Articles
Name | Author | |
---|---|---|
Case Study: Avion Express path to the Paperless Cockpit | Olegs Krisovatijs, Vice President Production, AVION EXPRESS | View article |
Documentation from author to crew in two steps | Dominik Weber, Team Leader Flight Operations Support, Lufthansa CityLine | View article |
Case Study: Driving fuel efficiency at Citilink | Arief Rachman, Manager Flight Dispatch, Citilink | View article |
Case Study: Driving fuel efficiency at Citilink
Author: Arief Rachman, Manager Flight Dispatch, Citilink
Subscribe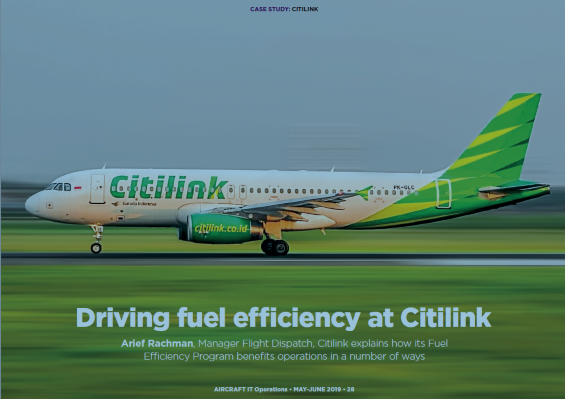
Driving fuel efficiency at Citilink
Arief Rachman, Manager Flight Dispatch, Citilink explains how its Fuel Efficiency Program benefits operations in a number of ways
In this article I want to share with readers what Citilink has achieved with its fuel efficiency program. First, though, it will be useful to explain a little about the airline. Citilink is a low cost carrier in Indonesia operating a fleet of 50 Airbus A320 aircraft. We are particularly proud of the awards that the airline has gained including a ‘Best Transportation Safety Management Award’ in 2017 from the Indonesian Ministry of Air Transportation; a four star rating from Skytrax as ‘Best Low Cost Airline in Asia’; and ‘Best Low Cost Carrier in Asia‘ from Trip Advisor. Citilink is also the airline with the best on-time record in Indonesia and the second best for on-time performance in Asia. Our scheduled route flight network (figure 1) focuses very strongly on the domestic market in Indonesia.
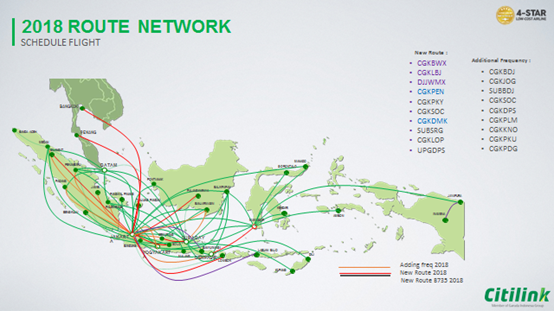
Figure 1
As a result, most of Citilink’s scheduled flights are two to three hours but we also operate charter flights to China, Japan, Malaysia, UAE and within Indonesia (figure 2).
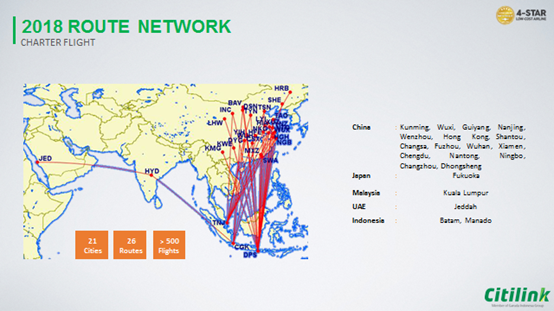
Figure 2
As far as cost per available seat kilometer (CASK) goes, Citilink is number two in Asia, a very important statistic for me as my job is to manage costs.
When looking at our fuel management program, we have made a number of assumptions including that our fleet of 50 A320s completes 100,800 sectors each year with 180,000 flying hours each year. We also assume that every 100 liters of fuel burned produces 233kg of CO2, 219g of CH4 and 23g of NOX.
In sharing how we have managed to achieve our fuel efficiency targets in Citilink, I’m aware that readers will already know how to be efficient but might well face the same problem that we faced in Citilink: how to implement efficiency initiatives in the daily operation of the airline and across the different areas in the business. We have approached that challenge by focusing on how cost and efficiency can be driven across four divisions: Ground Operations, Maintenance, Flight Operations and Finance. (figure 3)
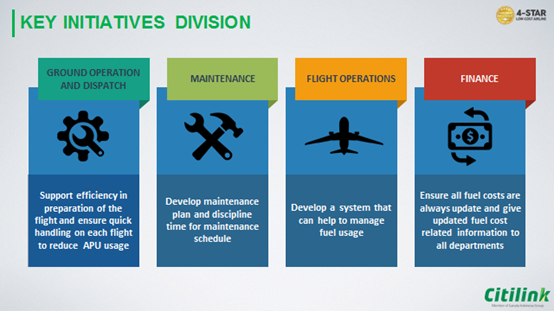
Figure 3
Ground Operations
This division focuses on supporting efficiency in the preparations for the flight, ensuring quick handling for each flight to reduce APU usage. We have created training, procedures and policies recorded in the Operations Manual and have pushed the personnel in the division to optimize efficiency.
Maintenance
We have developed a maintenance plan and worked to improve the time discipline for the maintenance schedule. Also we minimize the amount of fuel in the tank during maintenance.
Flight Operations
As readers know, with flight operations it is the pilot who is best placed to do more to improve efficiency but sometimes they don’t do that from concerns about safety and other issues. That is a challenge: to talk with pilots about their perceived barriers to efficiency.
Finance
Ensure that everybody and all departments who need them are supplied with up-to-date fuel costs information.
MAKING THE EFFICIENCY PROGRAM COME TRUE
Let’s now look at the steps that we have identified and taken to be able to realize the efficiencies we want.
Ground Operation and Dispatch – preparation
The first consideration for fuel efficiency is the accuracy and properness of the computerized flight plan. This would include using the most efficient routes. At Citilink, we only give the pilot that one most efficient route in the database: so, how have we managed that? In my experience, Dispatch won’t have sufficient confidence to discuss the efficiency of various route choices with the pilot so we remove any choice of routes. Each dispatcher can decide whether that route makes sense or not and can make changes, if need be, but have to record the reasons for any changes they make. Also, the head of the department should monitor any deviations each day and should be coaching their staff when there are deviations from the SOP (Standard Operating Procedures).
Our next consideration is to use the most optimum flight level, which is usually generated by the system, and then we also ensure the accuracy of the Cost Index. We try to recalculate the Cost Index weekly using big data with analytics about the weather, levels of traffic and fuel charges – in Indonesia, fuel charges are changed every week according to the $US exchange rate. This is not led by the fuel efficiency project manager but by the appropriate department heads who work with their staff to make it happen.
We also endeavor to achieve an accurate estimate of zero fuel weight (ZFW) while computing the flight plan. As readers will know, deviation from the zero fuel weight can add 35 kg of fuel use per hour of flight for every 1 ton of extra weight. We use big data analytics and the characteristics of Citilink’s routes which has achieved a big saving of fuel.
One big fuel saver is fuel tankerage policy which is used to optimize the difference of fuel price between Citilink Indonesia’s stations. The calculation is made every two weeks with the updated fuel price and already taken with the factor from the fuel burn per extra weight (1 ton fuel ‘cost’ of 35 kg burn of fuel). Every airline has a fuel tankerage policy but we know that the tankerage policy is opposite to the company’s commercial policy because we always have to take into account the needs of cargo department as to the load. One thing to implement about fuel tankerage is we have a base calculation for the company plus we incorporate understanding about our route characteristics. Each place we fly to is different with different characteristics for passengers and different cargo revenues. So for every route we can decrease or increase the weighting for the fuel tankerage. On our busiest routes we are confident to increase the fuel tankerage but on the routes to smaller cities, we are not confident to increase fuel tankerage.
Flight Operation – Engine Start and Taxi
Actions taken to improve fuel efficiency in this section are actions that the pilot can take but the company can develop a policy and how to make it happen, and we can share experience.
Citilink has a policy of single engine taxi but not for all flights and it can cause other problems such as not being good for the engines and sometimes increasing the noise levels for passengers. So we implement this policy if the estimated take-off weight is less than 65,000kg and if the aircraft is going to China. In fact, one minute of single engine taxi out per sector saves 430,000 liters of fuel per annum. We have identified five areas on which Flight Operations should focus in the SOPs. One is limiting weight, then limiting thrust, checklists, engine start sequence and stabilization times. This is our concern and we have advice from the pilot management especially as regards the flight standard; also we collaborate with the flight operations department to create the SOP
Flight Operation – Take off
Looking now at ‘Flex Thrust’ Normal Operating Procedure; Citilink does not have a procedure for reduced take-off but only for flexible take off. Our system can compute the most accurate flexible thrust take off. We have built the system to do this because, when we checked in line operations, we saw that pilots sometimes forgot to make the necessary corrections. Flexible thrust aims to meet several aims. It reduces noise, it reduces overall sector fuel consumption, it reduces engine wear and maintenance costs. Currently 85% of A320 family departures are ‘Flex Thrust’.
The next contributor to fuel efficiency is to depart in direction of flight. We communicated with the other parties like the ATC (Air Traffic Control) controller to try to get a direct route for departure and tried to get a new SID (Standard Instrument Departure). The ATC also likes this if we can give them information to reduce traffic levels in the sky. So there is the opportunity to give the information and to advise ATC how to reduce air traffic during approach or landing. These are important bearing in mind that airborne fuel flow is six times more than for ground idle so that the fuel burned in 18 minutes of taxi will be equivalent to only three minutes when airborne.
Next, we use ‘pack off – take off’. This is more extreme for me because, to implement this, I removed the ‘pack on’ connection on the performance chart leaving only ‘pack off – take off’ with no option for ‘pack on’.
And, like many readers, no doubt, we also have a policy to minimize APU use. The APU on the Airbus A320 uses 110kg of fuel per hour. At Citilink we aim for 30 minutes ground time so we were using almost 65kg of fuel for the APU on each sector. Now, we stop the APU ten minutes before the scheduled departure time for morning flights when the weather is still cool so both the crew and passengers will still be comfortable. However, reducing APU use by just two minutes per sector saves 780,000 liters of fuel annually. Also, we delay starting the APU when arriving until when the aircraft reaches the parking stand. The APU uses six times as much fuel as mobile ground support equipment so, on some routes, we replace the APU with ground support equipment but not on all routes because there is limited ground support in some stations.
Flight Operation – Climb
Citilink will reduce the climb profile. A default has been set-up in the MCDU (Maintenance Control and Display Unit) to be 800 and 1,000 and 1,500 feet. Take off fuel burn is three times that during taxi (see above). Climb profile has been tailored to the direction of flight for turns limited by altitude due to noise abatement requirements. We use V2 + 10 to 3,000 ft. AGL (above ground level) for altitude restricted SIDs when the departure runway is more than 90° from the direction of flight. Used on one third of departures, this saves 3.2m liters of fuel each year. A challenge in Indonesia is that airports are not always as they are in other countries – there are often mountains in the proximity. So we decided on the new departure procedure that Flight Operations Control (FOC) uses and we collaborated with the ATC controllers to get what we wanted.
Flight Operations – Approach
We also got what we wanted regarding SID or STAR (Standard Terminal Arrival Route). And we collaborated with other airlines to make it happen so that, at some airports, where they didn’t use RNAV (Area Navigation) arrivals, we suggested they change to RNAV arrivals, reducing IFR arrival distance by 4 miles and saving 50 liters of fuel.
We use decelerated approaches as normal SOP for the Airbus A320 but maintain the speed profile of the aircraft using flap/gear selection according to altitudes which, again used on one thirds of arrivals, saves 4.5 million liters of fuel each year.
Flight Operations – Landing
We have implemented reduced flap landing as normal SOP if the runway length is more than 2,500m, this is mandatory. It delivers quieter approaches and, if used on one third of landings, saves 3m liters of fuel each year. Idle reverse is normal SOP for our pilots thus avoiding using reverse thrust if we’re landing on a runway longer than 2,500m. This policy means quieter landings and reduced carbon brake wear as well as reduced engine wear and maintenance costs and, as before, if used on one third of landings saves 1.2m liters of fuel per year.
Notwithstanding all of the above, we still will rely heavily for our fuel efficiency strategy on maintenance and reducing the weight of the aircraft. We have identified a number of changes that will help to achieve weight reduction. First, the removal of one oven because we’re a low cost carrier so we don’t need two ovens and can save 20kg of weight by that removal or save 40kg by removing both ovens. We’ve also removed the life rafts which are only for ETOPS (Extended Twin Engine Operations) and have reduced the quantity of water on board during a flight according to the flight duration; if it’s less than one hour, we halve the quantity of water carried and on a one to two hour flight, we only carry half the quantity of water for each lavatory.
The achievement
Up to September 2018, we were just ahead of our fuel saving target which is a saving of 14,000 tons of fuel for the year and, by September, we had reached 12,700 tons with three months still to go.
KEY STRATEGIES
These are the five strategies (figure 4) that we have pursued in order to implement our fuel management program and realize our fuel efficiency targets.
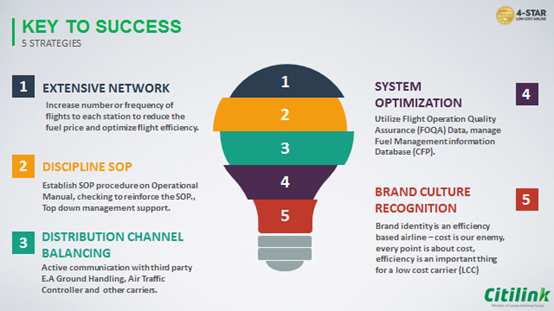
Figure 4
Extensive network
To increase the number and frequency of flights to each station to reduce the fuel price and optimize the flight efficiency.
Discipline SOP
We make sure that all personnel exercise the discipline to work according to the SOP. This is the responsibility of each department and division not the project manager. If any problem arises, the department can call the staff for training or coaching. Everybody should understand that cost is our enemy.
Distribution channel balancing
We maintain good and active communications with third parties: ground handling, Air Traffic Control and other carriers.
System optimized
In Citilink, staff income is in two parts, one is salary and one is based on performance. So we have established KPIs for employees, including pilots, which includes elements from the efficiency program and safety related measures. We also utilize Flight Operations Quality Assurance (FOQA) data and manage the fuel management information database.
Brand Culture recognition
Our brand identity is as an efficiency-based airline
THE SKYBREATHE SYSTEM
I’ll close by explaining why we decided we needed to have the SkyBreathe system by OpenAirlines. We had already done the things listed above but we still had a problem about how to measure the achievement of each individual member of staff and department and engage them which is something that SkyBreathe can deliver, i.e. we can see the achievements of each individual in the business and each department. You cannot improve what you don’t measure. Plus the system also helps to engage with flight dispatch and pilots as to where they can help to reduce fuel consumption, and this has the potential to drastically improve best practice application rates and increase savings.
Contributor’s Details
Arief Rachman
Arief joined Citilink Indonesia in 2008 as a flight operation specialist. His main role was to set up and develop Ops Control. From 2013 – 2018 he moved to the new position of Manager Flight Dispatch and was also involved with the project team charged with driving cost efficiency, with the target to develop, initiate and enhance an efficiency program and ensure all employees have the knowledge, initiative and culture to drive cost effectiveness and efficiencies.
Citilink
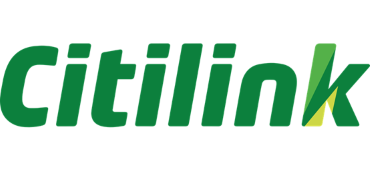
Established in 2001, Citilink is a low-cost airline based in Jakarta, Indonesia. The carrier is a subsidiary of Garuda Indonesia and was set up to operate shuttle services between Indonesian cities. The airline operates a fleet of 50 Airbus A320 aircraft.
OpenAirlines and SkyBreathe

OpenAirlines was founded in Toulouse, France, in 2006 to meet the needs of airlines to optimize their flight operations and reduce their costs. Leveraging a team of airline specialists and data scientists, it offers innovative software solutions. Capitalizing on its participation in the European Research Program, Clean Sky, from 2009 to 2014, the company developed SkyBreathe®, an innovative eco-flying solution to save fuel and reduce CO2 emissions.
Comments (0)
There are currently no comments about this article.
To post a comment, please login or subscribe.