Articles
Name | Author |
---|
Case Study: Finnair – Introducing an EFB-based operational efficiency tool to the Airbus A350 fleet
Author: Henri Lönn, Development & Support Manager, Finnair
SubscribeFinnair – Introducing an EFB-based operational efficiency tool to the Airbus A350 fleet
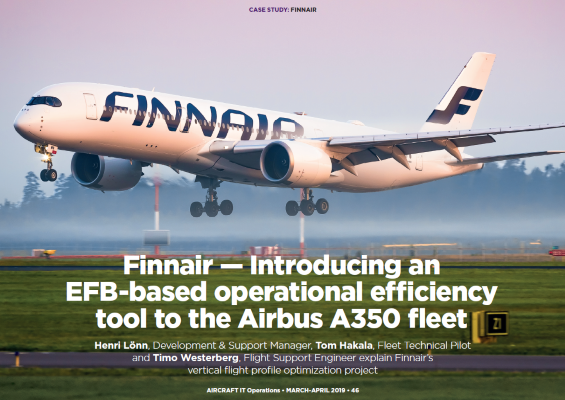
Henri Lönn, Development & Support Manager and Tom Hakala, Fleet Technical Pilot explain Finnair’s vertical flight profile optimization project
In this article we will share our experience of evaluating, selecting and implementing, on Finnair’s A350 fleet, an EFB software solution which uses vertical flight profile optimization to determine the most cost-efficient altitudes and speeds from take-off to landing. But before we jump in, let’s take a quick look at Finnair, the company, to understand the business context in which our software implementation project was completed.
FINNAIR
Finnish flag carrier Finnair celebrated its 95th anniversary in 2018, making it one of the oldest airlines in Europe and the fifth oldest airline in the world still operating in its original form. In 2015, Finnair was the first operator in Europe (and third in the world) to take delivery of an Airbus A350 and has since added another 12 wide body aircraft to its fleet, with another seven to be delivered within the next three years. Finnair’s A350-900s are currently in use on routes between Helsinki and Bangkok, Beijing, Hong Kong, London, Shanghai, Seoul, Singapore and Tokyo. Finnair’s fleet also includes A319/A320, A321 and A330 aircraft.
In addition, Finnair has a joint Air Operator Certificate with regional airline N°RRA, which flies Finnair’s Embraer 190 and ATR-72 aircraft to a network of domestic and European destinations.
Key figures for 2017 included:
- Revenue €2,568m;
- Available passenger kilometers (ASK) 36,914 million;
- Revenue passenger kilometers (RPK) 30,750 million;
- Operational EBIT (Earnings Before Interest and Taxes) €211m;
- Employees 5,918.
PROJECT BACKGROUND
Finnair is a successfully growing business with a long history of fuel efficiency innovation. In addition to modernizing its fleet with efficient A350 aircraft, which use approximately 20 per cent less fuel than their predecessors, Finnair strives to continuously improve fuel efficiency by optimizing its operational practices, e.g. through engine-out taxiing, reduced discretionary fuel uplift and similar measures. Our fuel efficiency project led us to identify in-flight vertical profile optimization as a promising area, which had been untapped to date because of technical limitations of the flight planning and flight management systems (FMS).
Initially, we sought a solution which could be implemented on all Finnair aircraft, but it soon become apparent that the more sophisticated EFB tools on the market require a connection to aircraft avionics in order to provide optimum operational efficiency. More precisely, they require an Aircraft Interface Device (AID) which allows the EFB to read flight data such as speed, wind, temperature and weight from the avionics buses. Our new A350s were the only aircraft in our fleet with line-fit AID hardware and were also earmarked for pilot in-flight connectivity, so it made sense to focus our efforts on that portion of the fleet.
With limited AID experience, we seized on the flight profile optimization project to also explore the possibilities of the hardware and the data it makes available. It allows us to retrieve data automatically from AID in real time to reduce pilot workload and build more automated processes within EFB applications.
Of course, implementing new EFB software while getting to grips with the AID hardware and testing the cockpit connectivity all at the same time was demanding, but it also made clear to us that, as an industry, we are on the cusp of some major changes. It’s hard for anyone to predict the exact impact of these technological advances and what the airline world will look like in five or ten years, but our implementation shows that aircraft connectivity has enormous potential when leveraged with the right tools.
PROJECT PHASES
Finding the right solution
We started our project with a comprehensive market study of suitable vendors and software solutions, which ultimately resulted in a shortlist of five candidates. The study also revealed that commercial off-the-shelf products for in-flight profile optimization are not broadly available, with many start-up companies and prototype solutions requiring a corporate partner to develop the product to maturity. So, we made product maturity an important criterion for our selection process, together with software platform requirements (at that time Finnair was a Windows-only company) and usability aspects. We awarded bonus points for useful additional features such as turbulence avoidance as well as for the ability of the software to adapt to new or changing requirements.
Making the decision
In our evaluation of the five candidates based on these criteria, the Pacelab Flight Profile Optimizer (FPO) software by Berlin-based TXT company PACE came up tops. Pacelab FPO has been commercially available for some years and was ready for operational trials.
We had fifteen Finnair A350 pilots trained to use the software and conduct tests and analyses in approximately one hundred sectors across our route network for two months. Then we used flight data and pilot feedback to assess the fuel and cost savings potential and the overall usability of the software. Due to considerable noise in the data, the former was not as straightforward as we had hoped. For a meaningful comparison of the routes flown with and without Pacelab FPO in the same period of the year, for example, we had to normalize a wide range of variables including wind, cost indices and weight. We achieved this through a sophisticated multivariate analysis with IBM’s statistics tool SPSS and were able to prove accumulated savings, even though the savings achieved on individual flights can vary considerably.
We built our business case on the demonstrated fuel and time savings, also taking into account the resources saved in the OCC if they no longer needed to support flight crews with in-flight calculations, plus ascribing monetary value to the improvements to flight safety, customer experience and in-flight sales provided by Pacelab FPO’s turbulence forecast module.
BEFORE AND AFTER
Before implementing the new software, our flight profile optimization was performed during flight planning on the ground by the flight dispatch in OCC (Figure 1, dark blue content). Flight plans were calculated a few hours ahead of departure based on the weather forecasted at the time and an estimation of aircraft weight. This meant of course that changing weather conditions and/or pilots’ extra fuel decisions would not be reflected in the original flight plan, although Finnair had a procedure of updating the profiles from OCC roughly mid-route on long-haul flights based on weight updates provided by the pilots. However, this procedure did not address a functional limitation inherent in our flight planning system, which cannot introduce flight level changes in-between waypoints. Particularly on flights with longer segments, this means missing out on the additional savings potential offered by optimized step climb and step descents.
With the new software installed, a more sophisticated optimization can be performed on the flight deck (figure 1, light green content). Pacelab FPO loads the operational flight plan (OFP) with the initial optimized vertical flight profile and speeds but leverages the availability of real-time data such as the actual aircraft weight to continuously re-calculate the most cost-efficient altitudes and speeds with great accuracy. The optimization is always applied to the entire remaining route, trading off operational efficiency
Figure 1
TECHNICAL IMPLEMENTATION
As noted above, getting the software up and running on all EFBs took us longer than expected because we kept learning new things about the A350 systems and the AID hardware. The implementation phase started in January 2018 and thanks to the excellent cooperation of the small Finnair implementation team and PACE experts, who provided support on both software and hardware issues, we managed to almost meet the target date and achieved full operational use by the end of May.
We tackled a steep learning curve during this period, and we think the following insights are worth sharing:
- Good EFB connectivity is indispensable. We started out with ground-based connectivity using cellular and Wi-Fi to load OFPs and send log files. At the time of writing we were testing Inmarsat’s SwiftBroadband-Safety (SB-S) on two aircraft for in-flight connectivity, which will help us tap into additional savings provided by continuous weather updates.
- Supporting ground infrastructure is a boon. We focused on creating an integrated process and data flow from flight planning to post-flight analysis which will be explained in more detail below. Another important objective was to put a ground-based monitoring system in place, which checks that the software is running smoothly and that pilots are using it routinely, the rationale being that because pilots can do their job without the software they are less likely to report errors or malfunctions.
DATA FLOW AND INTEGRATION
We consider an uninterrupted flow of OFP data from flight planning to post-flight analysis as a key prerequisite to improving operational efficiency (figure 2). The initial OFP is generated with our ground-based flight planning system and shared with PACE for further optimization. PACE supplies us with weather services and publishes flight plan updates based on the latest forecast at regular intervals. Closer to departure time a final version is made available, which can be ingested by the Pacelab FPO software and used enroute as a reference point for quantifying the savings potential of following the optimized flight profile, as described above.
Our pilots have really taken to their new EFB tool, which tempts many of them to explore what-if scenarios – ‘If I change the arrival time, how would that affect my operational efficiency? Would I have to change altitudes and speeds?’
At the destination airport, a log file of the trip is sent to Finnair’s post-flight analysis system as soon as the aircraft has established a Wi-Fi or cellular connection. That way, we are able to automatically collect information about tool usage and the total savings our flight crews achieve by using Pacelab FPO.
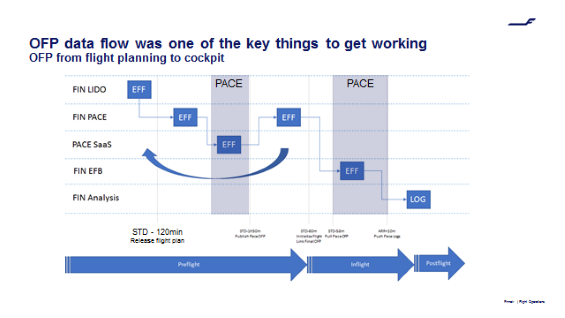
Figure 2
CHANGE MANAGEMENT
Pilot acceptance is of course pivotal to implementation success, but first we had to get Pacelab FPO approved by our local CAA, as it is mandatory for any new EFB software. Negotiations with the CAA went smoothly, so we were able to complete the approval process in less than two months; the fact that Pacelab FPO had already been approved by other European authorities for other PACE customers certainly sped the process along.
The acceptance of a new EFB tool depends on the perceived benefits it brings to pilots’ day-to-day activities and how comfortable they are using it, which is why we started a comprehensive training and mentoring initiative.
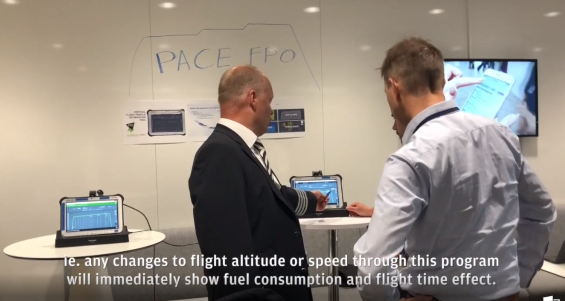
Figure 3
Our primary instruction material was a computer-based training (CBT) provided by PACE, which introduces the software’s core functionalities and explains how to use them most effectively. We supplemented this with an in-house self-study option for pilots interested to gain a deeper understanding of the underlying business logic, optimization algorithms, etc.
Around the time of the software roll-out, we installed a promotion desk, which offered crews preparing for a flight a chance to gain hands-on experience with the software, with knowledgeable staff on hand to answer any questions or concerns they may have (figure 3). The response was extremely positive, and we received a lot of valuable feedback and suggestions for future improvements. We find it very important to listen and to act on our pilots’ suggestions to ensure their continued trust in the software.
We also promoted the Pacelab FPO software to other internal stakeholders and published an article targeted at the wider public in our marketing magazine BlueWings.
Pacelab FPO’s usage rates have grown steadily, as shown in figure 4. In fact, those figures may even be a little conservative – at the time of writing, the software was used on approximately 80 percent of all flights, or almost 90 percent if you count the flights where non-usage is due to IT-related problems.
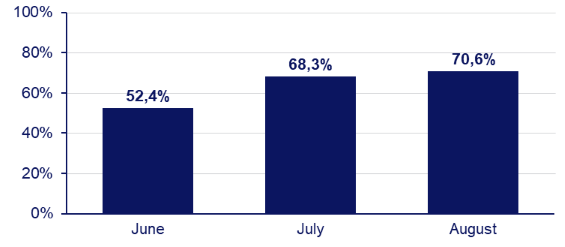
Figure 4
CONCLUSION
The implementation of the Pacelab FPO software has helped us realize a substantial part of the technological and economic potential of our next-generation A350 aircraft and the connectivity provided by its AID – we have successfully improved our operational efficiency and work processes, empowered our flight crews and created a safer, more enjoyable passenger experience. And most importantly, we are keeping fuel burn and harmful emissions to a functional minimum.
Contributor’s Details

Henri Lönn, M.Sc.(Tech) is the Development & Support Manager at Finnair Flight Operations. In addition to the daily operations support, recently he has been focusing on different flight efficiency initiatives and EFB development.
Tom Hakala
Captain Tom Hakala, M.Sc.(Tech) works as a Fleet Technical Pilot at Finnair flight operations. Tom is currently focused on fuel efficiency and technical area in flight operations. He has also a strong background in aircraft performance and in the flight planning area.
Finnair
Finnair is the fifth oldest airline in the world still operating, and the flag carrier and largest airline of Finland which, with its subsidiaries, dominates both domestic and international air travel in Finland. The airline flies between Europe and Asia along the shorter northern route and to over 100 destinations in Finland, Europe, Asia and North America with an almost all-Airbus fleet of more than 60 aircraft, including several new Airbus A350 XWBs.
Pace
PACE has built a reputation for developing trail-blazing software products, which took them from university spin-off to international market player and partner of choice for leading aerospace and aviation companies. The Pacelab range of commercial off-the-shelf software products is based on a strong commitment to sustained innovation and product quality that addresses both customers’ business and technological needs.
Comments (0)
There are currently no comments about this article.
To post a comment, please login or subscribe.