Articles
Name | Author | |
---|---|---|
Fuel Efficiency Solutions | Wayne Beardsley, Consultant - Fuel Efficiency Solution, Rolls-Royce | View article |
Putting the customer first | Alexander Tatidis, Sales Representative/Assistant Sales Manager, Flygprestanda | View article |
Case Study: ETL: the move from paper – part 1 | Cameron Hood, CEO, NVable, Rob Woods, Head of Engineering, Air Arabia Maroc, and Dave Cooper, Line Maintenance Manager, British Airways Cityflyer | View article |
Column: the World according to IT and me.. Sturgeon’s Law | Paul Saunders, Solution Manager, Flatirons Solutions | View article |
Case Study: ETL: the move from paper – part 1
Author: Cameron Hood, CEO, NVable, Rob Woods, Head of Engineering, Air Arabia Maroc, and Dave Cooper, Line Maintenance Manager, British Airways Cityflyer
SubscribeETL: The move from paper – Part 1
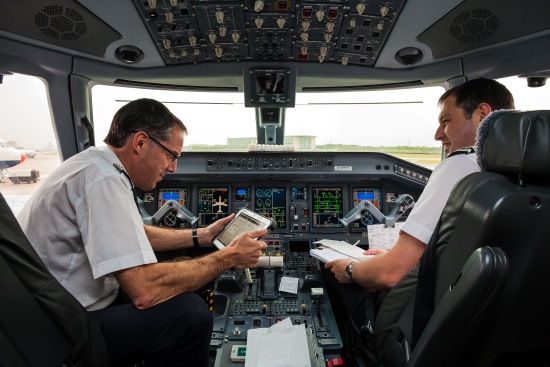
Standfirst Cameron Hood, CEO, NVable, Rob Woods, Head of Engineering, Air Arabia Maroc and Dave Cooper, Line Maintenance Manager, British Airways Cityflyer share their experience with digitizing the Aircraft Technical Log
WHAT IS AN AIRCRAFT TECHNICAL LOG?
The Basics
The process of recording technical findings and maintenance actions in a technical log (generally shortened to techlog) is part of the daily oversight of the aircraft. Although the format and content of the techlog varies between airline operators the role it performs is fundamentally the same. At a minimum:
- The status of the aircraft is recorded prior to each sector flown. This includes departure and arrival location and times; fuel uplift and levels; oil and hydraulic fluid levels; defect status; any de-icing that has been applied; plus, other regular line maintenance activities are usually recorded.
- The techlog remains with the aircraft. This means that engineers and flight crew are able to access the aircraft’s maintenance record regardless of where they join the aircraft and regardless of the ability to communicate with other teams (e.g. MAINTROL) or systems.
- A copy of the techlog record is left on the ground prior to take-off. This serves as a record of the state of the aircraft prior to each flight.
- The captain is responsible for signing off each techlog record and by doing so is accepting the status of the aircraft as fit for flying.
- The line engineers are responsible for signing off each maintenance activity that is recorded in the techlog. By doing so, they are confirming that any such activity has been completed to the correct standard, and as such is released for service.
- The aircraft is not allowed to take-off with open defects. Therefore, all defects must either be rectified or deferred (in accordance with strictly monitored processes) prior to take-off.
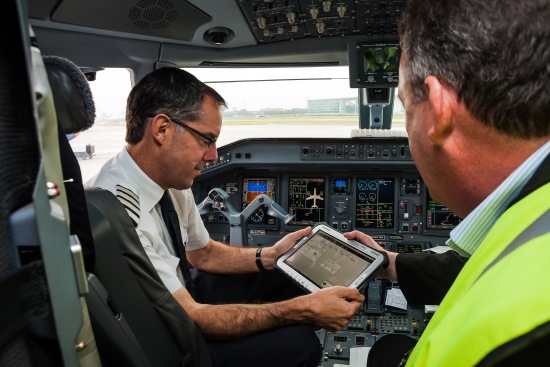
Current Process
The techlog is responsible for recording the primary technical and operational data for each flight and is therefore a key data feed for many airline functions. The normal process within an airline will use a carbonless multi-part pad which records multiple copies (on different colored sheets e.g. white, pink, yellow, green) to record a techlog entry. The pads are specially printed to reflect the techlog layout of the airline and will have a unique number printed on each ‘page’ to ensure that there are no gaps in the techlog records. For the majority of airlines, the techlog procedure is a variation of the following:
- Complete the relevant section of the techlog; engineers will fill in maintenance tasks and fluid checks; the captain / first officer will complete the details of departure and arrival, along with fuel, de-ice and the final sign-off prior to flight.
- Tear off the appropriate copy of the sector record and leave with the ground staff. A new page in the techlog is then used for the next sector.
- Ground staff will take their copy to local office.
- At the end of the day, scan and email (or fax) the copy to the back office function of the airline. At some point (generally with at least a day’s lag) the data from the scanned/faxed sector record is entered by hand into the airline maintenance system.
- With Multiple Engineering bases for larger fleets, all originals must also find their way back to the Head office for archiving.
The various copies of the techlog will also be taken and distributed throughout the airline. For example, finance may wish to perform fuel reconciliation while another department may use the data to report on emissions, and so on.
Who is Responsible?
The airline is responsible for ensuring the techlog is being recorded according to their procedures. The format of the techlog form is important; however, the focus of the Authority is procedural. It is the procedure itself that is certified by the local Aviation Authority and any changes need to be agreed with them. The importance of this cannot be exaggerated. As one UK Civil Aviation Authority representative put it, “If there is no techlog completed and left on the ground, there is no flight. It is as simple as that.”
WHAT IS AN ELECTRONIC TECHLOG?
A Digital Record
In simple terms, an Electronic Techlog (ETL) is a replacement for the paper process described above using a computer (whether that is a laptop, tablet or some type of in-built device on the cockpit). The difference is that the information written on the paper forms is recorded on the computer and this creates a digital record. An ETL has to satisfy all the same criteria as a paper techlog because it is performing the same function. So, for example, there must be a way to leave a copy of a sector record on the ground prior to take-off. However, it is useful to be clear in thinking of the ETL primarily as a replacement of the actual paper technical log itself rather than a substitute for the entire process. This must include the ability to appropriately ‘sign-off’ the techlog as well as recording approval numbers.
Why make that distinction? The Aviation Authority which oversees the airline’s AOC (Air Operating Certificate) will look to certify the aircraft technical log procedure. The fact that the airline uses a paper or electronic technical log is less relevant. The paper form itself is not certified by the aviation authority, but rather, approved for use in it. Similarly, an ETL will not be certified but can be approved for use. Just as a good paper form design will make it simple for an individual to complete a form, and will also guide them to use the underlying procedure, so does an ETL. An ETL can provide more support to the user than paper and this is one of the potential benefits. Being clear on this distinction helps to focus on what the ETL actually needs to do.
There are a few ETL solutions in the market and they have the following minimum functionality:
- Record the technical log data which is configured to a greater or lesser extent for the airline on a computer;
- Transmit the data from the computer to a server;
- Pass that data to the airline;
- Provide live visibility of the data.
The conversion from the paper process does introduce new problems and these considerations should be part of an airline’s assessment of where a particular solution is a good fit for their organization.
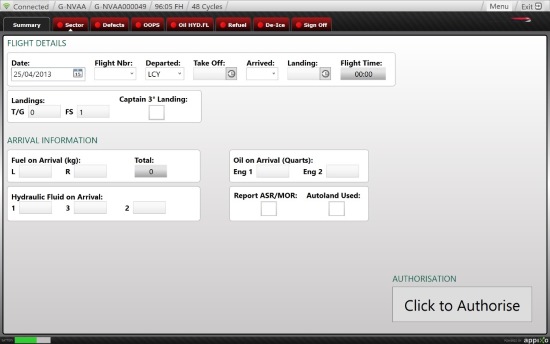
Potential Problems
New maintenance tasks
The ETL needs to be supported in operation and there are some additional tasks that should be considered. Unless the device is docked in the aircraft cockpit and charged, the devices (let us assume laptop or tablet PC) must be charged regularly. Depending on the hardware this may be a battery swap or a physical removal and charge. It may also be possible to charge such devices on the aircraft. The correct approach for an airline will depend on preference, aircraft type and even the view of the local Aviation Authority. There may also be a requirement to regularly swap storage devices such as SD cards depending upon the airlines procedures.
Coping with technology failure
With a paper process there is little that can actually go wrong. A pen may be lost or run out of ink, but crews are always prepared for such eventualities. The paper techlog pad may run low on paper, but that is a simple matter of monitoring and restocking. Electronic devices and the infrastructure to actually send and receive data create a few more challenges:
- Hardware Failure – the PC itself could fail. A line station is not an office environment. Paper techlogs are used in and around the aircraft, so ETLs need to be used similarly. This means more risk of dropping, water damage, dirt, oil, screen damage, etc.
- Hardware Loss / Theft – although the aircraft is a controlled environment the risk of loss or theft is real.
Software Crash – the software which is recording the technical log may run into a problem. The impact may be that the techlog cannot be recorded or, worse, the data it has already recorded becomes corrupt.- Cannot transmit data – if the ETL depends on either the availability of a network to send data (e.g. Wireless Network; Cellular Phone Network; Satellite Network, etc.) it may not be available in a particular location at a particular time. The reasons can be many and varied, but the absence of connectivity is a frequent problem. If this is the way that the ETL leaves ‘a copy on the ground’ prior to take-off then there is a problem.
All these challenges are potential failure modes but the fact they exist does not mean an ETL cannot deliver a good reliable service. It merely means that airlines should consider how an ETL solution defends against the problems and recovers from them if they do occur. Those companies that have faced these challenges through implementing ETL systems will no doubt have many stories to tell about the success, or otherwise, of various solutions, and what they consider to be the best approaches.
Handling Data
During normal operation the ETL data will generally be sent to the airline. The actual mechanism varies between ETL implementations but the end result is that the airline will receive a stream of data regularly. This potentially means opening firewalls, setting up FTP sites and managing the input of the data (either manually or automatically).
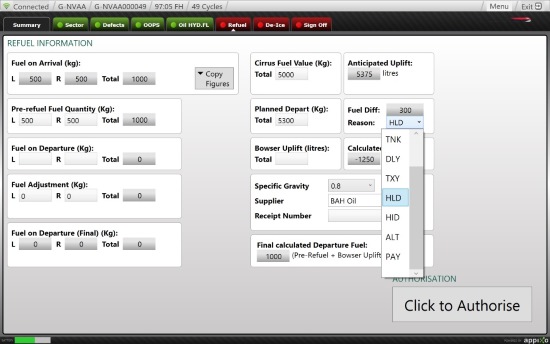
WHAT ARE THE BENEFITS OF AN ETL?
We will make a couple of basic assumptions that an ETL solution:
- Is able to reliability transmit the data collected as part of the techlog process back to some sort of data hub; and
- That data hub can be accessed via a website that allows people secure access to the data gathered on the ETL. This includes the sector, defects, defect actions, out of phase tasks, etc.
Real Time Visibility Across the Fleet
One of the key benefits is the ability to see an up-to-the-minute status of the whole fleet. This means that all the data collected in the techlog is available for various teams in the airline organization making it simpler to control and plan. Having access to the data is like being able to open up a window into the cockpit, at any time and from anywhere in the world.
- Maintenance Control Centre (MCC) – tracking deferred defects, hours/cycles and out of phase tasks becomes significantly simpler when the Maintrol team can see all the activities and expiry dates in real time. Managing AOG (aircraft on ground) recoveries is greatly aided and speeded up with live first hand data too.
- Third Party Maintenance – for any third parties involved in the maintenance of the aircraft, having the ability to see (and print off) the sectors they have worked on saves time. It also allows them to plan for receiving the aircraft at a remote station.
- Continued Airworthiness – from experience, we know that, particularly from the point of view of the post holder, the comfort of being to see the status of each aircraft and know that they are compliant is invaluable.
- Line Stations – having full visibility of the aircraft during the full day of operations allows for better anticipation and forward planning of the day or nights maintenance activity.
- Records Department – the records department is able to be autonomous, not relying on other departments such as the MCC to pass on information.
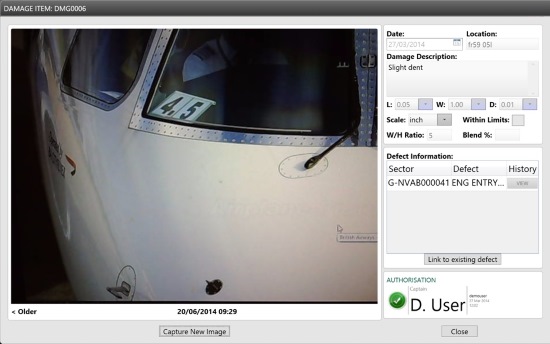
Reduced errors
Even a simple technical log will have around 100 data elements captured in each sector (the number will depend on the complexity of the aircraft and the data the airline wishes to record). With a commercial airline typically flying an average of four sectors a day and assuming 300 flying days a year, that means there are (conservatively) around 120,000 pieces of data recorded per aircraft per year in the techlog. That equates to over 2,400,000 for a fleet of 20 aircraft.
It is no surprise that a paper form introduces some errors when recording that data. Simple things like calculating flight times and fuel uplifts, even the quality of the hand writing can impact the accuracy of the data. Add the fact that the data is then manually typed into other systems and it should be no surprise that data errors creep in. There are also occasional problems with losing a sector record as it makes its way from a station to the data entry; resulting in a missing techlog sector. An ETL introduces the possibility of:
- Automating calculations;
- Applying basic validation rules;
- Applying more complex business rules.
These help to ensure that the data is accurate at the point of data capture. Some solutions may also integrate with a feed of data from the aircraft (for example, chocks on and off).
Automated Data Entry to Maintenance System
Closely associated with the data errors is the ability to automate data entry into the Maintenance system. The capability to transfer the digital sector record directly into the Maintenance system has many advantages, the primary one being that the data is very quickly available in the ‘system of record’. Despite this being a main driver for ETLs, it has been difficult to achieve, with only a few suppliers having a live data feed into a Maintenance system on an operational fleet.
Reduced time to complete techlog
Partly because of the automation and partly because an ETL should be simple to use, the time to review, transcribe and update the techlog is reduced. To a degree it depends on the selected solution, but there is evidence from some airlines that completing an ETL takes less time than the paper equivalent.
Simpler Line Maintenance Management
The data being easily available for all defects, defect actions and the equivalent for any out of phase tasks greatly simplifies the control of maintenance on the line. Some solutions have additional functionality to specifically plan and monitor line activities. Generally, since the techlog data is input into the maintenance system this becomes the source system for line maintenance planning. However, maintenance systems were not designed to manage line activities (their focus is on record control and hangar maintenance) and where there have been attempts to add such functionality it has often fallen short. This is primarily because:
- The feed of data from the line is not timely enough to be useful (i.e. a paper techlog); and;
- The underlying system is not designed for the more agile needs of line maintenance.
The result of introducing an ETL is the ability to plan activities on accurate, timely data.
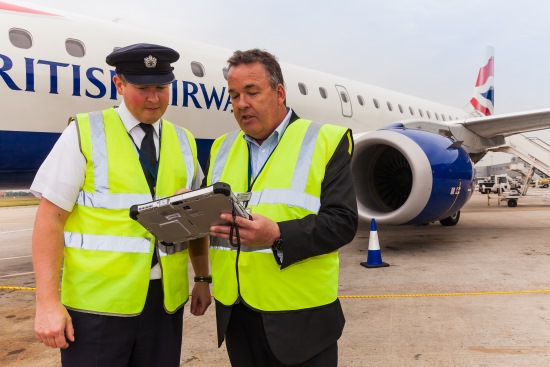
Alerting
As the data is passed from an ETL to the data hub there are opportunities for creating alerts. These can be categorized as simple and complex. For example:
- Simple Alert – send an email and SMS alert when a particular category of defect is raised, or when a defect is deferred.
- Complex Alert – send an email and SMS alert when oil consumption for an engine (calculated over a rolling 50 sectors) breaches a threshold (defined for that particular engine).
This type of functionality allows an airline to monitor their fleet in real time. Plans can be made to react to highlighted issues or prevent a problem developing, which is a step towards predictive maintenance.
Timely Data Reporting and Analytics
The data gathered in the ETL can provide insight into daily operations and go a long way to providing a foundation for weekly SLAs (service level agreements) and monthly reliability reports (other streams of data would be required to produce full reliability reports). The key difference between analytics driven from the maintenance system fed by a traditional techlog and one based on an ETL is timeliness. With an ETL in place either the ETL solution itself or the maintenance system can drive analytics from current data – this allows the various teams in the airline to be proactive. Some examples of analysis include but are by no means limited to:
- Defects;
- Repetitive/Recurring Defects;
- Defects by Aircraft; ATA Chapter; Station;
- Engineer report (all defects and defect actions involving an engineer);
- Recurring part replacement.
- Fuel;
- Fuel reconciliation;
- Burn by from and to station combination;
- Summary for emissions reporting.
- Oil and Hydraulic Fluid;
- Engine monitoring (oil consumption patterns).
- Personnel reports;
- An ETL will often be able to identify users that have completed certain tasks (engineering and flight).
- Dashboards;
- Operations room monitoring;
- Executive overviews.
Efficiency
The key efficiency that most people think of when considering an ETL is eliminating manual data entry. Whilst this is an important efficiency gain it is by no means the only one.
- Line engineers no longer need to send out paper techlogs (using whichever mechanism). Although this would generally be a task kept to the end of the day, it is an extra hour or two of effort in which a skilled line engineer is doing clerical work. The impact is not that hour alone but the interruption to other work.
- In the normal paper techlog process updating Maintrol on an issue is mainly via mobile phone and email. This is purely because Maintrol will not have visibility of the activity recorded on the techlog. Once visibility is provided, Maintrol can focus their efforts in ensuring the day is going to plan. The line engineer will still be on the phone to Maintrol – but discussing something that needs focus, not merely reporting back.
- The addition of line maintenance planning (functionality offered by some ETL solutions) reduces the need for Line Engineers to go back and forth to the Line Office, printing task instructions etc. The time this takes can be considerable, depending on the airport, the gate location and the office location. The functionality additionally simplifies the planning task for Maintrol.
- Capacity Planning – Daily defect meetings and shift handovers that ensure optimized work load capacity planning become cognitive, efficient and informed.
Cost Reduction
A paper techlog process is not cost free. Carbonless multipart pads with an airline’s techlog form printed along with unique numbering is not cheap. There are also, generally, costs associated with sending a techlog page back for processing. It is true that there are new costs associated with running an ETL, however a thorough analysis demonstrates an overall benefit when the hard costs are taken into account, along with the efficiency improvements and the benefits from the improved visibility of the aircraft status which makes it possible to proactively manage the daily activities.
At first pass the business case for an ETL can appear weak. This is often because departments within the airline look at it in isolation. When the impact is analyzed across the airline and the benefits analyzed – you can be assured that the business case adds up.
Part 2 of this article in the next issue of Aircraft IT, will look at the process of electronic techlog implementation with some practical advice gleaned from our own experience of introducing electronic techlog solutions into working airlines.
Contributor’s Details
Cameron Hood
Cameron Hood led the technology team involved in the very first implementations of electronic techlogs through CoreData which was subsequently acquired by Data Systems and Solutions (at the time, a joint venture between SAIC and Rolls-Royce, which then became Optimised Systems and Solutions and is now known as Controls and Data Services). Cameron is the founder and owner of NVable, who have developed a new platform that offers electronic techlog and more.
Rob Woods
Rob Woods has been involved in the implementation of electronic log book solutions supplied by Data Systems and Solutions at Mytravel and, subsequently, Thomas Cook. He has experience of being involved at the leading edge of the introduction of new technology and has the battle scars to prove it which well qualifies him to understand the introduction in his position as Head of Engineering at Air Arabia Maroc.
Dave Cooper
Dave Cooper has been involved in the introduction of the Electronic Techlog (eTechlog) across a fleet (initially with the Data Systems and Solutions version) and a transition to the new eTechlog from NVable. He has experience of the challenges in managing the changes which has given him particular insight into what is important in a solution for his position as Line Maintenance Manager at British Airways Cityflyer.
Air Arabia Maroc
Set up as a joint venture between Moroccan investors and Air Arabia, Air Arabia Maroc is a low-cost airline operating out of Mohammed V International Airport, Casablanca to mainly European destinations. The current fleet consists of four Airbus A320-200 aircraft.
British Airways CityFlyer
BA CityFlyer, British Airways’ wholly owned subsidiary, operates a fleet of Embraer 170 and 190 aircraft from London City airport and London Stanstead airport to UK domestic and European destinations.
NVable
Clients have been placing their trust in NVable to help find and deliver real business solutions using information technology (IT) for over 10 years. The portfolio spans consultancy and software services with end-to-end solutions that work based on the company’s CoNVerge platform designed to integrate established databases and new solutions such as eTechlog.
Comments (0)
There are currently no comments about this article.
To post a comment, please login or subscribe.