Case Study: Lufthansa: Digital Flight Deck
Author: Matthias Schmitt, Flight Operations Engineering, Lufthansa German Airlines, and Heidi Brockmann, Product Manager and Senior Consultant, Lufthansa Industry Solutions
Subscribe
Digital Flight Deck
AIRCRAFT MANUFACTURERS FLIGHT OPS DOCUMENTS
Readers will know that manufacturers provide various manuals with aircraft, such as FCOM (flight crew operating manual), MMEL (master minimum equipment list), AFM (aircraft flight manual) and QRH (quick reference handbook) – this latter is normally paper based and in the cockpit, so we’ll leave it out for this case study because it’s more interesting to show how you manage to get an FCOM to an OM (operating manual) Part B or vice-versa. The FCOM contains general information such as aircraft systems, procedures, limitations, performance and the operating engineering bulletins. The Master MEL is also straightforward; it’s just a minimum equipment list (MEL) albeit, the original equipment list prepared by the manufacturer. The aircraft flight manual includes the CDL ( configuration deviation list) – one chapter for the OM Part B.
OM PART B BASED ON EASA OPS AMC3
That is FCOM but there are also the European regulations (EASA OPS AMC3) – AMC (applicable means of compliance) – and the regulation for the OM Part B, known as ORO ( ORGANISATION REQUIREMENTS FOR AIR OPERATIONS) 100 Operations manual – general. The underlying objectives of this regulation are, first, administration and control of the Operations manual. Also in the regulation are aircraft operating matters, type related, taking account of the differences between aircraft types and classes, variants of types, and the definition of headings. At the next level there are route/role/area and aerodrome/operating site instructions and information including instructions and information relating to communications, navigation and aerodromes/operating sites including minimum flight levels and altitudes for each route. Plus, of course, there are the training syllabi and checking programs. The problem is that airlines can end up running two manual sets that both require regular updating and harmonizing, especially in areas where they overlap. It was this challenge that drove the business case for Lufthansa to use a documentation solution that would manage both manuals from one source to ensure that they were always in step.
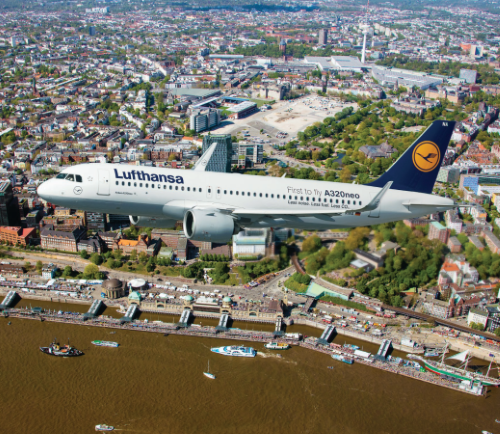
BUSINESS CASE
For the business case, the consideration for Lufthansa is that their Flight Operations have to match a lot of requirements concerning construction and presentation of the manual. The authorities demand that Flight Operations provide an OM Part B; so the requirement for Lufthansa Flight Operations is to build up standards to harmonize OM Part B with manufacturer manuals wherever they addressed the same challenges, e.g. standardization for pilot training. For every European airline, it’s a challenge to bring the FCOM and OM Part B together. To match these requirements, a smart software solution is needed – and that is the nub of this article.
FCOM VS OM-B; FOR EXAMPLE WITH THE A350
To illustrate this, we’ll use the example of the Airbus A350.
Figure 1
On the left of figure 1 there is the manufacturer’s manual including the FCOM with the top-level structure of the chapters and, below that, the master MEL which includes the chapters you know already. On the right is the OM Part B (OM-B) based on the chapter level: the challenge is how to match items from the FCOM within the chapter structure of the OM Part B.
So, let’s start with the master MEL, the minimum equipment list which, in the OM-B, can be found under the same heading ‘Minimum Equipment List’. You’ll find there all the information from the manufacturer (MEL items, operational procedures) but transferred into the OM-B structure.
Figure 2
Similarly with the other chapters in the FCOM (figure 2), Interface search, General information, Aircraft Systems, Limitations, Performance… they all have their equivalents in the OM-B. Interface Search is to be found in the OM-B chapter ‘Aircraft Systems’ which also contains the Aircraft Systems information from the manufacturer’s FCOM; General Information is usually in OM-B chapter ‘General Information and Units of Measurement’. Procedures in FCOM are interesting because the overall ‘Procedures’ heading doesn’t exist in OM-B. The FCOM chapter ‘Procedures’ includes Normal Procedures and Abnormal Procedures whereas in OM-B, ‘Normal Procedures’ includes Standard Operating Procedures as well as Normal Checklists, Tasksharing, Supplementary Procedures. After all of the ‘Normal’ procedures, OM-B has ‘Abnormal and Emergency Procedures’.
Essentially, OM Part B includes the same content as FCOM but in a different order and all at the same structural level.
DOCUMENT PROCESS
Figure 3
The business or documentation process used to drive both manuals from a single source is one with which readers will be familiar (figure 3). The manufacturer’s manual is imported, a comparison is made with the previous revision and changes are transferred into the working document (part of the import process). The content will be edited where necessary to edit Meta data or to change descriptions. The next step is to start to make a revision including undertaking quality assurance and freezing a revision before, then, publishing that revision. It’s possible to publish a revision, generate a comparison with the previous revision and store the published revision. The next step is a new one, the Transformation. If you have stored all your published revisions, it’s possible to choose a fleet and to choose a target pattern; then the latest revision is set as default but with the option to go back to older revisions. The result is a transformation from, say, an FCOM, to a single source publication.
DOCUMENT TRANSFORMATION MODULE
To create this mapping between different document structures a transformer module is needed that requires, on
an administrator level, a pilot or flight ops engineer who understands the content of the FCOM/OM-B; who creates the default mapping; chooses the document type, for example, in FCOM or the master MEL, and creates the target mapping to be saved in a transformation file, say, ‘FCOM to OM-B’ – the user can choose the name. At the Author level it’s possible to use this pattern to create a transformation publication. Choose a fleet, choose a target pattern such as ‘FCOM to OM-B’ above, override the default latest revision, if requested, to generate the transformed publication. That’s a necessary point to avoid redundancy, having two documents in the content management system that are nearly the same; because you now have the content of both documents but each in a different order (see above).. With a pattern we use the published result to switch the order.
CONCLUSION
In conclusion; the objective for Lufthansa is that flight operations need the capability to match these different requirements in a smart software solution as an integrated process. They don’t want to work with two kinds of documentation to have the FCOM on the one side and OM Part B on the other side where they have constantly to match them with each other to ensure consistency. They want to work in FCOM or OM-B and to get the results and have what might be described as a ‘magic button’ to publish in FCOM or OM-B, whichever is appropriate, but from the single source. That’s the plan – to create a reusable default pattern to publish and update different manuals from a single source. That will make it possible to handle future structure changes with Lufthansa requirements.
Note – Airbus FCOM structures
With regard to Airbus FCOMs, with an A320 FCOM or A330 or A340 FCOM, the structures are not the same, they are in a different order. Airbus is trying to harmonize the FCOM structures and using the A350 structures as the basis so that all other FCOMs will soon be harmonized in the same way as the A350.That is why we have used the A350 as the example to give readers an idea how this pattern could look.
Contributor’s Details
%20photo-sm.jpg)
Matthias L. Schmitt
Matthias joined the aviation industry in 1991 shortly after graduating in Aeronautical Engineering. He has held various positions within Lufthansa German Airlines flight operations support divisions; for the last ten years heading a team of flight operations engineers preparing Operations Manuals with a focus on type related information. Here, Matthias supported the company’s move from paper to a paperless world and introduced a XML-CMS based manual production for multi-platform use.
%20photo-sm.jpg)
Heidi Brockmann
Heidi is a graduate in Computer Science who joined Lufthansa Industry Solutions in 1997. She started her professional career in several technical documentation projects in the Aviation environment from development to consulting, project management up to product management, balancing customer related requirements with IT specific implementation for successful introduction projects. Driven by the incorporation of latest technology, the way to a paperless environment based on a knowledge management approach continues to be her focus.
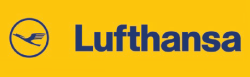
Lufthansa
Lufthansa is the largest German airline and, when combined with its subsidiaries, also the largest airline in Europe,
both in terms of passengers carried and fleet size. It operates services to 18 domestic destinations and 197 international destinations in 78 countries across Africa, the Americas, Asia, and Europe, using a fleet of more
than 270 aircraft. Combined with its subsidiaries, the group has over 615 aircraft and, in 2014, carried over 106 million passengers.
Lufthansa Industry Solutions
Lufthansa Industry Solutions is an IT service company for process consulting and system integration. This wholly-owned subsidiary of Lufthansa Group supports its customers with the digital transformation of their company. Its customer base includes both companies within Lufthansa Group as well as more than 150 companies in various other industries. Lufthansa Industry Solutions emerged from Lufthansa Systems AG on April 1, 2015. The group of companies employs around 1,200 members of staff at several branch offices in Germany, Switzerland and the USA.
To post a comment, please login or subscribe.