Articles
Name | Author | |
---|---|---|
Be ready for GDPR | Sander de Bree, Founder and CEO of EXSYN Aviation Solutions | View article |
A new way of looking at and managing pre-maintenance data Part 2 | Steve Sayers, Director of Technical Publications, FLYdocs | View article |
Paper to Data — Data to Dollars Part 2 | Rob Saunders, Consultant, Aircraft IT | View article |
New technologies and Blockchain | Mathieu Gimenez, Innovator at the MRO Lab Singapore, Air France Industries KLM Engineering & Maintenance (AFI KLM E&M) | View article |
Digital twins, AI, mobile apps and drones | Mark Martin, Director, Operator Edition Product Line, Aviation & Defense Business Unit, IFS | View article |
New technologies and Blockchain
Author: Mathieu Gimenez, Innovator at the MRO Lab Singapore, Air France Industries KLM Engineering & Maintenance (AFI KLM E&M)
SubscribeNew technologies and Blockchain
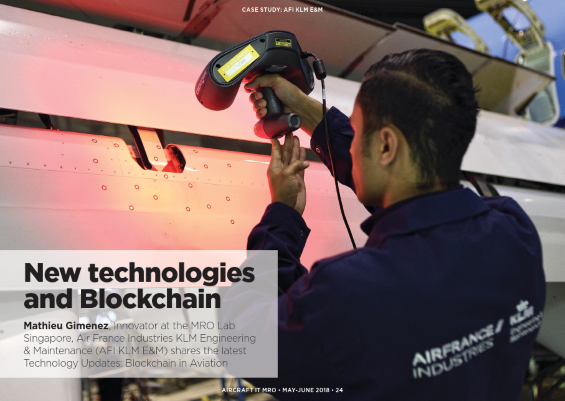
Mathieu Gimenez, Innovator at the MRO Lab Singapore, Air France Industries KLM Engineering & Maintenance (AFI KLM E&M) shares the latest Technology Updates: Blockchain in Aviation
This article will share with readers some innovations instigated in AFI KLM E&M and I’ll highlight a specific use case developed using Blockchain but first let me tell you something about Air France Industries KLM Engineering & Maintenance (AFI KLM E&M).
AIR FRANCE INDUSTRIES KLM ENGINEERING & MAINTENANCE
We are, as the name probably suggests, an airline MRO which means that we operate aircraft in Air France and KLM plus maintain and repair our own aircraft as well as third-party operators’ aircraft.
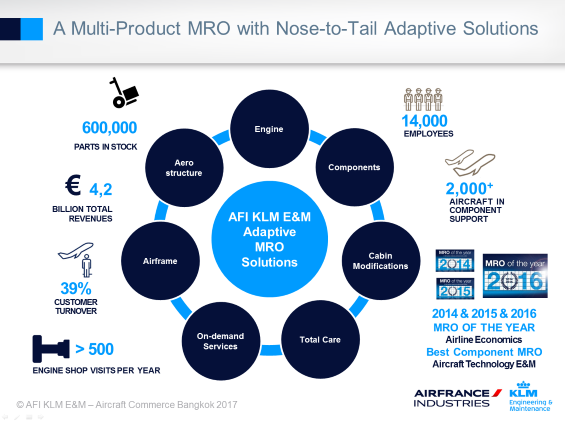
Figure 1
AFI KLM E&M provides maintenance services from ‘nose to tail’ (figure 1) which means that we can deliver maintenance services for airframes, aero structures, engines, components and cabin modifications. We’re proud to be able to say that, for the third year in a row, we have been selected by Airlines Economics to be the MRO of the year. Our adaptiveness is one of the key values that have been recognized by our customers which is important today because the world is changing fast, so adaptiveness is an important value.
Figure 2 (below) shows a rough map of our global network.

Figure 2
It’s not up-to-date because, at the time of writing, we had just signed a new joint venture with Sabena Technics which will open in Singapore and is in line with our growing presence in Asia, a strong presence in Europe and in Miami with Barfield as well as in Dubai. So we have a global network and over 200 customers worldwide.
With the new generation aircraft and engines we had to innovate and provide new maintenance services which is what we have been able to do; providing cutting edge maintenance services for the Boeing 787, Airbus A350, A320neo aircraft and GEnx engine for a number of customers for those new platforms (figure 3). We’ve been rolling this out quite fast and we are ready to serve all of those platforms.
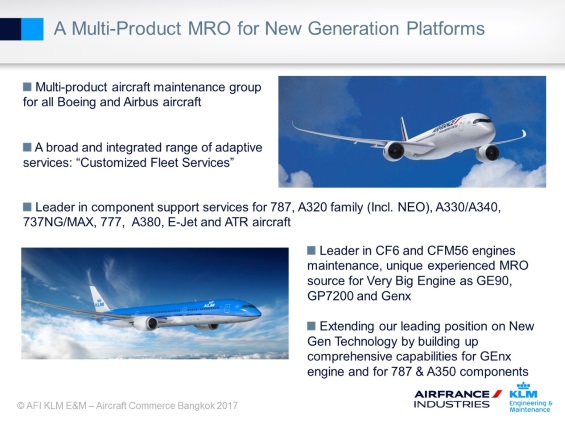
Figure 3
PARTICIPATIVE INNOVATION
This will be the main focus of the article and innovation is not a new thing for AFI KLM E&M; for more than twenty years we’ve been involved with and undertaking participative innovation. That means that any employee in the group can submit an idea, carry out the project and get rewarded for it. And over the twenty years we have collected around a hundred thousand suggestions at the rate of 4,000 to 5,000 ideas a year; it is our main generator of ideas. In figure 4 you can see a couple of images from the different award ceremonies that we organize every year in Paris.
In February 2015, we wanted to accelerate our rate of innovation with an emphasis on how we’re going to organize innovation, and how we’re going to proceed and move forward by creating tools.
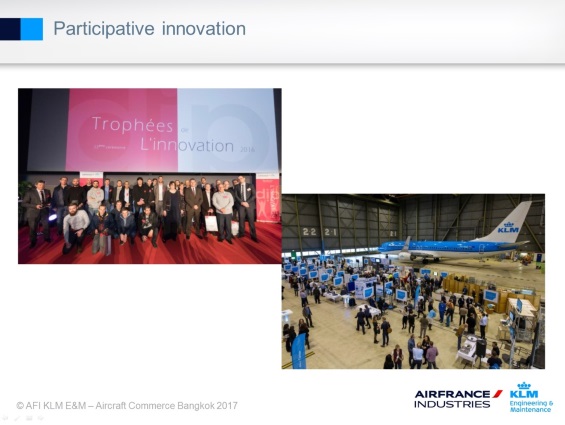
Figure 4
The first thing we’ve created is a brand called ‘The MRO Lab Adaptive Innovations’ to include all innovation in AFI KLM E&M and our global network. Adaptiveness is, as I’ve already said, very important for us to be able to tailor and adapt our services to our customers and the MRO Lab Adaptive Innovations is organized with a network of ‘Innovation Leaders’ in all departments throughout the company and those people are ready for change management; they are the ones who are going to push the disruptive innovations. Our motto is ‘Think big, start small and act fast’. That is the main value we would like to emphasize in the MRO Lab Adaptive Innovations.
THE MRO LAB
Let me describe the MRO Lab, the tools we have and some key innovations that we’ve been able to release in the last year. Participation in innovation is in our DNA and is one of the pillars of the MRO Lab. To support that, we’ve designed ‘creativity rooms’ all around our facilities world-wide (figure 5).
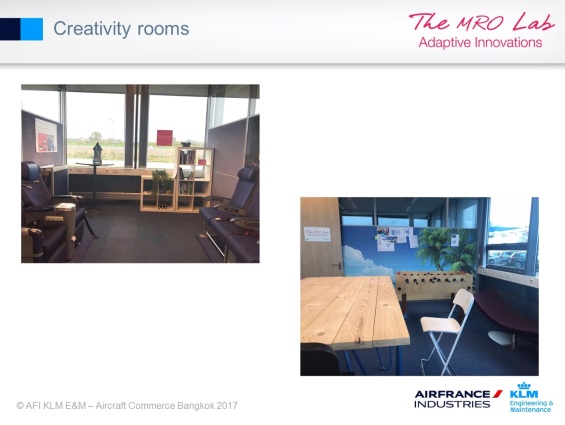
Figure 5
The idea was that if we design meeting rooms that were not usual, our white collar employees will be encouraged to think out of the box. That was the main purpose and it worked quite well, we even had high performance meetings in those rooms with impressive results.
At the time of writing we were building a new concept called a Maker Space; a Maker Space is a room where blue collar employees can go and use tools and machines such as 3D printers. They are trained on those machines and the goal is for them to work on their professional and personal projects within this room, at no cost to them; we believed that will generate more ideas and innovation within the company.
We also work with industrial partners, with Start-ups and with Universities (figure 6)…
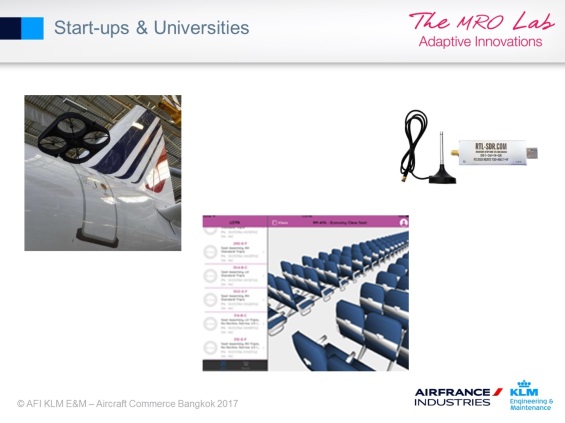
Figure 6
… on projects such as using Drones to inspect the outside of an aircraft or an App for cabin description so that, when a part needs to be replaced, the part number can be accessed quickly and ordered through a mobile device.
One of the other tools or resources in the MRO Lab Adaptive Innovation is the AIR FRANCE KLM Digital Studios, where teams from all divisions of the business (passenger, cargo and maintenance) can work together on digital innovation. The first such facility is in Amsterdam and there will also soon be one in Paris; it is a unique innovation with a nice set-up and able to facilitate a lot of sharing between the employees in our huge company
DIGITAL INNOVATION: SOME SPECIFIC USE CASES
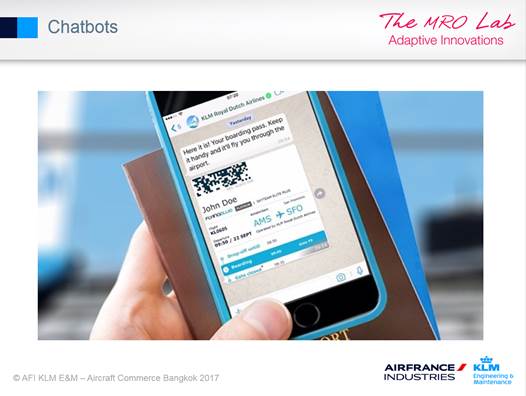
Figure 7
TRAINING
The training department is really active with innovation in AFI KLM E&M. Most of their course material has been moved from paper to augmented and virtual reality using HoloLens and HTC Vive. The photos in figure 8 are real; it is how we train our people today…
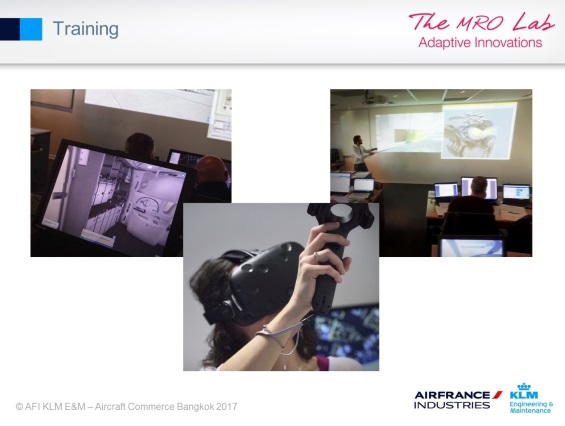
Figure 8
… and if, as a customer, you want to use our training, this is how your people will be trained. The main benefit is better communication, better understanding, less hours within an actual aircraft. We’ve done some case studies using a HoloLens with a group of five people and we confirmed that they came to understand their training much faster than people using other systems such as a PDF.
PREDICTIVE MAINTENANCE
Last but not least, Prognos is our predictive maintenance solution. I think this is our greatest source of pride today in AFI KLM E&M, being able to predict component failures on aircraft and engines and we are about to also release this solution to our customers. There are a number of people working in the business in Paris and Amsterdam on this solution, to be able, for each and every component, especially the ones that are critical, to predict failure long before it happens so we can remove, repair and replace the component before facing an AOG (aircraft on ground) situation.
THE MRO LAB SINGAPORE
The last big resource in the MRO Lab Adaptive Innovations is the MRO Lab Singapore, a co-innovation center that AFI KLM E&M established in February 2016 with Ramco Systems, and the Singapore Government. At the Lab, we undertake digital innovation and use new technologies to solve business pain points in MRO. Generally, we develop these innovations in two to three months and we’ve been working with some great technologies such as HoloLens and RFID (see more below) and we have a great multicultural team (figure 9). They are impressive: able to learn fast about new technologies such as Blockchain which they knew about a bit when we first mentioned it but they had never used it. So we did it and a couple of months later we had completed a use case. That’s the spirit of it; we’ve been able to tackle new technologies and address new business pain points every month with our multi-language, multi-cultural team in the Lab.
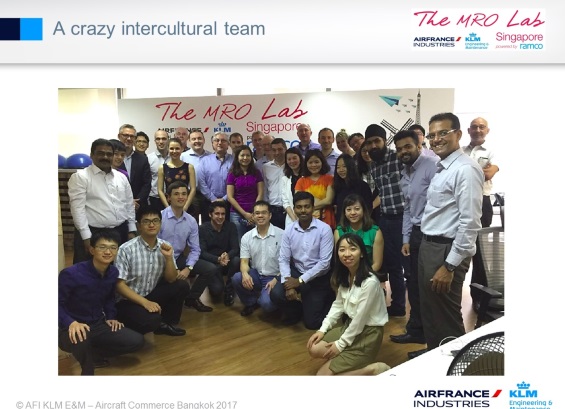
Figure 9
Some examples of a new technology we’ve been using (figure 10) would be, given that adaptiveness has always been a key value for us, we’ve been using big data, GPS tracking, Bluetooth Beacons, IoT, augmented reality, virtual reality, voice recognition… they all sound techy but we use them for specific use cases when we think there is a value for using that technology as opposed to another one. We’ve also been working a lot with chatbots recently.
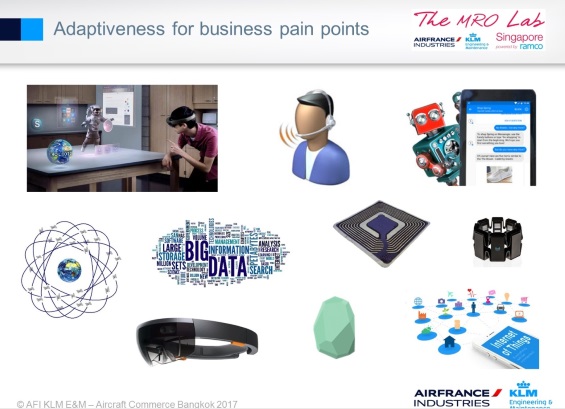
Figure 10
The most recent product concept that we’ve released is the 787 Operators Community, dedicated to our customers. It is a web platform for customers who fly the Boeing 787, for them to be able to share their best practices and operator experience around the 787. And, at the time of writing, all the operators in question were testing and giving AFI KLM E&M their feedback on the platform.
That’s a key point when we do a proof of concept dedicated for customers: we want to give it to the customers, get their feedback and, if they’re happy, we’re happy. If, on the other hand, they’re not satisfied, then it’s probably not a good solution.
BLOCKCHAIN USE CASE
Now, to the Blockchain use case. We have developed a Blockchain use case in Singapore for the main reason that we wanted to try this technology, to see how valuable this might be for the aviation sector. However, we still want to follow a few principles. We want to make it realistic – it has to answer a real and specific business need not just be developed for its own sake, i.e. if the job could be done with a normal database, why use this more complicated one? We also want to have it tailor-made as we have specific processes and want to adapt to each customer. We further want a multidimensional approach, which is quite interesting as this is not only a technical design or technical solution, it has to deal with legal issues, with organizational and change management, and other considerations.
The first use case we tackled was in the aviation supply chain, mainly because we had identified four aspects of Blockchains that are also essential in the aviation supply chain: resilience, traceability, integrity and disintermediation.
For a small demo we’ll look at a specific part where an operator, for this purpose Air France, is requesting the MRO, AFI KLM E&M, for the loan of a part; in case of an AOG situation. Today, most of the work is done using ERPs; however, ERPs do not communicate so much, they don’t exchange much data and the data is not secure, it could be hacked. So the video shows how users in the operator and the MRO can share the information for the loan. A licensed engineer in Air France has already requested the part, the Loan Officer in Air France has request for a loan to the MRO (AFI KLM E&M) and is waiting to receive the part. The short video below shows how it works.
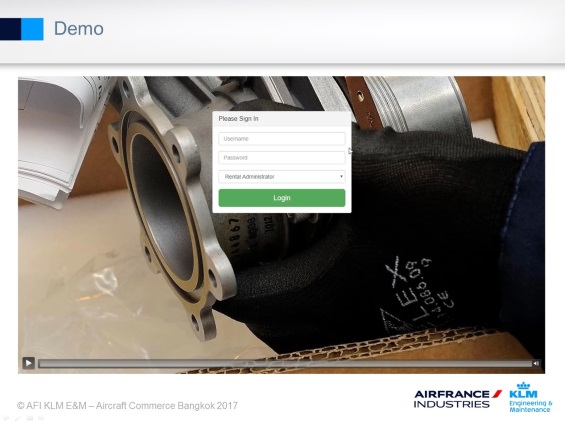
Blockchain demo
First logging in as the MRO to create a rental order, we see the loan order from Air France and the history of the specific part. This is the Blockchain of that specific part, its history, and is not hackable nor can it be modified. So, the MRO selects the part, selects the certificate number and proceeds through the loan or rental. As the demo shows, we can see that this has been registered within the Blockchain. So now it is part of the block and cannot be modified any more. Next, the Air France clerk logs in to receive the goods; so he has received the part which he can confirm while the MRO can still see the history, the Blockchain of this part, and, once again, this cannot be modified; and it is public, so that whoever needs to can have access. Then Air France can confirm that it has received the part and it’s all good. The part is now in Air France’s hangars where a licensed engineer will install this part in the AOG aircraft, i.e. remove/install a part – the first two columns in the video are for the part that has been removed and the next two columns for the part that has to be installed. The engineer proceeds through the change, and this also is public so that everybody knows what has happened.
A few weeks later he has used the part and now is ready to remove it because it has been loaned and needs to be returned to the MRO. So the engineer removes the part, to avoid paying any extra charge, and all the usage that has occurred while the part was installed on the Air France aircraft – how many hours, how many flights – is all tracked and has been logged in the Blockchain.
Having removed the part, it is returned to the MRO and that is logged within the Blockchain. So this will improve the traceability of the life of a component. As an MRO, we can log in and access the user receipt to confirm that the part that has been loaned or rented has been received back; the MRO can check the history and that the contract signed with this customer is what really happened; because the Blockchain records what really happened: then, if everything is correct, the MRO can approve.
Summary of Blockchain
What Blockchain saves depends on which technology. Blockchain will save a lot of administrative tasks but there are technologies such as the Internet of Things (IoT) that will also save AOG time.
Once there is a Blockchain linked to all the ERPs of the different operators and MROs, by modifying something in an ERP a request can be sent by one user or knot to the Blockchain and, depending on validation by the other knots in the Blockchain, which are able to decide whether to accept a new block, new information can be entered in the database. So, if a mistake has been made and the user/knot wants to correct it in the Blockchain, they’ll need the approval of the other knots. Each blockchain needs to be tailor-made and, for dealing with mistakes, it is necessary to consider how it can be tackled and ensure that, if a mistake occurs, it should be possible to correct it and update the blockchain.
CONCLUSION
These have been some of the processes and ideas we have developed in AFI KLM E&M to drive innovation plus some ideas on Blockchain and where it might be used.
Contributor’s Details
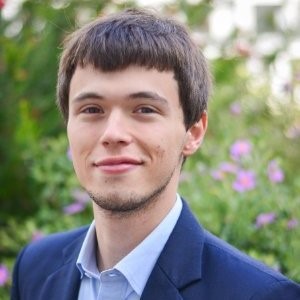
Mathieu Gimenez has been at The MRO Lab Singapore since 2016 bringing his aeronautical expertise to run proof of concepts in a very short time, following design thinking and agile methodologies. He holds a Master of Science in aeronautics and a degree in flight testing. He worked in the USA as a production engineer in Dassault Falcon Jet before joining Safran Engine Services (Snecma) where he played a significant role in the Silvercrest flight test campaign and developing a software to detect sensor failures.
AFI KLM E&M
Aircraft maintenance is one of the three businesses of AIR FRANCE KLM. As an airline with an MRO arm, AFI KLM E&M is faced with the same limitations and the same challenges as its customers. Long experience means the MRO can deploy an optimized maintenance policy. This, combined with technical excellence, enables them to offer some of the most competitive MTBR (Mean Time Between Removals) on the market. The MRO is also developing repair process partnerships with OEMs to minimize and optimize maintenance costs.
Comments (0)
There are currently no comments about this article.
To post a comment, please login or subscribe.