Articles
Name | Author | |
---|---|---|
Case Study: MATMen – In-House Solution for Supply Chain Optimization | Petr Barton, Inventory Manager, Travel Service a.s. | View article |
Case Study: A digital future for Air Evac | Tammie Bethel, Records Specialist, Air Evac | View article |
Case Study: Achieving a Continuous Compliance Culture at Southwest Airlines | Don Tilden, Director of Central Publications, Southwest Airlines and John Zawlocki, Fleet Solution Manager, Flatirons Solutions | View article |
Case Study: MATMen – In-House Solution for Supply Chain Optimization
Author: Petr Barton, Inventory Manager, Travel Service a.s.
SubscribeMATMen – In-House Solution for Supply Chain Optimization
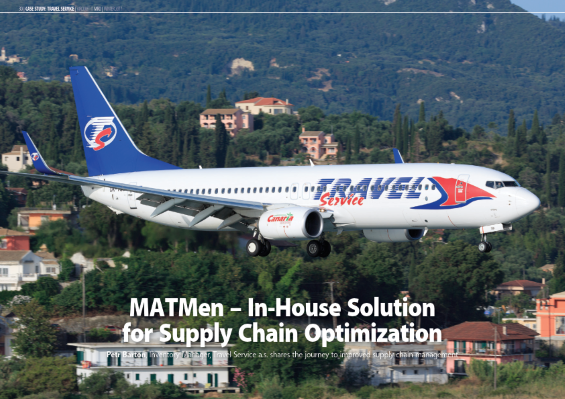
Petr Barton, Inventory Manager, Travel Service a.s. shares the journey to improved supply chain management
INTRODUCTION
Travel Service operates from 22 outstations around the world and line maintenance on outstations is outsourced from local MRO companies. For years we faced troubles with missing materials which caused serious operation troubles and AOG (aircraft on ground) delays. These errors were due to the human factor that engineers on site did not report to us the fact that they had used spare parts so the internal system continued to show that part as available. There was also a lack of information about removed parts from aircraft that were sometimes waiting at the outstation for several weeks without any progress. We also found overviews missing for engineers about incoming parts for planned works.
About Travel Service a.s.
Travel Service a.s. is the biggest airline in the Czech Republic with its head office on the Václav Havel Airport Prague. Travel Service operates charter flights mainly to holiday destinations and also wet and dry aircraft leases to other airlines. It has subsidiaries in Poland, Hungary and Slovakia and also operates scheduled low-cost flights under the brand SmartWings as well as operating business jets, which are available for private air charter.
The Travel Service fleet consists of the 27 Boeing 737-800, 2 Boeing 737-700, 2 Boeing 737-900ER and 4 Cessna Citation Sovereign. The airline was also expecting in
June 2018 to receive delivery of its first Boeing 737 MAX 8 from total 30 ordered.
THE ORIGINS OF THE PROJECT
In 2016, the first point that we needed to address was to have good real-time data about stock issues from outstation inventories and to have the internal system maintained up to date with correct quantities in order to reduce delay compensation payments for passengers and AOG transportation costs. Due to this reason I started development of a web application to cover this function.
I started by identifying the main criteria needed for a perfect result:
- Real-time information sharing;
- Easy to use;
- Reduction in the number of emails daily.
The key point for me was to develop an easy to use application which understands the airline’s supply chain needs.
Today our web application called MATMen contains nine modules and covers our daily operation from storekeeper to engineer and connect Travel Service with third party logistics and line maintenance companies for real-time cooperation.
HOW WE STARTED
Our development journey started with some straightforward words:
‘We need real-time stock issues from our outstations’.
So we developed an easy application with a login page, stock overview and issue button. Our first testing project was the outstation in Muscat with our own engineers and a representative of the logistics department on site. After 14 days of testing we received very positive feedback from our staff and our development journey has continued with improvements to the station module – developed parts requests creation and overview for monitoring of incoming parts for planned works from our main base in Prague. Over time, these modules have expanded and have been improved.
THE STORY OF EACH MODULE
STATION PARTS MANAGEMENT
Station Parts Management was developed as a complete parts management for outstations and was the first module in the application to cover the full parts/logistics overview for a station.
This module covers these functions for each station:
- Incoming Shipments Overview;
- Exchange Parts Overview;
- Parts Request Creation;
- Parts Request Overview;
- Goods Receiving;
- Station Inventory;
- U/S Parts Management.
Descriptions of main functions:
Incoming Shipments window shows all shipments shipped from main base to station. The outstation staff confirms delivery of parts and receives parts into the inventory.
Exchange parts window showing all contracted power by the hour (PBH) parts for station that need to be returned back to the supplier on time.
Parts Requests Overview is for planners/engineers on station to check where parts for planned works are. There is an option here to search by work orders.
U/S Parts Management is a unique tool for managing material returns from station to main base or directly to the repair shop or supplier.
Our first connected third party line maintenance company was Brok-Air on the Canary Islands and Eulogio Álamo Díaz, Logistic Manager of Brok-Air says “Travel Service app is one of the most efficient apps for stock control, shipments and inventories. Very easy to use and quick response.”
EXCHANGE PARTS MANAGEMENT
This module was developed to improve our power by the hour contracts to reduce delays with returning our core units back to the supplier and also reduce costs for late returns. The module is integrated into station parts management and each station can see parts not returned and the date by which that part must be returned. For each core return to supplier we have an automatic email core return notification sent to the supplier which contains information about returned unit and shipping details.
STORES MODULE
The Stores module was developed to improve the efficiency of our main store, reduce human errors and ship parts without any delay.
This module produces for each shipment:
- Pick Ticket;
- Preparation Status;
- Customs Invoice/Packing Slip;
- Automatic shipment notification for each outstation.
After implementation of this module into our daily operation we have seen a large reduction in errors. We can now track all outgoing shipments effectively, create performance reports and track shipping costs. We have a shipped shipments overview with the delivery status and proof of delivery for each shipment.
AOG DESK SHIFT HANDOVER
This module was the first real challenge. It was necessary to create something unique for our 24/7 AOG Desk when employees change shifts at every 12 hours of work. In previous years, for AOG events/shift handover tracking they used only an Excel sheet which was not sufficient. After some meetings with AOG Desk employees about their needs, I developed an overview for their events tracking. On the main window they see open events that need to be solved with priority and deadline, aircraft registration, creation/update date and time, as well as the user who created the event.
HEAVY CHECKS MANAGEMENT
We’ve seen a lot of problems with material requests every year during the heavy checks season. Our heavy maintenance is fully outsourced between MROs in Romania, Hungary and United Kingdom. With each heavy maintenance check, we have a representative from purchasing department on site. There are hundreds of emails between the MRO, stores and purchasing team every day and it created big problems due to the fact that all requests came from the MRO on Excel sheets with many versions. Heavy checks management was our second challenge.
We needed to improve these points:
- Reduce the hundreds of emails daily to more manageable numbers;
- Reduce errors with material preparation;
- Create a single point of communication;
- Have all material requests in one place.
We created a great overview for each heavy check to reduce the hundreds of versions of Excel sheets. Purchasing department now receive requests from the MRO and insert new material into the heavy checks management module with the order type (PO, RO, EO, STORE), work order reference and required date/time. They have tracking information available for each request. If the material request is created with order type ‘STORE’, the stores team in Prague sees in their module which material must be sent to the MRO.
This feature allows us to consolidate materials, save transports costs and track all shipments. We have also a possibility to give access and share these data for each check with the MRO.
Petr Hutla, Head of Logistics & Stores at Travel Service a.s. says: “The MATMen is a powerful app, which is being used on a daily basis by TVS logistics department and by our partners around the world. I believe everyone is facing an e-mailing volume headache – especially during a heavy maintenance check season. I remember this was the first objective for Peter. Use your application to get rid of the thousands of e-mails generated during a check. The result was more than we expected and, at this moment we are started to think about all the communication troubles we’re dealing with and how to use MATMen to avoid them. New modules have been developed since that time and, currently, we’re preparing a new version of the AOG DESK SHIFT HANDOVER module, which will allow us to monitor our AOG performance. As this application is tailored specifically for our line maintenance needs, fills the gaps in our IT system and is user friendly, I see a big future for MATMen there.”
PRODEX INTERFACE
During spring 2017 we decided to outsource inventory and logistics support for our France operation. We chose PRODEX Worldwide as the best option for us with great experience in the aviation supply chain. We placed inventory with them at Charles de Gaulle and Lyon Airport to support our operation in these locations. Due to this reason we developed an interface to have all information from PRODEX in real-time. We developed the creation of pickslips from the PRODEX warehouse, management of incoming shipments for airside delivery to line maintenance with proof of delivery and a U/S Parts Management module integration for collection of removed parts from line maintenance located on airside.
Adrien Perdriat, Managing Director of PRODEX says: ”PRODEX Aerospace Supply Chain specialist is committed to meet the Travel Service requirements and provide a full range of specialized solutions for handling their Aerospace needs (Routine, Critical and AOG). In particular through our Roissy CDG and Lyon LYS warehouses from where we have to organize the storage of components and consumables. Thanks to Travel Service’s own web application the process is fluid and very functional. In real time we can organize the dispatch of the goods. The Key benefits are the traceability, inventory management, order management visibility, all web based so available at anytime and anywhere”
UNSERVICEABLE PARTS MANAGEMENT
Unserviceable parts management was developed for monitoring of parts removed from aircraft around outstations and is integrated into each stations management module. It gives us a great overview of parts removed from aircraft and allows us to react quickly without any delays. Also integrated here is shipments tracking and producing of shipping documents for each shipment.
REPAIR MANAGEMENT
Repair management was developed as the latest module in the application. It is used for monitoring of shipments of parts to be sent out for repair. It allows us to monitor TAT from repair order creation through shipping and received date. It is integrated into stores and unserviceable parts management modules.
DASHBOARD
Dashboard has been developed for our engineering department to see the status of each part request shipped from main store to outstations. There is an option to track the requests which are waiting for shipping and an option for monitoring of delivery status per station or work order. Here is a small preview:
FUTURE DEVELOPMENT
In the future, I would like to focus on improving the monitoring of incoming shipments that have been received from couriers and are awaiting to be received into our internal system. Another goal of the future will be to create an easy to use mobile app to give our staff great overview on their devices.
Contributor’s Details
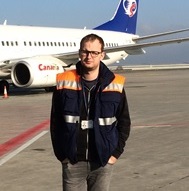
Petr Barton has more than four years’ experience working in aviation supply chain. He started at Travel Service a.s. in 2013 as storekeeper and, after two years, was promoted into new role as team leader of exchange control department with main responsibility for PBH and Consignment Stock contract. In 2016 he was promoted to Inventory Manager with responsibility for the main stores, outstations supply chain and 18 stores employee. He also worked as part of the team implementing the new MRO System. Petr working on number of innovative and optimization projects within stores and logistics departments.
Travel Service
Travel Service a.s. is the biggest airline in the Czech Republic and operates charter flights mainly to holiday destinations and also wet and dry aircraft leases to other airlines. The fleet consists of the 27 Boeing 737-800, 2 Boeing 737-700, 2 Boeing 737-900ER and 4 Cessna Citation Sovereign. The airline was also expecting in
June 2018 to receive delivery of its first Boeing 737 MAX 8 from total 30 ordered.
Comments (0)
There are currently no comments about this article.
To post a comment, please login or subscribe.