Articles
Name | Author | |
---|---|---|
Commercial aviation in 2019 | Mark Martin, Director Aerospace & Defence Business Unit, IFS | View article |
MRO 4.0: The Next Big Step for Processes – Using Digital Twins and Location | Dr. Hugh Revie, Sales Director Aerospace, Ubisense | View article |
Case Study: CSAGA Looking to an efficient future | Yang Kai, IT Project Manager, China Southern Airlines General Aviation Ltd (CSAGA) | View article |
Effective and efficient – obtaining regulator acceptance for electronic signature | Mark Schulz, Senior Vice President Worldwide Sales, EmpowerMX | View article |
MRO 4.0: The Next Big Step for Processes – Using Digital Twins and Location
Author: Dr. Hugh Revie, Sales Director Aerospace, Ubisense
SubscribeImproving business efficiency in an MRO environment
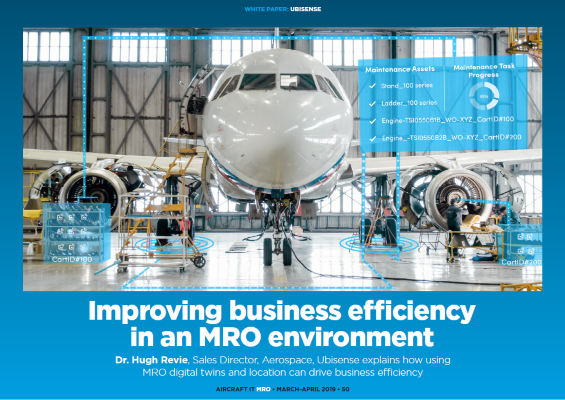
Dr. Hugh Revie, Sales Director, Aerospace, Ubisense explains how using MRO digital twins and location can drive business efficiency
Industry 4.0 is a hot topic within many sectors; what it means and where customers will be able to realize value by implementing specific facets of this technology: it fosters what has been called a ‘smart factory’. Within modular structured smart factories, systems model physical processes, create a virtual copy of the physical world (the Digital Twin) and make decentralized decisions. Over the Internet of Things (IoT), systems communicate and cooperate with each other and with humans in real-time both internally and across organizational systems utilized by participants in the value chain.
There are many sides to Industry 4.0, the Smart Factory or in this specific case, the Smart Hangar, but at the heart of this new way of running industrial processes and their component parts is digital technology and the use of data. In this paper, my plan is to offer readers a new perspective on one aspect of how they can apply Industry 4.0 ideas, methodology and data management to better manage their maintenance, overhaul and repair businesses, creating the start of an MRO 4.0 implementation.
Ubisense Limited is a real-time location focused solution company. So, perhaps, it will come as no surprise when I say that I want to describe how location can help influence your business and improve the efficiencies of what you do in an MRO perspective and within your Smart Hangar. I will also explain what we mean by a Digital Twin, what it means in this context and how it can help to better understand what is going on in your business.
THE IMPORTANCE OF LOCATION
Within the MRO community, the concept of using ‘location’ is new for most companies since there are very few that are currently using this as a tool to help drive efficiency.
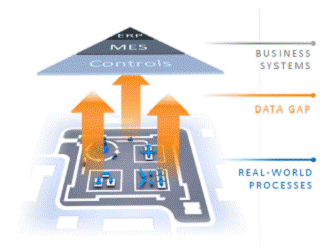
Figure 1 – Link between business systems and the real world processes
Figure 1 offers a good perspective on today’s position in most MRO companies showing business systems at the top of the graphic, including ERP or MES systems, systems of records, control systems, etc. – the systems that are managing what is happening in the business. At the bottom of the graphic is the real world, which is the hangar floor and all the activities that go on there. Currently, the activities that are planned in each business are managed using the systems and data available, with no link to what is actually happening on the hangar floor. This creates a data gap, where there is no way of knowing what is happening on the hangar floor until after it’s happened. Only limited historical information is fed back into the systems to indicate if things haven’t happened in the way they were planned or that there is a disconnect somewhere. Eighty percent or more of activities on the hangar floor aren’t being controlled and managed from the business systems or from the available data.
Ubisense has created a solution, SmartSpace, which helps close that data gap to manage the activities that are completed on the hangar floor and integrate with the business systems and records. Therefore, the data contained and managed within the business systems is now connected to actual events on the hangar floor (Figure 2).
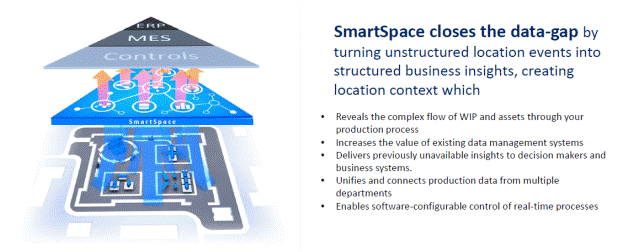
Figure 2 – Closing the data gap
HOW A DIGITAL TWIN CAN HELP YOUR BUSINESS
Perhaps the first thing to establish is what is meant by the term ‘digital twin’. Digital twins come in lots of different guises. There are probably more than five different types of recognizable digital twins and these include product design, manufactured product, plant design, plant equipment and control room. Each of these digital twins reflects the activity of the user or business and helps users to perform their tasks more efficiently and at lower cost.
Imagine if you were able to send a real time demand for technicians to help on a particular task that is in a specific zone on the aircraft. Imagine also if the business systems were able to direct the technicians with the right skills, experience and in the right location to help complete the task. This is currently being achieved in other sectors where they have already adopted this technology.
So how are we able to build this technology into the MRO environment? Initially a digital twin of your business is created reflecting the infrastructure and the activity completed within the environment, enabling users to see exactly what is happening on the hangar floor.
A 3-dimensional model of your business is created in SmartSpace to replicate the infrastructure within the hangar environment that enables the user to track material, tooling, components or tasks within that environment in the model. This is the initial aspect of starting to build a full digital twin of your work environment, creating an image of what is being done real time.
USING LOCATION TO DRIVE THE BUSINESS
In other sectors, location is already being used extensively. In the sports world and in particular football, all players have an embedded tag to track their activity. Initially this was used to show TV audiences who the individuals were as well as providing statistics on their performance. Now this same technology is used extensively to review and change plays, depending on how successful they were. This is now a key element in the sports world to gain a competitive advantage.
Similarly, in other types of business, location has been used initially to track where ‘things’ are in real time, then, once the tracking is fully operational, for analysis and extensive review to gain a competitive advantage by improving business efficiency. I believe the same process will work within the MRO sector with initially ‘things’ being tracked then rapidly followed by significant business improvements.
How can we adopt what has already been accomplished in other sectors to rapidly implement a location-based solution in the MRO business and gain significant benefit?
WHAT’S THE VALUE OF A DIGITAL TWIN AND LOCATION IN AN MRO?
So location has been used in other sectors to drive real efficiency gains, but what is the real value within the MRO environment?
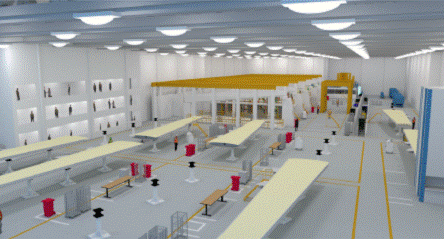
Figure 3 – Manufacturing facility Digital Twin
The first step in this is to create a digital twin of the facility. Figure 3 shows an example of the digital twin for a manufacturing facility in the UK where a three-dimensional model has been created to reflect the actual hangar.
Within the model, the digital twin enables the business to control what happens to objects and processes in that environment.
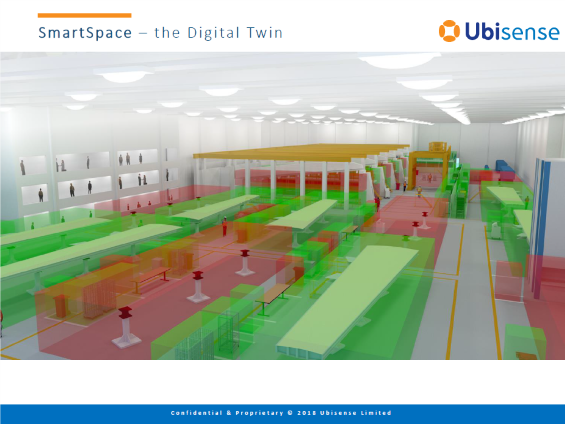
Figure 4 – Operational Digital Twin
Figure 4 shows how the digital twin works, there are areas or zones, that are expecting to see work orders, which could be an assembly or a maintenance activity, that are being managed. So, if things go somewhere where they’re not supposed to go, messages can be sent and that whole process can be managed within the solution to get a perspective of what needs to be done, what is being controlled from the system of records or being controlled from the ERP system, to make sure that what gets done on the factory floor is what was planned. This effectively closes the data gap shown in Figure 1 and joins the planned activities to real world actions.
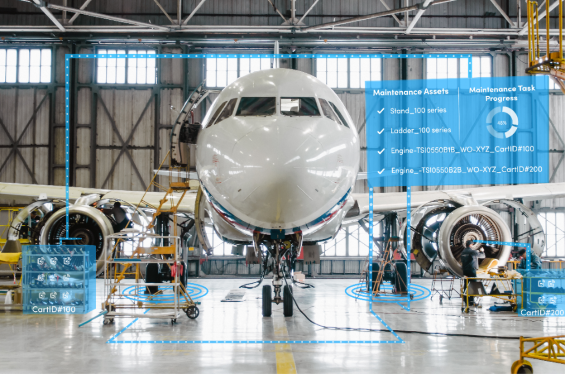
Figure 5 – Maintenance Hangar Digital Twin
Figure 5 illustrates a similar solution within a maintenance environment showing information about components, tooling or tasks in real time and visible to all SmartSpace users.
THE MRO DIGITAL TWIN
Within the MRO environment, there are four key pillars.
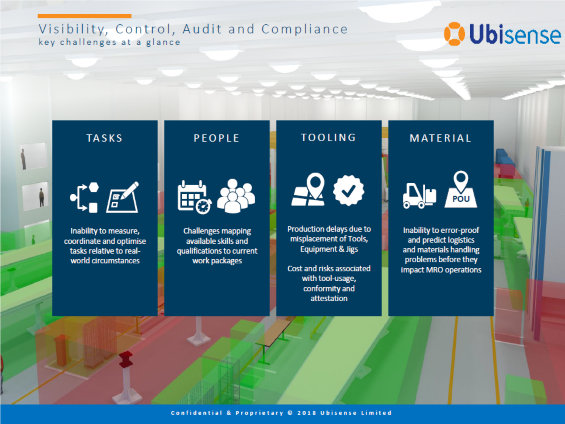
These pillars are: the tasks that should be managed within the MRO processes; people and the various skills that are required to perform the tasks; the tooling required for each task; and the material required. Each of these pillars is discussed in further detail highlighting some key components and areas where value can be realized.
Tasks
Looking first at the tasks, here are some examples of how tasks can be scheduled and coordinated effectively within an environment, where the user creates the rules within SmartSpace to manage what gets done, when and how.
- Plan efficiently using actual data;
- Record actual vs planned activities;
- Record findings over time, resource, skills and materials for information that can be used in future planning;
- Execute consistently;
- Save the plan template for training, insight and future use.
People
This is about making sure that the right people are available and, if the business allows it, to track those people to know where they are. In most cases, people get allocated to particular work orders or tasks so it’s possible to know where they should be. Here are a few examples of what can be captured and monitored to review what is working well and what is not working well within that facility and returning the value through the business.
- Check/monitor skills required to complete planned tasks;
- Check/monitor currency of qualifications of those with correct skills;
- Allocate specific technicians to tasks;
- Manage and control enablement of Electronic Task Cards for technicians on mobile devices;
- Record time spent on tasks;
- Sign completion/closure of tasks.
Tooling
This can be managed through a digital twin and is one area where many of those adopting this technology start, by managing how they issue the tools out and where the tools are to ensure that they are always controlled. Again, here is a sample list of what can be achieved to ensure that tooling is available, conformant and able to be located:
- Ensure tooling is serviceable;
- Ensure tooling is available;
- Deliver tooling to zone prior to need;
- Confirm use of tooling;
- Return tooling to storage.
With ground support equipment (GSE) or larger more expensive tooling, SmartSpace can help to understand how these tools are managed including their utilization. Another example could help manage when a tool is issued to one individual but, instead of the tool going back to the tool store, it can be transferred to another individual but still be controlled through the tooling inventory management process. This is possible because, with SmartSpace, the user knows where the different people are and knows where the tools are so that people can exchange tools easily and in a controlled manner within this environment. With real-time tracking of GSE, a team lead awaiting a specific GSE can be notified instantaneously when it becomes available and claim it faster, thus reducing the overall span-time of a repair.
Material
It is always important to know where material or components are. Is it at the right place at the right time so that the user can pre-draw the material and get it to the point of use in a timely manner? The solution can also manage the store so that the business knows how much material is available (how many consumables or other types) and can manage that in real time as well as pull all that information together. Again, here is a short list of aspects of material management that need to be considered:
- Check material is available, if not place an order;
- Prepare material for delivery to zone just in time but prior to demand;
- Confirm consumption of material and recover possible lag time in replenishment;
- Arrange for return to store of unused stock.
SINGLE PLATFORM
All this information provides a single platform that delivers visibility to all internal processes and activities. This is shown in Figure 6.
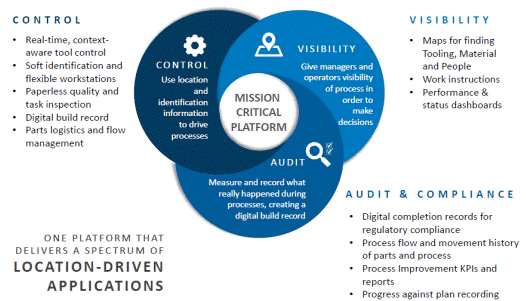
Figure 6 – SmartSpace solution providing control, visibility and audit
Many things can be tracked, so it is possible to see in real time where the various components are and at what stage the work orders are within that area, providing complete visibility of what is happening.
There is also complete control since, within SmartSpace, there is the ability to put controls in place enabling the business to build rules to monitor their critical processes, making sure that what gets done within the hangar floor is more efficient, flexible, profitable and safe.
Finally, there is audit and compliance. With SmartSpace the business can audit what has been done, when it has been done and who did it. A good example would be in the car industry; if there is a problem with a car and it needs a recall, traditionally that recall would cover, perhaps, a quarter of a million vehicles. Using SmartSpace, this can be significantly reduced to just a few thousand vehicles because historical data shows who performed the task, which tool was used and what other vehicles the tool was used on. So, it is possible to identify exactly where the problem is and which vehicles were potentially affected.
There are a number of examples where SmartSpace has already been used successfully within an aerospace environment. In one case, a customer had set an ambitious target to quadruple production within a two-year period and Ubisense was selected to assist with efficiency improvements and process waste identified as key opportunities for successfully achieving their rate increase. In other examples, a significant reduction in operational costs was achieved, comparing actual expenditure against plan, and for other customers the system delivered real time visibility of work in progress along with more efficient tool utilization and management. There were also improved turnaround times with some customers achieving as much as 20% improvement: that’s not only important for an MRO but also important for their customers who can reduce the amount of time the aircraft is out of service.
SAMPLE USE CASES
Perhaps the best way to understand where digital twins and SmartSpace might be useful for an MRO operation is by going through a few customer use cases. Hopefully, these will help readers see the potential that there is for them to start the process of building a digital twin.
It is best to select quick wins that will deliver real value and enable the organization to gain knowledge and confidence in the potential benefits. As you will see, there are many use cases that businesses can start to adopt, and I am sure that readers will be able to think of examples beyond the ones listed where they could potentially start to drive real value. When businesses begin using this technology, the most successful are those that implement one use case at a time but within the context of a long-term plan.
Also, think outside the box, do not just consider what other companies might already have done. As long as there is a way to capture information about an object and its location (RFID, barcode, BLE or other technologies) then it is possible to know where it is, where it has been and its history. The important thing is being able to understand the value of capturing this information and having the means to realize the value.
SUMMARY
MRO 4.0 has enormous potential that can be realized in all companies and that potential will be easier to realize by putting a system in place that can start to manage the business and its facilities on a real time basis.
Our experience at Ubisense, in other sectors where we have worked for many years and have been able to improve their processes and efficiencies, can be transposed to an aerospace and MRO environment to help MRO companies embark on this journey. One key point to remember is to go for easy wins, do not try to go for difficult challenges at first but use easier ones as part of a master plan to build and embed understanding in the business and start to build your Digital Twin as part of your MRO 4.0 future.
Contributor’s Details
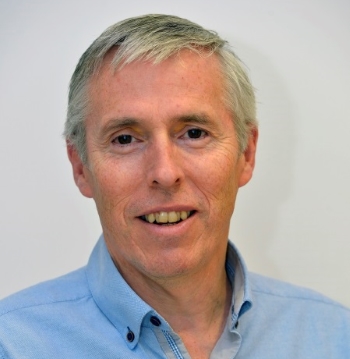
Hugh has now been working in Aerospace for more than 30 years and, prior to joining Ubisense, started his career in aviation after graduating with a doctorate in Engineering and, initially working for British Aerospace. Around 18 years ago, he created his own company, CoreData Limited, focused on helping airlines, MROs, OEMS and aircraft supply chain companies with solutions that could drive value from the large amounts of data they were accumulating. He finally sold the company to Rolls Royce.
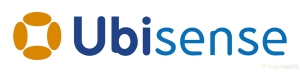
Ubisense
With offices in UK, France, Germany, North America, Canada and Japan, supported by a network of highly skilled partners around the globe, Ubisense has more than 900 customers across many sectors and has been influential implementing Industry 4.0 in many of those customers. Their solutions are based on powerful enterprise platforms, supported by a range of customer-led applications that use location to deliver a real-time digital twin of physical operations. This is proven to drive quality, increase productivity, manage complexity and reduce costs.
Comments (0)
There are currently no comments about this article.
To post a comment, please login or subscribe.