Articles
Name | Author | |
---|---|---|
White Paper: A more efficient maintenance data standard | Iryna Khomenko, Manager, Operational Efficiency, IATA TechOps | View article |
White Paper: A lifelong digital maintenance record for aviation assets Part 1 | Karl Steeves, CEO, TrustFlight and Jack Hsu, Senior Manager, Boeing Vancouver | View article |
Case Study: All change for the better at Mexicana MRO | Enrique Guido, CFO, Mexicana MRO Services | View article |
Case Study: Increasing engine on wing time at Neos Air | Ivan Albini, CAMO Postholder at Neos Air and Ville Santaniemi, Senior Partner at QOCO Systems | View article |
Case Study: Increasing engine on wing time at Neos Air
Author: Ivan Albini, CAMO Postholder at Neos Air and Ville Santaniemi, Senior Partner at QOCO Systems
SubscribeThis case study will look at how Rolls-Royce’s revolutionary new approach to aircraft engine product lifecycle management (PLM) is working in practice. Rolls-Royce’s Blue Data Thread digitalization program, powered by QOCO data handling, was covered in Aircraft IT Winter 2021/22 issue: now, in this case study, we’ll look at a real-world case where the system has been used by an airline. As always, we’ll first introduce the subject of this study, Neos Air.
NEOS AIR
Neos, established in 2001, is a small airline, part of a larger holding and fully owned by Alpitour Group, a leading travel operator in Italy. The core business is leisure flights with a fleet that consists of six Boeing 787-9, five 737-800 and four 737-8 aircraft.
NEW AIRCRAFT AND ENGINES NEED A NEW APPROACH
Neos’s 787 Dreamliners are powered by Rolls-Royce Trent engines and, as part of the engine management plan implemented by the OEM to increase MTBSR (Mean Time Between Scheduled Repairs), they introduced a method, called DAC (Direct Accumulation Count) of cycles for aircraft engine management. The purpose is to increase cyclic life by analytically determining how much of that life is consumed during each flight. The rationale behind it is that, during each flight, under typical
conditions, the engine will consume a fraction of a full cycle. By accurately measuring that consumption it is possible to better determine the remaining safe life for the part rather than having to rely on rigid time driven calculations of remaining life. That more realistic measurement of actual wear rather than simple used time makes it possible, if wear is less than the worst-case scenario that is used in old-fashioned lifing methods, for the part and the engine to stay on wing longer. In order to achieve optimum effectiveness, methodology such as that requires lots of information to be provided to Rolls-Royce, some of which will be coming from Neos’s MRO software AMOS which the airline has been using since 2004.
When Neos Air took delivery of its Rolls-Royce Trent powered 787s, in order to be able to measure the life and calculate the life expectancy of all the parts in each engine, Rolls-Royce first needed to build up a profile of Neos’s operation (phase one). For that they used data coming from the 787 with ACARS messaging using a downlink from the aircraft. A second set of telemetric data that was generated by each engine during the flight, which was downloaded by the maintenance crew when the aircraft had landed. The process continued for some months until Rolls-Royce had built a profile of Neos’s ways of using the engines. In phase two, the airline was able to declare that the DAC system was the executive method of lifing for these engines, in order to do which, it was necessary to go through several steps of approval which included the interfaces with the MRO system, AMOS for Neos Air, and Rolls-Royce, through a third-party service provider which is QOCO.
QOCO was founded by people who previously worked with another airline which also uses AMOS. So, they already knew exactly how the system works and developed a process that facilitates communications between the MRO system and the Rolls-Royce server. Neos collects data from AMOS and then pushes it to a repository in their own system. This data is then available to Rolls-Royce who, in turn, provides data on the exact level of life consumed and remaining for each engine (figure 1).
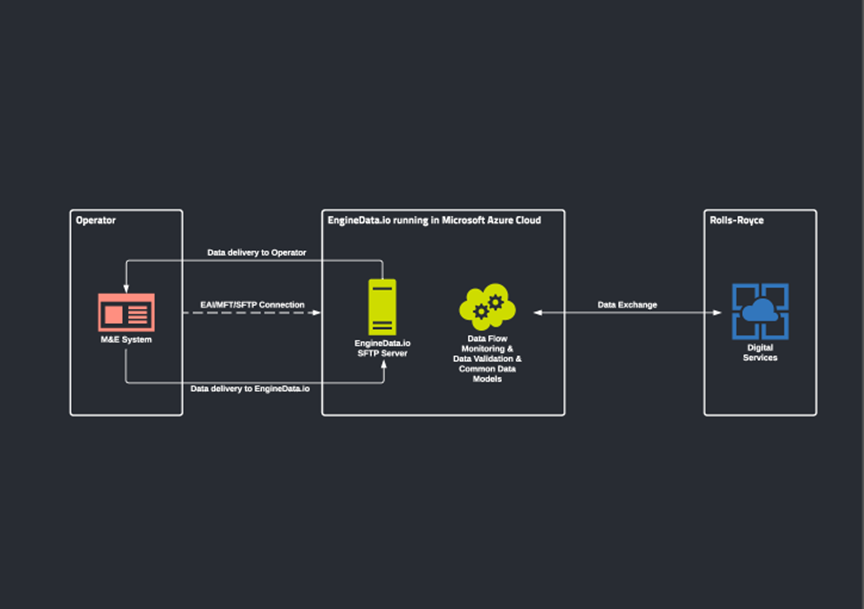
There was no need for Neos to choose QOCO from a number of solution vendors, it was the only one able to provide this particular link between the airline and Rolls-Royce.
THE QOCO SOLUTION
QOCO works with Rolls-Royce to support service delivery to provide the data capture and management component in the OEM’s Blue Data Thread as part of the digitalization of Rolls-Royce TotalCare. How the vendor works with airline is that they undertake a project with the airline or operator to set-up the data exchange, build the connections and get to know the people. However, when COVID-19 arrived, that was not possible which meant working with MS Teams became the norm. The Neos Air implementation was the first one to be managed completely remotely, with no on-site presence for QOCO.
The first step is to have an implementation project for the data exchange in which QOCO works with the airline or operator through the different phases such as ‘discovery’, ‘definition’, ‘implementation’ and ‘roll-out’. QOCO’s objective is always to minimize the workload for the airline, so they aim to utilize existing services that the airline has and, as QOCO will be integrating with the airline’s maintenance and engineering systems, they try to use the capabilities of that system as much as possible. In addition to minimizing the burden for the airline, QOCO uses the most suitable technology. They configure and deploy the required data pipelines between the airline and the EngineData.io platform utilizing existing data services and the most suitable technology. SFTP (Secured File Transfer Protocol) transfer or APIs (Application Programming Interface) depending on the airline’s capabilities. Part one is the implementation project that QOCO does for the airline. In the background there is the data exchange platform, software that runs in Azure Cloud environment which is the backbone which QOCO needs to connect with the airline’s systems.
Once the implementation project has been done, the next step is to go live with the data exchange and complete the handover to QOCO’s continuous services. QOCO does not only provide the platform for the data exchange but there are complementing continuous support services aligned with the platform, including data monitoring to monitor that the data is received when it should be received. The service also includes data quality controls that will notice if, for instance, there is a missing flight for one aircraft, and will trigger the system to contact the airline through Rolls-Royce to resolve any data issues. As the system is constantly reviewing the data, it will notice if there are any issues that need to be actioned.
With Rolls-Royce and with the data exchange services provided by QOCO to Rolls-Royce who manufacture the engines, they can keep track of their assets as they are used by different airlines and keep a digital copy of the engine. It means that the airline can keep the engine running safely on the wing for a longer time which is a huge benefit, enabling them to maximize operations.
This has a particular impact with life limited parts (LLPs); the traditional approach is that the manufacturer, who doesn’t know how the airline will operate the engines, has to assume the worst which means that life limits are usually set according to worst operating conditions. With the data exchange, Rolls-Royce receives IoT (Internet of Things) data directly from the engines; QOCO provides the complementing data from the maintenance system which completes the picture. With that complete data set, Rolls-Royce is able to extend the use life of life limited parts which, in turn, further supports longer safe operating times on wing for the engine. It also reduces unscheduled maintenance events which, as all airlines know, are costly in terms of both the financial consequences and the reputation damage they can cause. This more detailed and comprehensive picture of how the airline is operating the engine can also feed into a predictive maintenance process.
In all this, QOCO is the enabler; they don’t store the data but simply enable Rolls-Royce to provide the value adding services for the airline.
TRAINING AND WORKING TOGETHER
Because QOCO is a data exchange solution that runs in the background, when it is working well, it will be running seamlessly and unnoticed. But, of course, things do happen from time to time. There might be changes in the operator’s IT but, even if not notified, that will be picked up by the solution. If QOCO does not receive data or if the data is in any way unusual or corrupted, QOCO will notice and will contact the airline to resolve the issue. The only requirement from the airline’s IT perspective is that QOCO will typically need the help of the airline’s IT system administrators when it comes to setting up the required components for the data integration. QOCO, as a software business, has available expertise to work with the corresponding people from the airline’s side.
IMPACT OF COVID-19 ON THE PROJECT
Neos was affected by COVID in several aspects of the business. In this particular instance, since they had to deal with COVID anyway, it was not that difficult to keep working on the project, either by remote working through Zoom or directly in the office; when COVID started to spread in Italy in February 2020, Neos started working on this project and was able to proceed with it. Of course, there were times when Rolls-Royce also experience COVID related problems and were sometimes unable to work remotely because of security issues. But mostly there were no issues in carrying through the phases of implementation. There was a phase when Neos had, for example, to carry out testing by sending specific data to a dedicated testing repository in Rolls-Royce; then there was another step where they had to send the same data for approval and for reliability to QOCO. Those phases did not need person to person meetings; they could go ahead with server-to-server connections. So, the project suffered no delays as a direct result of COVID.
Overall, Neos felt that QOCO provided the exact directions with control documents, revision levels and so on. They were able to provide the exact instructions to use the system and the system itself is already structured to be a data exchange through a structured process. Data exchange is implemented in a way that the M&E system (AMOS) is actively initiating the data transfers to and from EngineData.io service. So, with this system it is possible to set up a two-way communication with any other system while ensuring the necessary level of security with no connections coming from outside. There is a simple way to transfer data through an XML file which then must be structured in a way that QOCO has instructed. Neos had to refer to their own IT department for some steps that required scripts to be actioned or filed with the operating system of the server on which AMOS runs. However, apart from that, all Neos had to do in AMOS was to set up the structure of the XML to be transferred out or received.
The technical documents provided by QOCO are clear correct and complete. One part of the technical documentation is about how to extract data from the maintenance and engineering systems and how to import data to that system. The other part is that, during the discovery phase, both parties (airline and QOCO) agree on the technical architecture of the solution to set up how the data is actually exchanged – transferred between QOCO and the airline. Larger airlines will usually have an integration platform and QOCO can connect to that, while smaller airlines will use other processes with which QOCO can happily work. QOCO has its own toolbox with tools that it can utilize on such occasions to help the operator where the required services are not available.
REGULATORY AND INTERNAL APPROVALS
From QOCO’s point of view, approval is threefold. Rolls-Royce provides technical clearance to use the DAC (Direct Accumulation Count – for aircraft engine management purposes) system. Then the airline needs to approach the local aviation authority to get their approval. Finally, of course, there will be internal approvals at the airline. All three need to be in place. QOCO will support and provide documentation, but more often than not, further support is not necessary.
The system itself, the way in which Rolls-Royce proves the information is already approved by EASA. Rolls-Royce holds the EASA type certificate for the engine which means that EASA has approved this maintenance and engine management process so Neos simply had to amend its continuous airworthiness management process. By adding this particular process to measure the life of LLPs (Life Limited Parts), the benefit was to avoid the removal of an engine due to life expiration of LLPs. That was and is a huge benefit that Neos has derived together with, of course, the only other way they could have reached the same goal would have been by making a repetitive and frequent manual input to and out of AMOS of the necessary data.
With this automatic routine, the airline is able to avoid manual inputs and instructions which, in turn, removes the main problem that human interactions can bring which is human error. With the data sent automatically from AMOS, and sent to the right place as well as Neos also automatically putting that data into yheir own systems, it frees people up to work on other things
The process has been approved by the Italian LAA (Local Aviation Authority) and the ENAC (Italian Civil Aviation Authority). Fortunately, approval of a dedicated AMP (Aircraft Maintenance Program) revision was less of a problem than it might have been due to the change being already EASA approved.
THE SYSTEM IN PRACTICE
Integrated within the AMP (Aircraft Maintenance Program) is the LLP life which is controlled with fractional data, i.e., data referring to that fraction of a flight consuming the LLP. Sending that data to the system means that, in a few months, it is possible to measure performances of all parts of the engine and how much of a component’ life has been consumed during any particular flight.
For Neos, this combination, QOCO and Rolls-Royce is not the only such system with which they are sending data this way. In a very similar way, the airline is also sending the same sort of data to Boeing for other maintenance related reasons such as reliability and AHM (Aircraft Health Monitoring). It is a good way to share data from AMOS with outside entities. Once the data exchange structure is up and running it works. AMOS was switched on at Neos in 2004 and has never gone down, it’s very reliable. In a similar manner, the airline wouldn’t have anything else other than what QOCO is doing. In the time Neos has been using QOCO, there have been a couple of changes in the way AMOS gets data from the database with the aim to have an optimized way for achieving that. QOCO is continually improving the data transfer method so that the system is continuously monitoring and fine tuning. It is clear to Neos why Rolls-Royce chose QOCO for this function.
QOCO works with Rolls-Royce which has the Blue Data Thread program and, when QOCO is setting up the data exchange, the two parties have agreed on a joint data model which includes data from different aspects of aircraft maintenance. The requirements for one specific service under Blue Data Thread is the DAC system. Working with the airline, QOCO will jointly define the data scope which will be much wider than just the requirements of the DAC system. Prior to working with Rolls-Royce, QOCO worked with another airline and set up the same kind of data exchange for their A350 aircraft which also have the Rolls-Royce Trent engines. That resulted in QOCO receiving enquiries from other airlines asking how it had been done and could QOCO do the same for them which, in turn, lead to QOCO working with another airline. Ultimately, Rolls-Royce contacted QOCO to suggest the collaboration.
FUTURE PLANS AND NEXT STEPS
The process of measuring and recording life used and remaining on LLPs does not yet cover all of the LLPs in an aircraft engine with Neos; so, there will be a progressive inclusion of other LLPs into the system and away from the traditional method of ‘one flight equals one cycle’. That will be reflected in a corresponding growing number of components that can continue safely on wing based on actual condition and not just cycles flown.
Contributor’s Details
Ivan Albini
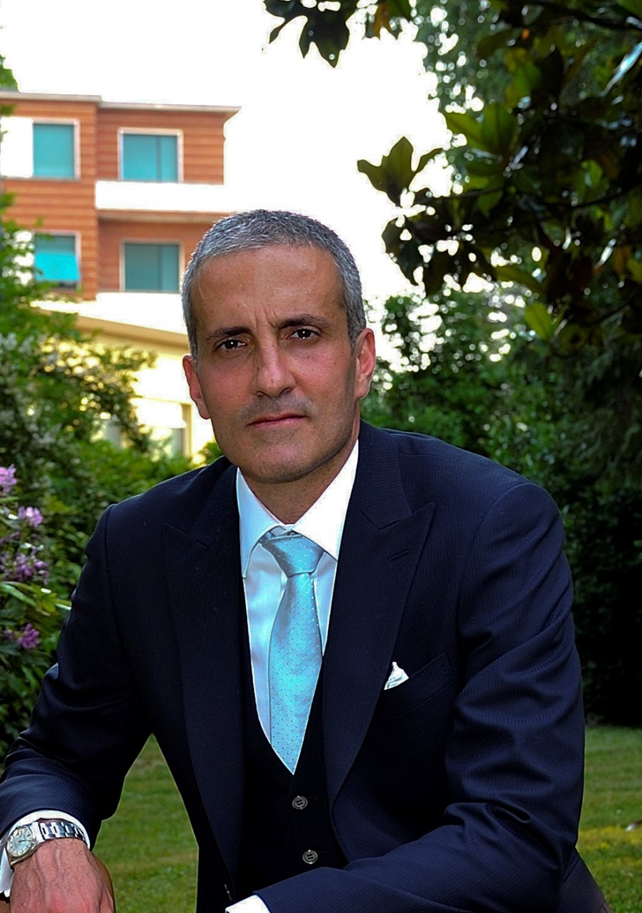
Ivan Albini, CAMO Postholder at NEOS, started his aviation experience in 1998, with Lauda Air as power plant engineer, then he moved to Air Europe 1999-2000, and joined NEOS in 2001, participating in its startup. In NEOS, he started as power plant engineer, was promoted engineering manager in 2008 and eventually CAMO Postholder in 2017. His technical background covers either legacy and new gen aircraft, such as 737ng, 767, 787 and 737max.
Ville Santaniemi
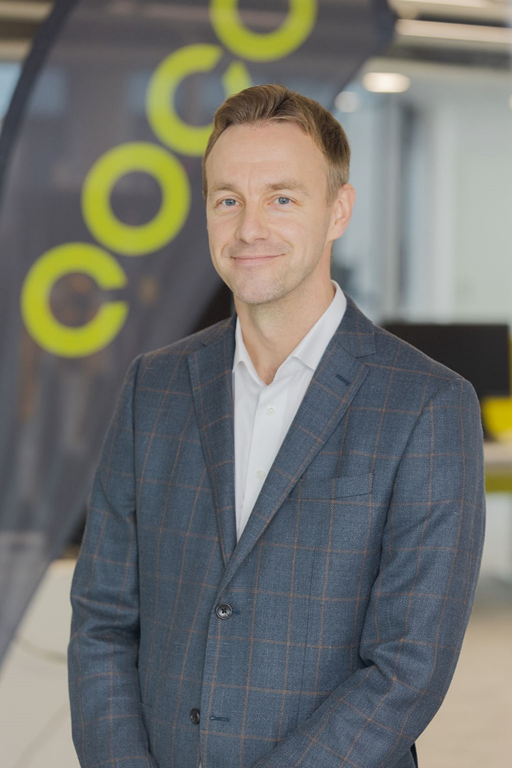
Ville Santaniemi, Senior Partner at QOCO Systems, entered world of aviation in 2005 when he started working for Finnair. With a strong background in IT and business, Ville has always felt comfortable working with and aligning the needs of these two areas. In aviation, Ville’s expertise lies mostly within aircraft maintenance and airline operations. His career has taken him from Finnair to Emirates and now to QOCO as a Senior Partner since 2015.
Neos Air
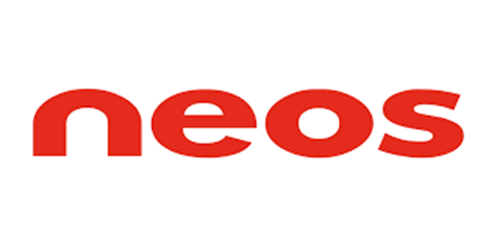
Neos is an Italian airline operating a fleet of Boeing 737 Next Generation, 737 MAX and Boeing 787 aircraft to over 73 scheduled destinations in southern Europe, Africa, Asia, the Caribbean, Brazil, USA and Mexico. Neos became the first Italian operator of the Boeing 787 when its first 787-9 entered service in 2017. For many years Neos has been working with Costa Cruises to transport passengers to and from ships’ departure and arrival points.
QOCO Systems
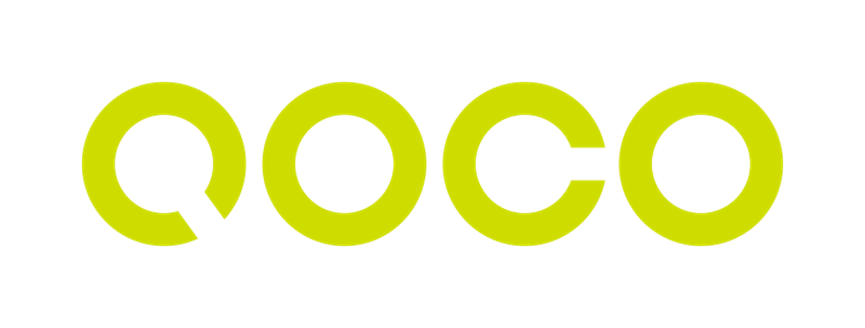
QOCO Systems helps the aviation industry to succeed by creating new ways to work, to communicate, and to utilize data. A trusted partner of airlines, MROs, and aircraft OEMs for twelve years, QOCO’s goal is to enable operational excellence and efficiency in the aviation industry with disruptive SaaS solutions: MROTools.io for streamlined tool management in aircraft maintenance. EngineData.io for intelligent data exchange between the collaborating parties in the aviation industry.
Comments (0)
There are currently no comments about this article.
To post a comment, please login or subscribe.