Articles
Name | Author | |
---|---|---|
Case Study: Using technology to improve flight ops experiences at IndiGo | Aakash Bhatnagar, Director-Flight Operations Support, IndiGo, and William Hu, Regional Head/Senior Sales Director, Asia Pacific Region, NAVBLUE | View article |
Case Study: SWISS International Air Lines introduces an Electronic Log Book (eTL/ELB) | Marcus Di Laurenzio, Project Manager, SWISS International Air Lines, and Udo Stapf, CEO, CrossConsense | View article |
ATM Enhancements and Trajectory Based Operation (TBO) from ICAO | Henk Hof, Head of ICAO & Concepts Unit, Eurocontrol | View article |
Case Study: Icelandair EFB Project | Captain Grétar Mar Óðinsson, Lead EFB Project Team Manager & Capt B757, Icelandair, and Jens Pisarski, COO & Partner at International Flight Support | View article |
Case Study: Icelandair EFB Project
Author: Captain Grétar Mar Óðinsson, Lead EFB Project Team Manager & Capt B757, Icelandair, and Jens Pisarski, COO & Partner at International Flight Support
Subscribe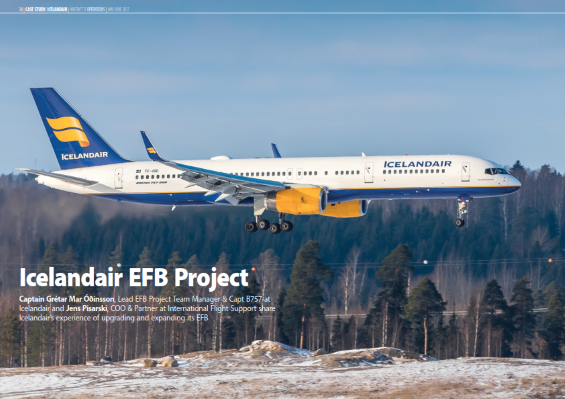
Airline Case Study: Icelandair EFB Project
Captain Grétar Mar Óðinsson, Lead EFB Project Team Manager & Capt B757 at Icelandair and Jens Pisarski, COO & Partner at International Flight Support share Icelandair’s experience of upgrading and expanding its EFB
Icelandair has had an EFB project running for a few years, since 2004. This article will explain something about the project; how it came about, how it is evolving and how Icelandair sees its EFB in the future… what they wish to get from it. During the course of this project over several years there have been a lot of changes from when the project started in 2011 up to the present time. Today, the talk is of integration, trying to combine data into one application, a single user experience: it’s all very encouraging.
But before we go any further, some words about Icelandair, quite a small airline whose location is in the middle of the Atlantic Ocean on an island with a population of just 330,000. The airline is 80 years old (1937–2017) and serves major markets in Europe (26 destinations) as well as North America (18 destinations) through its Keflavik hub. Its business strategy is based on the geographical position of Iceland, midway between North Europe and the East coast of the USA. This means that, despite its size, Icelandair carried some 3.5 million passengers in 2016, a figure that has been growing at about 15 percent each year for the past six years. The fleet includes 28 Boeing 757 with four 767s plus 16 Boeing 737 MAX on order plus a further eight options. 737 deliveries will start in early 2018 and the aircraft will be equipped with the same EFB solution that is used on Icelandair’s 757 and 767 fleets.
ICELANDAIR EFB PROGRAM HISTORY
The EFB program so far in 2011
With a history stretching back to 2004, Icelandair’s is a mature EFB program which started using laptops assigned to all flight crew. Installed on the computer were four applications; a Document Library (PDFs that removed paper from the aircraft), performance software, mass and balance (M&B) software (to be used as a backup) and a reporting tool. Later on the laptops were replaced with a tablet, but without making any significant changes to the platform. The reason why the platform didn’t evolve over some ten years was that the airline was never able to make the financial justification for a major upgrade, some of the benefits were already being enjoyed so the business case just wasn’t sustainable. And then of course, the financial crash in Iceland in 2008 didn’t make things easier.
However, when the dust started to settled in around 2011/2012 Icelandair decided to again consider bringing the EFB up to date. They knew form previous experience that Flight Operations alone wouldn’t be enough to get things running but thought that fuel savings could be a significant value to be gained from any upgrade, especially when, at the time, fuel prices hovered around $3 USD for a gallon (USG) as opposed to c$1.40 at the time of writing. There were opportunities to be gained from improving workforce efficiency by improvements such as eliminating repetitive work, and manual transcription. However, that was not sufficient to support a good business case with a positive return on investment. So, the sponsors approached the project from another angle, deciding to broaden it out to other departments in the organization in hope that, by doing so, it would be possible to increase the benefits side of the business case without proportionally increasing the cost of the project. In doing that, the decision was also taken to seek expertise from outside of the company.
Defining the scope of the broader project
Icelandair’s EFB project teamed up with Closed Loop Consulting and, with their help, brought together teams from different departments in the airline to evaluate whether there were opportunities to improve their operation. This could be by connecting the aircraft and its crew to the ground in near real-time regardless of its phase of flight or geographical location, to facilitate in sharing of data from the aircraft which could be used in different systems on ground to then feedback data to the flight crew to help them in their strategic decision making, before, during and after the flight. During this process the team realized that, by relieving themselves of constraints such as which OS to use, whether to use iPad or not, and whether to use app A or app B, made them capable of seeing the EFB in a different light as a functioning EFB solution for the company, not just as a cockpit device that pilots use on and off the flight deck. This systems-led approach was, at that time, new to Icelandair and to many other in the industry.
The team soon learned that there were numerous touching points and several opportunities to work with. It was also noted that data, or the ability to have access to data in a shorter timeframe and in a reliable, consistent format created opportunities that hadn’t previously been thought of. One such opportunity was data centricity which became a driver in the project but that also created new obstacles to be overcome including, how to connect all those data points, considering what data is of value and what opportunities it presents. For that, a strategy was needed and, for that, a grasp of the concept and term eEnablement was needed. The team had, and in a way still have, a hard time grasping this eEnablement idea which has been a buzz in the industry for the last couple of years but which still lacks any clear definition. The team had to think about how they would be able to work with it. But they understood that the sooner they got their EFB and eEnablement strategy in order, the more value they would get out of the available data. And in a business where margins are tight, everything matters.
Establishing the requirements of the EFB upgrade and the RFP
From all this work Icelandair was able to create a concept of operations, their vision for the EFB system: how it would work and how it could be used to help the business grow. New opportunities to improve were identified and the team was able to put a value on some of the resulting benefits, some of which were put into the Business case. From the concept of operations the EFB project team created a functionally specified RFP (request for proposal) which was sent out to the market with an invitation to the suppliers to innovate.
This functionally specified RFP included between 800 and 900 specific requirements…
.png)
Figure 1
… some of which can be seen in figure 1, which looks like a lot of requirements for an EFB. The scope of the RFP seemed to puzzle lot of people in the industry but the requirements covered a lot more than simply the device, the mount, the power and the software. They addressed the whole system including integration, security, project management, certification and testing: a long list but one that would be true for any airline. In the end Icelandair received just fewer than 30 responses from single suppliers to large scale integrators, bidding for parts of the solution up to responses covering nearly all the requirements for the solution as a whole.
The selection process and a soft reboot
Having asked so many questions, the team then had to consider an equally long list of answers while reviewing all of the responses; and rate them appropriately. In the end, that took a bit longer than expected as the time required for reviewing and rating had been underestimated. Nevertheless, in the end it was possible to narrow the field down to two ‘finalists’ and start serious talks with them. That also took longer than expected due to the complexity of the solution and different understandings of what was being asked for and how Icelandair’s requirements could be met. Unfortunately, in the end those talks ended without any contract being signed, largely because the finalists and Icelandair were unable to come to a common understanding on how the suppliers intended to meet the airline’s requirements. That actually left the challenge of how then to make the best out of this exercise for the airline.
Should the project simply be scrapped and the team go back to the drawing board? No, that was not an option because the project so far had cost a lot of resources and had gathered a lot of information as a result of the responses by the suppliers. The decision was to undertake a ‘soft reboot’ of the project which entailed some project shift and a more active role than originally envisaged for the project team in Icelandair. Instead of outsourcing a lot of the responsibility of project management, testing and implementation the airline decided to manage those processes internally. Project management is a daily task for airlines but for an airline the size of Icelandair, which was also experiencing significant growth at the time, it represented quite a challenge.
The project was and is championed by the flight operations department and it was decided not to change that. With good management, the airline was able to get the project back on track and sign the first contracts in early 2015; two years after completing the concept and some fourteen months after the initial issue of the RFP. The delay as a result of the shift in the project was about six to 8 months. In the rebooted project, the RFP responses were re-evaluated to identify the ‘best bits’ in order to retain the good business case. Even though the project plan had shifted, the requirements were the same as before and the same opportunities were envisaged. The only significant change was that the responsibility to achieve those benefits rested more deliberately with the airline than had initially been planned. The question now was how to manage that?
It was managed by selecting vendors that were felt to understand Icelandair’s requirements and were willing to go the extra mile to ensure that the airline could meet those requirements. The team wanted vendors who would be as much partners in the project as simply vendors of a solution because a successful outcome would depend on their active participation in the project. Also, in order to ensure that it worked within a realistic time frame, the project had to be broken into several phases starting with the basic hardware on the aircraft and the basic software modules and, from there, the project grew along the lines of an ITIL approach (figure 2).
.png)
Figure 2
There had to be a plan as to how and when the full solution would be in place and the project team had to work to that. However, it was not straightforward as there were a number of obstacles along the way which were outside of the team’s control but that’s something that simply has to be faced with this type of project.
Icelandair now has a great team for software, hardware, data access integration and analytics, and connectivity on the aircraft. There are also great connected back-end systems although figure 3 does not yet include Mxi Maintenix, Icelandair’s MRO / maintenance system which will also soon be integrated into the solution
.png)
Figure 3
ON THE AIRCRAFT
The hardware on the aircraft consists of a Panasonic Toughpad with the SCANDINAVIAN AVIONICS TCU and Mount with DIC-600. In June 2016, Icelandair commenced an operational trial period for completion with full fleet approval before the end of that year. From there, in the months and quarters that follow, Icelandair will continue to add functionality to the solution.
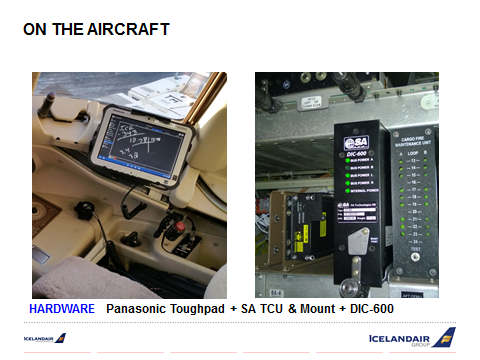
ICELANDAIR’S EFB
The set-up of the EFB system is fully flexible as to how information is presented whether by aircraft or by crew. The pilot’s first step is to update the system which runs as a shell so that all updates are driven through the INTERNATIONAL FLIGHT SUPPORTPFB™ Paperless Flight Bag platform for chart updates and airport database updates and document updates from the editing system. Scheduled flights are fed from the schedule system so that the traffic is understood by the PFB™ Paperless Flight Bag and the pilot can choose which flights to download and enter into a created flight library to go into the operational planning of each one. For the overview page (figure 4), the basic data comes from the scheduling system.
.png)
Figure 4 – PFB™ Overview Screen showing the imported scheduling data
As can be seen at the bottom of figure 4, the pilot has a function to choose manual loadsheet or ACARS loadsheet because Icelandair currently has a process to switch between them; the EFB facilitates this and, in some cases, the loadsheet module on the PFB™ is used as a backup, but otherwise as primary. The overview page shows the briefing package as it comes out of the flight planning system for reference and, of course, in the in-flight section there is an electronic OFP (operational flight plan). There will also be weather charts, wind charts; in short, everything that comes from the flight planning system. There is an electronic NOTAM module where the sorting is done by the flight planning system normally or the NOTAM source: the pilot also has the possibility to highlight and select NOTAMs which end up in the ‘Selected’ section. Behind the pre-Flight section, there is a depiction of all the data that normally sits in the journey log report and users can add other information that they might want.
.png)
Figure 5 – PFB™ eFlight Planning Module showing eOFP for eFuel and eTime checks
The architecture provided by International Flight Support to Icelandair for their EFB allows the modules’ sequence to be moved around and the input data can also be moved around which means that users can customize each module with the workflow appropriate to the airline using the system. Also, they can add new functionality at a later stage, as and when it becomes available. The system includes fuel planning which, again, can be customized to meet each airline’s individual needs and the various features of different aircraft types – number of fuel tanks, etc. There is an ATC/ATIS (Air Traffic Clearance and Automatic Terminal Information Service) Note Taker module allowing hand written notes to be entered and included in the post-flight report. The PFB™ take-off module is integrated with ACFT PERFO performance calculator in the background, is fully offline capable and can be customized. Loadsheet (cabin and hold) can take data from ground systems or be run wholly offline. Also the PFB™ system will automatically take care of the distribution of loadsheets to airports and handling agents once the loadsheet has been submitted. For the Navigation Log/eOFP, where necessary or required, the system allows the presentation to look the same as with the paper-based system that it replaces (Figure 5). With Landing and the Post-Flight reports, the PFB offers at least the same reporting capabilities as the system it replaces, as well as sending data to other parts of system – for instance, maintenance as supported by the PFB™ Back-Office integration engine (Figure 6)
.png)
Figure 6 – The PFB™ IT integration concept from International Flight Support
THE LESSONS LEARNED SO FAR
All EFB projects are both similar to and different from each other so no one solution fits all. They all share a common goal to improve the operational efficiency of the airline but how they do that varies between airlines. Running an EFB upgrade program like the one at Icelandair is a big challenge. It requires commitment from top management of the company, the right people on the project and good project management from all parties involved plus good cooperation between the different suppliers or partners in the project. It helps if the airline has previous experience with EFB but the perfect EFB does not come out of box – it does not exist. Airlines have to create it in cooperation with their suppliers and partners or internally, if the airline has the resources to do that. However, most airlines don’t as their main purpose is to get passengers and freight from A to B.
The EFB project at Icelandair has been a complex task and yours might well be too, due to operational, hardware and software complexities. However, to be successful you have to know, where you are, where you want to go, why you want to go there and some sort of a map on how to get there. And to minimize the likelihood of getting lost along the way you need to have a good group of people on your team and to have a great working relationship with your partners (vendors) in the project. For a complex project to succeed you need to break it into phases. Initially Icelandair probably tried to take on too much from the start, causing delay in the project; but by slicing it into more manageable phases you and your suppliers can more easily digest it and deliver a successful outcome.
Even though the project didn’t unfold as Icelandair planned for initially we are certain that we are on the right path to meet our requirements. We have a strong team in all of the suppliers and, what is most important, great backing from management. The eventual financial success of the program won’t be known until one or two years’ time when Icelandair has been able to measure the true value of the changes being made.
Importantly, systems such as EFB consist of people, structure and processes that work together to create an organizational outcome. While systems might be supported or enabled by certain technology; technology does not drive the system – but flexible airline and flexible vendor interaction does.
Contributor’s Details
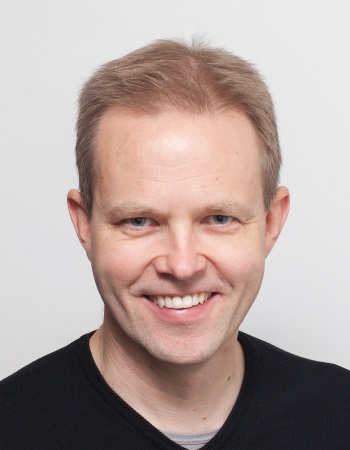
Lead EFB Project Team Manager & Capt B757
Icelandair
Captain Grétar Mar Óðinsson has been with Icelandair for the past 19 years flying Boeing 757 and 767. Alongside his flying duties, He has worked in IT, specializing in implementation and operation of back office systems. He has been involved with Icelandair EFB program since 2004, was part of the initial implementation team and was also involved in the first refresh cycle in 2009. Grétar became EFB Administrator at Icelandair in 2012 leading the EFB program.
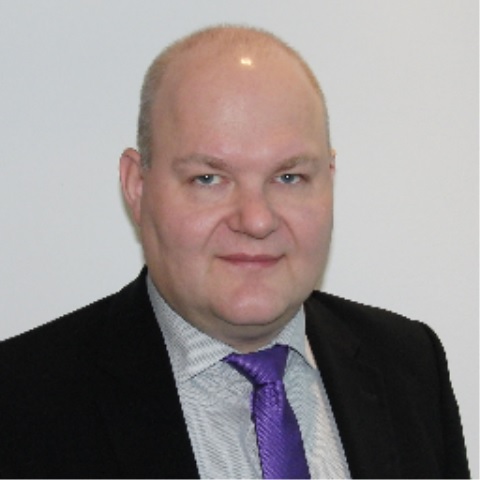
COO & Partner
INTERNATIONAL FLIGHT SUPPORT
Jens Pisarski has been a leading force in commercial aviation over two decades in establishing flight planning software provider AIR SUPPORT A/S on the world market. His responsibilities at International Flight Support since 2011 cover management, business development, sales, marketing, administration, key account management, financial aspects as well as IT Contract Management/legal affairs.
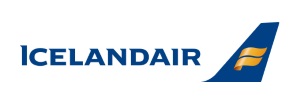
Icelandair’s business strategy is based on the geographical position of Iceland, midway between North Europe and the eastern coast of the USA, connecting 26 gateways in Europe with 18 gateways in North America, through Iceland as a hub. Icelandair offers flights to and from Iceland, with its fleet of Boeing 757, 767 and 737 MAX on order.
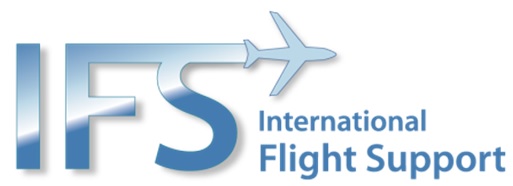
The business strategy the for PFB™ Paperless Flight Bag from International Flight Support – available for iOS and Win 8/10 solutions – is to offer advanced IT integration to the airline’s back-end systems while delivering fully flexible, interfaced and fully interconnected EFB software solutions to airline and military operators. Each EFB system is customized and optimized to each operator’s requirements during the set-up process without excess development time applying.
Comments (0)
There are currently no comments about this article.
To post a comment, please login or subscribe.