Iryna Khomenko, Manager Operational Efficiency at IATA updates the initiative to promote paperless aircraft maintenance
ABOUT IATA
Before addressing the key topic for this white paper, IATA’s Paperless Operations Initiative, it will be useful to offer readers a brief introduction to IATA. It’s a global trade association for the world’s airlines with 260 passenger and cargo airline members who, between them, account for 86% of global air traffic. IATA works principally to meet the needs of members; representing them, protecting their interest and leading the industry, with various initiatives, to make their businesses better and more straightforward. The association was formally founded in 1945, since when and to date it has focused very clearly on supporting safety, sustainability and profitability in the airline business. The division in which the paperless operations initiative is managed is Safety & Flight Operations (SFO).
The continuous improvement of aviation safety is the cornerstone of Safety & Flight Operations’ goals plus striving to ensure that membership delivers increased value through partnership, to protect the interests of the industry and to work towards a reduction in the environmental impact of aviation.
PAPERLESS AIRCRAFT OPERATIONS (PAO) INITIATIVE
Safety & Flight Operations division embarked on this initiative in 2011 encompassing a number of areas including:-
- Auto-ID for aircraft parts tracking and as an alternative means of compliance;
- The use of digital signatures- in technical operations;
- Electronic maintenance record keeping;
- Electronic aircraft lease transfers;
- IATA standardized maintenance agreement templates;
- Aircraft lease best practices;
- Support for use of electronic regulatory documents (XML FAA 8130-3 / EASA Form 1 and others).
The list is by no means exhaustive plus new topics are being added every year as suggested by members; but the topics listed are the ones on which the division is currently working.
PAPERLESS 2020 VISION
As part of the overall initiative, IATA has developed a vision for aircraft operations becoming paperless and has accepted, in its airline and industry working groups, that the target implementation year for this should be 2020. So, what is this vision?
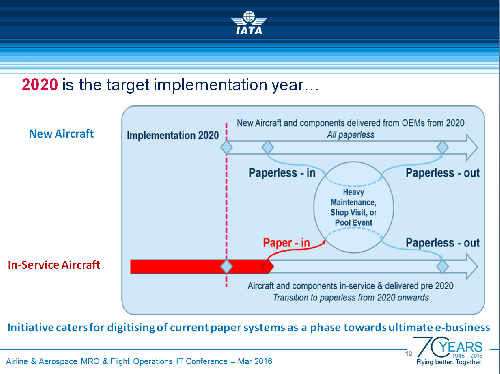
The above chart shows that, in line with the initiative, aircraft and components manufactured from 2020 will have all of their initial records and documentation in electronic format from the outset, ‘paperless in and paperless out’. Aircraft in service before 2020, with an associated paper trail, will initially go through the maintenance processes such as heavy maintenance, shop visit, or pool events for components, and will have their documentation digitalized during that process to come out paperless, ‘paper in and paperless out’. This is, of course, a simplified version of the vision and there is a great deal of work that has to be undertaken and completed in order to deliver this overall objective. In order to ensure that the whole move to paperless is properly managed, a ‘Transition Roadmap’ has been developed.
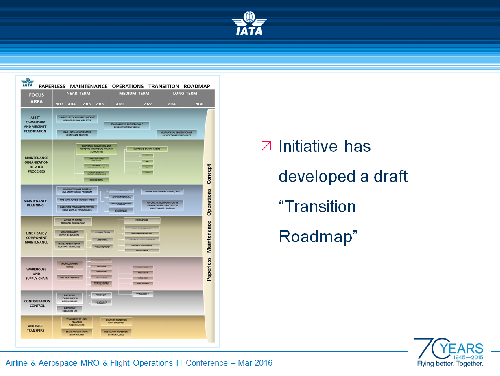
The roadmap identifies the focus areas to be tackled in order to achieve the target date and the tasks to be completed within each focus area during the near- medium- and long-terms. It also shows where and how focus areas are interconnected and how work in one area will link with tasks and achievements in another. Note that the Roadmap is a ‘living’ document and is updated as we have new information.
So, we know that we want operations to be paperless; the big question is; ‘how can that be achieved?’ This is also the interesting part.
ENABLERS OF PAPERLESS OPERATIONS
There are a number of technologies and processes that will have to be understood and considered for their suitability in this sector as well as how they could be adapted to work in the highly regulated and safety focused civil aviation environment.
RFID
Initially, the initiative looked into Auto ID/RFID technology which became popular in other industries more than ten years ago and has made significant progress in the pharmaceuticals and retail sectors. IATA has considered the application of RFID technology in connection with:-
- Tracking the expiry date, presence and security of emergency equipment;
- Warehouse location and logistics;
- Tooling;
- Ground Support Equipment;
- Chemicals expiry date;
- Assembly (OEM).
Plus there are IATA RFID initiatives with regards to baggage tracking and ULD (unit loading device) tracking.
However, in commercial aviation the RFID development rate has been slow in light of the heavily regulated nature of the sector. Every transaction completed in maintenance has to be airworthiness compliant which is why the levels of security are very high and numerous. For that reason, to introduce RFID parts tracking for airworthiness compliance as well as for warehouse management is challenging but the PAO group is working on it.
Three years ago, IATA produced a guidance to introduce RFID into airline operations and that guidance will be updated during 2016 because there are a few regulators’ documents that are being updated that will be included in the revised IATA guidance plus some new use cases are also being developed.
Digital signatures or e-Signatures
Looking at the records themselves, the PAO group has considered digital signatures which are now incorporated in many software solutions used in the sector. However, it can be challenging to make those modules fully functional in any MRO IT system so the PAO initiative has identified this as a main element that has to be enabled. Of course, there are in-house solutions that have been implemented in specific companies or airlines but the airline industry is very international in its scope and when a component or electronic maintenance record leaves an airline for another one in a different part of the world, then the question arises of standardization, harmonization and security. So this is what is being addressed by the initiative. What we do know is that in, for instance, passenger records, thanks to IATA’s e-ticketing initiative, the airline industry saves about $2 billion each year. So this is an initiative well worth pursuing.
Some examples of use cases where a digital signature can be applied in our sector would include…
- The registration documents of the aircraft;
- Manuals’ revisions (Maintenance program, Maintenance Schedule, etc.);
- Maintenance Records:
- Task cards;
- Work orders;
- Component overhaul / repair tag (8130, Form 1);
- Supply chain and procurement documents.
In 2015, IATA with support from industry experts developed a White Paper on an ‘Aviation Identification & Authorization System’, which describes the main principles and the concept of electronic authorization for aircraft operations. The idea is to enable such a system to be universally understood and accepted. The paper, which can be found on the IATA website, is the starting point for a unified industry approach to fully electronic maintenance records and is open for comments.
Most electronic signature solutions on the market offer users a PKI (Public Key Infrastructure) based solution. It’s an agreed solution, very secure and adopted by government entities: however, when it comes to the airline sector, PKI has proved to be expensive and something of a burden with a problem regarding scalability; so the PAO group considered what alternatives, options and concepts might be available. In doing this, IATA has established a joint project with Georgia Tech in Atlanta, USA, looking into Domain Name System (DNS) based electronic signatures. The project has developed Domain Name System Security Extensions (DNSSEC) to offer the same level of security as PKI plus the advantage of the new system is that it will use the Internet ‘dot’ as a route and a signature will be an IP address or a computer (as against using a private or public key) that will use Internet protocols. Also the DNSSEC Security tool will help to ensure the security of the process. We are just at the beginning of this development and IATA is evaluating whether more resources can be devoted for that. It has also been presented to various airline groups and industry groups from which the feedback has been very positive. The promise is that the new system should be less expensive but no less and probably more secure and reliable.
Electronic record keeping
One important step in this initiative has been to establish collaboration with ICAO (International Civil Aviation Organization); getting them on board and explaining how important was their involvement and to incorporate their guidance as well as that of national aviation authorities in achieving the introduction of electronic record keeping. As part of this, in 2015 ICAO agreed to the IATA initiated proposal for amendment of the Doc 9760 Airworthiness Manual, with guidance to, “… provide acceptable methods for the development of States’ requirements, and facilitate the implementation and acceptance of Electronic Aircraft Maintenance Records.” This guidance will be further developed over the next year or more so that, hopefully, soon we will have a more solid document to work with for airlines and aviation authorities to overcome the initial fear of and resistance to change by offering some useful plans on how to do it.
Standardized contracts
Another task within the paperless initiative is aiming for the standardizing of maintenance contracts. Mostly the users of these documents are the smaller or mid-sized airlines who do not have large legal departments and don’t wish to spend money on legal consultants to draw up legal contracts. Standardized maintenance contract are off-the-shelf documents that airlines and MROs can use as the basis for an agreement. These standardized documents are now available for a growing number of the engineering needs of airlines and engineering businesses and are available on the IATA website, free to download. Currently, IATA is working on a standard engine maintenance agreement and a shop visit agreement. These standard contracts are developed by a group of experts including airlines, MRO companies, regulators and legal experts. The next job on the list will be to develop a ‘power by the hour’ agreement for components. All the documents that have been developed are free to download from the IATA website (Legal Committee page).
Electronic Log Book
Finally, there will be a sub-group created in this initiative that will take care of Electronic Log Book issues. Over the past three to five years, we have heard of airlines who were trying to install fully functioning and operable electronic log books (ELB) but there have been some challenges and struggles with that. Almost every year, when an airline took delivery of a new type of aircraft from an OEM they would try to use an electronic log book and then would stop and revert to the paper log book. So IATA is planning to assemble an expert group drawn from airlines and to develop a survey to get airline feedback on the challenges and the process of ELB implementation. It is hoped that by the end of 2016, the first results will be available and the IATA group will be able to address them to the regulators and original equipment manufacturers (OEMs).
IATA WORKING GROUPS
There are a number of groups working at the moment.
Paperless Aircraft Operations
There is a group working with paperless aircraft operations which was, for some years, in the form of a think tank drawn from 20 airlines that met twice a year. It produced industry position papers, action items and standardized industry documents, and harmonized definitions, etc. But it was decided that the group and its work needed to be better known beyond just the airline community. So, the think tank became the Paperless Aircraft Operations Conference comprising more than 100 people drawn from airlines, regulators, lessors, OEMs and selected representatives of other industry stakeholders.
Aircraft Leasing Advisory Group
This group produces guidelines for efficient aircraft leasing including:-
- A focus on maintenance and technical issues encountered with aircraft leasing from delivery to redelivery;
- A detailed proposed redelivery process timeline;
- Transfer records and document lists;
- Incident clearance statement (formerly known as non-incident statement template);
- Life Limited Parts (LLPs) tracking template – for use when LLPs are used across the industry.
Airline Cost Management Group
This group collects airline cost data other than for maintenance, i.e. crew costs, overhead costs, other flight operations costs (ground handling, catering…). The group, which is governed by a Steering Committee drawn from 10 airlines, currently collects data from more than 60 airlines, reports every year and…
- Shares best practices on airline cost management, while providing an industry platform for effective cost benchmarking;
- Collects cost data from 60 airlines;
- Produces an annual benchmark report, exclusively available to its members free of charge; and…
- Organizes an annual Airline Cost Conference (more than 40 airlines attended in 2015).
Maintenance Cost Task Force (MCTF)
This task force has been operating for more than ten years and …
- Includes more than 50 airlines;
- Includes OEMs (Airbus, Boeing, Snecma, etc.);
- Collects maintenance cost data and publishes an annual benchmark report for its members;
- Works towards the harmonization of maintenance cost definitions;
- Produces best practices and guidance material, e.g. component maintenance, inventory management, etc.;
- Organizes the annual Maintenance Cost Conference (MCC) with more than 60 airlines (150 individual delegates) participating in 2015 and sharing experiences on how to improve maintenance costs and effectiveness.
Overview of working groups and committees at IATA
As well as working with our own members, we also work with ATA e-Business on some topics. And, of course, we welcome participation by any of our members in these activities and by non-members in supporting sectors such as MRO.
Finally, I’d like to share a quote on this topic from Ray Valeika, former SVP at Delta Tech Ops, “The Aircraft needs to be a standalone data system carrying its own records like a medical file.”
We all believe in this vision and are trying to enable it; and, together with our members at IATA, we will achieve it in the future.
Contributor’s Details
Iryna Khomenko
Iryna is currently working at IATA on an industry template agreement for Engine shop Visits and harmonized documents for Aircraft Leasing transfer. Before joining IATA, she worked for six years as manager of the Maintenance & Engineering finance department at Aerosvit Airlines, Ukraine. Her responsibilities embraced financial and economic aspects of the airline’s Technical Operations. Iryna started her career as an economist in Ukrainian – Mediterranean Airlines after obtaining her master’s degree in Management and Economics.
IATA
The International Air Transport Association (IATA) is the trade association for the world’s airlines, representing some 260 airlines or 83% of total air traffic. It supports many areas of aviation activity and helps formulate industry policy on critical aviation issues. A guiding concept of IATA’s structure is ‘Global Development, Regional Delivery’, where the Head Office divisions drive the development of global standards, systems and advocacy positions, while the regional and country offices are responsible for implementation.
To post a comment, please login or subscribe.