Articles
Name | Author |
---|
CASE STUDY: The path to new in-flight fuel savings at Transavia France
Author: Capt. de Norman, Pilot, Transavia
SubscribeCapt. de Norman explains how and why combining historical and real-time AID data triggers new in-flight optimization levers through the EFBs
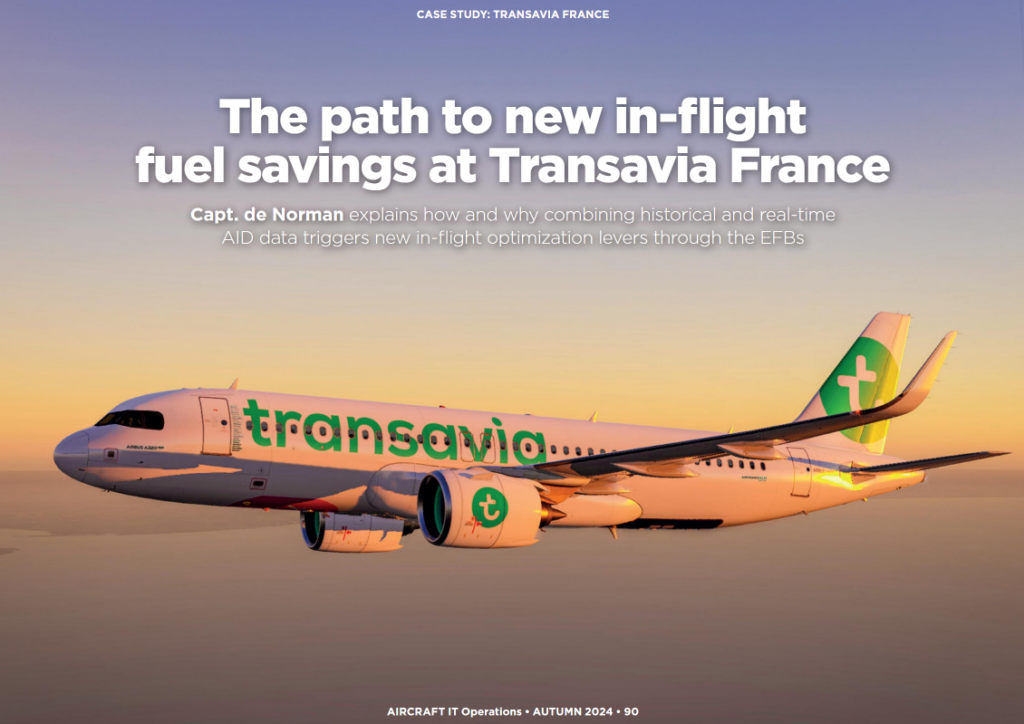
There is no doubt that reduced fuel consumption and lower CO2 emissions are high on every airline’s agenda for change. New digital software solutions will make that a great deal easier and more achievable but just as important is the human interface and engagement which, in this case means the pilots. It is a given that fuel efficiency solutions should use technology to support pilots in decision making for fuel management but without distracting them from their core tasks of flying their aircraft safely. In this article, I want to share with readers our experience at Transavia France of combining historical and real-time AID data for new inflight savings through the EFB. We are performing this project as a collaborative effort with OpenAirlines focusing on Engine Out Taxi In at the moment. First, though, some insights on Transavia France and about our commitment to sustainability.
TRANSAVIA AND ITS COMMITMENT TO SUSTAINABILITY
Transavia, the low-cost airline of the Air France – KLM group, operates more than 350 routes from France (Orly, Nantes, Lyon, Montpellier, Bordeaux, Marseille…), the Netherlands (Amsterdam, Rotterdam, Eindhoven) and Belgium (Brussels) to destinations in France, Europe, and the Mediterranean basin. At the time of writing in 2024, Transavia France had a fleet of 81 aircraft with 68 Boeing 737-800 and 13 A320neo. The airline is committed to its current fleet renewal program which will eventually see us switch to an all Airbus A320neo fleet. In 2023, Transavia France carried 13 million passengers to more than 120 destinations on over 200 routes. The guiding motto of Transavia is that ‘we make low cost feel good!’ There are more than 900 pilots and we ensure an open-door policy for employees to be able to raise concerns (safety-wise but not only that) which we try to answer honestly so that everybody feels part of the business and pleased to be so.
The sustainability roadmap for Transavia is part of the overall Air France-KLM Group commitment to reduce CO2 emissions per passenger kilometer by 30 percent by 2030, from the 2019 baseline. There are a number of initiatives to achieve this.
We are removing as much plastic as possible from onboard our aircraft. That is a big program that we started in 2019. Another step is to incorporate Sustainable Aviation Fuel (SAF) in the production of which the Air France-KLM Group has invested. As a concrete example, the first delivery flights of the A320neo are being made with up to 30 percent SAF. However, our first lever for achieving our environmental objectives is fleet renewal. Our A320neos enable us to produce a 15 percent saving in CO2 emissions and a 50 percent reduction of the airline’s noise footprint. That’s a big challenge for us as we’re based in an area where concerns about noise pollution is very strong. Education is important for pilots, cabin crews and ground ops personnel. When a pilot joins the airline, their induction includes a focus on fuel efficiency and CO2 efficiency because it is part of the pilots’ job today. It’s also part of our line training and a big focus point for the training department. As part of recurrent training for pilots, we have a monthly communication; there is also a company bulletin with facts and figures, it is a constant communication in the flight deck.
We encourage eco-piloting techniques such as, for instance, continuous descent approach, low-drag approach, reverse use and single engine taxi operations. We are proud today to already have good results with these practices but recurrent training and communication are the main keys to sustain this; both are really important when working with the pilots.
DIGITAL TRANSFORMATION TO BOOST FUEL EFFICIENCY
Digital is in the DNA from when Transavia was created. Regarding fuel efficiency, we started building a strategic partnership with OpenAirlines in 2010, implementing Clean Sky, a European project (figure 1). At this time, sharing and using aircraft sensor recorded data for another purpose than Flight Safety was very disruptive.
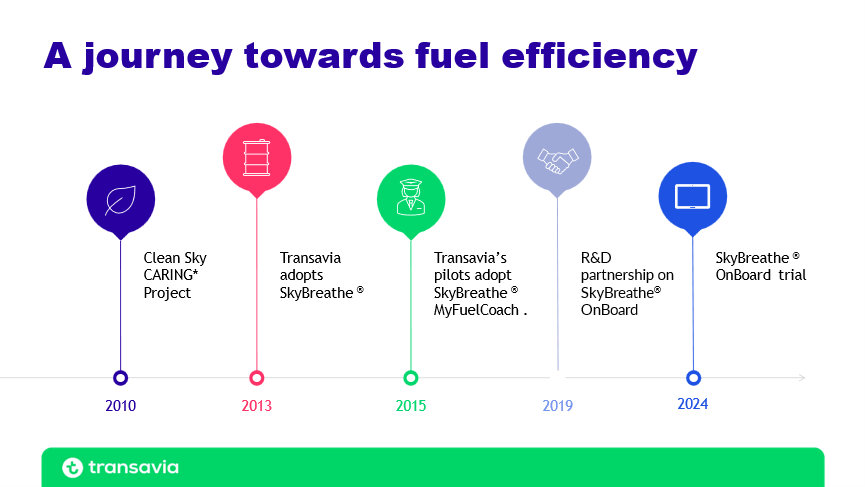
Figure 1
In 2013, Transavia became the first airline to adopt the initial version of SkyBreathe®, a web-based solution collecting/analyzing data from the aircraft (predominantly QAR and operational flight plans). We generated our first data-driven analysis for different stakeholders to see what was happening on different routes and in variable conditions; in short, we could start precisely monitoring our fuel consumption and the application of certain best practices. At that time, the website was also available to pilots who could monitor their own fuel efficiency on previous flights so that was a good learning tool for them.
Moving forward, in 2015, OpenAirlines offered us to be the SkyBreathe® MyFuelCoach application launch customer. OpenAirlines were the first to offer such an innovative application for pilots. MyFuelCoach is a mobile/tablet App on the pilots’ EFBs, for briefing and debriefing purpose.
NEXT CHALLENGE: BRINGING EFFICIENCY TO THE COCKPIT
The next challenge is to look at fuel efficiency with the focus on optimizing cockpit operation in real time. Based on our operational experience, we remain convinced that pilots’ engagement is pivotal on some best practices in order to capture the remaining potential of fuel savings, because small amounts of fuel saved per flight make big amounts of fuel saved globally. In 2019, before Covid, we started a new project with OpenAirlines to create a new application called SkyBreathe® OnBoard with a focus on Engine Out Taxi In. It provides real-time information to pilots and we worked with them on the development of the application. In 2024, we have been able to start the tests in real operations. There were some technical challenges connecting the EFB to the aircraft interface device (AID) as it was our first operational use-case. We overcame these technical challenges by managing smartly this three parties’ partnership (Transavia, Collins Aerospace and OpenAirlines). Indeed, our 737NG are equipped with Collins Aerospace Intellisight AIDs.
Our objective was to improve both the rate and quality of application of Single Engine Taxi In. EOTI is already a best practice for Transavia. For the B737NG, we have customized our Operations Manual Part B to allow the procedure to be applied by the pilots. The application rate on the network is, prior to the use of SkyBreathe® OnBoard, 35 percent in outstations and 45 percent at Orly. We know by providing the pilots with a ‘pop up’ on the Electronic Flight Bags’ screens taking into account all the mandatory conditions like N1, engine cool down time, arrival apron, taxiway specifications and conditions, airport congestion as well as the likelihood that pilots often have to stop the aircraft and/or change the route. As a result, the rate of application is not optimum.
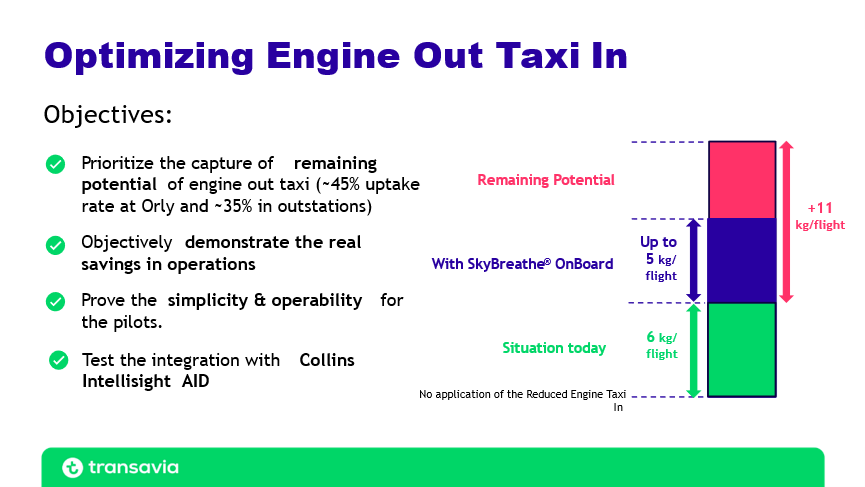
Figure 2
Today in nominal operations, we already save an average of 6kg per flight when the Single Engine Taxi-in procedure is applicable at the arrival airport.
The remaining potential on the same scope is estimated to be slightly more than 11 kg. With SkyBreathe® OnBoard, our objective is to boost Single Engine Taxi-in savings by an incremental 5kg per flight. There will still be unpredictable conditions (e.g. weather or ATC instruction) leaving the final decision with the Captain as to whether or not to apply the best practice under certain conditions.
In order to engage, and keep engaged, the pilots, and consequently achieve these objectives, the process needs to be as seamless as possible in operation. If the pilots depend on another App on the EFB, additional click, actions, input to make, this will lead to pilots’ disengagement. Indeed, the focus and priority will be given to the safe conduct of the taxi during this intensive workload trajectory of the aircraft. We need pilots to do their primary job which is to maintain the safety of the aircraft. For these reasons, we wanted an application ensuring minimal pilot workload, and reducing the cognitive bandwidth with the zero-input philosophy. This is really the game-changer and obviously mandatory to ensure pilots adherence to its use.
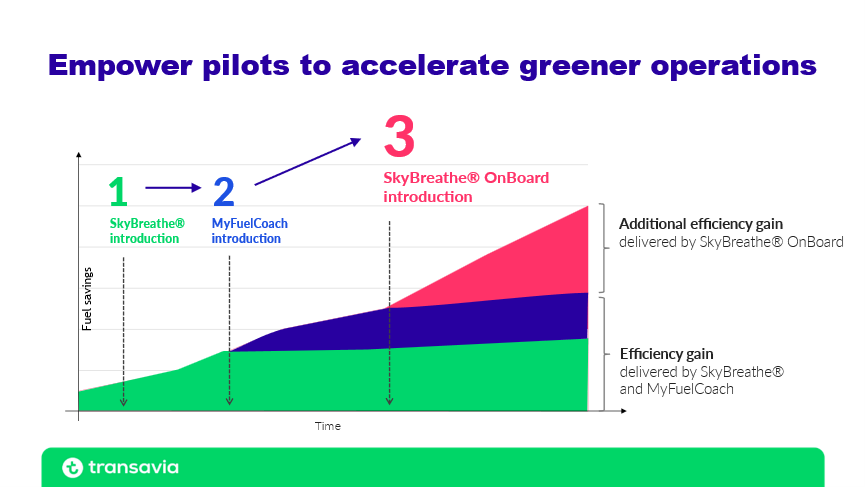
Figure 3
With the first monitoring steps in 2010 to MyFuelCoach starting from 2015, you can see the incremental benefits gained (figure 3). Now, with SkyBreathe® OnBoard, we are targeting to achieve further savings. This incremental step is estimated to save five or six kilos a flight which, adding up over a full year’s operation, leads to substantial savings. Again, the pilots need to be focused on the main job which means reducing their cognitive load (figure 4).
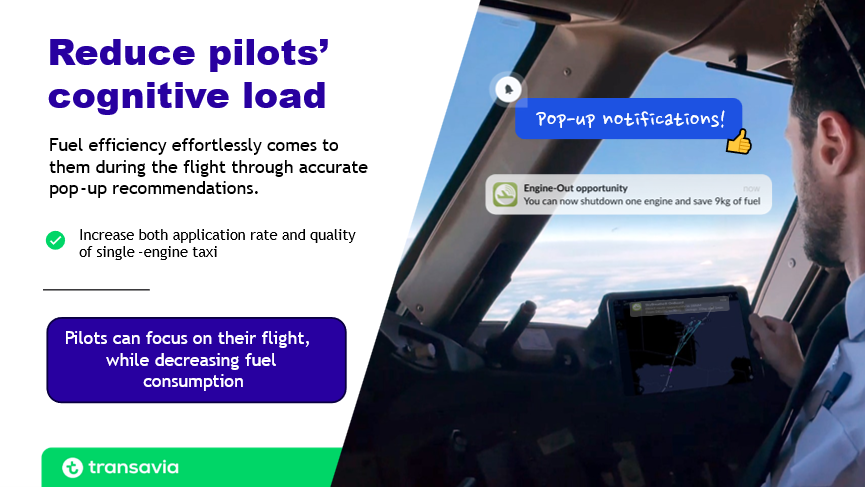
Figure 4
SkyBreathe® OnBoard requires minimal input from pilots. And the objective is to have an application working on its own reducing the ‘app fatigue’ for pilots. It will display iOS native pop-up notifications to the pilot (like we have on our mobile phones). These pop-ups inform the pilots, taking into account the limitations from Boeing, the engine OEMs and the standard operating procedures (SOPs) and come up when the pilots need this extra support. Indeed, these take into consideration the engine cool-down time, the slope of the taxiways, runway crossing and we hope soon to also be able to take into consideration the weather and contamination of the taxiway. So, once everything has been set-up in the App, the pop-up will optimally appear when the opportunity comes to shut down one engine for the taxi in.
In figure 5 is the project timeline.
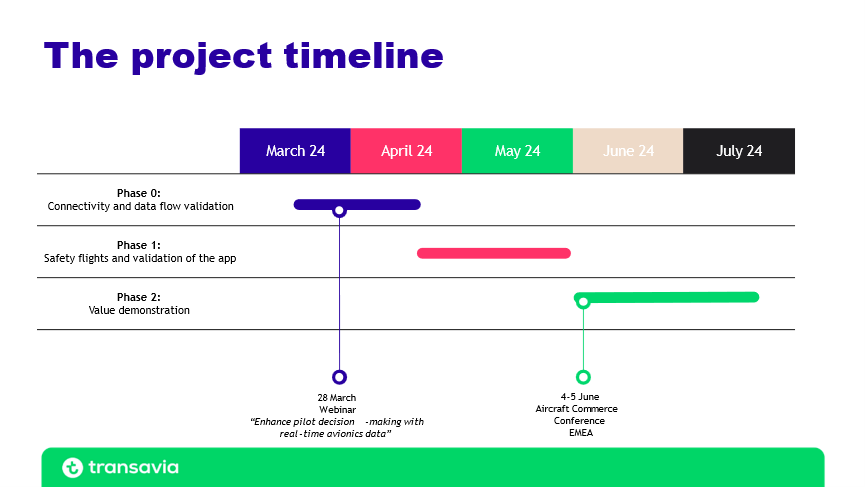
Figure 5
There was a long preparation phase to ensure that we properly connect the EFB world to the avionics one (the connectivity and data flow validation phase). We then also needed to be 100 percent sure that there won’t be any negative impact on operations or the workload and the fatigue of the pilots. A change management analysis has been conducted and the French competent authority has been informed; this safety and app validation flight phase enabled us to positively conclude all of this and reach the next step which is the value demonstration phase in May and June 2024. All pilots have been involved on a voluntary basis and across all of the network in order to precisely and objectively measure the contribution of SkyBreathe® OnBoard and therefore isolate how much it enables Transavia France to incrementally save.
IMPLEMENTING AN EFB LIVE-ASSISTANT TRIAL
Now, we are looking at how the new process will fit in our procedure (figure 6).
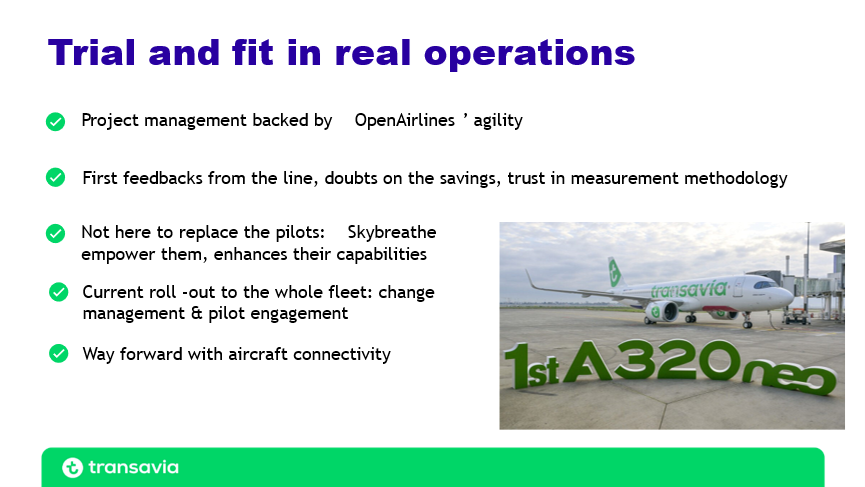
Figure 6
Agility and having an open mind, from us and from OpenAirlines, were (and will continue to be) important because, as a new product, we had to change many things such as having to review the methodology of calculations. We, initially, had doubts on the savings but trusted the OpenAirlines’ methodology. There were also some doubts from the pilots’ population which we had to address through communications. The objective is clearly not to replace the pilots, it is to empower them: this is like having another co-pilot in the aircraft to enhance the pilots’ capabilities to focus on their main job and assist them when they need it.
Now we are undertaking the roll out to the whole fleet. Initially, we are deploying the app on the 737 fleet. For that we had to work with Collins on a new AID configuration that we deployed to the whole fleet. We will then start to deploy on the A320neos when the first tests are completed, relying on Airbus FOMAX.
The EFBs are connected by Wi-Fi to the aircraft’s Aircraft Interface Device (AID), broadcasting aircraft avionics information to the application. Once on the ground, the EFB is additionally connected to a normal Wi-Fi connection and all the information is transferred to OpenAirlines. The operation is starting now and we do already have some positive results plus the quality of the application is improving a lot.
There is also the need to work with pilots’ unions when making any changes to working practices like that, especially if safety might be affected. Unions are part of the industrial landscape in France and have to be included. In the AF-KLM Group, we have good and opened collaboration with the unions with meetings twice or three times a year. When we share data to an external company like OpenAirlines, we need an agreement with the unions. In fact, every time we work with an external company, there needs to be an agreement with the unions.
Looking at the regulators in France, when we explained the project and showed them how the application works with the pop-ups, the first question was, ‘Will this require inputs from the pilots and does it involve any bright lights and/or any noise that might distract the pilots?’ We were able to confirm that there would be no pilot’s input, nor light or noise, just a pop-up. That was the main challenge from the competent authority.
This has been a worthwhile program during which careful planning and implementation taking into account the needs of all stakeholders have paid off. I hope that sharing our journey with you will help when you decide to make a similar commitment.
Comments (0)
There are currently no comments about this article.
To post a comment, please login or subscribe.