Articles
Name | Author | |
---|---|---|
The Internet of Flying Things: Part 1 | Michael Wm. Denis, a renowned author, speaker and independent consultant | View article |
Column: How I see IT – Publish, not pass-through: the innovation opportunity for MROs | Paul Saunders, Global Product Manager, Flatirons Solutions | View article |
Air Works Case Study: Thinking about MRO IT | Ravinder Pal Singh, Global Chief Information And Technology Officer, Air Works | View article |
Drinking from the Fire Hose – Modern aircraft and big data | Paul Saunders, Global Product Manager, Flatirons Solutions, and John Knolla, Manager, Product Support Engineering, LMI Aerospace | View article |
Drinking from the Fire Hose – Modern aircraft and big data
Author: Paul Saunders, Global Product Manager, Flatirons Solutions, and John Knolla, Manager, Product Support Engineering, LMI Aerospace
Subscribe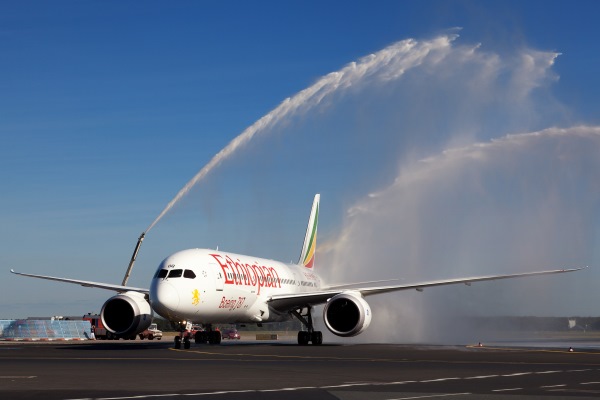
Standfirst Paul Saunders, Global Product Manager, Flatirons Solutions and John Knolla, Manager, Product Support Engineering, LMI Aerospace set out how airlines, operators and MROs can best use the stream of sophisticated information delivered from big data
A product manager spends 20% of their time thinking up new ideas and 80% of their time convincing others that those ideas are right for what they want to do.
Science Fiction inspires technology facts
Those of us who grew up in the seventies and eighties were not short of inspiration for thinking up ideas. Whether it was hover-boards in ‘Back to the Future’, talking cars in ‘Knight Rider’ or other cinema and television icons, there was no shortage of inspirational science fiction devices. While the ideas might have been ‘fiction’, the possibilities in the ‘science’ inspired a lot of people who later went on to have their own ideas that could be applied in the real world. In that sense, science fiction has actually helped us reach the point of technology development where we are today.
Of course, it’s fantastic that we have all this ‘stuff’ but the real question to ask now is, ‘does anybody need this stuff?’ or, more specifically, ‘do we and our clients need this stuff?’ For instance, hover boards do now exist and they’re great: so, couldn’t we equip all of our line engineers with them to get around airports more quickly and efficiently? OK, perhaps that isn’t a very good idea: that’s why some people are tasked to try and make sense of the many excellent ideas that are around; to consider what might be useful and what could deliver a return on any investment made in it.
Perhaps it will help to consider a real life example to illustrate what might really be important for our purposes and where we are today with technology. It comes from the background and experience of the world of running from which there are two scenarios to share that illustrate the real complexity that we all encounter from time to time and one very good way to handle it.
The risk of information overload and the tyranny of choice
A running equipment shop has all the potential to be the retail experience from hell; it’s a dazzling world of different shoes with different types of cushioning, different support, different grip… there are so many choices that it’s like Starbucks but even more complicated. Also, if you’re a technology geek, there is a stack of apps to help you work out how fast you’re running, how far you are from your optimal weight, how much further you have to run before you can eat that Danish for breakfast… a plethora of information. Apple’s Health Kit software even allows you to acquire, integrate and track more parameters from wearables and connected devices to help medical professionals diagnose or predict conditions or ailments. We are surrounded by the elements of a very sophisticated world with loads of choice and loads of complexity usually manifesting itself as an overload of information; potentially a really complicated world. However, in reality, when it comes to using the retail experience and the app ecosystem they can easily be marshaled to meet your exact requirements.
If the shoe retailer is of the traditional kind with a good knowledge of his products and the uses to which they’ll be applied, it will make your choice easier and better informed thanks to the combination of skills (the retailer) and integration (the store’s ability to bring many vendor’s products to bear). The same applies with the app ecosystem that, in reality, is a delight because everything is aligned with seamless and magical integration.
We can create a similar scenario in our world of aircraft maintenance. It all boils down to two things: we rely on highly trained individuals; we also rely on magical and seamless integration not only between our technologies but also within our virtual network… and, properly executed, the outcome is fantastic. So, let’s have a look at some common themes that we see every day with our customers and some of the challenges that they can come across.
Skills versus automation or skills leveraging automation?
It is not exclusive to aerospace to face the challenge of a skills gap. Like many industries, we are struggling to attract and retain the best possible people for our industry, and to train them so that they can be up to speed and at optimum proficiency and efficiency as quickly as possible. As a consequence some people look to automation to simplify the tasks we undertake and even to deskill the people we use to complete those tasks.
There have been a number of studies in the area of autonomy, including driverless cars, which are one thing; but the idea of a pilotless airplane is something about which we are probably more nervous. Pilotless drones exist today, but we’re a long way from being culturally prepared to use the same technology to carry passengers. In a similar vein, while we might not totally foresee the idea of removing the people from the line station or taking people away from maintenance activities, we might, perhaps, consider the possibility of deploying those people in a different and more economic manner. There are already use cases today which don’t so much de-skill the work at the line station but are more about helping the better skilled people to work sensibly; allowing them to take advantage of things like drones for inspection or use augmented reality to help with the deskilling of some tasks. All of that poses some interesting challenges from the training point of view. What we are looking to do is to squeeze as much out of our resources as we can while bearing in mind that skilled people are a finite resource.
Notwithstanding any of that, there is a training challenge: how do we engage engineering trainees with training content that is so different from the media and learning curriculums that they have become accustomed to in recent years. In the media world there is a phenomenon known as ‘the Buzzfeed-ification of content’. This is where news and entertainment content is divided into bite-size, easily digested viral chunks. It is ever more common to see top ten lists in serious media in order to compete for attention with the next generation media outlets that consumers are turning to for their updates. Training content is heading in the same direction. How long will it be before we see legacy type-training curriculums re-platformed into a top-ten list of things line engineers say about base maintenance guys? It won’t be quite like that, of course, but it might be content in that style, which is very concise, compact and informal in presentation. We’re already seeing our customers demanding that sort of treatment for content so that it can be used in a ‘bite-size’ form.
Walls don’t help with integration or big data
On the integration side of things, the marriage of data and networks can be complex. However, technology is no longer a barrier in terms of allowing virtual and physical networks from talking to each other. Nevertheless, the thing that really frustrates as an industry is that we seem intent on putting virtual firewalls or barriers in place, which prevent us from making best use of these integrated systems. We should be enjoying a ‘magical and seamless’ integration between systems and stakeholders and we shouldn’t be prepared to accept anything less than that; both in terms of systems and stakeholder integration. This is why we have industry data exchange standards and where we deviate from these standards, and when we put firewalls in place, we prevent technology from doing what it’s designed to do.
Now, what about big data? It’s one of those buzzwords that people often incorrectly use when they’ve put a couple of systems together and think that they now have ‘big data’. However, in order really to embrace the notion of big data requires that this integration is not just between proprietary systems but it requires a wider network of information and systems. Big data is about joining many data sources together and using decision support systems, business intelligences and data science to extract meaningful conclusions from an aggregation of data and content sources. It requires not just an aggregation of operator and OEM data, but the inclusion of external and consumer data sources such as economic, geographic and meteorological data. To do so requires a element of openness, the desire and ability to share data and most of all, the removal of virtual firewalls and barriers from the networks of all stakeholders involved.
Mobility and wearable technology
One other issue currently at the forefront of aviation IT minds is mobility. But mobility today has moved on from people struggling to build a business case based on a single use case to much more enterprise-wide initiatives, embracing the whole notion of taking advantage of paperless maintenance. For that to work, everybody really needs to embrace the idea that mobility is about getting the right information to the right people at the right time. All the questions about ‘which platform’, ‘which content’, ‘which device’ no longer really matter; as a vendor, a user or an IT provider, you need to be prepared to deliver whatever content users need to whichever platform that they want to use it on and on any device; whether that be laptops, tablets, phones or wearables.
And talking about wearables, while they might not yet have been the big hit that some predicted them to be, there are some interesting use cases such as Virgin Atlantic announcing that they would start testing out smart glasses. Also, the Apple Watch is on the market and while we probably won’t be putting them on engineers any time soon, firms like Ramco have been conducting trials with wrist wearables. However, the less attractive thing about those devices is their limited screen size, which would require businesses to redevelop their content or user interfaces in order for them to be able to be used with those very small devices.
What might be potentially more interesting is the next generation of head wearables offering totally immersive options for communication which could lead to a further leap in user experience and user interface. But, whichever form factor we are considering, to take advantage of them we need to be able to take advantage of those same virtual and physical networks already referred to above.
New stuff needs new thinking to deliver real value
What all of this (above) amounts to is that we have plenty of new stuff – new technology, new applications, etc. – there’s no shortage of toys, applications or software to choose from. That creates a problem for some of us inasmuch as we have to be able to go out and evaluate what these things can do, how that can be of benefit or use to our customers and then we have to put together a proposal and actual deliverable that takes account of all that.
There’s also no shortage of consultants, people who talk about the various challenges created by all of this stuff and how it works together (or not, as the case may be). While it’s true that each idea or device works individually in isolation, we need networks in order for it to work for us where we need it. Not just physical networks, we need networks of applications and hardware that actually talk to each other, from the aircraft right down to the shop floor. And there are other networks that we haven’t covered in detail such as the processes and procedures that drive the people in our organizations and the things they do, like moving an aircraft into the maintenance hangar and moving the right people and materials to meet it.
The network is more than a physical or a virtual element, it really is the sum total of how businesses operate. The challenge arising from all this is to drive us towards integration through standards that help us do our jobs and to devise a single network for our business from front to back. The problem is building that commitment within management, starting at the highest levels, then building a seamless integration across the enterprise: getting everybody involved can be a daunting task; that’s the real challenge.
Stability from technology, business challenge and culture change
So, when we look at how we go about this, it can be likened to getting the legs on a stool to make it stable. The first leg of this stool is the technical challenge which has been largely resolved with the applications, software and hardware available to us today. These have been around for quite a few years and there is a lot of choice.
The second leg of our stool is the business challenge and this is actually tougher to overcome. It’s where we have to be able to sell management on the specific approach that is needed to facilitate better inter- and intra-organizational integration and to demonstrate a return on investment. The 20/80 rule from the top of the article applies here with 20% of effort taken up developing the proposal and 80% taken up convincing the customer (or management) that this is the correct approach for them. The advantage that can be achieved through this process is that you get to know each other and can forge new business relationships based on dealing with a common challenge. And common challenges may extend outside of your organization’s walls, even to partner and competitor organizations. Creating seamless integration of knowledge and process may even lead to the phenomenon known as ‘co-opertition’, being able to justify collaborating with a competitor in order to ultimately serve the customer’s need.
The third leg on the stool is the cultural challenge. It’s not just a case of convincing management, it’s convincing everybody else in the enterprise not only that they need to be involved but also that it will be in their interest to be involved in the change process. This is the big challenge of change management; to get people to move away from practices that are familiar and comfortable, even if they are fundamentally flawed. But as technologies continue to make new models of interaction possible, there is a challenge not only to get people to recognize the possibility of change, but also to achieve that in a way that will supports the long-term success of the business.
Data that is managed is data that can be used
It might sound like a recursive cliché but it is nonetheless true that, ‘in order to work together we all need to work together’. It means that we have to have the technology to work together, the processes to work together and the will to work together. As we create these next generation tools to facilitate a magical and seamless integration across functional groups and to coordinate the technology, the business, and culture actors, change will happen. We will find – albeit gradually – that someday soon, instead of trying to drink from the fire hose, we’ll be able to direct every piece of that data to the places and people where it can be most usefully applied in achieving the business’s objectives.
Contributor’s Details
Paul Saunders
Paul is a technology specialist who has been working in aviation IT since 1998 with expertise in software design and mobility, having worked on apps used by pilots and engineers. In the adoption of emerging technology in aerospace, particularly mobility, Paul is a visionary and geek. He joined the TechSight/X team in 2013 where he serves as a global product manager spearheading flight operations, engineering services and mobile solutions.
Flatirons Solutions
Flatirons provides consulting, technology, and outsourcing for content lifecycle management (CLM). For more than 20 years, Flatirons has served global Fortune 1000 customers in aerospace, automotive, electronics, financial services, government, healthcare, and publishing. The business’s customer engagements help organizations efficiently deliver the right information, at the right time, to the right people by leveraging structured content and digital media – Turning Content into Knowledge®.
John L. Knolla
John Knolla has 20 years Technical and Management experience at companies such as Hawker-Beechcraft Corporation, Eclipse Aviation, Dassault FalconJet, ITT, and BAE Systems. He holds a Commercial Pilot’s License and has served on ATA working groups and the FAA/industry panel determining the certification, airworthiness and operational use of EFBs. John is a thought leader on the potential that modern standards, technology and applications promise to assist OEMs, Tier 1 and 2 Suppliers and Operators to get the most out of new and legacy platforms.
LMI Aerospace
LMI Aerospace, Inc. is a leading supplier of structural assemblies, kits and components, and a provider of design engineering services to the commercial, business and regional, and defense aerospace markets. LMI fabricates, machines, finishes, kits, and assembles machined and formed close tolerance aluminum, specialty alloy, and composite components. LMI also provides engineering and program management services, supporting aircraft product lifecycles from design to fleet support via complete turnkey engineering solutions.
Comments (0)
There are currently no comments about this article.
To post a comment, please login or subscribe.