Articles
Name | Author | |
---|---|---|
Charting an Optimal Course | JD Sillion, Chief Solutions Officer, Flatirons Solutions | View article |
Moving Day, Getting Ready and Afterwards | David A. Marcontell, President & COO, and John F. Smiley III, Aviation Analyst, TeamSAI Inc. | View article |
Case Study: New Generation Reporting Tools | Caroline Deba, Reliability Manager, Air Tahiti Nui | View article |
Case Study: Enhanced Business Operations | Jorma Ryske, Director Finnair IT Aircraft Maintenance | View article |
Charting an Optimal Course
Author: JD Sillion, Chief Solutions Officer, Flatirons Solutions
SubscribeCharting an Optimal Course
In the last article we discussed how adapting to S1000D requirements while maintaining support for iSpec 2200, as required for existing fleets, impacts the civil aviation ecosystem. This article identifies the requirements necessary to support a high performing multi-specification (multi-spec) technical information management system and options for getting there.
Requirements for a multi-spec Technical Information Management System
Whether an OEM, an airline or an MRO, at the most basic level every organization uses its technical information management system to create or bring in data and provide a way for end users (supply chain partners, technical operations and engineering staff, aircraft technicians, crew members, and others) to access it. At a minimum the system must provide content editing, storing, and viewing capabilities.
However, the reality of managing technical information throughout its lifecycle to meet specifications for existing and new-generation aircraft is much more complex than just addressing these basic concepts in a simplified fashion. To operate successfully in today’s multi-spec environment, organizations must meet these requirements:
Create and Support a Variety of Content and Data Types
This includes both structured and unstructured data, including SGML or XML for iSpec 2200 programs and XML-based S1000D data modules for new-generation programs. It also includes the ability to support a broad variety of media types, from 3D models, vector-based and raster graphics, video, audio, multimedia and other file types that are now available and can improve the precision of technicians’ work as well as reduce the time they spend performing it.
To meet XML requirements, more successful approaches include adoption of XML editors that reduce the learning curve for authors who are new to XML and that are tightly integrated with other components of the larger system, such as TechSight/X® Editor based on Serna XML Editor from Flatirons Solutions (formerly InfoTrust Group). It offers a word processor-like interface, instant XML validation, and other user-friendly features that make the adoption of XML easier while providing capabilities that experienced XML authors expect. Its integration with the TechSight/X CMS (content management system), also facilitates content authoring and editing to increase authors’ productivity and speed up the delivery of up-to-date information to end users.
One of the greatest benefits of adopting XML is the opportunity it affords organizations to reuse content across functional domains, such as engineering, technical publications, training, support organizations, and other groups. Reusing technical information — rather than recreating it in multiple departments for other purposes — is the best way to ensure information consistency, drive greater content accuracy and lower the cost of technical information even further.
Manage content for ATA iSpec 2200 and S1000D formats throughout its lifecycle
Organizations also must have a CMS (content management system capable of:
- Capturing, managing, and publishing content securely in multiple formats (print/PDF, SGML/XML, and HTML);
- Supporting automated import and processing for all common document types to reduce data processing time and costs;
- Versioning, access control, and rollback features for compliance traceability and responsive audit times;
- OEM revision management tightly coupled with the authoring environment to speed up revision times and improve author productivity;
- Powerful publishing capabilities, such as effectivity and applicability-driven fleet, tail, or serial number-specific publishing; both full and incremental publishing; the ability to publish to both online and offline, interactive electronic technical publications (IETPs) and mobile devices; and the ability to publish to external systems such as electronic flight bags.
Support print, web, and mobile delivery channels with an experience optimized for each one
A multi-spec system also must be able to display content to end users coming from both iSpec 2200 and S1000D formats, dictated by the aircraft program but of little importance to technicians and other end users whose concern is not with the underlying information standard but rather the timeliness, accuracy, discoverability, search relevance, and usability of the information itself.
This means organizations must be able to deliver information to the IETP (interactive electronic technical publication), Web viewer, or tablet devices with intuitive navigation and search (which reduces repair times and optimizes technical data for technicians’ consumption); with effectivity and applicability filtering (which aids the technician in compliance with regulations); with integrations to parts platforms and OEM ERP (enterprise resource planning), MRO, and records management systems (which streamlines repairs and accountability by giving access to external applications from within the viewer); and through stand-alone IETP deployment modes to allow for controlled access from remote sites.
To support growing demands for mobile access to content, the CMS and IETP system also should be able to deliver aircraft maintenance content and manuals to tablet devices. This provides technicians quick and easy access to all maintenance documentation at the point of performance, reducing the number of trips technicians make to computer stations and significantly improving time to completion. The most effective mobile solutions will provide touch screen search and navigation to minimize user clicks for finding information; and they will provide navigation of complex wiring diagrams so technicians can perform tasks at the aircraft itself with all of the information they require. For a complete mobile solution, organizations need to look for features that support technicians’ ability to view and order from illustrated parts catalogs, allowing them to complete tasks faster and giving them both on- and offline access to maintenance manuals so technicians can access information whenever and wherever they need it.
Integrate with work card systems
A multi-spec system that supports the authoring and editing of reusable iSpec 2200 and S1000D content also can afford airlines the ability to reuse information from maintenance manuals (AMMs, EMMs, and CMMs) directly in work cards. This speeds up the creation of work cards, improves work card accuracy and consistency, and can lower the costs of ongoing work card creation and revision management for both existing and new-generation aircraft.
Requirements for integrating maintenance manuals with work card systems that airlines should look for include capabilities to create, revise, and manage work cards and group work tasks into logical packages. The system should be able to publish work cards and other data for use by end users and external systems.
Furthermore, the system should manage maintenance visits through the import of maintenance visit requirements from existing scheduling systems with capabilities that include the automatic assembly of required job cards based on visit requirements; batch printing of maintenance visits to system printers; auto-populating access panel cards during visit creation so that access panels are tightly managed in the visit, reducing duplicate access open and closes; and integration with existing materials management systems to include real-time part and stock information in displayed work card content.
Optimize processes throughout the technical information lifecycle
One critical function for a technical information management system in an industry as heavily regulated as civil aviation is to the ability to provide visibility into the overall information management process itself – for both productivity and regulatory compliance purposes. This becomes even more challenging as airlines begin taking delivery of the 787 Dreamliner and anticipate how they will fold the A350 into their existing processes.
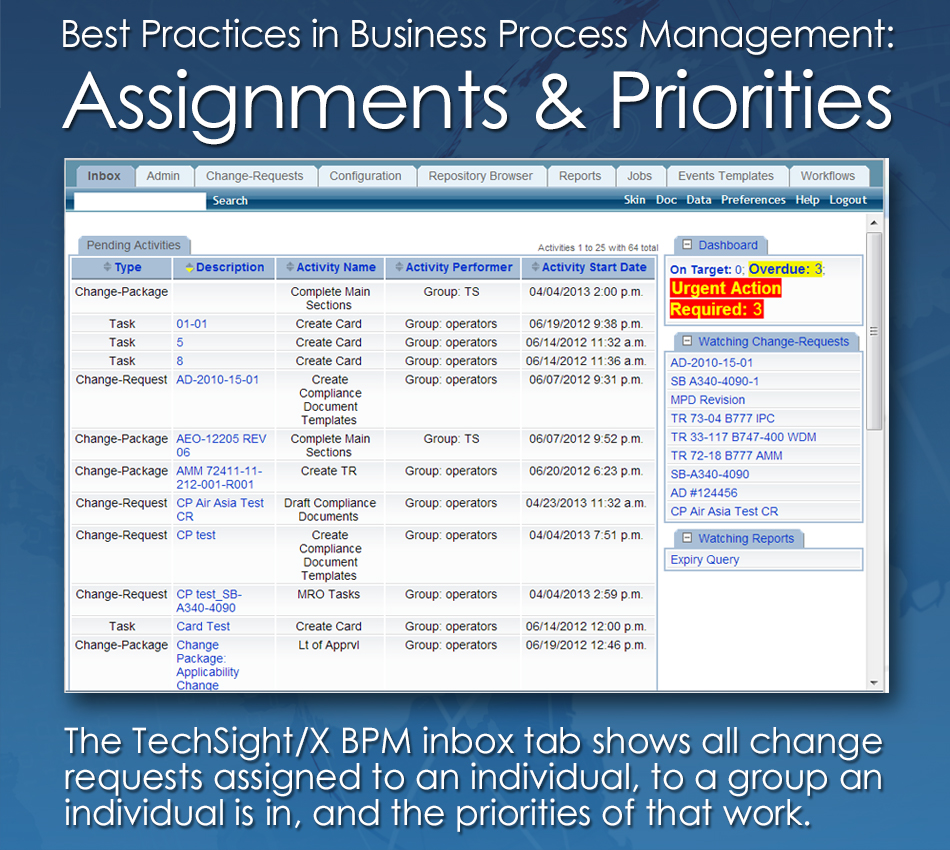
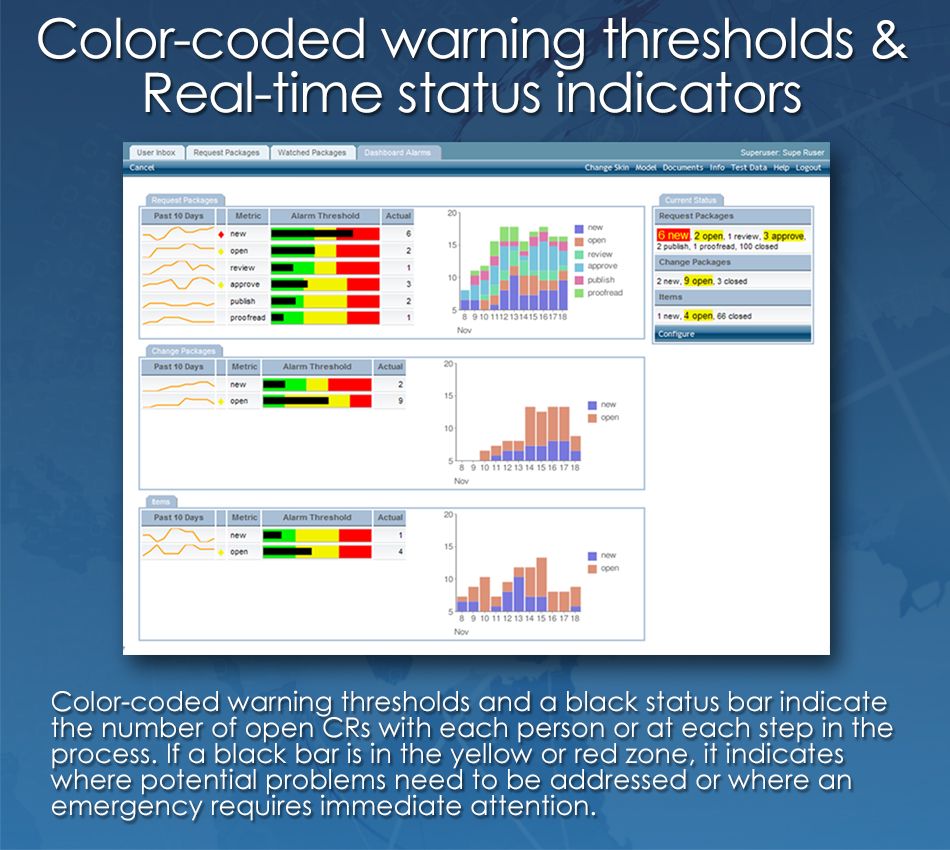
Integrate with External Systems
Technical information — such as that used to maintain or operate existing and new-generation aircraft — should never be isolated from the operational systems that invoke it. Providing streamlined end-user access to external data or applications that can contextualize technical information and make it more actionable for content consumers is key to driving productivity improvements.
Typical integrations aerospace operators should include in their system are:
- CMS integration with a maintenance enterprise resource planning (ERP) platform to assemble work packages for visits;
- Viewer integration with aircraft health maintenance (AHM) or other fault code generating systems to allow pre-emptive assembly of work packages;
- Viewer integration to parts lookup or ordering systems to allow for replacement ordering at the worksite;
- Record management integration to keep track of maintenance work that has been performed on aircraft.
Aerospace OEMs may also benefit from CMS-based integrations to back-end infrastructure such as engineering product lifecycle management (PLM) applications that supply reusable text and imagery assets for use in the assembly of technical publications or related training materials.
The requirements for a multi-spec technical information management system discussed above assume that a system can support multiple information standards, the fundamental capability underlying a multi-spec system itself. In order to take in, store, and publish out information (as well as perform the other functions described above) regardless of its format, the most efficient system will allow an organization to support content for both legacy and next-generation fleets as well as take in, store, and publish out data — without requiring an organization to alter or abandon legacy document type definitions (DTDs). The key to this system is normalizing the content through on-demand data transformation.
Choosing how to normalize the data is the function of the system design. With the global aerospace industry moving to the S1000D standard, it becomes a natural standard by which to normalize your data. The system then that uses S1000D for normalizing the data will take advantage of a common source database (CSDB) for content management. It must also natively support multiple S1000D issues and the transformation of source content from other formats (iSpec 2200, MiL standards) to S1000D as part of the content import process. When delivered to users, data can be presented in S1000D or iSpec 2200, PDF and HTML publishing options to provide the required level of flexibility needed to support a wide array of spec-defined programs and contractual commitments from within a single publishing environment.
The access a new technical information management platform has to historical data greatly impacts an organization’s data continuity. Organizations should work with content end users and IT to identify the content that has value and relevance to the enterprise and select a migration approach that captures that value at the lowest possible cost. As operators and OEMs evaluate the wealth of often unstructured content that underlies their businesses, selecting an optimal approach to get the benefits of this content without the cost or delay can be accomplished through examining legacy application server logs, polling end users, or reviewing contract commits to determine which content needs to be augmented for continued use versus simply archiving it for periodic reference.
As more airlines take delivery of Boeing 787 Dreamliners – and as Airbus ramps up production of the Airbus A350 – every organization in the civil aviation ecosystem will need to support some combination of these capabilities to fulfill its existing and new-generation aircraft program requirements. Let’s take a look at the options for acquiring a multi-spec technical information management system.
Evaluating product and solution-based approaches
A perennial question for organizations assessing their options to meet evolving technical information management requirements is ‘build or buy?’ Or, put another way, does my organization get the best long-term ROI (return on investment) from a content solution that is uniquely crafted to suit my needs (the ‘build’ approach in which a tailored solution is deployed) or one that uses commercial off the shelf (COTS) products that are configured rather than customized to meet the business’s information management needs?
The answer depends on the demands of the marketplace and the needs of the organization operating within it. There are both pros and cons that are worth discussing to understand the implications of this decision for aerospace companies as they consider how to meet their needs in the evolving landscape for technical information management.
‘Build it’ – the custom solution approach
The lure of a custom solution is an easy one to understand. After all, what organization wouldn’t want an application designed from the ground up to meet its business’s unique needs? A tailored approach to meeting an organization’s business and technology requirements carries strong benefits, from improving business processes, facilitating regulatory requirements, helping technicians perform tasks faster and completely matching the operations needs and processes, lowering the cost of publications, and more.
However, to meet the requirements outlined above, the functional scale is daunting even for the largest organizations. This approach typically involves a blend of commercial packages, open source offers, and heavy systems integration and custom development components to create a solution tailored to the needs of the organization.
The consequences of such a pieced-together solution are multifold, including higher costs and more complexity to meet custom requirements, the lack of proven reliability in a live production environment, little to no industry-specific functionality, costs for on-going support, longer time from funding to implementation, and long-term flexibility of the solution. By building custom features and functionality without the benefit of a broad user base, a manufacturer or operator seeking to implement their own technical information management solution is in effect building a product for a market of one. While this may sound like a cozy arrangement, what it means long-term for most organizations is an underfunded infrastructure that lacks the broad investment needed to grow features or functionality in response to or in anticipation of market needs.
In essence, the ‘build it’ approach to meeting technical information management and delivery requirements is a valid one, but only for organizations whose scale of operations is sufficiently large to ensure continued, ongoing investment in system capabilities in the absence of a broader community of like-minded adopters.
‘Buy it’ – leveraging a COTS product
In light of the drawbacks of the ‘build it’ approach, the traditional ‘safer’ option in many application procurement situations is to buy a fully productized solution. This option may be suitable for many organizations, including small or mid-sized ones willing to change their current business practices to adhere more closely to broadly defined industry best practices as modeled in COTS products.
For some airlines a COTS solution, such as those provided by airframe OEMs or entry-level commercial software publishers, may meet their basic content capture, revision management, and distribution needs. Particularly for carriers with small or homogenous fleets, the COTS option may represent an optimal approach in which the organization adopts both a full-fledged authoring and revision capability, but without the cost of complexity that comes from a custom-developed solution mentioned above.
For OEMs the more complex requirements around the authoring and distribution of multi-spec content to a wide array of manufacturing and end-customer content consumers is a more difficult challenge, one that is not well-met with a highly specialized offer due to both the complexity of the data being authored as well as the program-specific transformation and packaging delivery requirements.
For those considering the COTS route to adopting a new technical information delivery capability, there are a number of considerations including:
- Willingness of the organization to change its existing practices: since the software is being adopted in a more or less ‘as is’ form, the organization will typically need to change its business processes to better align to the tool.
- Vendor viability: since adopting a comprehensive technical information management system will be a commitment of 10 years or more for most airlines and OEMs, ensuring the financial and technology viability of the vendor being considered is key to avoiding the trap of relying on an unsupported, legacy tool. Organizations should evaluate the vendor’s track record in production environments as well as their domain knowledge and active participation in organizations that address evolving technology challenges in civil aviation.
- Roadmap and vision: since a COTS purchase represents a long-term commitment to a set of vendor-driven features and functionality over which the adopter will have little direct control, ensuring that the roadmap and product vision are complete and consistent with the organization’s identified needs is a critical step. A product lacking a coherent long-term roadmap with clear R&D support – signaling ongoing investment in the solution, or rather lack thereof – is probably a poor choice.
‘Blended’ approach – best of both worlds?
As is often the case, a middle approach to addressing the technology acquisition question is sometimes the most advisable for risk mitigation and outcome optimization. In the case of selecting a core technology upon which to build a multi-spec technical information management system, this middle approach involves selecting a best-of-breed (BoB) COTS product as the basis for a solution, then extending it judiciously to meet an organization’s specific needs.
In this model, extensions to the core product are done in partnership with the software provider to ensure to the greatest degree possible that extensions are made in a way that will be compatible with future updates to the core platform, and that they are architected in a manner that is compatible with the underlying COTS application.
For example, most COTS solutions should provide some level of support for the core functionality outlined in the requirements section namely:
- Content capture / revision management to process inbound content from the source;
- Authoring to allow new content creation and edits;
- Content and process management to drive change management process and implementation;
- Publishing to deliver content where, when, and how it is required;
- Viewing where content is needed most;
- Support for regulatory compliance, including reporting;
- Feedback capture to continually improve content, process, and product.
Some of the areas where you can expect to customize a COTS technical information management solution most effectively are listed below.
-
For airlines…
- Workflows and business rules for content creation and revision management to ensure continuity of internal and OEM change histories for use in compliance reporting and rapid, defensible change management.
- Viewer integrations to back-office ERP, maintenance, illustrated parts catalogs (IPC), and other platforms to improve productivity of maintenance staff using technical information by linking directly to ‘adjacent’ systems to make technical information more relevant.
- Back-office integrations between the technical information management infrastructure and ‘systems of record’ (ERP, CRM, etc.) to allow changes to source systems such as parts databases to flow seamlessly to technical publications.
- Style customizations for manuals and task cards to match an airline’s brand and naming conventions.
-
For OEMs…
- Content pipelines to manage program-driven receipt and delivery of structured content between partner suppliers and end-customer users. These pipelines typically provide processing features like validating to a specific schema or DTD, transforming within or across specifications, or filtering of data based on a particular set of conditions or effectivities. Pipelines can allow the same content to support multiple program commitments spanning manual types and specifications with minimal manual rework.
- Taxonomy management for managing industry, product, and region specific terminology needed to facilitate content usability. Taxonomy and terminology management allow authors to create content that is compliant, then to maintain it dynamically as business and regional needs dictate with minimal manual re-work.
- Supplier / customer portals to automate the capture and delivery of content in ways that are compliant with contract terms and maximize content reusability across the supplier ecosystem while ensuring protection of intellectual property and tracking of outbound technical information assets (watermarking where appropriate, etc.).
- System integrations to source content systems such as PLM (product lifecycle management), engineering and materials management with a goal to increase reuse of content whenever it is available.
A final note
Whether an organization opts for a build, buy, or a blended approach to establishing a multi-spec system for managing technical information, the considerations do not end with those discussed here.
Airline operators and OEMs also will need to evaluate their application hosting and service delivery model. For example, they should determine if they will opt for an on-premise solution or for a hosted solution. If they select the latter, then they will need to evaluate if they will use a private or a cloud-based model. Another consideration is using a traditional software licensing model or a software-as-a-service (SaaS) model.
Finally, whereas this article has discussed the technology considerations in supporting a multi-spec environment, one cannot under-estimate the level of effort required to support user adoption of a new system and the related change management support required to make a new system successful. Both topics merit further discussion within an organization to lay the foundation for success.
From theory to practice: lessons from early adopters
Charting a course to meet technical information management requirements in a multi-spec world presents a wealth of questions and options to participants in the civil aviation ecosystem. In the final article of this series, we’ll move from theory to practice to see how early adopters are addressing OEM and airline requirements to support new-generation aircraft programs in parallel with existing aircraft programs
Comments (0)
There are currently no comments about this article.
To post a comment, please login or subscribe.