Articles
Name | Author | |
---|---|---|
A better view of process in a paperless environment | Neal Reagor, Director Planning and Commercial Services - EAMS | View article |
Column: How I See IT – COVID-19: Impacts and progress | Allan Bachan, VP, Managing Director, MRO Operations, ICF | View article |
Looking into the future at Etihad Airways | Borja Dosal Roiz, Avionics Engineer / CAMO Fleet Management at Etihad Airways | View article |
IATA’s Digital Aircraft Operations Initiative | Iryna Khomenko, Manager, Operational Efficiency, IATA SFO, IATA | View article |
Case Study: MRO IT System Modernization at ATSG. | Paul Harding, Director, Information Technology, Air Transport Services Group | View article |
Looking into the future at Etihad Airways
Author: Borja Dosal Roiz, Avionics Engineer / CAMO Fleet Management at Etihad Airways
Subscribe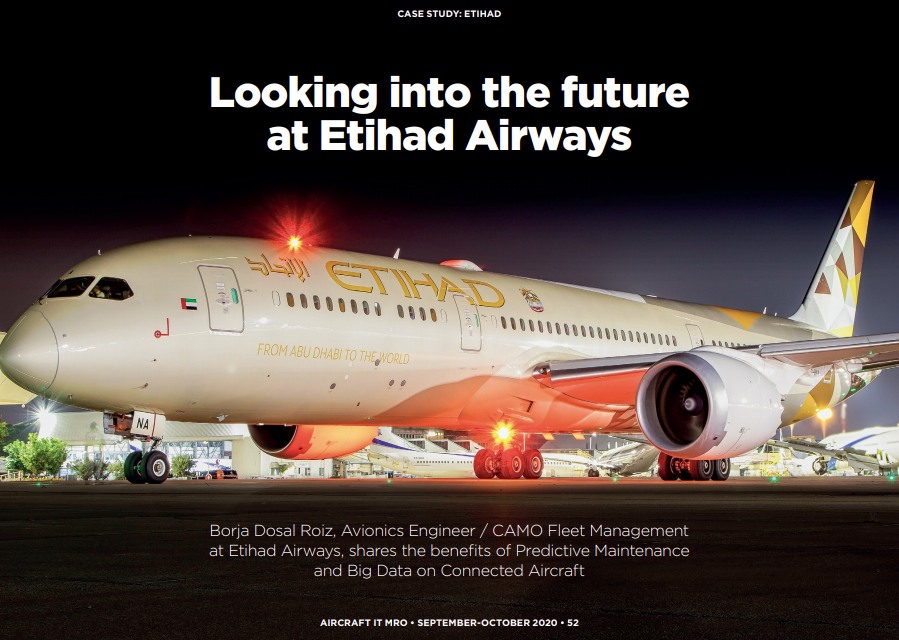
Borja Dosal Roiz, Avionics Engineer / CAMO Fleet Management at Etihad Airways, shares the benefits of Predictive Maintenance and Big Data on Connected Aircraft.
The plan for this article is to share with readers what Etihad Airways is planning to do in terms of predictive maintenance and big data on the connected aircraft. But it will first be useful to know about Etihad Airways and, in particular, the fleet.
ETIHAD FLEET
At the top of figure 1 is Etihad’s legacy fleet of Airbus A320 and Boeing 777 aircraft.
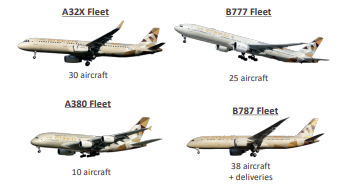
Figure 1
At the bottom of the figure is the new fleet. Etihad flies ten Airbus A380 and approximately 38 Boeing B787 with further deliveries scheduled over the next few years. But this presentation will focus on the Airbus A320 and what Etihad is doing in terms of predictive maintenance by using a software called Skywise Predictive Maintenance (SPM), which has been developed by Airbus.
SKYWISE AND FOMAX
Before we go into this, let’s consider a basic definition of maintenance and what kind of maintenance can be done on an airplane (figure 2).
First, there’s preventive maintenance. As we know, components have limited usage and we can replace them before they reach their end of life, based on flight hours, flight cycles or calendar days. But this would mean replacing the component too early.
Second, there is reactive maintenance which means replacing the component once it fails on the aircraft but, of course, that’s too late and will cause an operational interruption or delay.
Finally, there is predictive maintenance, which consists of predicting when a component is going to fail and replacing it before it causes a delay or operational interruption. Hence, the component will be removed right on time.
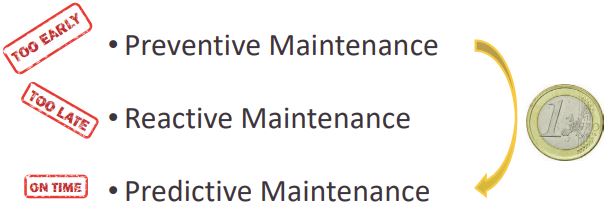
Figure 2
If we can move from a preventive maintenance model to a predictive maintenance model, the component will remain on the aircraft for a longer period of time and will only be removed right on time, avoiding unnecessary maintenance and saving costs.
What is needed in order to be able to do predictive maintenance?
The first requirement is big data. We need the aircraft to tell us what is going on and that means the aircraft needs to transmit thousands of parameters from its systems. The other requirement is to have algorithms, software and logic that will analyze the big data and, as an output, generate warnings and alerts that can be taken into consideration in order to perform a maintenance action on the airplane.
Big data needs special technology to extract aircraft parameters, and at Etihad we use FOMAX for this purpose; while for the algorithms that turn that data into useful information, we use Skywise.
FOMAX stands for Flight Operations and Maintenance eXchanger and it’s a new computer (figure 3.1) manufactured by Collins Aerospace that Etihad has installed on the Airbus A320 fleet.

Figure 3.1
On the front face of the FOMAX computer there are eight SIM card slots (figure 3.2), four dedicated to Airbus and four dedicated to theairline. To provide a rough idea, some sort of predictive maintenance would be possible without FOMAX but it would only allow us to monitor up to 400 parameters and generate up to 50MB of data per day. With FOMAX, it’s possible to monitor up to 24,000 parameters or generate up to 12GB of data per day. So, here is where Big Data comes into place.
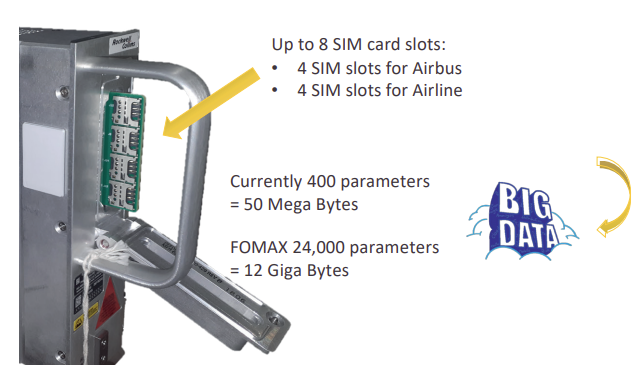
Figure 3.2
As shown on Figure 3.3, FOMAX transmits the data to Skywise through a 4G network at every landing. Skywise analyzes this data to generate warnings and alerts that the maintenance organization can take into account when performing maintenance actions on the airplane, like replacing a component, servicing the aircraft or refilling an aircraft system.
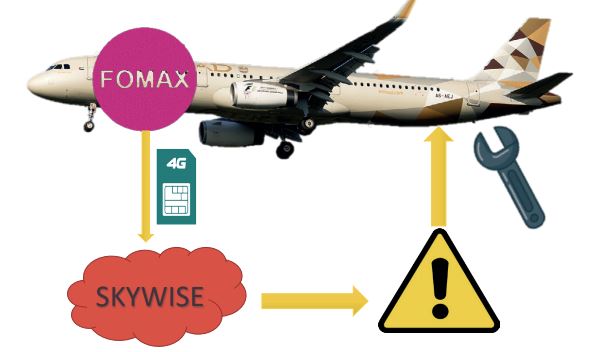
Figure 3.3
FOMAX FIRST INSTALLATION AND ACTIVATION
This first installation of FOMAX took place on an Etihad A320 in September 2018.
Figure 4.1 shows the associated wiring required to connect FOMAX to other aircraft computers and its location on the Avionics rack.
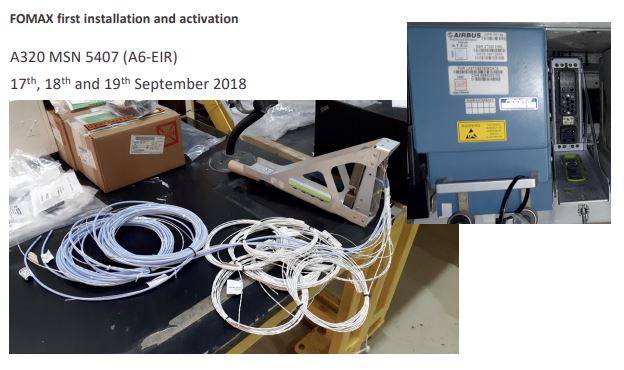
Figure 4.1
For the antennas, Etihad installed two 4G antennas near the passenger door in the forward section of the airplane (figure 4.2) – the purple cables in the top photograph are the coax cables that come from FOMAX, through the frame and up into the overhead compartment.
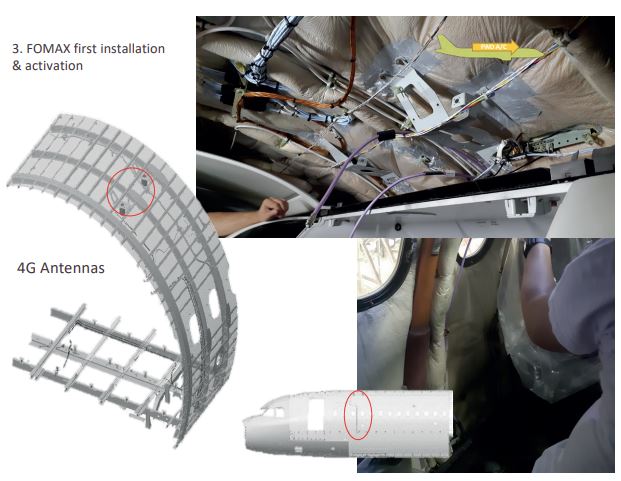
Figure 4.2
The two white brackets (also top photo and circled in diagram) are where the 4G antennas will be installed.
The circuit breaker (figure 4.3) is circled bottom left in the main CB panel of the Airbus A320 cockpit. As we are installing a new computer, we need to install a new circuit breaker.
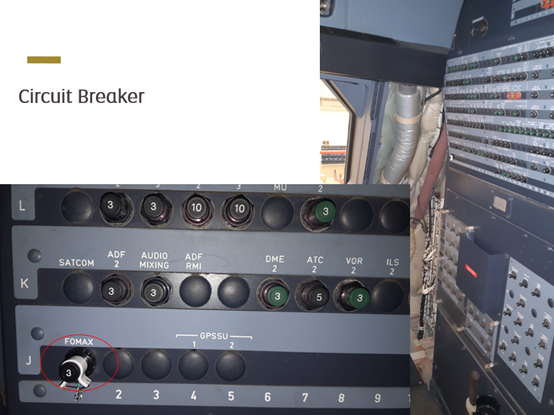
Figure 4.3
This is a view of the Avionics compartment from the forward cargo area and circled in red is the location of FOMAX (figure 4.4).
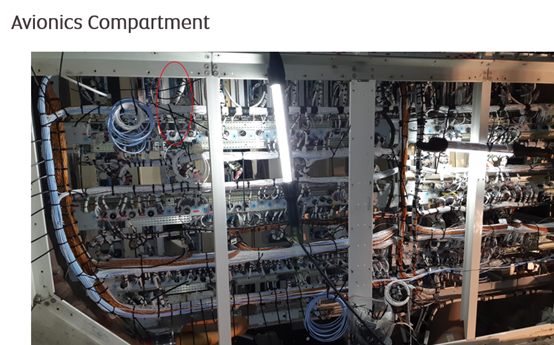
Figure 4.4
Once we have installed FOMAX, next we need to load the software onto the computer. For that, we used a portable data loader and the ARINC 615-A standard to accomplish the loading. During the installation we also install two new data ports. One is for software loading (ARINC 615-A), while the other is an Ethernet port used to connect a laptop in order to communicate with FOMAX using a software called LMF from Collins Aerospace (top left figure 4.5).
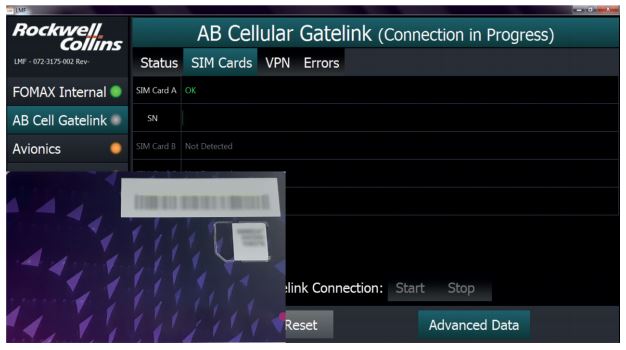
Figure 4.5
With this software, we can troubleshoot FOMAX, communicate with the computer, check the status of the FOMAX connection etc.
What figure 4.5 shows is the cross-checking of the SIM card serial number that is physically installed into FOMAX with the SIM card serial number that FOMAX is reporting as being installed. Once we have a match, we raise a Tech Request to Airbus in order to activate the SIM card and start the transmission of data.
THE NO FAULT FOUND DILEMMA
This is how the ‘No Fault Found’ (NFF) dilemma works. The predictive software tells us that the performance of a certain component is degrading and so a mechanic is sent to the airplane in order to replace this component. Once it has been removed, it will be sent to a shop where it will be tested but the likelihood is that those tests will result in a No Fault Found (figure 5.1).
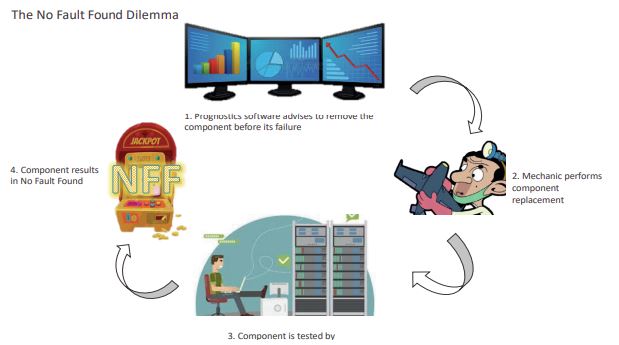
Figure 5.1
Airlines don’t like no fault being found because they are still charged for component testing. This happens because the component was removed in a degraded but not faulty condition, causing the NFF diagnosis.
Figure 5.2
The question is, how can the No Fault Found be avoided? Well, there are two options, as shown on figure 5.2.
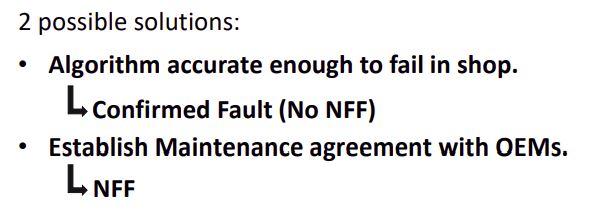
The first one, if the algorithm is accurate enough, will result in eliminating NFF events because the component will be removed in an almost faulty condition. Unfortunately, predictive maintenance algorithms are not always mature enough to achieve such level of accuracy and a quick maintenance action is required.
In a very few cases, the removed component could result in NFF. For these cases it is essential to establish a maintenance agreement with the manufacturer of the component so that they will accept an airline’s predictive maintenance alert as a valid reason to remove the component, in which case the airline will not have to pay for the no fault found testing.
CASE STUDIES
Before we look at any case studies, let’s consider how much a delay costs on an Airbus A320 (figure 6). On average, a flight delay can cost up to $9,000 per hour. Plus, the associated costs in the case of a flight cancellation, air turn back or aircraft diversion.
Figure 6 is a screenshot from Skywise Predictive Maintenance and each line seen on the screen represents a different predictive maintenance alert, applying to a different aircraft.
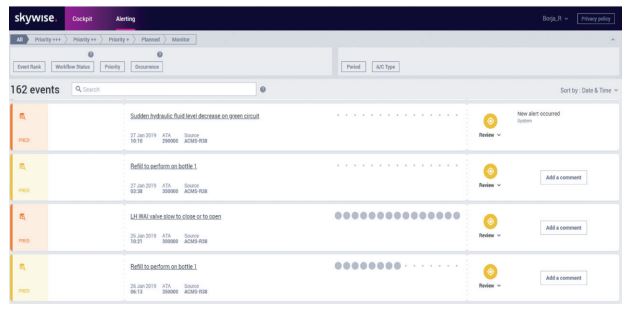
Figure 6
It shows the applicable ATA chapter, the title of the alert and the number of times that the alert has taken place over past flights. Once a user clicks on each of these alerts, they will see a graph, an evolution of the system and, based on that graph, it will be up to the airline to take a maintenance decision. With this I would like to make clear that predictive maintenance software will not tell us what to do. It will give us a picture or an overview of what is happening, with tailored maintenance advice provided, but it’s up to us (the airline) to decide what to do.
Now, let’s take a look at three different real alerts that were generated by Skywise and concluded in maintenance actions that increased Etihad safety, avoided delays and reduced fuel penalties.
Case 1: Oxygen Servicing
On the Airbus A320 Cockpit there are oxygen masks for the crew to use in case of an emergency (figure 7.1). The oxygen comes from a bottle located in the avionics bay and what we monitor on this alert is the amount of oxygen or the pressure inside the bottle.
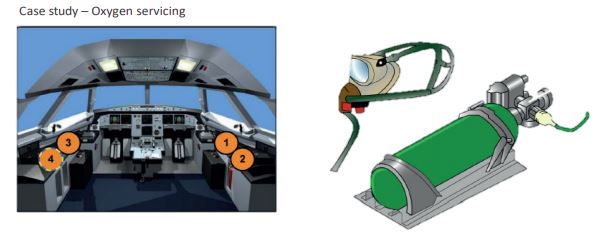
Figure 7.1
And this (figure 7.2) is the graph.
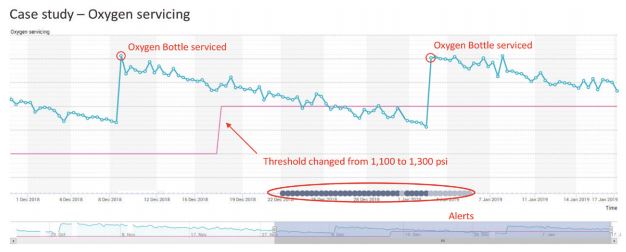
Figure 7.2
The horizontal axis shows the timeline and the vertical axis shows the amount of oxygen in the bottle. Each blue dot represents a flight and over the flights the bottle will lose oxygen because every time a new crew takes over the aircraft they will test the system and there will be a loss of the amount of oxygen in the bottle.
Each spike in the graph represents a maintenance action in which the bottle has been refilled. The purple line represents a threshold that can be modified so, when the amount of oxygen falls below the threshold value, alerts will be generated. In this case it’s up to engineering to take the necessary maintenance action; in this case, replace or refill the bottle with Oxygen.
Another example on oxygen servicing is the one below and, in this case, an example of what happens when we do not react right on time (figure 7.3).
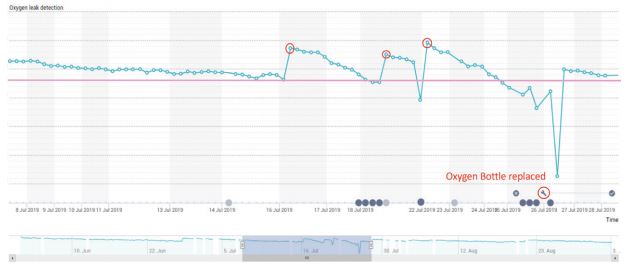
Figure 7.3
The bottle in this graph (figure 7.3) has been losing oxygen regularly over a period of one week. Suddenly, as it reaches the threshold, the decision is taken to refill it. After just a few flights, it has lost an amount of oxygen again and it is refilled again; a sequence that is repeated each time the amount of oxygen falls below the threshold. This is now the third time that the bottle has been refilled in just a few flights.
At this point, we should have stopped refilling the bottle and started looking for leaks because clearly something was wrong. We didn’t, and in just a few more flights the amount of oxygen fell to a critical level, after which we found a leak in the bottle itself and then it was replaced.
Case 2: Low Pressure fuel shut off valve
The Low Pressure fuel shut off valve (LP SOV) is a valve that plays the critical role of opening the fuel supply to the engine (figure 8.1).
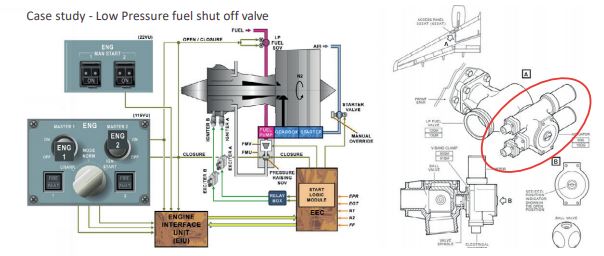
Figure 8.1
This valve is commanded by a dual motor actuator. On figure 8.2 we can see how the valve was taking around 1 or 2 seconds to be operated by the actuators, but suddenly this time extended to approximately 10 seconds, giving a clear indication that the operation of the actuators was degraded.
After a few flights showing a degraded performance, we decided to replace the dual motor actuator.
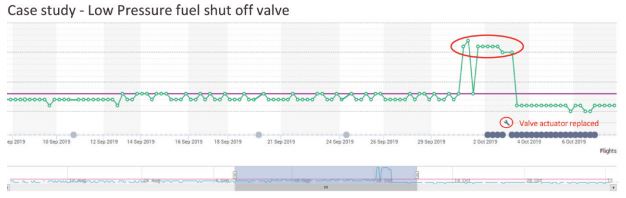
Figure 8.2
Figure 8.3 shows the test bench results of the dual motor actuator. According to the shop report “unit failed operational bench test”, which confirmed the predictive maintenance alert. In this case, the component was replaced right on time and just before its failure on the aircraft.
Furthermore, the report states the following about the motor actuators “R1 operates good in open direction and fails operation to close”, while the other motor actuator “R2 operates good in the open direction and has a rough operation to close”. So, clearly the valve was having trouble to operate in the close position and this was due to the degraded operation of the dual motor actuator.
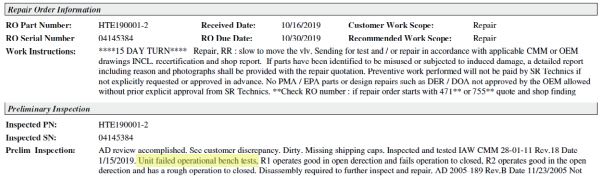
Figure 8.3
Case 3: Wing anti-ice valve
In order to avoid icy conditions affecting the leading edge of the wing, hot air can be diverted from the engine to the leading edge. This function is controlled by the wing anti-ice valve (figure 9.1).
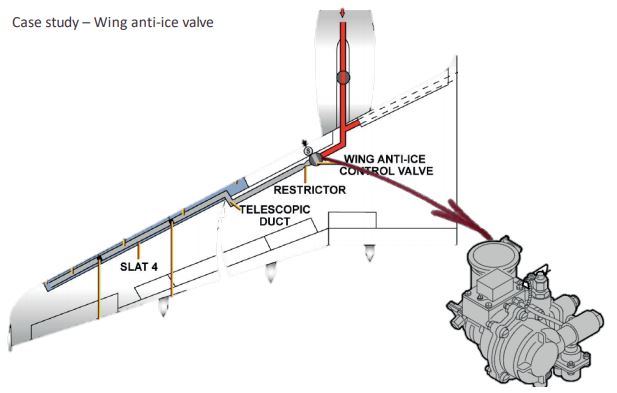
Figure 9.1
This alert will tell us if the valve is behaving abnormally. This is a good example because, if the valve is operating abnormally and there is no time available to replace it or no spare, the valve can be kept in the open position through an aircraft maintenance task. But if that is done, hot air is being channeled through the leading edge of the wing continuously which means an extra bleed of air coming from the engine which, in turn, incurs a fuel penalty estimated to be 80kg of fuel per flight hour. So, just by monitoring the functioning of this valve, not only can we avoid a delay but a fuel penalty too.
Figure 9.2 shows that the valve was operating abnormally but on an intermittent basis..
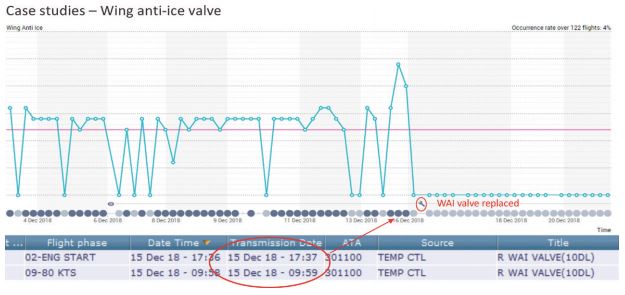
Figure 9.2
In this specific case, the two spikes (circled red) recorded times when the valve operated abnormally which triggered two Airman fault messages. We decided to replace the wing anti-ice valve. As can be seen on the graph, the newly-installed valve operated perfectly after being replaced, and when the removed valve reached the shop, tests confirmed that it was faulty.
CONCLUSIONS
Etihad is an Abu Dhabi based airline and Formula 1 is the biggest sporting event that takes place in Abu Dhabi every year. For that reason, I wanted to make an analogy between the evolution of Formula 1 pit-stops over the years and how aircraft maintenance will evolve in the future.
Figure 10 shows a video of a pit-stop in the 1980s, when it took 16 seconds to service an F1 car. By 2017, that time was down to 3 seconds. This is how I think predictive maintenance is going to change the way we do aircraft maintenance today compared to how we will do it in the future.
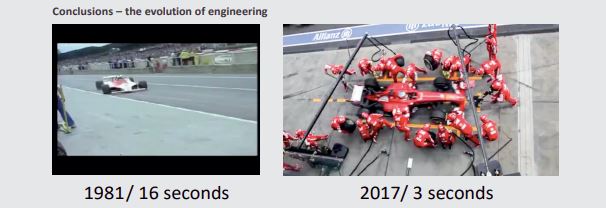
Figure 10
Contents
e-enabled aircraft provide unprecedented data volumes, but how are airlines using this big data to improve operational efficiency? Etihad Airways outlines the benefits from integrating data services into new maintenance methodologies to predict aircraft failure.
Contributor’s Details
Borja Dosal Roiz
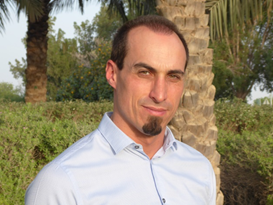
Borja Dosal Roiz obtained a Business Management degree in 2002 and an Aeronautical Engineer degree in 2007, specializing in Air Navigation. He started his professional career in 2007 working for Iberia Airlines followed by Spanair Airlines and British Airways, always holding the position of CAMO Avionics Engineer. Finally, in 2013 he settled down in Abu Dhabi and currently continues his Avionics Engineering endeavors working for Etihad Airways.
Etihad Airways
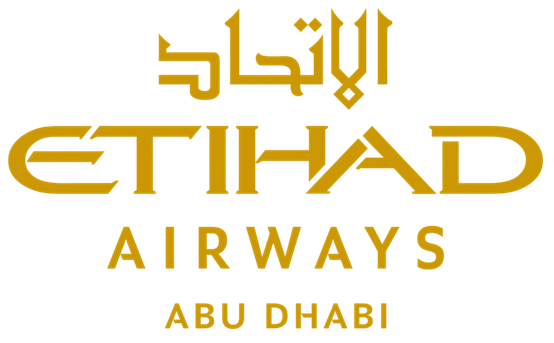
Etihad Airways is a national airline company of the UAE headquartered in Abu Dhabi. The airline operates more than 1,000 flights per week to over 80 passenger and cargo destinations in the Middle East, Africa, Europe, Asia, Australia and the Americas. As of August 2020, the Etihad fleet consists of a mixed fleet of Airbus A320/321, A380, Boeing B777 (inc freight types) and B787.
Comments (0)
There are currently no comments about this article.
To post a comment, please login or subscribe.