Articles
Name | Author | |
---|---|---|
CASE STUDY: Etihad Airways bring cockpit and cabin logs together | Masoud Al-Alawi, Manager Aircraft and Digital Operations, Etihad Airways | View article |
CASE STUDY: Digitalizing the warehouse at Finnair and DHL Supply Chain | Otto-Wilhelm Orumaa, Operations Excellence Manager, Finnair | View article |
CASE STUDY: A Better Documentation Solution for Cebu Pacific | Hazel B. Ocampo, Manager – Configuration Management – EFM at Cebu Pacific Air | View article |
CASE STUDY: Joramco’s new system offers a better way of working | Shakespear Nyamande, Vice President of Planning at Joramco | View article |
CASE STUDY: Digitalizing the warehouse at Finnair and DHL Supply Chain
Author: Otto-Wilhelm Orumaa, Operations Excellence Manager, Finnair
Subscribe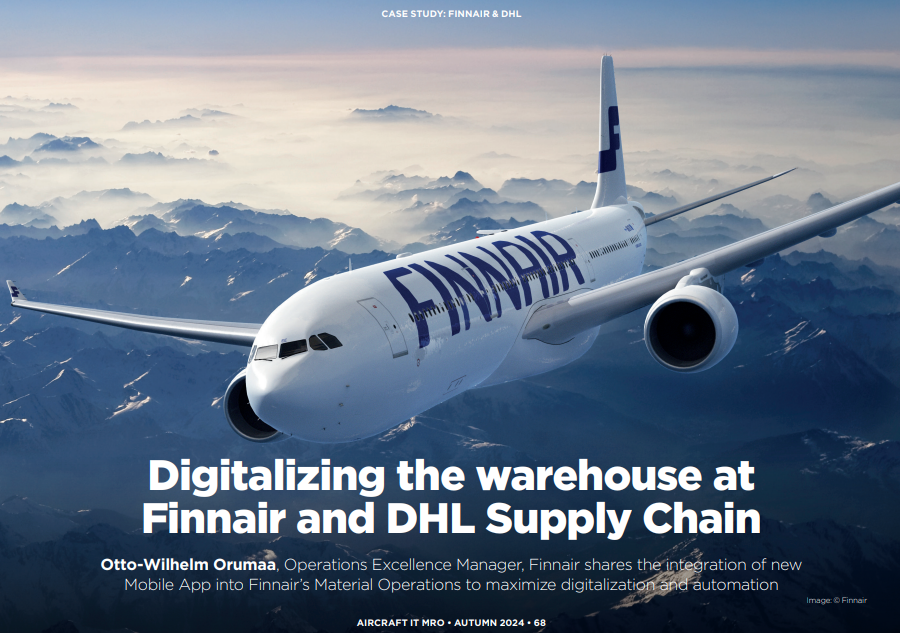
Ottto-Wilhelm Orumaa, Operations Excellence Manager, Finnair shares the integration of new Mobile App into Finnair’s Material Operations to maximize digitalization and automation
In this article, I plan to cover the implementation of AMOS’ Mobile App into Finnair’s materials operations and the part that DHL Supply Chain has played in that. But first we’ll introduce readers to the main protagonist businesses, Finnair and DHL Supply Chain.
INTRODUCING THE PEOPLE AND BUSINESSES
Having worked at Finnair for more than six years, I have been involved with different developments and projects including the subject of this case study, AMOSmobile/STORES implementation. Based the Material Operations department in Finnair, I am a local AMOS Super User and, for the AMOSmobile/STORES project, I was the project owner.
A few words about Finnair which was established in 1923, so just over 100 years old, and is the flag carrier for Finland. Compared to some, it is a small airline with a fleet of 80 aircraft consisting of Airbus, Embraer and ATR aircraft and a team of more than 5,000 employees. Finnair has been rated ‘Best Airline in Northern Europe’, according to Skytrax for eleven years in a row.
DHL Supply Chain started in April 2020 and, at the time of writing, there were 50 employees in the organization. They serve aircraft component and maintenance functions on a round-the-clock 24/7 basis. There are three main locations: VAKE-B serving as a logistics center where they receive parts and send all the parts to locations on the airport as well as to various outstations in the world. The main warehouse is located in Hangar 7 where Finnair’s main maintenance operations are based. DHL Supply Chain also has a small warehouse in Hangar 11. In addition to that, there are two trucks that are effectively mobile warehouses serving different aircraft at the gates around the airport with immediate replacement parts – the trucks carry the most used parts.
SWISS-AS AMOS IN FINNAIR
AMOS From Swiss AviationSoftware (Swiss-AS) has been Finnair’s main MRO IT tool since 2012. There is a Super User for each of the nine divisions in the airline, including the departments such as Engineering and Material Management. There are also several Key Users within each area, acting as main focal points and first points of contact for the end users to support them with addressing different issues as they arise and general developments. AMOS has been in daily use with the majority of Finnair Technical Operations personnel. We aim to utilize AMOS to the fullest extent possible; so, whenever there is a new module or a large amendment, we try to test it and review it to understand whether or not it would work for Finnair, and some of those are brought into active use in the airline. One such new module is AMOSmobile/STORES (AMS) plus Advanced Re-order Proposal (ARP) which supports Purchasing. In addition to the modules, we also utilize the data that AMOS generates daily whether that’s just an overview for the management or also a descriptive analysis – people trying to understand processes and how things happen or how they work. It’s also worth mentioning that we have integrated AMOS with the external Records Management System (RMS) so that all the work orders and digital documentation that is created inside or outside of AMOS can be then be collected to the RMS archiving process using automated solutions for achieving that.
AMOSMOBILE/STORES PROJECT
Now, coming to the heart of this article, the AMOSmobile/STORES project started in October 2022. Whereas previously we had been working in an old-school manner with paper and pens, the aim of this project was to transition to the mobile application and device and this was where the warehouse operation was a big thing. We wanted to increase process times and reduce the number of steps in a process. The whole idea was to get better control over the processes and material movement plus to gain other benefits the change would bring stepping forward to digitalization and automation. Together with the mobile device and application, we also took additional new AMOS modules to use such as Material Allocation that automatically allocated materials based on the part request; then, along with that, Picking List Management module which acts as a to-do list for the store operatives.
The project team saw collaboration between Swiss-AS, DHL Supply Chain and Finnair: we were able to learn from each other and refine the successful cooperation that we had enjoyed for several years already. The outcome was that Finnair was the AMOSmobile/STORES launch customer to go live with the solution.
The first workshop was held when the project started in October 2022 (figure 1.1).
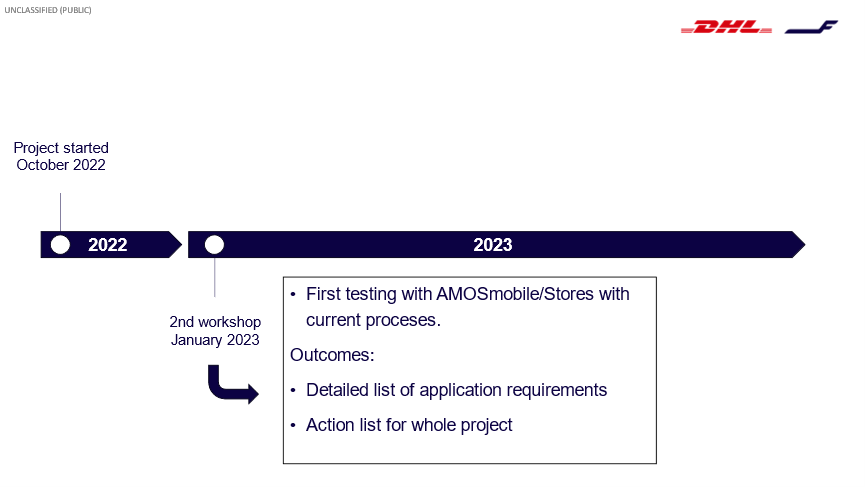
Figure 1.1
The second workshop was in January 2023 (figure 1.2).
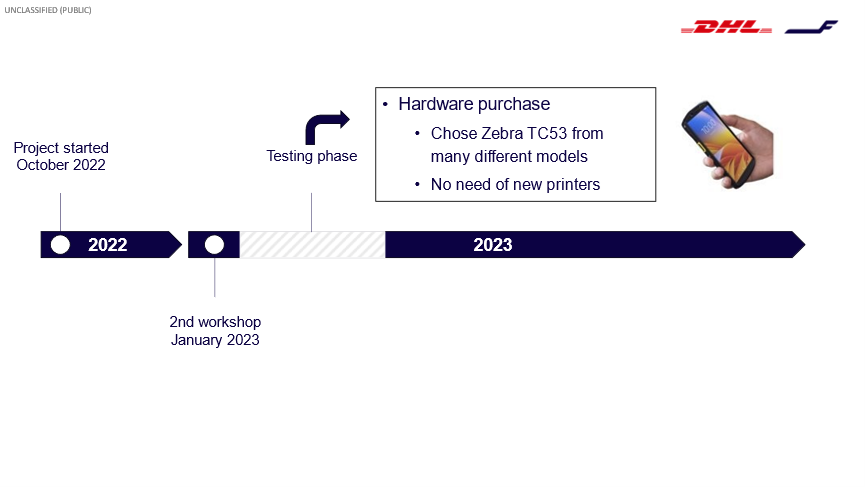
Figure 1.2
In that workshop we got to test AMOSmobile/STORES for the first time, with our and DHL Supply Chain’s current processes. The outcome was that we got a detailed list of application requirements to fit our current processes. Our goal was not to have major changes to the current ways of working in warehouse operations. On top of that, we created an action list for the whole project through 2023 all the way to the go-live.
Going to the next phase, we started testing different devices with AMOSmobile/STORES before deciding to go with the Zebra TC53 mobile device because of the brightness of the display, great battery life and the prospect of Android updates all the way to Android15. Also, we tested mobile printers held in the warehouse operations but we could see that they would not work in the current environment because the DHL Supply Chain warehouses are quite small; in light of that, we went with server printers that are located quite well already.
The third workshop was held in April 2023 (figure 1.3).
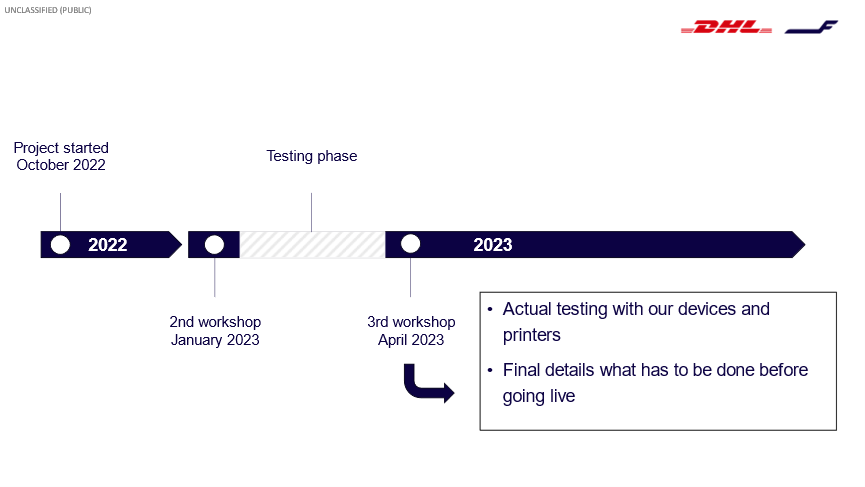
Figure 1.3
In this workshop, we tested AMOSmobile/STORES with our own and DHL Supply Chain’s devices and printers. This was led by Swiss-AS and we got the final details of what things had to be done before the actual go-live.
Then, in the summer and the start of autumn, we undertook final testing and making sure that the software, hardware and connections worked perfectly, plus we had to train DHL Supply Chain’s employees, the storemen, where we had to make sure that they were OK with the change and ready for the go-live (figure 1.4).
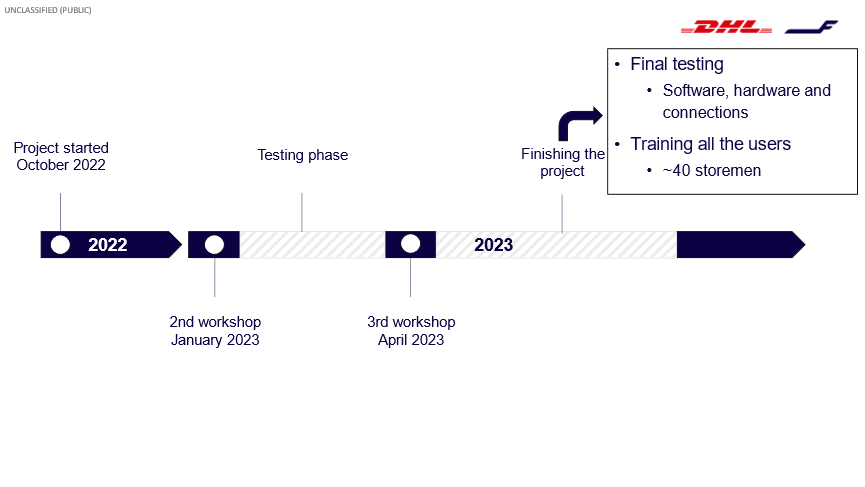
Figure 1.4
Finally, in October 2023, we got to go-live with the application (figure 1.5).
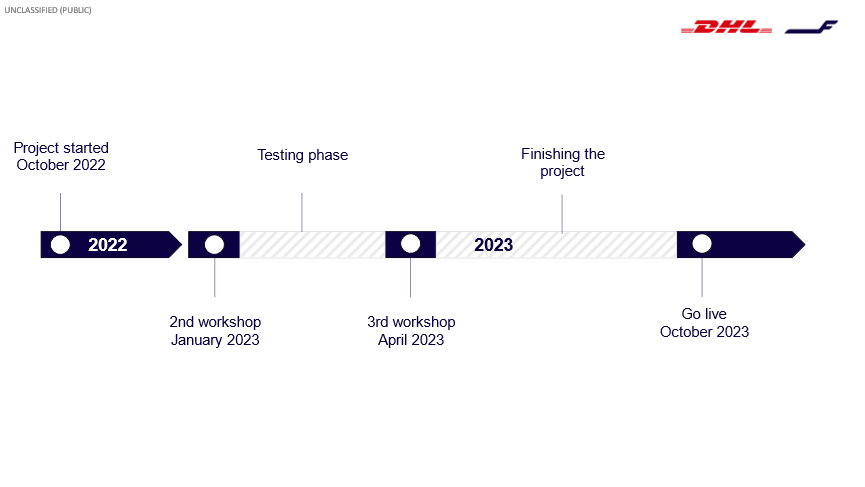
Figure 1.5
The day was excellent and went well and everything is now working as planned. Now, we’d like to show readers an example using the picking process to highlight the improvements in our processes. In addition to the picking process, we are also using the AMOSmobile/STORES application with inventories, location management and returns.
PICKING PROCESS EXAMPLE
Before AMOSmobile/STORES, the picking process looked like figure 2.1.
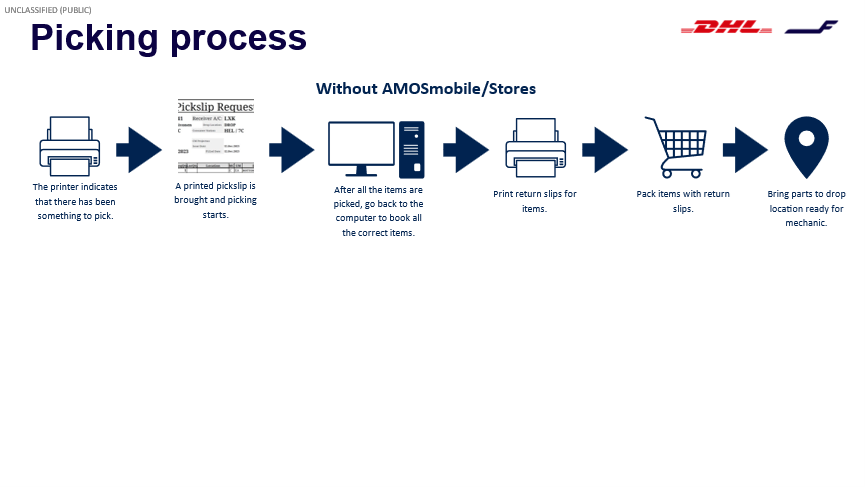
Figure 2.1
When a new order was printed out, that was an indicator to the warehouse and it meant that the store man had to find and fulfil new orders all of the time to make sure that they knew exactly when a new order came to the warehouse. They would take the paper and pick all the ordered parts from the warehouse before bringing them together. Then they had to go back to the computer and book out all of the parts that they had taken from the shelves. Also, they had to print out the return slips that would be needed if a part was returned to the warehouse. Finally, they would back the items with the reference slips and take the part to the pick-up shelves ready for the mechanic.
With AMOSmobile/STORES, the goal is the same sort of process as in the bottom line of figure 2.2.
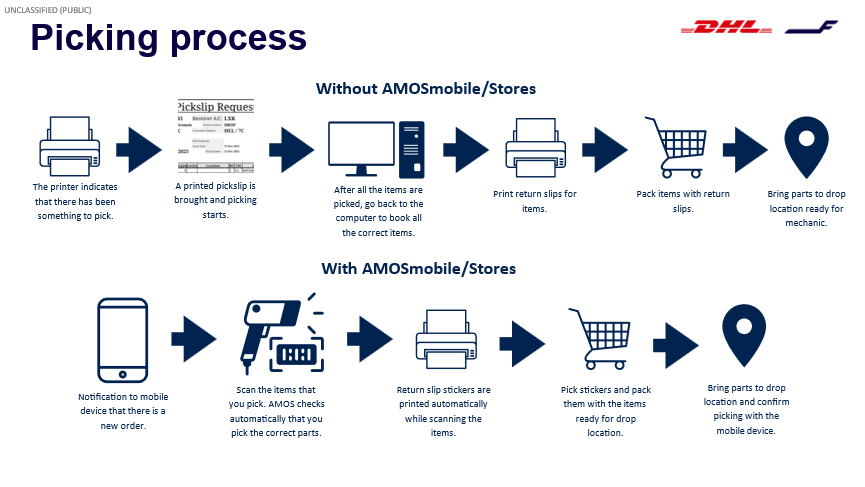
Figure 2.2
However, at the time of writing, the notifications in AMOSmobile/STORES application weren’t yet work correctly for us but we were getting there. The best part in this is that the store man can actually scan the parts and AMOSmobile/STORES will validate whether the part is correct and can be booked in this certain order. Reference stickers are also issued automatically so that we don’t have to print them manually anymore. When the store man is ready for picking, they already have the reference slips ready in the printer and waiting for them. Then all they have to do is pick those parts and drop it in the pick-up location, confirm the bookings in the application and the mechanic knows right away that the picking has been done and the parts are ready for them.
LESSONS LEARNED
Among the lessons that we learned from the implementation process (figure 3), the main thing was to properly understand the whole process and the details behind the change and behind the project.
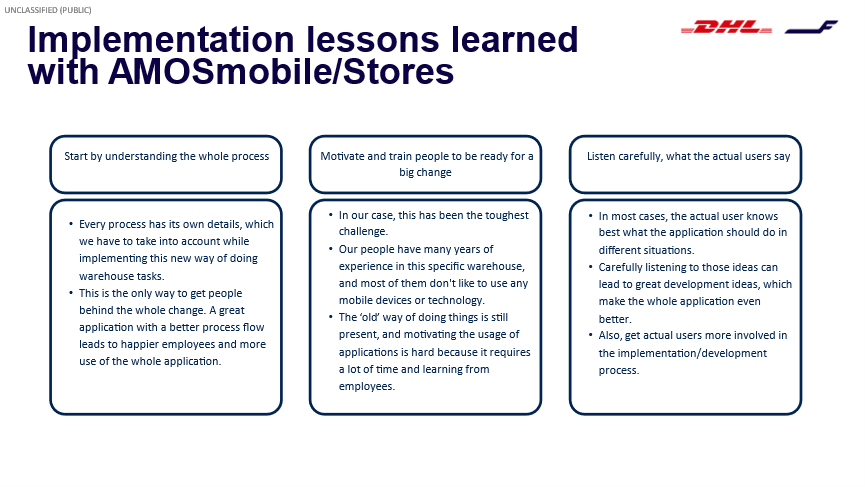
Figure 3
Together with that, was that you must be able to ‘sell’ it to the end users on the team. People are often wedded to and comfortable with their old ways of doing things so that changing that mindset, especially in the store or the warehouse, can be difficult. So, if you yourself understand what will be the benefit gained at the end of the process, you’ll be better placed to support the change with others in your team.
The last two lessons learned are from the warehouse. We saw that the motivating and teaching people for this big change was the key factor and it is something on which we are still working because our people tend to have long careers in these warehouse operations and are used to doing things in the old way, and, at the moment, they also have the capability to use the desk-top which means that many of them are reluctant to use mobile devices with our operations.
The last point we have put here is that you have to listen carefully to the end users; they have lots of great ideas for the application and processes, so lots of great continuous improvements have come from the warehouse.
We hope that, for any readers considering a project like the one we have described, you will find it useful to know about our experience and, especially, about the lessons we learned as a result of that experience.
Comments (0)
There are currently no comments about this article.
To post a comment, please login or subscribe.