Articles
Name | Author | |
---|---|---|
Case Study: MRO Software Implementation Case Study at Aircraft Maintenance Services Australia (AMSA) | Clanci Ferguson, Business Development Leader, Aircraft Maintenance Services Australia, and Gerry Croarkin, Business Development Director, Rusada | View article |
HAECO’s journey to Mobility | Louis Wong, Enterprise Architecture Manager, HAECO | View article |
Column: How I see IT – Go paperless: write that down! | Paul Saunders, Solution Manager, Flatirons Solutions | View article |
Look – no hands! Voice Control for MRO | Jeff Pike, Head of Strategy and Marketing, IFS Aerospace and Defense Center of Excellence | View article |
Paperless Maintenance: The shape of things to come | Paul Saunders, Global Product Manager, Flatirons Solutions | View article |
Look – no hands! Voice Control for MRO
Author: Jeff Pike, Head of Strategy and Marketing, IFS Aerospace and Defense Center of Excellence
SubscribeJeff Pike, head of strategy and marketing for the IFS Aerospace and Defense Center of Excellence, looks at how voice control technology is set to disrupt the MRO workplace
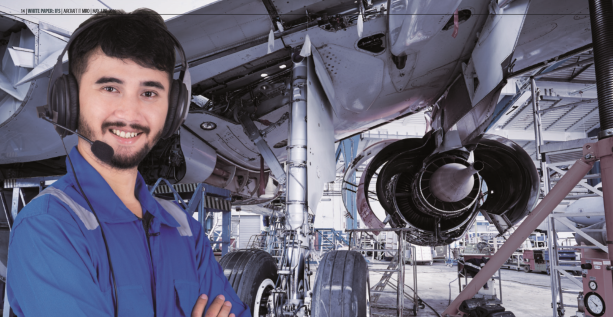
Civil aviation and defense maintenance engineers need two hands to work and two fingers to use a mobile device; not easy in any environment and certainly not in an engineering context. Voice recognition technology is becoming the next stage in mobile app enhancement for entering data, recording findings, instructing functions and ordering parts and materials: leaving the engineer’s hands free for maintenance duties and promising to bring huge changes to MRO, maintenance & engineering and the supply chain.
Working in restricted spaces is a common feature in a typical civil aviation or defense engineer’s daily routine. Most maintenance engineers have problems associated with physical access – having to work in very small spaces, cramped conditions and in uncomfortable climates or environmental conditions, aggravated by factors such as poor lighting or having to wear protective apparatus. Overloading the maintenance engineer – wearing safety kit and in the underbelly of an aircraft – with full information system (IS) functionality while working with limited room for maneuver, simply doesn’t make sense. Enter the development of next generation, apps-based ERP systems.
Mobility is already with us but what next?
The consumerization of IT for the aerospace and defense (A&D) industry and for aviation MRO continues apace, first with the arrival of mobile devices. Mobile devices offer one solution and are now commonplace in maintenance hangars – wearable technology has recently been trialed by both EasyJet and Japan Airlines to inspect aircraft on the ground. But just because you can use mobile devices, doesn’t always mean you should. Mobile applications offer a better platform than simply full ERP functionality on a mobile device for recording and viewing information which is quickly and easily accessible. Things such as asset history, a record of parts used or parts needed for repair and any notes of repairs performed, are displayed on an easy-to-understand interface – allowing engineers to be as efficient and effective as possible without the need to ‘down tools’ and report information back at base.
Mobile devices have significantly improved agility by placing role-specific applications, processes and information directly into the palm of your hand – the DoD (US Department of Defense) released its Mobile Defense Strategy in 2013 with the objective of creating a highly mobile workforce for greater mission effectiveness. While offering a solution to the problem of gaining essential feedback of specific operational information, mobile devices still need fingers to do the talking – the same fingers that are also needed to carry out essential maintenance.
Enter voice control technology. This consumer technology enables us to send a text, change the TV channel or alter the thermostat by talking to a smart device. So will voice technology usher in new ways of interacting with the ERP system in A&D engineering environments? I think so.
Management and maintenance on command
The list of potential benefits for using a voice system with mobile apps is impressive. Productivity, parts order accuracy and efficiency would all rise as a result of engineers no longer needing to down tools and take trips to report data back to base, or input data manually. More importantly, voice apps would be able to support airworthiness by making sure the right part is secured at the right time, streamlining the repair process and putting aircraft back in the air as soon as possible. Minimizing aircraft downtime in aircraft maintenance is essential – airlines and aircraft operators lose hundreds of dollars every second an aircraft is on the ground. This hands-free, heads down, approach allows engineers to focus on the task ahead, contributing to the quick sign-off for an aircraft while keeping to strict safety regulations. Here are some typical scenarios in both civil aviation and defense.
The signing off of aircraft has long been a problem in aircraft maintenance – the aircraft can’t take off unless approved by a maintenance engineer, which takes time. The process of having to remove safety kit and return back to a quieter environment in order to log vital information is time when the aircraft could be in the air making money or (if it is a military aircraft) supporting troops. The time spent could be costly, so it’s important for engineers to have access to a device capable of logging information immediately as soon as they see a fault on an aircraft. It’s easier when the tools help to exercise more control over the work environment, and process-driven actions in the hangar or in-theater do not have to be complex.
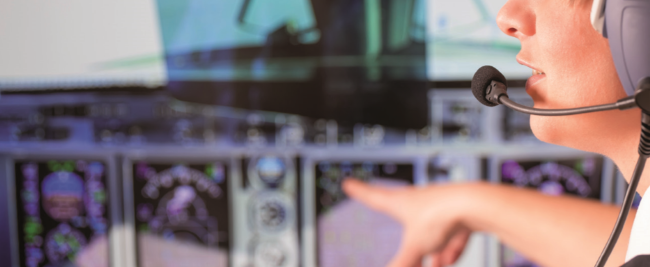
Voice recognition technology and mobile apps could transform the way engineers work. Engineers carrying out flight-line maintenance could ask their mobile device to report the tire pressure of an aircraft on the tarmac in front of them. This information could be fed back from the device – and compared with the actual tire pressure required for the specific aircraft. If the actual pressure was incorrect, the engineer could then verbally instruct the system to assign a maintenance task to the wheel in question.
In the defense environment, voice control offers an opportunity in reliability and maintenance. Assets with a logged, but not operationally critical, structural fault require regular eyeball checking. For example, when an infantry fighting vehicle returns from operations, health usage monitoring systems (HUMS) might identify a particular part that requires regular attention. On inspection the engineer could report the latest status of the part with a simple voice command – be it on land, sea or in the air.
In-hangar or at-base maintenance could also be revolutionized, with engineers working on aircraft or equipment able to quickly query the quality, status and lifespan of any part verbally; then check the availability of spares, all completely hands-free.
Talk to your ERP
IFS Labs, part of IFS Research and Development tasked with finding new ways to push the boundaries of ERP system capability, often looks to the world of consumer technology for inspiration. The Labs has designed a mobile app called IFS Intelligent Personal Assistant (IPA), that lets the user control IFS Applications by their voice, via a smartphone or tablet.
“Taking inspiration from intuitive web and social media applications and incorporating them into IFS Applications, IFS Labs helps pioneer the company’s continual focus on improving enterprise application usability – setting new standards in enterprise software design for its customers,” says Martin Gunnarsson product director, IFS research & development.
Having looked closely at Apple’s Siri and Microsoft’s Cortana – the apps A&D personnel are already using in everyday life – IFS Labs has now designed the IPA for people who want to search for data and update data in IFS Applications using voice commands with mobile apps. The IPA uses a standard software development kit for speech to text and text to speech, with the infrastructure for fetching data from IFS Applications built on current IFS cloud structure.
It’s all about use – so there is still work to do
Neither A&D nor commercial aviation is immune from the ripple effect of consumer trends as support solutions become less about Information System (IS) infrastructure and more about open access and ease of use. Current technology such as noise cancellation headphones and throat microphones allow voice recognition technology to work functionally in most environments, for example dealing with background noise on the airport tarmac or during frontline military operations. With voice apps, aircraft no longer have to wait long to be signed-off – engineers can report what they see there and then – rather than having to wait to get back to base to detail information – and get the plane back in the air as soon as possible.
Right functionality, right time
Voice technology in aircraft maintenance and engineering will result in more efficient maintenance, without investment in complex IT training – speeding up the maintenance process, and ensuring that aircraft spend more time transporting paying customers and that equipment is ready to support mission-critical military operations – not sitting idle on the ground waiting for an engineer’s attention.
Contributor’s Details
Jeff Pike
Jeff has worked over 30 years in A&D and IT including 20 years as a Royal Air Force senior officer specializing in management of major IT programs; defense logistics business transformation; and logistics operational research. He has 10 years commercial Business Development experience, in enterprise software, within global defense markets. Jeff is a supply chain optimization and logistics business transformation specialist with responsibilities including supporting global IFS A&D marketing, industry marketing and business development.
IFS A&D
IFS develops and delivers enterprise software for the Aerospace and Defense (A&D) industry. IFS Applications supports full-spectrum enterprise, project and program-centric manufacturing and vendors serving the A&D sector; heavy, complex, and component maintenance; and repair and overhaul (MRO) for civil aviation, military and service providers, as well as line maintenance or at-platform/asset support. IFS customers in A&D include BAE Systems, Lockheed Martin, General Dynamics, SAAB, GE Aviation, HAL, and Emirates.
Comments (0)
There are currently no comments about this article.
To post a comment, please login or subscribe.