Articles
Name | Author | |
---|---|---|
Case Study: MRO Software Implementation Case Study at Aircraft Maintenance Services Australia (AMSA) | Clanci Ferguson, Business Development Leader, Aircraft Maintenance Services Australia, and Gerry Croarkin, Business Development Director, Rusada | View article |
HAECO’s journey to Mobility | Louis Wong, Enterprise Architecture Manager, HAECO | View article |
Column: How I see IT – Go paperless: write that down! | Paul Saunders, Solution Manager, Flatirons Solutions | View article |
Look – no hands! Voice Control for MRO | Jeff Pike, Head of Strategy and Marketing, IFS Aerospace and Defense Center of Excellence | View article |
Paperless Maintenance: The shape of things to come | Paul Saunders, Global Product Manager, Flatirons Solutions | View article |
Case Study: MRO Software Implementation Case Study at Aircraft Maintenance Services Australia (AMSA)
Author: Clanci Ferguson, Business Development Leader, Aircraft Maintenance Services Australia, and Gerry Croarkin, Business Development Director, Rusada
SubscribeWith clear needs and a tight timescale to implement a new MRO IT system, Clanci Ferguson, Business Development Leader, AMSA and Gerry Croarkin, Business Development Director, Rusada, explain how AMSA did it
ABOUT AIRCRAFT MAINTENANCE SERVICES AUSTRALIA (AMSA)
This case study will share how AMSA (Aircraft Maintenance Services Australia) and Rusada went about implementing Rusada’s Envision MRO solution at AMSA. From starting in 1992 with about 40 people, in 2007 AMSA was bought by SIA Engineering Company (SIAEC) of Singapore. The business currently stands at about 150 people serving eighteen airlines having grown with, mainly, transit maintenance activities. This article is about why AMSA needed a new IT solution, why it chose Envision, how the implementation went and what the new software has brought to the business.
AMSA operates with five permanent stations located around Australia and geographically distant from each other; in Brisbane (head office), Coolangatta, Sydney, Melbourne and Perth. AMSA also provides support services to other locations as far apart as Darwin, Adelaide and Alice Springs and as remote as Rockhampton. Over the years, as the business grew, each station evolved their own individual Excel files to control their logistics movements.
AMSA has now reached the stage where it has started undertaking scheduled maintenance activities such as A Checks, in conjunction with Airbus, for operators such as Solomon Airlines. In light of these developments, AMSA needed a better company-wide IT solution and visibility of what it actually had across all locations. For instance, even at headquarters, the business didn’t fully understand the tooling available in each location across the company; it would be necessary to contact the stations and ask them to email their current spreadsheet status to head office which, for a company relating to airlines, wasn’t giving the sort of data and professionalism that was wanted.
IMPLEMENTING A NEW MRO IT SOLUTION
The challenges
One of the challenges facing Rusada when taking on the AMSA contract was that, because of certain inherent conditions, the vendor was under tight time constraints as to how they could successfully implement the new system over a number of diverse land stations. One of the key reasons for implementing the system was to have the same process across all of AMSA’s different line maintenance facilities, who were used to doing things in their own way (see above). That made it very difficult when moving people between different stations because, at each move, they had to learn that station’s local processes. It created a lot of redundancy and added unnecessarily to the time taken to get things done.
So, Rusada’s challenge was to get from spreadsheet systems that were different for each AMSA station, to a uniform system live across five stations within a very constrained timescale. The answer was a six week project from day one to being totally operational across all five stations. Added to that, the people at the line stations were very busy doing their day-to-day work which introduced the further constraint of not being able to pull people out of their routine work activities to concentrate on the implementation.
Preparation
In order to make this happen, and before on-site activities even started, Rusada pre-packaged a significant amount of what would be needed. So, the first three weeks was spent concentrating on setting up the data; getting good data in places where it was needed and structuring the necessary business flows so that, from that, it would be a faster task to roll out the new system across the organization.
From day one, AMSA wanted to adopt best business practice as the new processes were deployed across the organization and its geographically separated stations. As with any project, preparation was the key and in the preparation phase the start point was to configure the Envision system (which can support numerous types of processes from full fleet management to flight ops management) for AMSA, who were then mainly concerned with line maintenance, stores and finance management.
The first step was to create an empty database and copy that database into AMSA’s live database. Then Rusada started remotely working through AMSA’s various spreadsheets that were managing all of the company’s different data sets. The spreadsheets from each station were all in quite different formats so pre-preparation was necessary to ensure that different data from multiple sources could be loaded, reviewed, corrected and re-loaded. The process was repeated many times until there was good clean data throughout the different processes. Next was to load the static data, data about suppliers and transactional data. All AMSA data was setup and configured as per standard Envision ‘best practice’ approach, at Rusada’s office.
With that completed, Rusada then started the main implementation with a live configured database (no data loaded) and the test database (all samples data loaded), and with a team of two consultants on site to undertake separate implementations of the new uniform system across the five line stations. The database set-up had been confirmed with AMSA as had the configuration set-up and making sure that everything would work at different stations. In fact, all of the things that will be familiar to any implementation had to be achieved before Rusada got on site to ensure that the implementation could be achieved within the tight timescale.
The process
The process started in Brisbane where Rusada spent the first week in head office, which is also a base station, working with key personnel, looking at the model that was to be used and customizing it with the functions and processes in AMSA, adding in Rusada’s standard practices and further customizing to cater for the local requirements across the different stations. For instance, it was quickly recognized that how something might be implemented at a line station with three or four people is very different to what would happen at a station with twenty or thirty people. The outcome was a business model tailored to match what AMSA wanted. Some line stations have no dedicated stores staff while other stations have two or three storemen; so the whole area of controlling stock or tools is very different depending on the size of each station. Over and above all that, different line stations handled different aircraft types so that the tools and equipment they used would also vary accordingly. The challenge was how to manage the different types of processes that were specific to the operational needs of each station.
Best practice was agreed then rolled out with the first implementation in Brisbane from which a ‘Quick Reference guide’ was generated to be combined with Rusada’s generic training material for bespoke end-user training material specific to AMSA. All of the above was managed in just five days before senior management signed-off this business process model to be used across all AMSA bases.
Next all the live data for the Brisbane station was loaded and overnight a snapshot was taken of their dynamic information; that was loaded and it went live. The following few days were spent conducting on-the-job training of engineers, stores staff, etc. while, at the same time, preparing data for the next site, Melbourne. So, as site one was going live, the team were preparing for site two – multi-tasking to make optimum use of the time available.
Rusada used the proven model already established for Brisbane to roll-out in Melbourne, along with another re-education process. But, because one of the key reasons for implementation of the new system was to standardize across all the different stations, this was also the template for each station’s business process changes. It wasn’t so much implementing Envision to simply do their normal tasks but in a different system; AMSA were doing this to achieve commonality of best practice across their different business units, and, from that, to achieve operational efficiencies and visibility improvements throughout their business.
So, the Melbourne team were shown how they were going to do it as opposed to Brisbane head office and first station in the implementation having been told, ‘these are the different ways it could be done’, from which the best model was selected. The Melbourne go-live was managed within three days from where the program moved to Sydney which, being the third implementation site, was much easier but still the staff had to be re-educated from their own ways of doing things. Again, go-live was achieved in three or four days.
A TIGHT TIMETABLE AND A CLEAR FOCUS
From Rusada arriving at the first site to having gone-live over the first three stations took just over two weeks while the overall implementation was completed in six weeks. The new solution was rolled out by AMSA to the other two stations at Perth and Coolangatta.
The whole concept was to leverage Rusada’s consultants’ experience to develop a ‘best practice’ solution appropriate for the client. This project was also used as Rusada’s prototype for rapid implementations and was completed with minimal disruption to the client business’s day-to-day operations. Obviously, individual implementation times will depend on the job to be done and the environment in which it has to be implemented. But Rusada has embraced the idea of the three-month (90 days) project as espoused by Ravinder Pal Singh at Air Works (see Aircraft IT August 2015), because people can concentrate on a three month period. A large project might have to be sub-divided into sub-projects so that, say, the first three months might be delivering proof of concept. But there have to be aggressive plans that allow people to start seeing the benefits of investment in a new system as quickly as possible.
As was alluded to earlier, the immediate reason that AMSA needed to do this and in the time period set down was predominantly the A380 A Checks that they were going to start undertaking for Airbus. Clanci went to Melbourne to start the project about three weeks before the implementation in Melbourne. About two weeks after that, AMSA got the first shipment of spares from SIAEC and Airbus to enter into to the new system and start the A Check maintenance program. AMSA is backed by its parent company, SIA Engineering Company and the move to a new system was part of that relationship as well as to grow AMSA’a capability in the whole sector.
WHY AMSA CHOSE RUSADA AND ENVISION
Before deciding which software package to adopt, AMSA reviewed the offers from a lot of MRO IT developers and vendors, and was particularly impressed by the range of modules they could use with Envision from the outset. AMSA has already grown significantly over its first fifteen years and will continue to grow both in size and capabilities. Although currently it only requires the Material and Logistics modules, AMSA didn’t want to find itself in five years’ time having to undergo another system implementation process in order to continue to grow and/or undertake further maintenance tasks. The fact that Envision is fully deployed will allow AMSA to exploit future business opportunities, such as Fleet Technical Management, without needing another implementation. This differed from some offers where each module is only installed when required. It was also useful, from AMSA’s point of view, to have firm commitments around implementation costs at the time of selection because the budget for the new system was very tight. As has already been mentioned, time was also tight and Rusada was able to work with that. That set time and cost was a major plus in AMSA’s considerations.
Already, AMSA has started tapping more heavily into the finance modules and in recent months has been able to pair Envision with an existing finance software package to continue growing the new system now that it has been implemented.
BEFORE AND AFTER
Then and…
Before the implementation, every line station in AMSA’s business had its own spreadsheet system run by an individual member and held on a hard drive at that station. These systems worked and satisfied airworthiness requirements, but they exhibited a number of shortcomings. For instance, because, each station dealt with a different group of airlines, that added the complexity of a different spreadsheet for each airline within each station. Some spreadsheets were even held on the hard drive of the individual managing them at the station so that, when that person went on leave, the company lost visibility of what was in stock. Furthermore, it led to tooling and spares being purchased at all locations rather than looking at what could be transferred between stations. AMSA’s Quality department also had to interrogate multiple local spreadsheet types to gain data about different stations. What is more, the different spreadsheets didn’t even look alike.
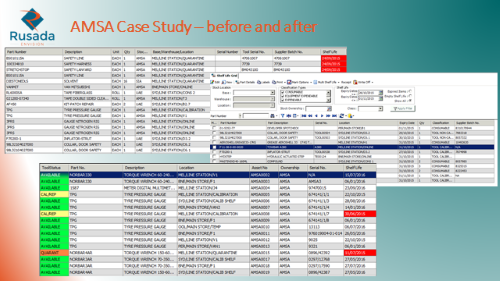
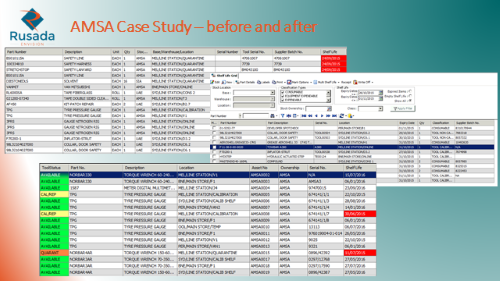
As airline customers started to use more than one of AMSA’s bases, when they asked for documents from different stations, they were getting sheets that looked completely different depending on which station was supplying them and that was not how AMSA wanted to be perceived.
… Now
Following the implementation of Envision, one the greatest gains for AMSA is that the head office now has full visibility of what is happening at all of the business’s station and in real time. The corporate finance department can see what stock the company holds, regardless of where it is. Given the distance between bases, AMSA doesn’t often transfer stock between stations – it’s usually cheaper to buy locally. However, the company now has the chance to see what it has and make an informed decision on whether to transfer or buy locally. The Quality department can also now look across the business and stock can see what is being used on each aircraft and whether the data on shelf-lives and calibration-lives is correct. In the past, when the stock department travelled to a station from head office as part of the audit for an airline they might well discover potential problems only at that stage. AMSA now has the visibility that it requires.
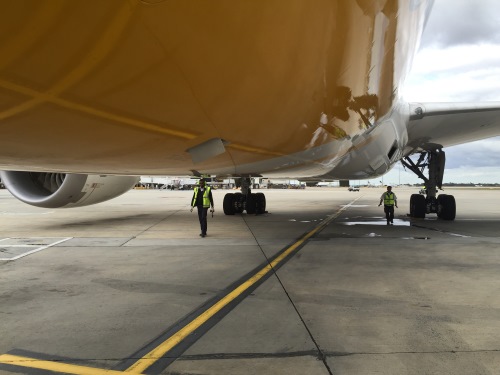
It’s now possible for people to move between stations and for, say, one storeman in Melbourne to also look after stores in Perth. That flexibility, given the large distances between stations, is a significant plus point for AMSA. So now, when an airline asks AMSA for information, they can have that information from the company or from individual stations but it will all look the same which, as far as the business is concerned, represents a great improvement on the previous situation and a sound IT platform for the future.
Contributor’s Details
Clanci Ferguson
Clanci is an Aeronautical Engineer and the Business Improvement Leader for Aircraft Maintenance Services Australia (AMSA) focusing on Logistics and Finance integration, specifically using Envision. Preceding this she managed A380 maintenance conducted by AMSA and before that, was an officer with the Royal Australian Air Force (RAAF) working in both maintenance and operational planning as well as hazard reporting and incident investigation. Clanci also developed the curriculum for and trained junior RAAF engineering officers.
Gerry Croarkin
Gerry Croarkin is the Business Development Director for Rusada. He also oversees product development and is tasked with designing the next generation of Rusada’s Envision software. His role takes him all over the world in search of deals or partnerships that will further enhance Rusada’s reach and reputation within the MRO solutions industry. Gerry has been with Rusada for three years during which sales have reached record highs.
AMSA
Aircraft Maintenance Services Australia (AMSA) PTY LTD is a wholly-owned subsidiary of SIA Engineering Company and provider of world class aircraft maintenance services to a wide variety of domestic and international airlines. AMSA has achieved significant growth over recent years, expanding its client base through the dedication of the employees and management as a team. Today AMSA services more than 18 international airlines including Singapore Airlines, Emirates, Virgin Australia, Malaysian Airlines and AirAsiaX.
Rusada
Rusada provides MRO software for the civil and defense aerospace industry with a global customer base of fixed-wing, rotary-wing and MRO center businesses. Envision is Rusada’s MRO/Operations and fleet management software solution delivering flexibility to meet and respond quickly to change plus providing key management information and operational process control for airlines operators, line maintenance providers, and MRO organizations on every continent. Clients include Airbus Helicopters, Air Arabia, Abu Dhabi Aviation, Fokker, Sky Shuttle, SpiceJet, SIAEC and more.
Comments (0)
There are currently no comments about this article.
To post a comment, please login or subscribe.