Articles
Name | Author | |
---|---|---|
Case Study: Lufthansa fuel saving | Tom Duddeck, Manager Fuel Efficiency, Lufthansa German Airlines | View article |
Case Study: ETL: The move from paper — Part 2 | Rob Woods, Head of Engineering, Air Arabia Maroc, Dave Cooper, Line Maintenance Manager, British Airways Cityflyer, and Cameron Hood, CEO, NVable | View article |
Case Study: Icelandair Fuel Savings | Einar Ingvi Andrésson, Manager, Fuel Efficiency, Icelandair | View article |
Qatar Airways Live Flight Tracking | Stephen P. Carroll, Flight Operations Project Manager, Qatar Airways | View article |
Case Study: Lifting the load | Brian Watson, Manager Weight and Balance, Alaska Airlines | View article |
Column: The World according to IT and me.. So… Apparently something happened in June | Paul Saunders, Solution Manager, Flatirons Solutions | View article |
Case Study: Lufthansa fuel saving
Author: Tom Duddeck, Manager Fuel Efficiency, Lufthansa German Airlines
SubscribeLufthansa fuel saving
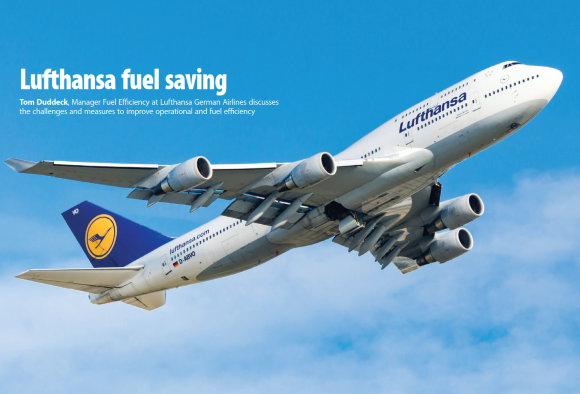
Tom Duddeck, Manager Fuel Efficiency at Lufthansa German Airlines discusses the challenges and measures to improve operational and fuel efficiency
FUEL EFFICIENCY AT LUFTHANSA AIRLINES
It’s a key issue for airlines the world over and so, in this article, I want to share with readers some of the programs to drive fuel efficiency at Lufthansa Airlines. In particular, I’m going to focus on our use of post-flight analysis tools. And, to put this case study into perspective, I’ll share a little about our fuel efficiency efforts, the type of projects we are targeting in our department in general, and Project OMEGA, the implementation of the Honeywell Aviaso Fuel Efficiency Tool in Lufthansa, in particular. Last but not least, I’ll share examples of what we have done so far with the tool.
First, let’s start with an overview of fuel costs versus operating result in Lufthansa Group (Figure 1) as an indicator of why we needed to undertake a fuel efficiency program.
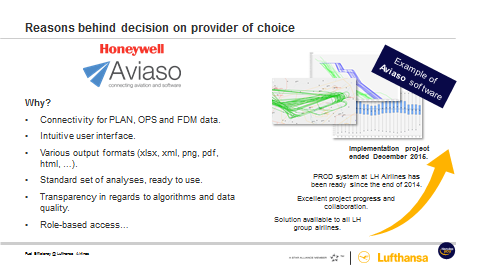
Figure 1
2015 was a good year for the airline industry and for Lufthansa because the price of fuel was at an all-time low, enabling us to achieve an operating profit of about €1.8 billion. However, while fuel prices are falling, fuel costs overall did not decrease that much and, for Lufthansa, fuel cost is about €6 billion every year. Also, as you can imagine, as soon as the price of fuel starts to rise again, things will be as before. There is an easy calculation of additional profit that can be gained if fuel cost can be reduced. On the graph in Figure 1, that projection is the dotted line which shows that the impact of a 0.5 percent saving on fuel costs per year could generate an additional 17% on operating profit; a huge gain. Airline operators should definitely think about fuel efficiency because it is very beneficial for the business.
A focus on fuel efficiency
At Lufthansa, we started some years ago with a fuel efficiency department and, today, there are about 40 people working there full-time covering several projects, though we do not implement all of them by ourselves. We collect the ideas for these projects, set them up with the appropriate responsible departments, follow up and evaluate them after they have been implemented. There are several areas in the business where fuel efficiency measures can be implemented. Obviously, Flight Operations is the biggest one because that is where the fuel is burned; so there are several projects in there. Then there is Network and Ground which indirectly affects fuel burn as well as Technical Performance, to determine how well a plane flies. And, in Lufthansa Technik, we have some of the largest MRO partners in the world. An obvious area for a fuel saving program is Weight Reduction and there are a lot of projects in that field plus, of course ACT/ATM (air traffic control/management) especially in Europe with SESAR (Single European Sky ATM Research), there are a lot of things that can be done. All of this adds up to over 1,200 projects targeting fuel efficiency and other efficiency measures in the Lufthansa Group. Our department doesn’t only cover Lufthansa but also group airlines in addition to the specific teams in those group airlines; we collect all the projects to avoid doing any project twice within the group.
At Lufthansa Airlines alone, we have some 200 projects already implemented or in progress which is forecast to have generated some €140m saving in 2015. In short, the importance of fuel efficiency is very significant. That said, we have to recognize that we have more or less reached the limit of what can be achieved with the current approach that we have used over the past few years. So we now distinguish programs by whether they follow that conventional approach or a more systematic approach (see Figure 2).
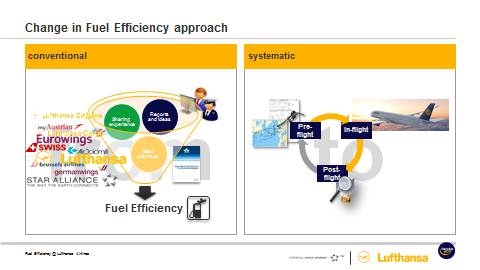
Figure 2
The conventional approach simply looked to collect ideas from colleagues and evolve fuel efficiency projects from that. Also, Lufthansa Group is one of the largest airline groups in the world and, with the Star Alliance, has a lot of partners around the world so we share experience within the group and with partner airlines such as United Airlines and Air Canada, and a lot of good ideas come from those shared experiences. Of course, we also have ‘best practices’ from IATA, ICAO and so on. All of this contributes to collecting fuel efficiency ideas from people. However, we felt there was a limit to what can be achieved with that approach. So, we had to think about a new approach which I would call the systematic approach.
We divide this systematic approach across the three main phases of a flight. Pre-flight, with all the planning, dispatching and everything that has to happen before a flight can take-off; in-flight, when the fuel is burned and the aircraft itself can be managed; and, what’s new to our considerations, post-flight where we collect all the data gathered from the preceding phases, put them together and systematically analyze them to discover and reveal any fuel efficiency gaps. After that, we implement measures to deal with those efficiency gaps, which gives us that systematic approach to continually improve our fuel efficiency measures. That said, ideas from colleagues are still welcome; the connection between both approaches is what will drive further progress.
PROJECT OMEGA – HONEYWELL AVIASO FUEL EFFICIENCY
Post-flight analysis is the tool used at Lufthansa within Project Omega and, for that, we have implemented the Honeywell Aviaso Fuel Efficiency tool. To give readers an idea about our approach in this, I’ll explain why we chose Honeywell Aviaso as our provider (see figure 3).
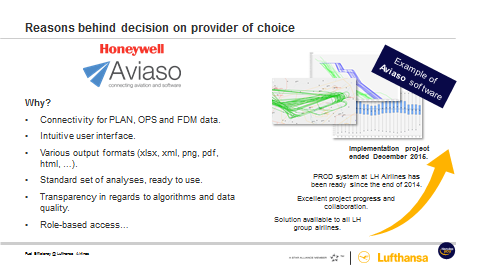
Figure 3
First of all, for Lufthansa, it was really important to first gather all the data that we have – flight plan data, operational data, FDM (flight data monitoring) data – in order to match the different data sources with each other as well as to ensure data quality. The tool provides an intuitive user interface to better understand what it does – the analyses, the filters, the visualization settings. The interface is easy to use because it’s also a web app to which everybody in the company can gain access. There are various output formats (xlsx, xml, png, pdf, html…) for the tool which is really important for us because we want to push the information to other systems as well as users who might not have access to the tool. Then we have a standard set of analyses which are ready to use and are especially useful for new users who can simply open the tool, select the standard analysis for whatever fuel factor they want and get results right away. And something that is also really important for Lufthansa is transparency.
Before this post-flight analysis tool, the whole in-flight process, more or less, was opaque for us: we gathered the data but we were not able to use it in any kind of analysis. We did not want to move from one opaque resource to another, even if we could get results from it. We wanted to be able to check what the tool does throughout the process and the tool provides us with the transparency we want; we can actually see what calculations are behind a result and we can drill down into the detail of these calculations to see each data field and when it is combined with other data fields; plus we are able to see the data quality mechanisms running in the background. It all gives confidence in, for example, communications with cockpit crews. And last but not least, the tool enables users to define role based access – we don’t want everybody to have access to all data but need to specify who has access to which data.
These and other reasons lead us to choose Honeywell Aviaso. So far, the solution is available to nearly all Lufthansa Group airlines and during the project there was excellent collaboration with Aviaso. Our PROD (production) system has been available since December 2014 and the implementation project officially ended in December 2015 having started in 2013. Aviaso became involved in March 2014 after one year of preparation through the formal process of selecting a provider. From then it took only three quarters of year to implement the software in our IT systems. Since December 2015, we have operated the post-flight analysis system every day.
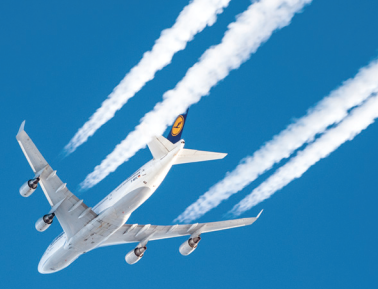
OMEGA ANALYSIS AND ACHIEVEMENTS
After implementation we had the post-flight analysis tool, we had a growing body of results and we knew what was going on, more or less, but we needed to consider how things could be changed. As I said above, flight operations are a major factor and flight operations are conducted by cockpit crews; so, it was important to involve cockpit crews into fuel efficiency measures: the challenge was; how to achieve that? How to share the idea of using fuel more efficiently with the people who use the fuel?
Informing the people who use the fuel
The other challenge was sheer numbers. Lufthansa has more than 5,400 pilots so, simply writing a letter setting out ‘how to’ save fuel, would not work very well. So we considered what we might do instead which lead us to look at how pilots and crew get information which is the briefing package, the main preparation for the flight. So, why not simply adapt that briefing package to offer the crew dedicated individual, flight relevant information for each flight event within the context of OMEGA? The implementation in the end was to provide an automatic export of the pilot briefing complement. We use sophisticated user defined fuel burn analyses, which enable us to define our own analysis in detail. It works by first collecting the data to apply in the OMEGA tool and generate comparisons between the actual burned fuel versus the planned burned fuel on flights and to generate statistics in order to analyze extra fuel burn (in OMEGA, ‘Delta Fuel Burn’). We then have a dashboard from which all the analyses can be accessed and exported automatically to the briefing system as an A4 page, complementary to the briefing package so that pilots can print it out, plus we have that same information on the EFB as well. So every pilot gets Lufthansa’s OMEGA briefing complement for every flight they undertake.
Finding and closing efficiency gaps
Readers will know that the actual flight path does not always represent the flight plan; there will be efficiency gaps in both the lateral and the vertical profiles but the question was, how could those gaps be closed? The challenge here is that OFPs (Operational Flight Plans) must conform with all legal requirements and flights have to use the published routes, waypoints, etc. However, while in-flight shortcuts might significantly vary from the planned routing, the pilots might not know about possible short cuts. They have experience on several routes; they know about a specific route and might get a short cut at a specific time but as soon as they go on another route, they don’t any longer have that experience. Our solution was to use the post-flight analysis tool to find, analyze and publish significant lateral shortcuts. The way to do that is by setting up analyses to offer guidance as to where we could look; then we go into map view to see the actual flight profile, the air spaces passed through, the waypoints, etc. and find out whether there is a short cut possible. The analysis then measures whether this short cut would really benefit us, i.e. offer a fuel efficiency gain; can we save trip fuel or transport fuel by using this short cut, or Direct? We can then publish and use these Directs in the months ahead.
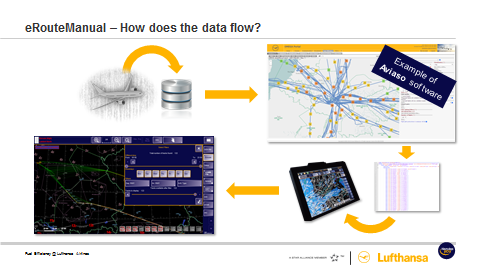
Figure 4
As I’ve already mentioned above, we have to publish these Directs because pilots need to know about them: there are two ways in which we can do this. First there’s the ‘old school’ way of publishing a text message to our pilots to which we add the so-called ‘additional company information’ which is part of the briefing and the flight preparation process so the pilots will look into that and they might read that there is a Direct possible from point A to B which could save a number of nautical miles. That’s an easy solution but the problem is that, if you have a long-haul flight, the pilot might not remember throughout the whole mission a text that he read before the start of the flight. For that reason, we moved to a more sophisticated approach with the charting application (eRouteManual) from Lufthansa Systems which is provided on Lufthansa’s EFB. Together with Lufthansa Systems and Aviaso we connected both systems with each other so that we are able to export our lateral trajectories from the OMEGA system to the EFB and show them in the charting application. That offers something more visual and displays the actual flown trajectories on the EFB: we have a store of up to 150 trajectories of the latest flights which are shown on the maps during the flight when the pilot can switch it on or off to see where colleagues have flown before and where they might have had a shortcut as well as information such as where they had to detour from the planned arrival routes.
Reduced Engine taxi in procedures
Another example where the OMEGA system has helped to improve performance by improving the information on which decisions are based is the reduced engine taxi in (RETI). This is the best practice that always crops up when fuel efficiency measures are discussed; everybody wants to do it but the question is, ‘what is the potential saving?’ It’s possible to switch off one engine but not at every airport or in every situation. We needed to know, ‘is there fuel saving potential left for using this procedure or not?’ Again, the solution was to go into the analysis tool, check the data, set up specific filtering and specific analysis for this and gather the information from which to generate the results we needed.
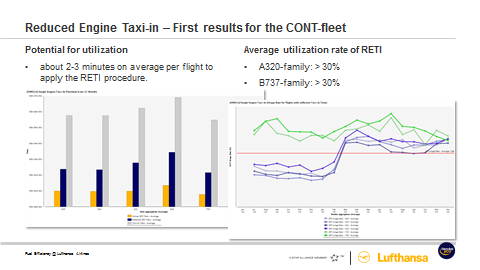
Figure 5
The outcome was that, looking across all flights (not just those where reduced engine taxi in is possible), we found two to three minutes of potential savings (possible additional ‘single-engine taxi-in time’) left, which has a huge cumulative impact. Our current utilization rate for this procedure in the continental Europe fleet is 30%. For the intercontinental fleet the utilization is even less. So, there is a savings potential left which we can address. The graph on the right of Figure 5 shows a huge jump in the data corresponding to when we first communicated the results to pilots. We had a utilization rate of about 15% so we asked them to use RETI more often and they did, hence the step change in the graph.
These are the top examples of fuel efficiency initiatives implemented over the last year. We have also had a lot of departments coming to us asking for data, for results, for information about the flights, etc. So there are other, smaller examples of what we were able to do with the post-flight analysis tool.
Other uses for the post-flight analysis tool
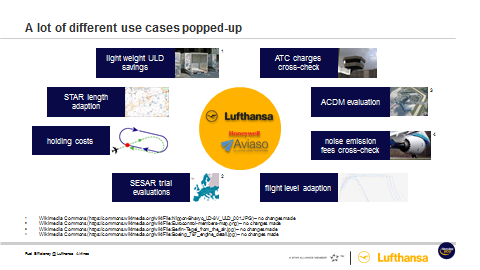
Figure 6
Among these different cases we had light weight ULD (unit loading device) savings that started with an idea from our colleagues at Lufthansa Cargo who wanted to verify their own figures with ours; they also use the OMEGA tool. Then there were ATC (Air traffic Control) charges cross checks: we know where our planes are flying, which waypoints they cross, where they cross borders, etc. so we can check ATC charges. STAR (Standard Terminal Arrival Route) length adaption is something we did in Frankfurt, something we had to do for our OPs (operating procedures) to get better figures for the STAR or arrival route length. With ACDM (Airport Collaborative Decision Making) evaluation, if the airport tells your ACDM that they can decrease the taxi out time, it’s possible to check if this is true using our tool. The one time this has happened, we found it not to be true. It’s possible to calculate holding costs – fuel burned during holding – and how often aircraft are in holding. One thing with which all readers will be familiar is noise emission fees which can be cross checked in a similar manner to the ATC charges (above). Lufthansa has a whole department working on the SESAR trials and working with SESAR teams all over Europe who use our tool to verify trial flights and to evaluate those flights. And we have flight level adaption for flight planning.
Our team is proud of all that we’ve achieved and particularly proud that we won the 1st Innovation Award of the German Aviation Industry in the category Emission Reduction. That really endorsed the program and the OMEGA system that I’ve tried to describe to you in this case study.
Contributor’s Details
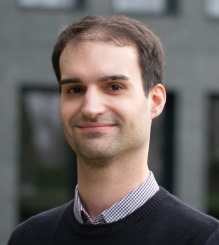
Tom Duddeck is a Manager for Fuel Efficiency at Lufthansa German Airlines, responsible for the continued operation and development of the post-flight analysis tool as well as for developing fuel efficiency analyses. He has been working in the fuel efficiency department since 2014. Before that, he had been working for two years in development of the flight planning system LIDO/Flight at Lufthansa Systems. Tom graduated at the Technical University of Dresden with an engineering diploma in Transport Engineering with focus on logistics and aviation.
Lufthansa
Lufthansa is the largest German airline and, combined with its subsidiaries, also the largest airline in Europe, both in terms of passengers carried and fleet size. It operates services to 18 domestic destinations and 197 international destinations in 78 countries across Africa, the Americas, Asia, and Europe, using a fleet of more than 260 aircraft. Lufthansa is one of the five founding members of Star Alliance, the world’s largest airline alliance.
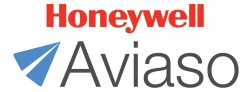
Honeywell Aviaso/Fuel Efficiency software helps airlines and operators discover fuel savings by implementing sophisticated analysis tools. It provides flexible instruments for comprehensive monitoring of fuel efficiency improvement programs. Honeywell Aviaso/EU-ETS ensures full compliance with the EU Emissions Trading System and supports fully automated data collection with adapters directly connecting to the major airline IT systems. The company maintains data centers in Switzerland and Sofia and provides customized hosting-solutions for aviation companies.
Comments (0)
There are currently no comments about this article.
To post a comment, please login or subscribe.