Articles
Name | Author |
---|
CASE STUDY: Silk Way West Airlines embraces digital EFB and EFF solutions
Author: Zahid Sultan Khan, Chief Pilot, Silk Way West
Subscribe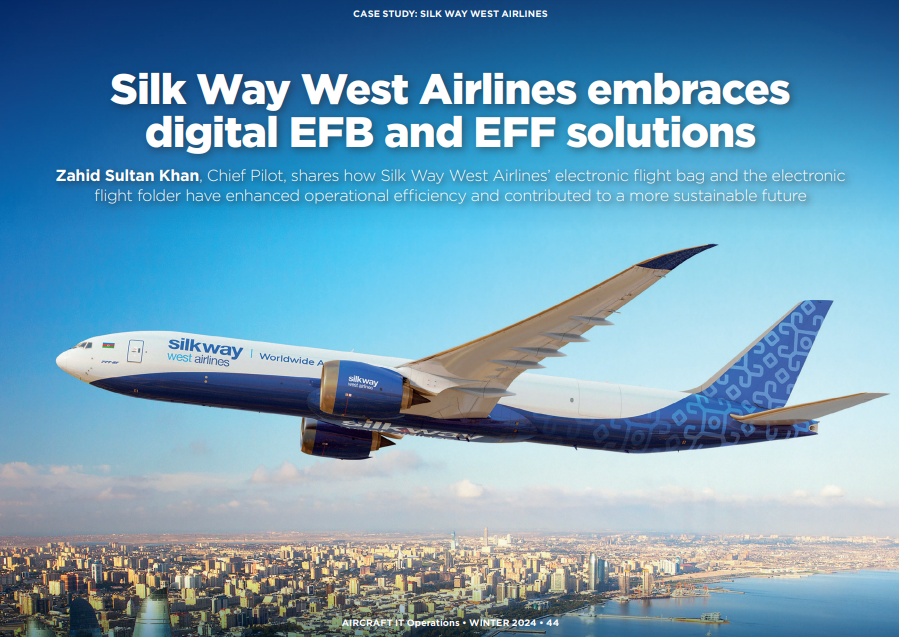
Zahid Sultan Khan, Chief Pilot, shares how Silk Way West Airlines’ electronic flight bag and the electronic flight folder have enhanced operational efficiency and contributed to a more sustainable future
The main focus for this case study will be on Silk Way West’s selection and adoption of a new digital EFB and EFF solution but first and to set the scene, I’ll give readers a brief introduction to the airline where this case took place.
SILK WAY WEST AIRLINES
Founded in 2012 in Baku, at the heart of the Silk Road, Silk Way West Airlines, sister company to Silk Way Airlines, is the largest cargo airline in the Caspian Sea region. Based at Heydar Aliyev International Airport, Silk Way West operates around 350 flights a month across Europe, Asia, and the Americas with a fleet of 12 dedicated Boeing 747-8F, Boeing 747-400F and Boeing 777F freighter aircraft. The airline’s annual cargo turnover exceeds 420,000 tons, while our growing route network covers more than 40 destinations across Europe, the CIS, the Middle East, Central and Eastern Asia, and North and South America. As well as scheduled services to those more than 40 destinations, Silk Way West also operates charter flights all over the world.
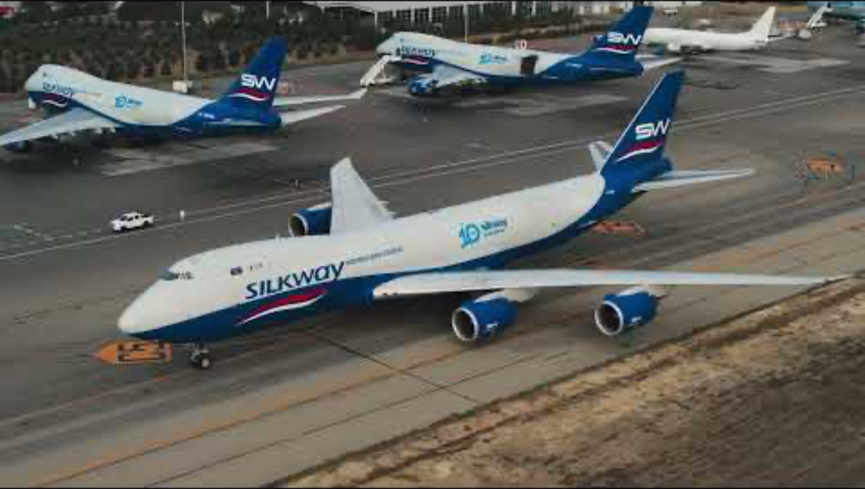
Many of our requirements for products such as EFB (Electronic Flight Bag) and EFF (Electronic Flight Folder) can be quite different from those of passenger airlines. In this case study, I would like to tell readers about our electronic flight bag solution and our solution to enhance operational efficiency and contribute to a more sustainable future.
Sustainability is important to Silk Way West: the cornerstone of our success can be found in re-investment and giving back to the operation. As a signatory to the United Nations Global Compact initiative, we have confirmed and formalized our commitment to the environment. Silk Way West was delighted to be the official Global Air Cargo Partner for COP29, held in Baku, Azerbaijan in November 2024. Technological innovation in the field of flight operations is a key part of these sustainability goals and we have decided to renew our fleet of aircraft as a prerequisite key factor towards achieving those goals. In recent years, we have ordered some of the most technologically advanced next generation freighters in the world. At the time of writing, we had six Boeing 777 freighters, four Boeing 777-8 freighters and four Airbus 350 freighters including options on order.
For a cargo airline, it is very easy to stay under the radar of sustainability since there is not too much light being shed on the cargo industry, with the mainstay of focus being on the movement of passengers. However, at Silk Way West, we understand the need to invest and to renew our fleet. As part of that, we looked at our Boeing 747-8s which are already modern aircraft – even if their origins hark back to the more than 50 years old Boeing 747. Our twelve aircraft might not sound like a substantial fleet, but with more than 450,000 tonnes of cargo volume globally, we realized that the impact on the environment is still significant, albeit with a smaller fleet.
The first example of our fleet upgrade is in the video below.
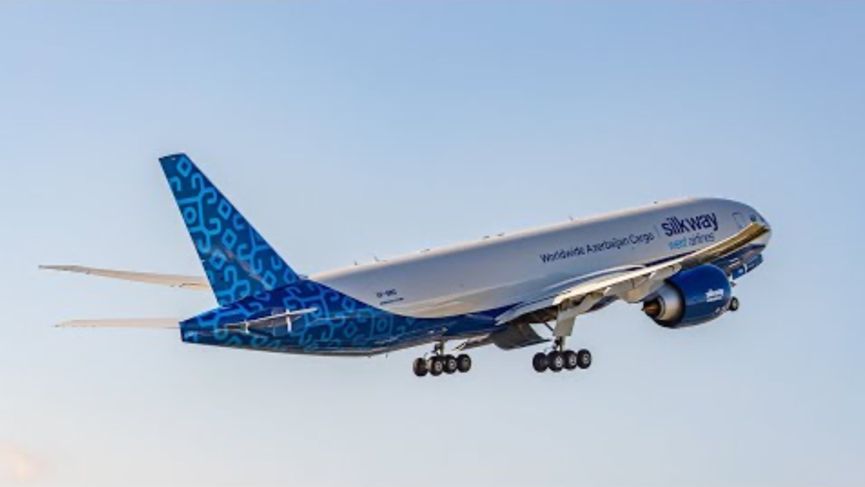
Some readers will recognize that the Boeing 777 aircraft has been around for some time but the B777 freighter, the current version being about 15 years old, still burns a lot less fuel than a Boeing 747-400 freighter. For example, the B747 on average burns approximately 12 tonnes of fuel an hour whereas the B777 freighter burns 7 tonnes – little more than half. Although the freight volume carried is lower (the B747 freighter can carry 115 tonnes of payload while the B777 freighter can carry about 105 tonnes) that is still less fuel per cargo tonne carried – aptly owing to the adage that ‘sometimes, less is more’.
REASONS TO IMPLEMENT AN EFB SOLUTION
One obvious reason to implement an EFB solution is fuel saving from how much less documentation is carried on board. A reduction in paper charts, folders and manuals saves Silk Way West an average of 36kg of weight per flight. that might not seem like a lot when an aircraft is taking off with 447,000kg but, looking further into that; 36kg of fuel is approximately 7.2kg of additional fuel burn per flight; that still does not sound like much but 7.2kg per flight over our 350 monthly flights is about 2.5 tonnes of fuel, which adds up to about 30.2 tonnes of fuel saving a year, just by adopting an EFB. Prior to the introduction of the EFB, we had to carry all the charts in paper form. Of course, the wider the geographical area you cover, the more charts that are needed and, for us, someone going to the aircraft and physically updating the charts was time consuming, so we used to simply create a whole up-to-date charts bag and swap that out to save anybody having to go on board. It was easier for us but still the whole manual process involved with that was costly in both time and money. The manpower needed to keep charts up-to-date and the amount of physical space needed on board for world-wide charting, including alternates, was considerable. One could say ‘well why not only put the charts onboard for the route being flown’? True, however we could have a situation where an aircraft scheduled to fly from Baku to Hong-Kong had to be re-allocated to fly to Chicago instead – the other side of the world. It would have been impractical to change, at short notice, the charts required for the new flight. So, as a mitigation, we carried all of the global charts that our pilots might need, on board and that required incredible logistics.
We did retain paper back-up for a while after the change but we do not anymore for charts and we recently received approval from the Azerbaijan State Civil Aviation Administration to also remove the paper Operations Manuals. At the time of writing while we were going through the certification for the Electronic Flight Plan, the OFP (Operational Flight Plan), we had to carry a back-up during the certification process but this was just for the transitional period and we will soon be wholly EFB/EFF based.
For me, one of the biggest benefits is that the EFB also improves our regulatory compliance with National Aviation Authorities and for IOSA audits and compliance. As a pilot I understood the operational challenges and so, in the implementation with the Logipad team, it was a core requirement for me that a flight should never be able to be ‘closed’ or completed without filling out all of the minimum mandatory regulatory requirements. I knew that if you give pilots a chance to miss a thing, they will miss it, because after all we are human. For instance, every hour, we should record the altimeter readings for RVSM (Reduced Vertical Separation Minimum) compliance. However, if we pull a completed paper flight plan in the office and do an internal audit, I am quite sure there would be one or two of those readings missing. By having an EFB solution, you can improve your regulatory compliance with the relevant regulators.
Another big reason is Big Data. The EFB allows Silk Way West to have easier access to key data and reporting, and we can see – at-a-glance – trends in fuel use, volume optimization of aircraft and more. For example, if I want to see how much fuel we have burned over the month of October, with one click of a button, there is the data. I can also see how much fuel we planned to use and we can quickly see trends. Also, we are constantly reviewing the performance of our aircraft and making sure that fuel consumption is according to our expectations. With the fuel savings initiatives that we have developed, we want to know whether they are working or not and an EFB solution makes that analysis easier. It also enhances the competitiveness of the business and gives us a strategic advantage over other cargo carriers that are not thinking about digitization. An example of this is that that we can see very easily if we are optimizing the volume on our aircraft and if we are carrying enough payload. On a cargo aircraft, volume is like real estate; if you are not using it, you are losing revenue.
Having an EFB also reduces our flight operations costs and handling costs related to flight plan delivery; we often paid ground handlers at outstations to physically deliver the flight plan to the aircraft. Furthermore, it reduces delays at outstations. As I mentioned previously, we are a big charter carrier and I cannot tell you how many times I have flown to some remote place in the world where there is no printer and I remember an occasion in Africa where I was waiting; the aircraft was ready to go but we had to wait two hours, just for a paper flight plan to be printed and brought to us. Some may suggest that we could receive it through ACARS but then there are various legal documents that are provided locally, by the local station. If you cannot print something, it sounds like a small problem, but a couple of hours delay in a flight operation is massive problem.
WHY LOGIPAD WAS CHOSEN
One of the reasons why we selected Logipad was its ability to be integrated into Silk Way West’s operations; it was easier for us to integrate Logipad, compared with some other solutions. The integrations that were necessary were to our crew, flight and load planning systems plus our accounting and finance departments. The manual processes involved in data entry from paper, or some other solution that does not connect to our accounting department finance software, have been eliminated with Logipad and, if it feeds information directly to the accounting department, they will not be bothering us in Flight Operations with questions like… ‘Where is the fuel receipt for this flight?’, ‘Where’s the catering receipt for that flight?’ It’s all automated now.
Logipad offered a highly customizable presentation of information and, surprisingly, at the time we were looking for an EFB solution, not many EFB companies were providing live inflight synchronization of the flight plan between multiple iPads on the aircraft. As a cargo airline, we only have two pilots on board, one of whom is the pilot monitoring, whose job is to fill out the flight log. Without a Flight Attendant, if that Pilot goes to get a cup of tea, what can the other pilot do if his own iPad is not up to date with the log, he cannot just reach over for the other iPad in a wide-body aircraft. Again, you would think it would be easy in the modern digital age but many of the EFB providers at the time were not offering this solution which Logipad had developed.
Logipad also has an excellent document library, eliminating the need to have another solution for the eLibrary. This along with their eForms solution was really advanced for us and we were impressed by that. Also, the general robustness of the system architecture impressed us. Another key deciding factor was the fact that Logipad is a part of DextraData, a larger IT company. That is important because when changes or a technical solution to a problem need to be done, there are IT specialists on hand who can deliver changes and solutions in a timely fashion. We were also happy with their personable approach to customers, in addition to a high level of support and expertise.
AN INTRODUCTION TO LOGIPAD
Erik Burkel-Grehs, Sales Development Representative, Logipad
Logipad is an in-house developed EFB solution from German-based DextraData. The Logipad team numbers about 70 people, mainly based in Essen, Germany with the goal to optimize the processes of airlines and of flight crew in particular, we do that in order to save time and costs.
How Logipad works
Digitalizing all of the paperwork, helps airlines to be more sustainable. Here are some key facts about Logipad (figure 1).
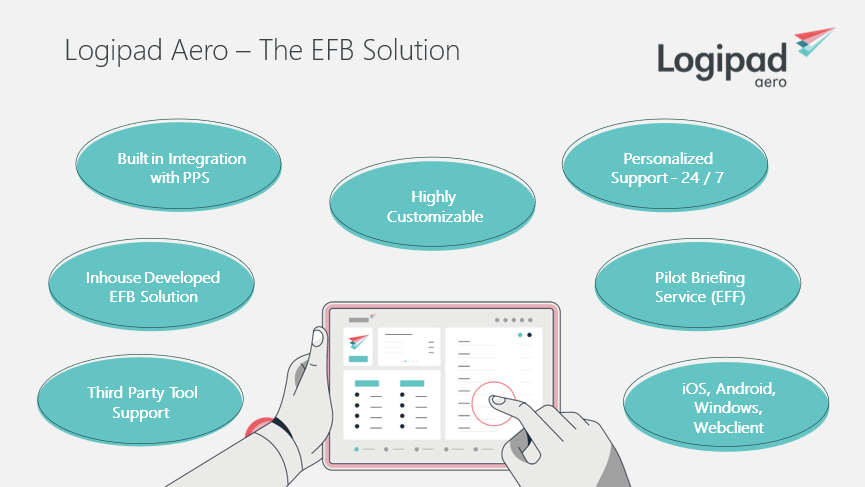
Figure 1
One of the main features of the solution is the EFF module where the pilot briefing takes place and the solution’s biggest strength is that Logipad is highly customizable making it even more convenient for pilots to find documents and to work with the briefing, and that saves time. Logipad offers personalized support 24/7, based in Germany with fast reaction times; necessary in aviation and appreciated by customers.
The Application can be run on iOS, Android, Windows and Webclient and, interestingly, almost all third-party tools can be integrated with Logipad into the brief. If users have information such as performance, weight & balance, etc., data that needs to be included in the briefing, that can be added into the briefing so that, with it all in one place, it can be in the briefing service which is also very convenient. Logipad also has a close relationship with PPS flight planning system and therefore a short integration time and a built-in integration for the briefing template.
How Logipad is built
There are two sides to the solution; modules and tools (figure 2).
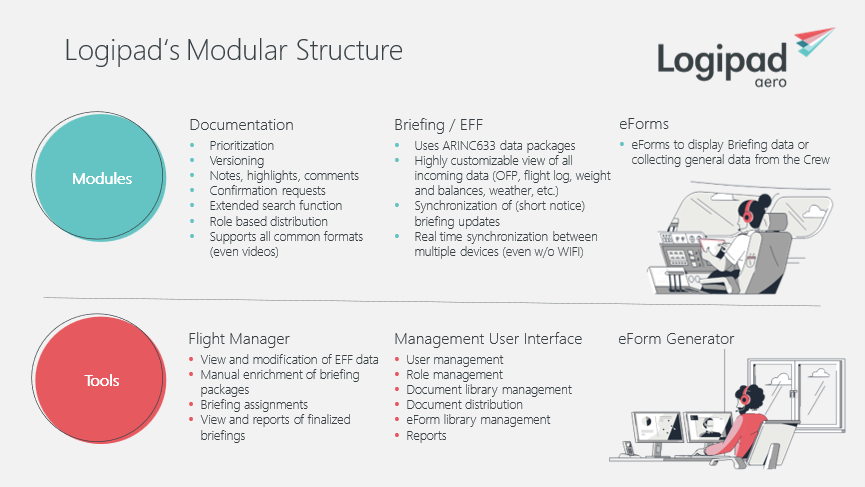
Figure 2
The application side is built in modules the first of which is the documentation module which holds the library where documents are stored for use by pilots. It includes a very good search function and the capability to make documents confirmable so that management knows when they have been received and read.
Besides that, there is the briefing module which is the module where the briefing takes place. For data transfer, we use the standard ARINC633 data packages. Again, it’s highly customizable and can enrich briefing data from the flight planning system with all the information available from third party tools. It has synchronization which means that when there are updates to briefing packages there is almost real-time synchronization to the application, if there is a Wi-Fi connection. Users get notified if there’s an update and the briefing package will be updated, again in near real-time. There is also device-to-device synchronization that functions without Wi-Fi. So, if the pilot in command and the co-pilot are on the briefing simultaneously, which is possible, those data or information that they enter into the briefing are synchronized simultaneously. There is no redundancy with both pilots working on the same briefing.
And there is the eForms module, helping users to display data more conveniently and more easily, since they can make their own eForms. While Logipad does make some complex eForms, the solution comes with a built-in form generator for users to make their own eForms and they can integrate data into the eForms to work with that data easily. eForms can be pre-filled so that users spend even less time with the data.
Besides the modules, Logipad has Tools, which is more about the back-end of the solution for Flight Ops and EFB administrators. First there is the Flight Manager, which is where the briefing data from the Flight Management System gets into the back-end of the system to be enriched with flight information data and all the third-party tool data before being packed together and sent to the application.
The management user interface is the management tool where users can manage the users, manage the library and get the reports off. Then there is the eForm generator, the tool to generate your own eForms.
Zahid Sultan Khan
THE IMPLEMENTATION JOURNEY AND CHALLENGES
As well as the implementation, we will also look at associated challenges we faced at Silk Way West and how we overcame them.
One of the two main challenges that we found with implementation of an EFB solution was integration with other systems. A key requirement for Silk Way West was that the EFB solution should integrate into all of the departments in the company. Speaking as a Pilot, my own view is that paper is always the easiest option for us. It is easy to just take a piece of paper and fill it out in flight. I realized that there was little point incorporating an EFB solution for the sake of it, it had to work for the whole company. That is another reason why we opted for Logipad because we found that, as an IT company, they were intellectually and technologically capable of integrating other systems into Logipad for us. It was quite a challenge to get other companies whose solution might not have been set up to integrate with other systems to talk with the Logipad app and, as I mentioned above, DextraData being an IT company made that much easier.
The second challenge with implementing the EFB at Silk Way West was determining the operational workflow which a pilot would go through in flight. My view would be that if you are going to implement an EFB solution, you need to have the vision for what is required from the solution you select and how it should be used in practice. This is vital because there are so many providers out there, so many solutions that you might find yourself being led up the garden path going with a company with an EFB solution that does not fulfil all of your requirements. You need to have a clear vision of what you want from your EFB solution.
We wanted to maintain familiarity with traditional workflows for pilots and our Operations Control Center (OCC) while delivering the advantages of an EFB solution. There are occasions where an airline might approach EFB selection with a clean sheet notwithstanding the fact that they already have established systems and procedures before embarking on an EFB. Perhaps they still want to start afresh and take a new solution as is. With the cargo industry, we tend to have relatively refined processes already. In our case, these processes are traced back from another major European cargo carrier who has been in the business for more than fifty years and has, in that time, refined these processes very well. Therefore we’re quite happy with our processes and wanted to maintain familiarity for the pilots and OCC so that they would not find it a huge difference from the traditional workflow – mitigation in the Management of Change. We were also looking for logic and simplicity in the workflow plus, of course, you always must incorporate human factors along with threat and error management into the entire process. If there is a mistake to be made, it will happen at some point. The great thing with EFB and technical solutions is that verifiers can be incorporated so that if, say, the pilot tries to enter a zero-fuel weight that exceeds one of the limitations for the aircraft, the system will warn the pilot and will not allow the entry. Overall, an EFB solution improves flight safety if it is done correctly.
THE FUTURE VISION
Let us now look to our future vision and what we aim to achieve with Logipad. The solution is young in our operations and to that end, we want to see a robust in-service performance. We are still proving the system to our national regulator, the State Civil Aviation Administration for Azerbaijan. An EFB solution, as well as an EFF, is quite new to them so we have to prove, that the system is robust and capable of overcoming flight operational challenges. Going fully paperless requires confidence in the system and its performance delivery to avoid downtime for the flight operation stemming from an EFB or EFF problem; that would be completely unacceptable as far as Silk Way West is concerned.
We also wanted to be able to collate accurate operational data which will be used for business optimization and allow the airline to evolve with market trends. It is still new territory for us but we are really keen to see what data we will be able to take from Logipad for our business.
At the time of writing, we were working on connecting the cargo manifest with the EFB and the integration is in progress. We expect this to be a little easier since our load plans, load sheets and cargo management are already in a digitized state. At the moment, we are at a hybrid stage with the EFF while this work is completed. The load sheet and manifest were two of the outstanding things left to do, but it is in progress and is more than possible.
We aim for continued innovation and sustainable development. That will entail feeding back experience to improve the product and to which Logipad are very open and encouraging. We also aim to work together to continue incorporating new technology and enhancements within the EFB. DextraData’s IT background opens opportunities and possibilities for collaboration in other fields of logistics. Silk Way is not just an airline; we are one of three airlines in the group and, 80 kilometers outside of Baku, we are building our own airport which aims to be a bridge of logistics between the cargo flows of the East and West. There are other areas of logistics which come into play here such as the handling of cargo on the ground and so we will be keen to work with DextraData to see how they can develop IT solutions for our complete logistics chain.
Embarking on a program like this can be a step into the unknown and so I hope that this brief story of our EFB program at Silk Way West will be useful for readers who might be considering a similar move.
Comments (0)
There are currently no comments about this article.
To post a comment, please login or subscribe.