Articles
Name | Author | |
---|---|---|
Predictive maintenance — beyond the buzzwords | Sander de Bree, Founder & Chief Visionary, EXSYN Aviation Solutions | View article |
Digital twins: improving the way things work and wear | Nadine Etong, Director MRO Product Line, IFS | View article |
Smartwings App helps better manage parts | Petr Barton, Operational Supply Chain Manager, Smartwings | View article |
Looking for a smarter supply chain in MRO: Part 1 | Amol Salaskar, Consulting Business Analyst in Aviation and MRO, IBM | View article |
Digital twins: improving the way things work and wear
Author: Nadine Etong, Director MRO Product Line, IFS
SubscribeDigital twins: improving the way things work and wear
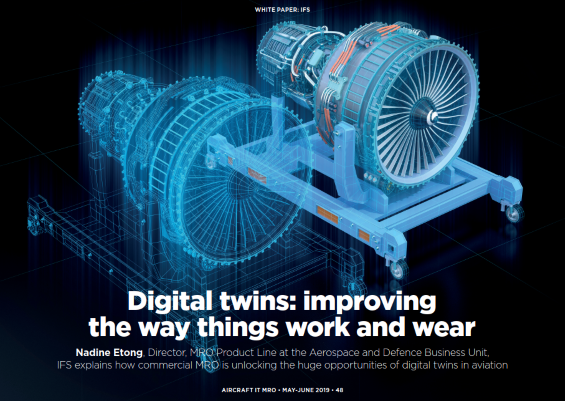
Nadine Etong, Director, MRO Product Line at the Aerospace and Defence Business Unit, IFS explains how commercial MRO is unlocking the huge opportunities of digital twins in aviation
Nadine Etong, Director, MRO Product Line at the Aerospace and Defence Business Unit, IFS
With interest in digital twin technology at an all-time high across a wide variety of industries, one of the forerunners in its adoption right now is the aerospace and defense sector. This is particularly true for the commercial aviation segment. In this article, I want to zero in on the potential benefits in this for independent MROs, outlining how they can leverage the technology to better serve customers, differentiate their service offerings and increase understanding of the specialist assets with which they work.
The global digital twin market size is expected to reach USD 26.07 billion by 2025 – registering a strong CAGR (compound annual growth rate) of 38.2% over the forecast years – and we are now starting to see the first successful use cases of digital twins in action in commercial aviation. GE has already built digital twin components for its GE60 Engine family and also helped develop the world’s first digital twin for an aircraft’s landing gear. In this last scenario, sensors placed on typical landing gear failure points, such as hydraulic pressure and brake temperature, provide real-time data to help predict early malfunctions or diagnose the remaining lifecycle of the landing gear.
FOUR TECHNOLOGY DRIVERS
These major advances in digital twin capabilities have been driven by four key technologies:
- IoT (Internet of Things) and Big Data – The proliferation of sensors on assets or components combined with connected systems allows organizations to gain detailed insights into live performance.
- Advanced analytics – Through machine learning we can use this data to predict and simulate the future condition or deterioration of the asset in question.
- Computing power – Cloud-based technology vastly improves the affordability and availability of the computing power required to run large-scale digital twin models.
- Accessibility – Where previously a digital twin may have been locked into the control room of a factory or organization, this data can now be accessed from anywhere via mobile devices.
DIGITAL TWIN IN NAME ONLY – DISPELLING THE ‘PHYSICAL’ MYTH
But, in order to use them for the benefit of the business, it will first be necessary to understand them: so, what is a digital twin? An accepted definition would be a replica of anything which gives you real-time insight into the status of a real world asset to enable the organization to better manage equipment and inform business decisions. In fact, digital twins have been around – at least in part – for a while, but they’ve taken names such as ‘mirrored systems’ and ‘connected factories.’
However, these deployments have been focused on physical assets, unlike digital twins which are not limited to a 3D model of a single piece of equipment. Running a digital twin for a single asset is only the first step and, thanks to those four enabling technologies, this can now be extrapolated to create a digital twin of a whole fleet of assets. Take this a step further and a digital twin of the whole fleet can become part of a digital twin of an entire business or organization, with process flows visualized and bottlenecks flagged in real-time – much more valuable than one fancy 3D model.
No twins are identical
Digital twins work in different situations, applications and processes depending on the context of the organization in the supply chain. Component manufacturers, for example, are primarily focused on individual components, while engine OEMs care mainly about the engine as an entire asset. Heavy/base maintenance inspectors and regulators are more focused on overall maintenance business processes and standards, and this continues right up to line maintenance providers who look primarily at MRO data and the airline/operator which wants to piece together a digital twin of the entire aircraft.
It’s all about the data – business applications act as key enablers
These differing priorities have a consequence on what a business application needs to do to manage digital twin data. A lot of the data required for digital twin technology sits within supporting business applications: assets are mapped within enterprise software, including historical maintenance data, work orders and original engineering and design data.
From this we can see that enterprise applications are hugely beneficial in constructing different kinds of digital twins. In some cases, the supporting enterprise application acts as a digital twin of certain processes—whether that is the entire business or running a 3D model by taking in data from several third-party systems. In others, the enterprise software could be the source of the digital twin, becoming part of a larger data ecosystem which builds up a digital twin somewhere else. However, this requires flexible and agile enterprise software that has been designed to support digital twin initiatives and is suitable to fulfil a variety of roles – failure to track and deliver data in the right place at the right time could lead to weak links in the chain and undermine an entire digital twin operation.
FOUR BUSINESS BENEFITS FOR INDEPENDENT MROs
Independent MROs who are regularly capturing key data streams in their enterprise software can start to quickly take advantage of digital twinning to differentiate their service offerings against other independent MRO competitors, and also against large inflexible OEMs that have a number of disparate systems in place.
There are a number of ways independent MROs can leverage digital twins to benefit themselves and their customers
Increase aircraft safety
Using serialized asset digital twins in conjunction with real-time/near real-time monitoring and predictive analytics can help detect a defect earlier, through prior insight into the component’s condition. The net result is that part safety is increased, making aircraft and airlines safer. One strong example is Dutch carrier KLM— it reduced its minimum equipment list defects and delays and cancellations by 50% since introducing AI to manage predictive maintenance.
Evolve from repair shop to power-by-the-hour service provider
Digital twins can transform the maintenance models offered by independent MROs toward offering lifecycle support contracts that reduce maintenance visits and costs through individual serialized inspection and service schedules. By taking the pressure of asset maintenance management, MROs allow airlines to focus on their core business of flying passengers, not spending cycles managing wrench turning. MROs can also redefine service contract terms for the specific assets being maintained, based on their digital twin history and projected future performance.
Extend asset life
Digital twins also enable MROs to build a broader understanding of supported assets while in service. They can use predictive maintenance techniques to maximize their availability and time on-wing, or overlay health monitoring data with a digital asset twin to trend performance and reliability on a serial number basis. This gives them unparalleled insight into the assets they support over time. As more asset information is built into the digital twin, MROs can learn from this to cement their reputation as asset or component experts.
Improve the business supply chain
The benefits of a digital twin spread more widely than just the single component in question. By knowing in advance which component will fail, supply chain managers can plan and have parts and material ready and available when needed—either to replace the failed component or for use as part of the repair process. The net result is that supply chain managers have better control of their stocks.
CASE IN POINT: TEST-FUCHS
One IFS customer that has designed a dedicated digital twin program is TEST-FUCHS, a leading manufacturer of test systems and components for aerospace and defense organizations. TEST-FUCHS has a dedicated digital twin approach for ground support assets and test equipment.
As manufacturer of the assets, TEST-FUCHS looks at the engineering and design and procurement data of the asset it is selling, and also has full control of the IoT-enabled test facility to provide maintenance data in real-time and then execute that maintenance in its repair shop. This gives the company a deep view of the data which builds up in an asset’s lifecycle and provides visibility across the entire digital twin landscape around every asset. IFS Applications plays a prominent role in this environment—enabling TEST-FUCHS to build up an enterprise-wide picture of their business processes to put the digital twin strategy into action.
UNLOCK MRO POTENTIAL
MROs are ideally placed to harness the ROI (return on investment) and benefits of digital twin technology to improve and optimize their service offerings and business performance. But in all these examples I have shown, to effectively put a digital twin strategy in place requires the support of agile and flexible enterprise software geared towards data-driven decision-making. With a strategy that is both solid and visionary, and the right software support, independent MROs can take a slice of the USD 26.07 billion opportunity that the growing digital twin market represents, and better serve their increasingly demanding airline customers.
Contributor’s Details
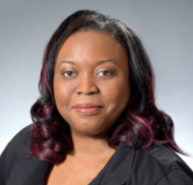
Nadine Etong is Director of the MRO Product Line at the Aerospace and Defence Business Unit at IFS. With over ten years of professional services, product management and marketing experience in the Aerospace and Defense market, Nadine has worked closely with numerous commercial aviation and independent MRO organizations on the selection and implementation of next-generation enterprise asset management software. She is a member of the International Association of Business Analysts (IIBA), holds a Bachelor of Computer Sciences from the University of Quebec in Montreal, and is currently working towards her Masters in Technical Projects Management
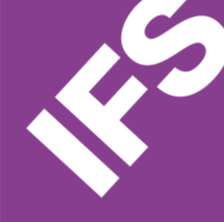
IFS has been delivering value-added solutions to the A&D sector for more than 20 years, providing solutions for commercial aviation, defense, fleet and asset management, logistics, manufacturing and more. Their aviation and defense industry experts are committed to ensuring the future success of customers by providing best-in-class solutions and industry expertise to prepare them for what’s next.
Comments (0)
There are currently no comments about this article.
To post a comment, please login or subscribe.