Articles
Name | Author |
---|
CASE STUDY; PLAY Airlines gets efficiency and future-proofed
Author: Halldor Gudfinnsson, Director Flight Operations and Tómas Ingi Gunnarsson, Supervisor Dispatch, both at PLAY Airlines
SubscribeHalldor Gudfinnsson, Director Flight Operations and Tómas Ingi Gunnarsson, Supervisor Dispatch, both at PLAY Airlines describe an Operations IT suite to help the airline thrive today and face the future with confidence
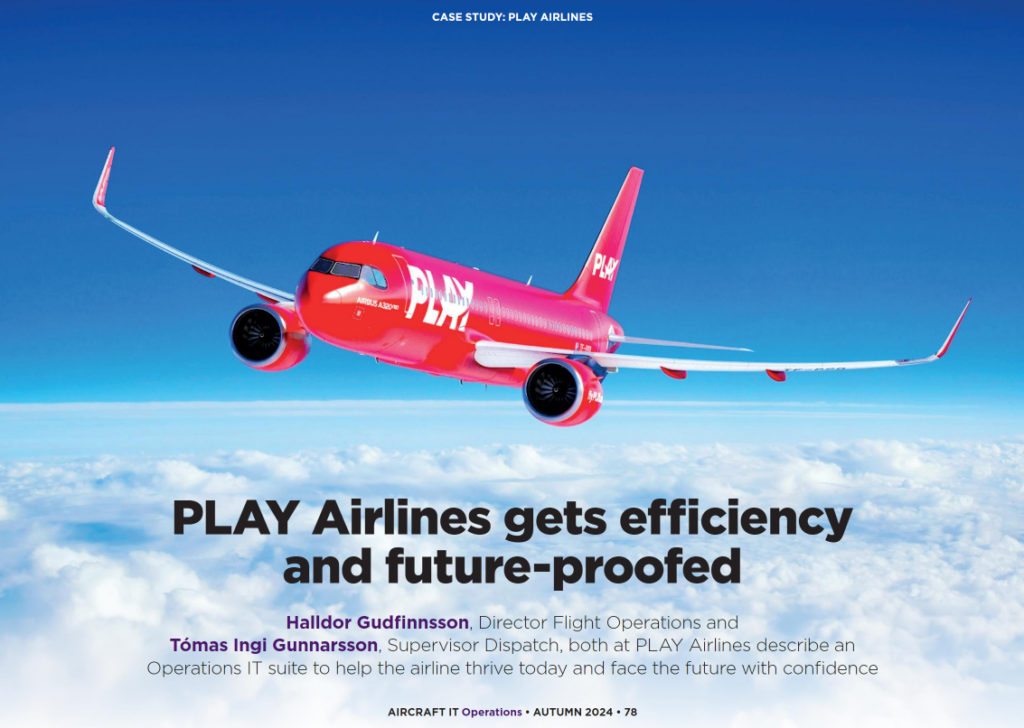
Halldor
In this case study, we aim to share with readers our experience of implementing NAVBLUE products into our airline. But let’s first set the scene with an introduction to PLAY.
PLAY
The airline is a low-cost carrier (LCC) based in Iceland and had been operating for three years at the time of writing. Having started the business five years ago, it took about two years to get the AOC (Air Operator certificate). Today, we have a fleet of ten aircraft – we like to describe ourselves as relatively small but beautiful – and all of those aircraft are from the Airbus A320 family. There are four A321neos and six A320neos. With an average age of 3.51 years, again at the time of writing, it is a young and efficient fleet.
Our main market is using Iceland’s mid-Atlantic location to connect North America and Europe to each other and for visitors from either continent to Iceland itself. At the end of 2023, PLAY had 477 employees from 30 different nationalities: their average age was 32.45 years. It’s a diverse and young workforce.
In 2023, PLAY carried 1.5 million passengers between 38 destinations with an 83.4 percent load factor plus an on-time performance rate of 83.2 percent and trending up even though we have had to deal with issues such as eight volcanic eruptions in the past three years. Of those passengers, 41 percent were travelling between North America and Europe via Iceland, 27 percent were travelling from Iceland to North America or Europe and 32 percent were travelling to Iceland from those continents.
In 2024, PLAY will be operating to and from about forty destinations (figure 1).
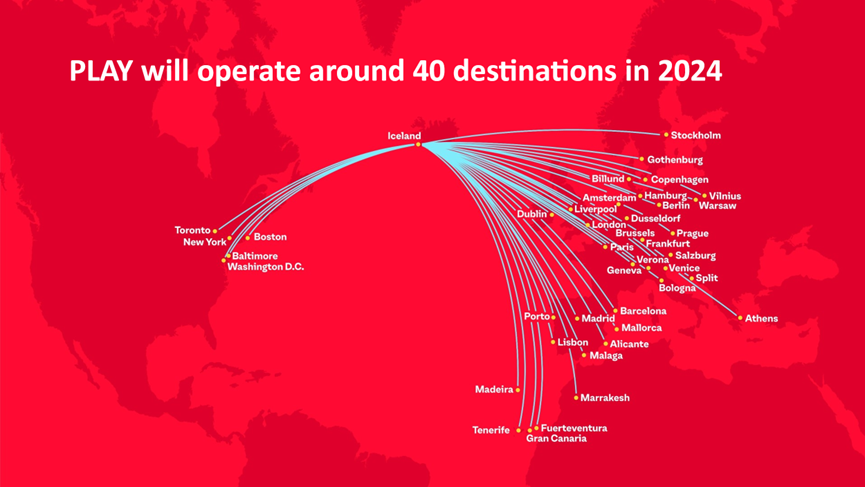
Figure 1
As we’ve already seen, we’re right in the middle of the North Atlantic where the weather is always good… or not! We serve Eastern North America and a lot of destinations in Europe as well as North Africa, Madeira and the Canary Islands. That’s a brief overview of PLAY but the purpose for this case study is to share why we chose NAVBLUE for all of our Flight Ops systems and to highlight some of the benefits we have gained from it.
WHY NAVBLUE?
When PLAY started, some of us had previous experience with NAVBLUE solutions from working at another airline that is no longer with us. That gave us the opportunity to source people with the know-how and experience to operate NAVBLUE systems. Because of Covid, they were all available in Iceland. But the main reason for selecting NAVBLUE was the availability of a one-stop-shop; we can get all of our systems, from ground to cockpit, from NAVBLUE which is also an Airbus company. Altogether, it was a ‘no-brainer’. And, having made the decision for NAVBLUE, most important for us was the honest, agile, rapid support that we got from them during the startup phase as well as the ongoing support that we continue to get. They understand us and they understand our needs; it’s a good collaboration. Also, the systems are highly configurable to work with EASA rules and with the Union contract rules, all of which is easily done through the NAVBLUE operating system and N-Ops & Crew. That configurability extends to being able to work with any future regulatory rule changes which is very important for us.
Also, with the AIRAC database, a minimal level of internal system support is required to maintain it which means less day-to-day work; everything goes through the system seamlessly. There is also automation available across the NAVBLUE portfolio which is very important as it reduces our workload and manpower demand as well as reducing the error rate. The outlook for the future is exciting because NAVBLUE is coming up with a lot of new solutions and, very importantly, there is a roadmap which they stick to so that we can anticipate and plan for when we will get those solutions.
Of course, as with any business, cost is critical in PLAY. My department in the airline is responsible for about 85 percent of the entire airline’s costs.
NAVBLUE INTEGRATED SUITE
As stated above, NAVBLUE is an Airbus company and we fly Airbus aircraft so there is some continuity there plus, it is an integrated Suite (figure 2).
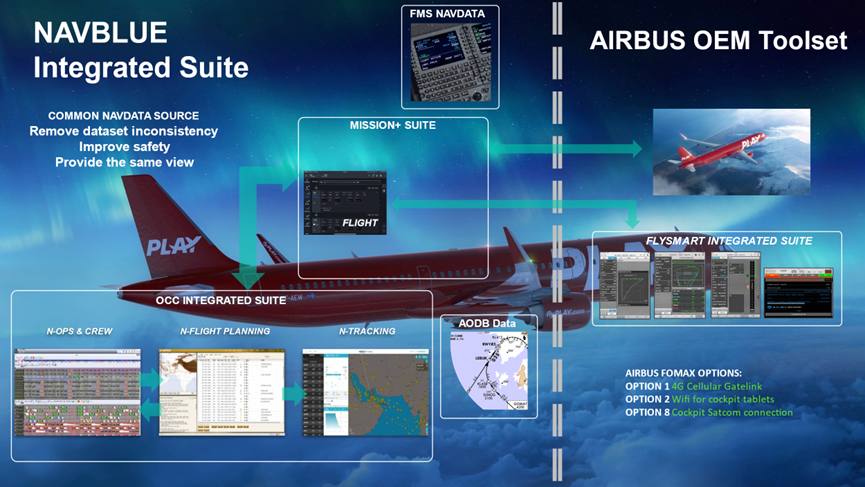
Figure 2
Tómas is better qualified to explain the details about the specific components in the suite such as N-Ops & Crew, N-Flight Planning and Tracking, etc. But, from a pilot’s point of view, the figure shows the OCC Suite that we use in PLAY which incorporates the Crew Scheduling system and N-Ops & Crew. We have to do everything in the Flight Planning System but the systems talk to each other which is important to us. We use N-Tracking to track our flights with FlightWatch and we are in the early stages of implementing Mission+ Flight which will enable us to go paperless. We’re pretty excited about that with the Mission+ FLIGHT and were, at the time of writing, in the test phase with it; the plan is to implement it in the second half of 2024.
We also have the Flysmart+ Suite which most Airbus operators are used to with its performance calculations and the ability to do manual computations when we have to, it occasionally happens and the system makes it very easy. It’s good for us to be able to access performance information and the eQRH, which I think is a fantastic tool because although I’m a bit old school, I like paper, I’ve now grown fond of the eQRH because they are easy to use, all of the information is accessible and we use iPads so everything is very quick. Now, the only paper that’s left on the flight deck is the Operation Flight Plan and that will go when Mission+ FLIGHT is fully implemented. We use the Airport Obstacle database to plan flights and do routes, etc. and the FMS (Flight Management System) NavData is NAVBLUE also. The main thing here is that its all seamlessly integrated together which reduces the likelihood of errors which, as we all know, are not at all welcome in aviation.
We are also implementing FOMAX (Flight Operations and MAintenance eXchanger) in all of the fleet and, at the time of writing, were just using Option 1 which is the ability to download our FDR (Flight Deck Resources) data for each flight without doing it manually, just streaming it through 4G or even 5G. As I said, Tómas will explain the way the solution works.
We don’t have Wi-Fi on board our aircraft at the moment so there is no Internet connection, we use Tallis FMCGs with the NAVBLUE database and the FOMAX connection, just the flight part recording facility, but, in the future, we plan to integrate FOMAX to, effectively have a mini-Wi-Fi on board which will then talk to the aircraft systems and feed into our Apps on the iPads. Also, we are working with CrewApp: our phones are with us at least 18 hours a day so pilots can easily see their upcoming flights and who will be flying with them. That App takes all of its information from N-Ops & Crew; but it also gives information to the same solution.
Tómas
Looking now at how we use the NAVBLUE solutions (figure 3), the N-Ops & Crew is our rostering and scheduling system which is also the heart of the company.
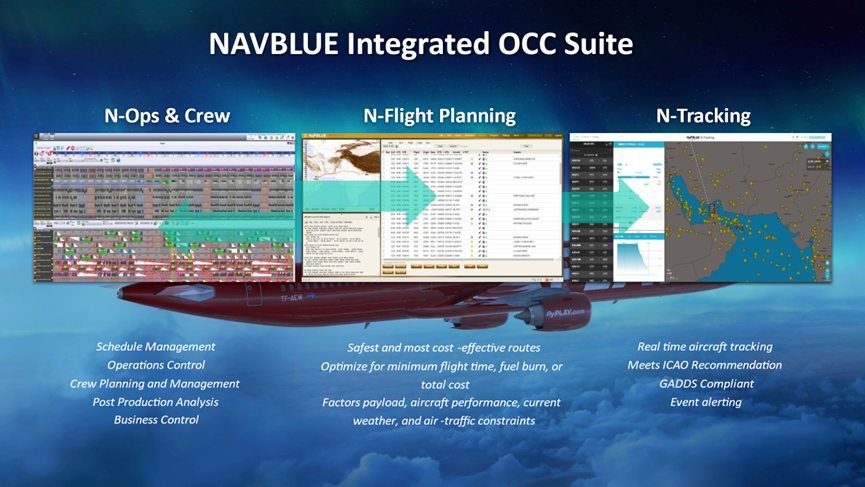
Figure 3
So many other systems in the company are connected to N-Ops & Crew to feed information into it and take information out of it. Since the implementation of NAVBLUE in PLAY, we have been adding to the system and figuring out how to connect together the different systems that we have. NAVBLUE has been very supportive in helping to create those connections and has been rapid in getting them working. The integration between N-Flight Planning and the N-Ops & Crew is very reliable, probably because they are related components in the same system; we’ve never had a wrong registration on a flight plan, everything is really reliable. Even with last-minute changes, when you might be hurrying, the system can still be trusted.
Similarly, from N-Flight Planning to N-Tracking the connection and integration is very reliable. Prior to the implementation of Mission+ FLIGHT we were, at the time of writing, printing out all of the flight plans. N-Flight Planning is pushing us to introduce more automation in flight planning. That is very exciting for us and we want to continue to implement automation in our dispatch and that comes with Mission+ FLIGHT. To summarize what we have to say about those systems: we like them, they are user-friendly and they are visually clear and attractive.
Halldor
I recently asked a pilot who had tried the system in the simulator ‘how does the system work?’ and he confirmed that the system works very well. The same goes for the NAVBLUE Suite, it works very well. So, what are our goals with NAVBLUE?
First goal is to implement Mission+ FLIGHT. We’re excited about that, having tried it out during flights and it looks good, and works well. There are a few hiccoughs to iron out but nothing major. We also want to expand the use of automation; not only the flight planning with automated flight plans. There are so many systems that PLAY is connected to, for example, N-Ops & Crew, the crew scheduling system. For instance, Maintenance uses Gamit and that does more than just retrieve information from the scheduling system but actually writes into it as well. With regard to MELs (Minimum Equipment Lists) or, say, work orders for maintenance, everything is on the platform which everybody uses all of the time: maintenance, crew scheduling, rostering, it doesn’t matter what it is. So, yes, we plan to increase automation through these connections with our other systems such as payroll and other data systems; there are endless numbers of systems that can connect into NAVBLUE. Another goal is to achieve optimum fuel usage because, as we said earlier, cost is everything and, like all airlines, PLAY burns a lot of fuel. But it is important that we control the consumption and make our fuel policy as focused and economical as possible; in doing that, we will also reduce the CO2 emissions about which the world is so concerned – we’re proud to be playing our part in that with the help of NAVBLUE.
All the systems that we have mentioned are contributory to running a lean company and we hope that readers who are contemplating a similar implementation to the one that we have undertaken, will find our experience useful.
Comments (0)
There are currently no comments about this article.
To post a comment, please login or subscribe.