Articles
Name | Author | |
---|---|---|
What IT can do: The OEM perspective | Henrik Ollus, Customer Success Manager, QOCO Systems | View article |
Case Study: A lifelong digital maintenance record for aviation assets, Part 2 | Karl Steeves, CEO, TrustFlight | View article |
Case Study: Digital Transformation at Etihad Airways Technical | Eric Bogner, Manager Strategic Partnership and Performance, Etihad Airways and Arish Sayed, Manager Projects – Technical, Etihad Airways | View article |
Case Study: Enter Air’s post-pandemic upgrades are supported by a flexible MRO IT solution | Konrad Dymowski, Enter Air | View article |
Case Study: Enter Air’s post-pandemic upgrades are supported by a flexible MRO IT solution
Author: Konrad Dymowski, Enter Air
Subscribe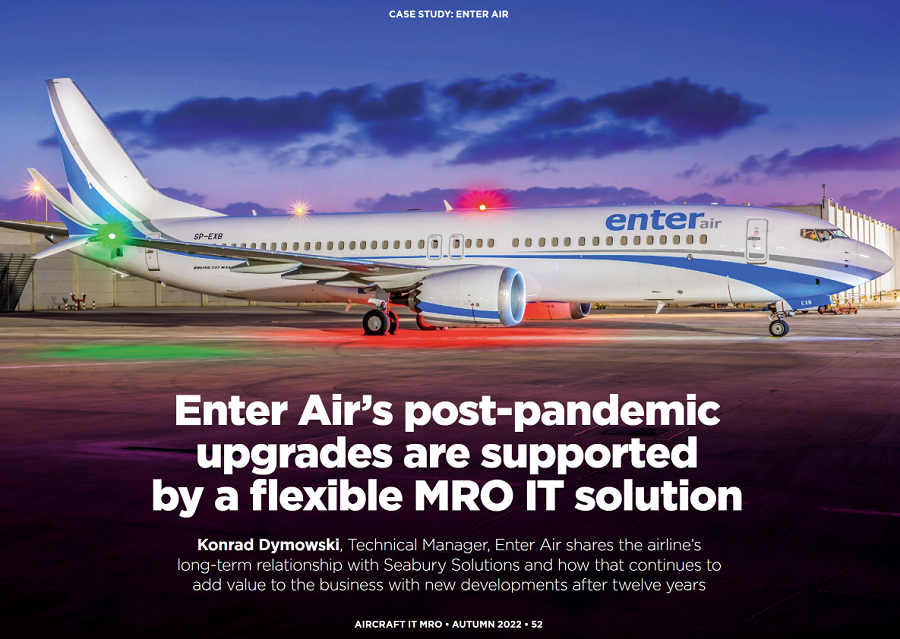
Konrad Dymowski, Enter Air shares the airline’s relationship with Seabury Solutions and how that continues to add value to the business with new developments after twelve years.
Enter Air is an airline launched in 2010 and located in Poland flying to Paris, London Gatwick, Basle, Greece and Spain, generally carrying passengers on a charter basis. Mostly, this is tourists in the summer whereas in winter, autumn and spring, it’s more ad hoc flights and special flights for military customers, for sports customers (players and fans). The fleet is Boeing 737 with 23 NGs and 4 MAXs. This case study is about a specific function that a satisfied client wanted from their long-standing MRO IT solution provider.
DECIDING THAT A NEW MRO SOLUTION WAS NEEDED
A number of factors lead Enter Air to the decision that a new MRO software and fleet management program was needed. From 2011, there were discussions inside the airline about implementing MRO software instead of using Excel workbooks and other Microsoft products to manage MRO processes and workflows. It was understood that, in order to grow the fleet, it would be necessary to have a developed aviation software system which could support the CAMO. Seabury, having started in 2002, had only recently entered the aviation market and, being a young airline, we felt there would be an advantage to be gained from working and co-operating with another business at roughly the same development stage as Enter Air, and to develop the system based on the needs of Enter Air.
SELECTING AND IMPLEMENTING A NEW MRO SOLUTION
The process started with a normal RFP (request for proposal) from the responses to which Enter Air selected three short-listed vendors from which group the final selection was made for Alkym from Seabury Solutions. A key reason for that was the developmental compatibility of the two businesses; the Enter Air team highlighted to Seabury Solutions that they were keen to have a partnership in which they could grow with the IT vendor. For that reason, the relationship between the two has always been special not, only from a technical support point of view but also with special requests: recently at Enter Air there have been some large-scale special projects to improve the operation: the airline worked together with Seabury solutions on those challenges. After an eleven years relationship, everything is renewed whenever there is a push for a new objective and new levels of excellence. Working with Enter Air, Seabury Solutions developed a planning optimization tool (see below).
ALKYM; THE SOLUTION CHOSEN FOR ENTER AIR
Three years ago, Enter Air approached Seabury Solutions with the need to have a planning optimization tool that would enable them to better understand flight scheduling as well as to understand all, of the work orders that are created, together with the job cards that need to be executed inside those work orders. It sounds simple but this was a huge endeavor not only from a software development point of view but also as far as the user interface is concerned. Both parties worked together; Seabury Solutions designed the first stage of the tool, Enter Air approved it and Seabury started developing the actual solution which is now an established solution used by Enter Air plus it gives Seabury a great inroad into flight operations because it’s possible to combine flight scheduling with maintenance activity. That was a useful project on which both parties worked and there are more to come.
At a high level, Alkym offers control and management software for aircraft maintenance, catering for technical operations and logistics operations. Furthermore, all of those areas have inside of them different applications that communicate with each other, it is an integrated solution that all works on a platform that has been developed over twenty years. The philosophy of that platform is empowering the end user. Everything that Seabury does is about how the user could modify it, use it and extract data so as not to have to keep returning to the vendor for reconfiguration of the software.
CHALLENGES ENCOUNTERED
During the time when COVID had to be considered, the Enter Air team requested Seabury Solutions to finish a particular interface which communicates the airline’s Operations with the Maintenance, Repair and Overhaul (MRO) operation. It’s a massive project, the type of project that does not require too frequent site visits but still needs visits every two or three months. With COVID, that was impossible so it all went online which was a challenge and there was some delay. It meant there had to be some creative ideas to replace the on-site presence with online alternatives. One specific delay was the development of the requested interface based on SPEC 2000 Charter 80.
This is an important factor from Enter Air’s point of view; with the definition of the interfaces, we also have plans for our next steps, for future interfaces or improvements. When COVID started, Enter Air was significantly affected by the financial costs. So, it was necessary to put all projects on hold for nearly two years which meant a two-year gap for new projects and developments. Now, the airline sector is once again on a firm footing and Enter Air has re-started conversations about future projects, including working alongside one of the project managers from Seabury with normal co-operation resumed.
What was found to be pleasantly surprising at Enter Air, with projects there having been long-term and not being certain of the effects from the delays, was that, once the re-starts got underway, things picked up quite smoothly.
TRAINING, SUPPORT AND REGULATORY APPROVAL
For a new customer to a solution, training is very important. However, in the case of Alkym at Enter Air, although the system is well-developed with many options so would not be easy to learn in one two-week class even working intensively, Enter Air has been using Alkym since 2011. That meant that training was not necessary but Seabury did make visits where one of their project managers went to the airline to work side-by-side with users on the new tool. As important as training is the continuous support that Seabury Solutions maintains for Enter Air and, indeed, all customers. That allows both parties to regularly review how the solution is performing and, as importantly, how it is affecting the processes in the airline. The system is built for everybody but specific airlines or CAMO requirements or even the regulator might have other requirements and Seabury’s continuous support ensures that each airline can ensure the system meets their own needs.
The majority of improvements in the system do not need regulatory approval. The system itself, when it was first implemented, needed approval. Future developments that Enter Air is going to arrange with Seabury will probably need CAA (Civil Aviation Authority) approval. For instance, one such development will be a more developed interface between Enter Air’s two system providers and that might well need approval; but small improvements do not need to be approved because the system and control of the system is not fundamentally changing the way people work, it’s just improvements. With CAA audits twice a year, the auditing on the system is constant so that the CAA knows exactly how the system is behaving and what changes are implemented. Seabury has many years of experience working with CAAs around the world through their safety oversight software and has a number of CAA customers.
LESSONS LEARNED AND ADVICE TO OTHERS
One thing that, on reflection, could have been done differently, is that we should have devoted more time to the change process and/or arranged for more in-site support. As a specific example, the Maintenance Program report was covering all the information needed but the format that Enter Air wanted to use to provide that information to the civil aviation authority was very specific to them. So, in the spirit of Seabury Solutions’ philosophy of empowering the end user, the vendor brought forward a development that had been scheduled for the next version of Alkym and instigated it right away. The development process was accelerated and now Enter Air can customize their own maintenance program reports. If ever changes need to be added or removed, the airline can do that for themselves while, should there be any technical support needed, they can call Seabury Solutions. This all fits with Seabury’s continuing to visit customers for up to a few months after a new implementation or upgrade. Those interactions ensure an all-round view of the system in use, and how to resolve any problems that might arise.
For other airlines who might be considering a similar development to that undertaken by Enter Air, we’d suggest that a key feature that we were looking for is flexibility. From discussions with colleagues around the sector, it seems that the biggest software providers are good for a ready solution for each operator. Each CAMO, each technical department, each airline is organized in its own specific way; so, a system that is flexible and can adjust to the operator’s or airline’s needs is the most important consideration. It is important to know whether the system under consideration can be tailored to the user’s needs plus how they will see the system in the end. It is also very important to know the provider’s manpower resource, how fast changes can be made, how long it would take in adjusting the system, how often there are system updates. If the software cannot be tailored to the user’s needs, then it’s not a solution.
BENEFITS REALIZED
The biggest benefit that we have appreciated at Enter Air is that the system is tailored for the airline’s needs. We did not have to adjust to the system but rather the system was adjusted to fit the airline. As a result, we are very confident that the system is controlling our CAMO and, from that, each responsibility, whether that is logistics, spare parts control, warehouse invoicing, maintenance tasks and planning, or all of the engineering responsibilities. In each of those, Enter Air is able to be very confident that the software is handling the work reliably.
NEXT STEPS AND FUTURE PLANS
There are a few big projects on which Enter Air is working with Seabury including improvements in control of the communications between the airline and the maintenance providers using the on-board tablet. Enter Air has another provider who provided the electronic technical log book (ETL/ELB) system. So, we want to connect the two solutions with a two-way communication between them. This will be a huge improvement on which we are working now. But, overall, Enter Air is making improvements all the time: we don’t wish only to use the system as it is because, at any stage there will always be room for improvement.
Contributor’s Details
Enter Air
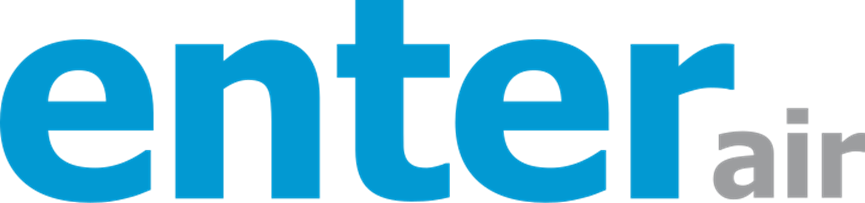
Enter Air is the largest charter airline operating in Poland and also the largest private air carrier in Poland. The Group offers connections to the leading Polish and international travel agencies, flying to over 30 countries, ranging from Iceland and Portugal to Kenya and Thailand. In 2017, Enter Air carried two million passengers, of which 1.5 million were to and from Poland. The fleet consists of 23 Boeing 737-800 aircraft and four Boeing 737 MAX 8.
Seabury Solutions
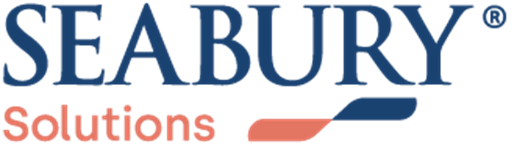
Seabury Solutions delivers IT solutions to enhance operational and financial performance. Utilizing decades of technological expertise that knowledge has been leveraged into a suite of products that enhance decision making for Asset Management, MROs/M&E, Regulatory Compliance, and Safety Oversight & Performance Analysis. Alkym is a Maintenance Software, specifically designed to enhance operational & financial performance. Originally developed for Aerospace & Defense, the M&E/MRO Software has been refined to also cover Asset Management for multi-industries.
Comments (0)
There are currently no comments about this article.
To post a comment, please login or subscribe.