At Etihad Airways, we were amazed at how much we were getting from the people just by democratizing access to the data and giving them the possibility to use the data, link it together.
LOOKING TO THE FUTURE
Nothing can stand still and already Etihad Airways is looking to its future plans (figure 10).
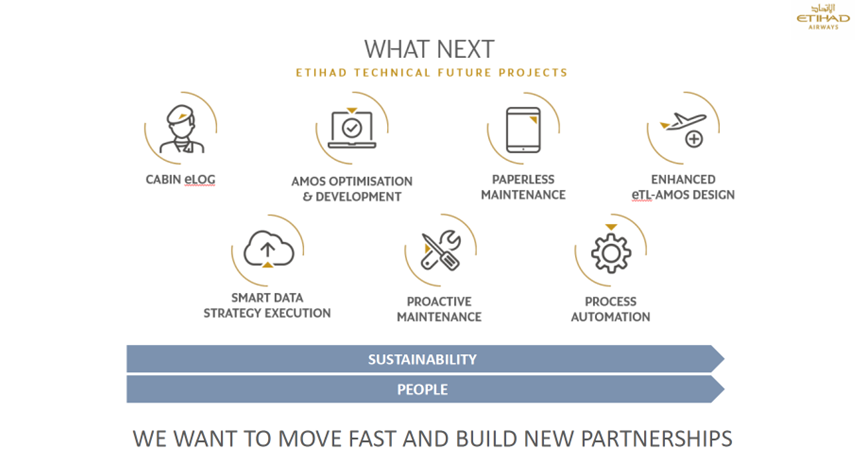
Now that the deployment has been achieved, we want to start talking about the Cabin eLog solution. We also want to participate in AMOS optimization and development. Etihad has some very competent people supported by a great AMOS Competence Center. We want to progress with paperless maintenance, something that every airline and operator should aim for. The aim is to enhance the eTechLog8 and AMOS design. Etihad has one of the best integrations currently in the market but that is still not fully satisfying and we can help our people to improve those integrations with AMOS and with the technical system. The focus is on smart data as opposed to big data. Etihad has already tried big data solutions and wants to work with them but has also identified that if we don’t know how to use the data, we don’t get to best outcome. Smart data involves the people in the business who can really use the data and give a meaning to the data.
Proactive maintenance: here again we have tried a system but were not very satisfied and there is currently a lot of information with the current format and there is a lot of work that can be done in this area before we try to predict something which is not yet happening. Our priority is to work on proactive maintenance. Etihad Airways has already had some great wins on process automation which is definitely something that the business wishes to progress.
Overall, this project should support Etihad’s sustainability target and help with the development of our people. We want to move fast and, to be able to achieve that, we want to build new partnerships. So, if you are one operator, if you are one software development company, and if you’re looking for a partnership with an airline, we’ll look forward to connecting with you. We at Etihad certainly gained from the partnership with Conduce.
Contributor’s Details
Eric Bogner
With 22 years of experience in commercial aviation industry, the last 14 with Etihad Airways, Eric has managed various roles in both maintenance and operational environments, is passionate about aviation and has been driving executing key projects as part of Etihad Technical’s digitalization strategy. He led key workstreams as part of Etihad Airways MIS transformation and was the Project Manager for the implementation of the integrated eLogBook.
Arish Sayed
Being an active part of technical operations for the last 20 years, Arish has been directly involved in key transformational projects with Etihad Airways.
These include the Electronic Logbook and MIS transformation, among others, having overseen their successful adoption and implementation within the organization.
Arish has been a lead aircraft engineer and has also been involved with Aircraft Transfers, Entry into Service and 145 Training as part of his extended profile.
Etihad Airways
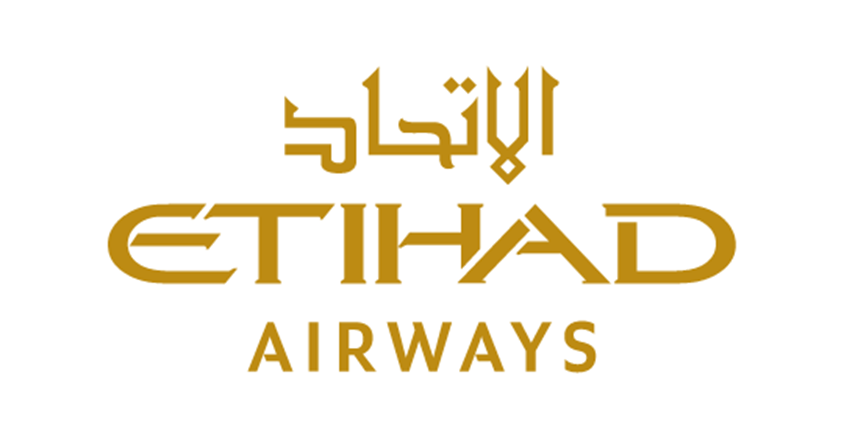
Etihad Airways, the second flag carrier airline of the United Arab Emirates flies to passenger and cargo destinations in the Middle East, Africa, Europe, Asia, Australia and North America. The fleet includes both Airbus and Boeing aircraft types: Airbus A320/321 and A350; Boeing 777 (including freighter variant) and 787; one of the most advanced fleets in the world. Etihad Engineering is the largest MRO service provider in the Middle East.
Comments (0)
There are currently no comments about this article.
To post a comment, please login or subscribe.