Articles
Name | Author | |
---|---|---|
Future-proofing the Supply Chain | Saravanan Rajarajan S, Associate Director – Aviation Practice, Ramco Systems | View article |
new way of looking at and managing pre-maintenance data Part 1 | Steve Sayers, Director of Technical Publications, FLYdocs | View article |
Paper to Data – Data to Dollars Part 1 | Rob Saunders, Managing Director, Air2MRO | View article |
Case Study: Counting beans and tightening bolts | Kevin Chi-Ming Chen, Senior Vice President, Evergreen Aviation Technologies Corporation (EGAT) | View article |
Case Study: Fleet Technical Management and CAMO | Darmilo Sosa, CEO, Wingbox Aviation | View article |
Case Study: Fleet Technical Management and CAMO
Author: Darmilo Sosa, CEO, Wingbox Aviation
SubscribeFleet Technical Management and CAMO
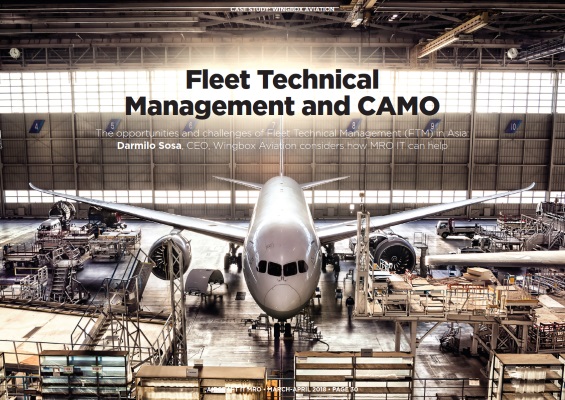
The opportunities and challenges of Fleet Technical Management (FTM) in Asia: Darmilo Sosa, CEO, Wingbox Aviation considers how MRO IT can help
The theme of this article will be to share with readers some thoughts on fleet technical management (FTM) today and how technology can be used to improve processes and outcomes. First, though, a little background to Wingbox Aviation.
WINGBOX AVIATION
Ours company is based in the Philippines and, while we are small, we are proud of our achievements. Wingbox provides services for airlines and leasing companies with aircraft returns, deliveries, FTM and MIS (maintenance information system), plus some MROs for quality and engineering purposes.
THE CHALLENGES FOR SMALL AIRLINES AND OPERATORS
Competition
The first big challenge is in increased competition with every year, in Asia, a lot of airlines starting and some of the established operators growing. Both Airbus and Boeing have a focus for the next twenty years for about forty per cent of aircraft deliveries to be to Asia Pacific with nine per cent alone going into South East Asia. Given those figures, it’s easy to imagine what the competition will be like. With this competition, users and passengers will look for better services. In 2016, Oxford Economics estimated that 46% of the world’s middle class in will be in Asia Pacific. Those middle classes and most passengers will compare between different airlines or corporate operators. This means that small airlines and corporate operators will have to create a successful brand to be able to compete. The positive message Wingbox takes from this is that challenges for smaller airlines and corporate operators present opportunities for us.
Regulatory requirements
The second major challenge will be that of regulatory requirements with all the safety concerns and with the emphasis on accuracy of fleet management. Regulators will usually look at our annual reliability, how many MELs (Minimum Equipment List) we raise each year and any ADs (Airworthiness Directives) that might not been complied with or MPDs (Maintenance Planning Documents) that have been complied with.
Solutions
To overcome challenges and achieve goals, we might remember the Chinese philosopher Confucius who reminded us that, ‘when it is obvious that the goals cannot be reached, don’t adjust the goal, adjust the action steps.’ If you want to build a successful brand but it doesn’t seem to be happening, you need to change your action steps. Right at the top of any actions needs to be one hundred per cent compliance with all regulatory requirements relating to safety concerns. Second will come the actions needed to create a successful brand.
When these challenges are successfully overcome there will be a definite and positive financial impact for the business. There will be cost implications. For a small airline or corporate operator, there will be the challenge to attract, hire, train and maintain good quality technical personnel. Most technical people will want to have the best employment opportunities and big airlines will wish to hire them, which means there will be competition in attracting the best people. Also, there will need to be the establishment of an infrastructure within which the facility and, importantly, the system (MIS) can best support the goals.
Benefits to be gained
On the other side, there will be a definite financial saving to be realized from correct fleet management. Proper maintenance of all maintenance tasks will eliminate poor maintenance practices plus competent technical personnel will know that the correct implementation of modifications will improve the performance and reliability of aircraft so that a business will be able to achieve reductions of waste in man hours and materials. Increases in productivity will result in better aircraft downtime and help to maintain the value of the asset.
I have worked with a leasing company for quite a while and for all the projects that I have undertaken, regardless of whether the airplane is leased or owned, i.e. whether eventually it will be returned or sold, that process will be very difficult if the asset has not been managed well. In one of these projects, an airline spent millions of US$ to comply with the lease return conditions; because they didn’t manage it well; such a simple example is they put a wrong laminate in the airplane cabin which then had to be replaced at a cost of hundreds of thousand US$. For a small airline, that was a very large cost.
SUCCESS AND CONTINUOUS IMPROVEMENT
Fleet management success can be achieved by a small airline but the question today has to be why small airlines and corporate operators are experiencing big challenges in the road to achieving this.
Good and competent people
The first issue is their ability to attract and retain competent people. There are big challenges for small airlines and corporate operators in this with many people preferring to go to a big company to gain training and experience and/or taking their trained skills and experience to a big company. In a similar vein, the dynamism of employment today can mean that anybody, from the CEO to the shop floor, can be attracted to a new employment for a variety of reasons.
And we have also to consider the thinking of millennials because, in time, most of the workforce in our sector will be millennials. There are a lot of narratives about millennials including that they have a pragmatic idealism, that they empathise too much in work and life and that they are too inclined to the social side of life. I recall, when in Europe on a business trip, I was at Heathrow Airport and read an article on how to deal with millennials which caught my attention because I think I’m the only non-millennial on our engineering team. I thought the article applicable to our company and so, on my return, I arranged some meetings in addition to the usual daily, weekly, monthly, lunch… meetings. The new ones were monthly meeting at which people spent five to ten minutes chatting. It’s effective especially during some of the times when we were experiencing the tremendous challenges of the projects.
Good and reliable IT
The second issue is to have a good and reliable IT system. This would include system functionality that enhances the management of the fleet, of whole assets and of all components. I still remember my first job after university. With the IT system everybody was using Excel files which we found very risky because, on a couple of occasions, MPD (Maintenance Planning Document) tasks were missed, ADs were over-run as a consequence of which aircraft had to be grounded for a longer time because the maintenance had not been properly performed. The system should also definitely be user friendly with an ease in audit and system checking and at a reasonable price, especially for any customizations.
THE IT CHOSEN BY WINGBOX
The MIS system that met our expectations, for both functionality and value for money, was OASES by Commsoft which we have found excellent for airline IT and MRO IT solutions.
Extensive Solutions
First, it offers extensive solutions with comprehensive capabilities from Continued Airworthiness right across to Material Management (figure 1).
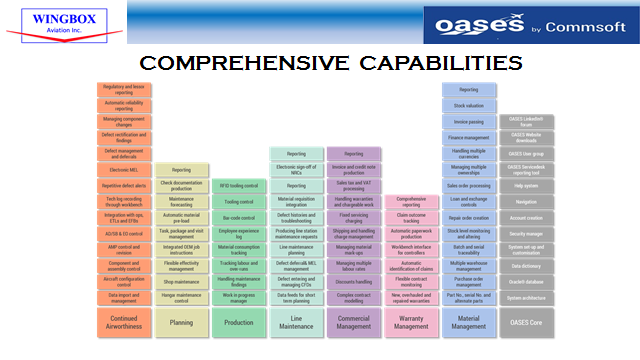
Figure 1
Sensitive to new trends
The system is sensitive to new trends and technologies. There is an e-records system. I recall while I was working in a leasing company when an airline was returning an airplane: it was twenty years old so there were many records but the one that we particularly needed had been lost by the airline. At that time, Boeing only had a seven year retention period for archived records but fortunately, when they had undertaken an audit, they had scanned some records so that we were able to find the missing record which saved a lot of money, especially for the airline.
e-Record System
Modern e-Records systems such as AirVault / Stream integrate easily with most MRO systems. With OASES, Customer Work & Repair Orders are electronically received into the MRO IT system while completed Work & Repair Orders are similarly delivered electronically directly into the customer’s document management system. It reduces the user’s administrative burden which, in turn, helps to mitigate risk; it can analyse and see trends in work efficiency and reliability by using advanced OCR search tools and it generates a comprehensive audit trail.
MOBILE SOLUTIONS
The system has a mobile solution to meet the growing use of mobile solutions in aviation for such as forecasts and Carried Forward Defects (CFD), which is very useful for planners and maintenance personnel, especially line maintenance. Because OASES mobile was developed in HTML5, it can be used on tablets, on smartphones and in most browsers. But, critically, mobile apps need to be agile: capable and ready to respond.
MRO IT SYSTEM
Now we come to the central topic in this article; the MRO IT System.
Modular structure
In Wingbox we use OASES, as I’ve already mentioned, and it has a modular structure (figure 2) backed by flexible commercial policies:
- It’s licensed by concurrent users and modules;
- CAMOs pay per MSN (manufacturer’s serial number);
- There are equalized monthly payments;
- No cost upgrades;
- Minimal ‘up-front’ investment needed;
- There is personalized support; and…
- There are dedicated account managers.
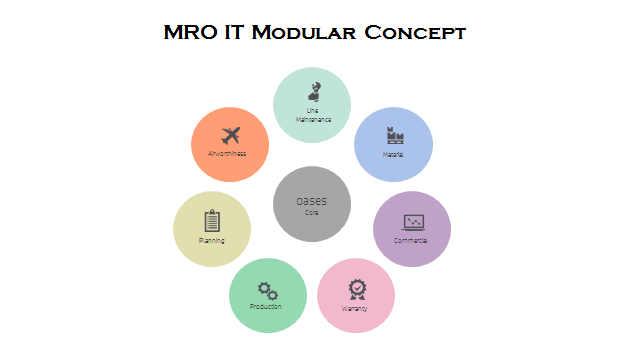
Figure 2
There is a full end-to-end process control (figure 3) and everything together drives value through an efficient fit to needs.
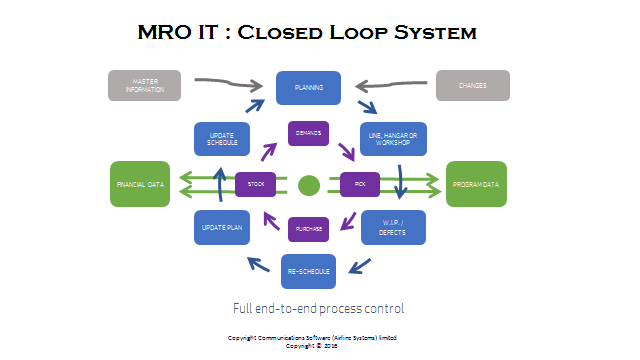
Figure 3
Significant features for FTM and CAMO
This is the start of preventive maintenance with the set-up of the maintenance program; then there are the ADs and SBs (Airworthiness Directives and Service Bulletins). The system will generate work scope and create a work order; it will also generate a task list for lessor/customer review which is a very important thing from the lessor perspective during the return when they will want assurance that all the tasks have been included in the lease with the work package. I have often experienced that every task has been missing which meant the ‘C’ check that’s supposed to be for 30 days had to be increased by a further 15 days for the return. The system is able to generate work pack / cards and checklists (if required) and to record the completion of tasks after the MRO has completed them. It can create/review a ‘last done / next due’ report which, on an A320 or B737 can amount to 6,000 tasks; plus it can create an AD/SB statement to assure the airline that nothing has been missed.
Audit and security admin
The OASES system includes extensive security controls that limit access to key users and managers. A sample screen can be seen in figure 4.
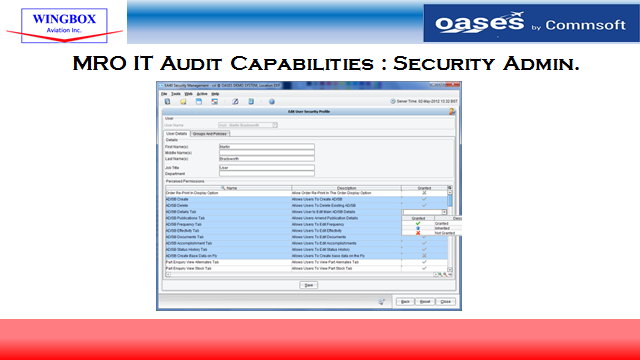
Figure 4
The benefits of integration
Where an airline’s IT and the MRO’s IT are interlinked with each other, that means:
- Less human interventions which will translate into increased output accuracy – this is in line with thoughts about big data and artificial intelligence which is now at a stage where it will be able to manage what we need as long as humans retain control of the checks and balances in the system.
- Increased productivity: I can recall from a previous job presenting to the boss a proposal for an MIS implementation. The owner of the airline requested a justification and, during the meeting, asked why he needed to spend hundreds of thousands of dollars for an IT system. All I had to mention was productivity. He asked for a further explanation which was that, from the planner who creates the forecast there is only one click for the material planner and purchasing to be able to see everything and then to the maintenance people… it’s all in one link which will increase productivity.
- Cost saving. Normally maintenance and engineering people only spend money. But if the airline and MRO ITs can be interlinked with each other there will be a cost saving.
I hope this has enlightened readers on Wingbox’s experiences with technology and IT; the challenges we have faced, the opportunities that have presented to us and the benefits that we have discovered in applying IT to our processes
Contents
Due to market pressures, small airlines and corporate operators in Asia are looking to enhance their maintenance activities with independent third party services but this requires a flexible, capable and affordable MRO IT system.
Contributor’s Details
Darmilo Sosa, CEO, Wingbox Aviation Inc.
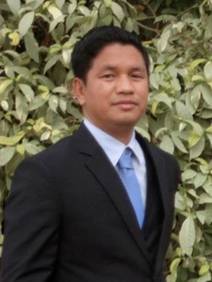
Wingbox Aviation
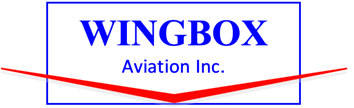
The Wingbox TEAM is composed mainly of aviation engineers and legal counsels with extensive experience in aviation-related matters. Such experience has enabled the incorporators, especially the aviation engineers, to perform services, both locally and internationally, in connection with aircraft delivery and re-delivery, particularly on data-gathering and analysis, documentation, and aircraft inspection.
Comments (0)
There are currently no comments about this article.
To post a comment, please login or subscribe.