Articles
Name | Author | |
---|---|---|
Future-proofing the Supply Chain | Saravanan Rajarajan S, Associate Director – Aviation Practice, Ramco Systems | View article |
new way of looking at and managing pre-maintenance data Part 1 | Steve Sayers, Director of Technical Publications, FLYdocs | View article |
Paper to Data – Data to Dollars Part 1 | Rob Saunders, Managing Director, Air2MRO | View article |
Case Study: Counting beans and tightening bolts | Kevin Chi-Ming Chen, Senior Vice President, Evergreen Aviation Technologies Corporation (EGAT) | View article |
Case Study: Fleet Technical Management and CAMO | Darmilo Sosa, CEO, Wingbox Aviation | View article |
new way of looking at and managing pre-maintenance data Part 1
Author: Steve Sayers, Director of Technical Publications, FLYdocs
SubscribeA new way of looking at and managing pre-maintenance data
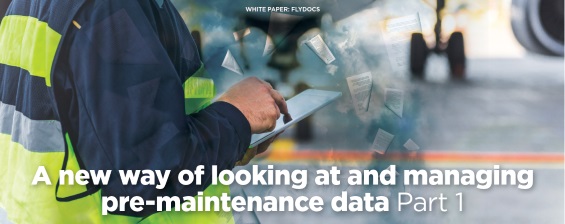
Every airline or aircraft operator needs maintenance for their aircraft; however, when the data comes from different sources, presented in different formats, this process becomes unnecessarily complicated.
INTRODUCTION
In the aircraft maintenance and engineering environment, whether it is an airline, operator or even an MRO (Maintenance Repair Organization), digitalization of data is rendering ever more elements of maintaining, servicing and operating aircraft safer, easier, more intuitive and more accessible. However, one ingredient in the mix seems stubbornly not to fit this pattern of improvement – specifically in regards to access and usability – and that element is pre-maintenance data. This term might not be that familiar to readers so let me explain what I mean by pre-maintenance data, what I see as the obstacles to making it more user-friendly and accessible, and how a modern document management system can provide the answer.
PRE-MAINTENANCE DATA
As previously stated, pre-maintenance data is the information that all airlines and operators require to service and maintain their aircraft. It is the information that an aircraft engineer uses during maintenance work, providing not only assembly or disassembly instructions, but also relevant warnings and cautions at the appropriate steps to ensure the work is carried out in the safest possible way. Part numbers and parts information is also provided within the IPDs (Illustrated Parts Data) or IPCs (Illustrated Parts Catalogue) including details of OEM (Original Equipment Manufacturer) approved alternative parts.
Pre-maintenance data is also required at the aircraft end of lease phase, when an aircraft is being decommissioned out of the airline’s fleet. When Lessors using as system like FLYdocs access their aircraft data, they will see records of all the maintenance, servicing, modifications and even repairs that have been carried out on their aircraft while in service with the airline. Lessors will audit repairs and maintenance activities, and will require access to the relevant pre-maintenance data information as part of their auditing process. This could be in the form of the AMM (Aircraft Maintenance Manual) for maintenance verification or in the case of a repair the SRM (Structural Repair Manual). A good digital document management solution such as FLYdocs enables access to all this data and links the record of the work undertaken to the relevant version of the pre-maintenance data and all other relevant supporting documentation the work was authorized against. It should even allow access to previous revisions of pre-maintenance data.
.jpg)
As part of the ‘type certification’ before an aircraft can be released into an airline or operator’s organization, the OEM would have to verify that the maintenance data works. This verification could involve the proving of assembly and disassembly processes.
That said, opportunities do exist for appropriately approved airlines or operators to create their own maintenance data; not relating to major airframe or engine assemblies, but for areas like additional inspection steps or minor modifications. This is particularly relevant around areas like cabin modifications, which are not covered by the OEMs, but are one of the main areas of modification the airlines and operators make to their aircraft.
HOW PRE-MAINTENANCE DATA IS USED
As part of the pre-maintenance process, the OEMs create and issue maintenance programs, which specify what needs to be serviced and when. It provides details on when components and assemblies need to be changed or serviced. It is possible for airlines and operators to change certain maintenance points and servicing schedules based on statistical data captured through reliability data analysis, but any proposed change would have to be agreed by the relevant OEM and the Regulatory Authority. For example, it could be possible to extend certain scheduled maintenance points if the data and records supported it. A digital document management solution should be able to forecast and trend servicing requirements, particularly those associated with component changes, etc.
HOW PRE-MAINTENANCE DATA IS ORGANIZED AND CATEGORIZED
OEM created/distributed pre-maintenance data is organized and categorized in pre-determined sets, i.e. AMMs, IPCs/IPDs, etc.; these are all created to specific industry wide standards such as S1000D. The SRM manual sets limits for acceptable damage under which the aircraft can operate. It also provides the relevant repair specifications. Part of the damage verification process could require the use of NDT (Non Destructive Testing); this is particularly important when trying to address damage on carbon fiber material or engine fan blades.
In some cases damage will fall outside the SRM limits; the airline or operator will then have to contact the relevant OEM to authorize a specific repair. The OEM will provide the required information and repair tolerances. Airlines and operators who have the appropriate Part 21 Approvals have the capability to create their own repair documentation instructions using the authorization and specification supplied by the OEM. Some repairs will be approved and authorized for a particular period of time or for a specific number of flight hours, and some will remain as permanent repairs and stay in place for the life of the aircraft.
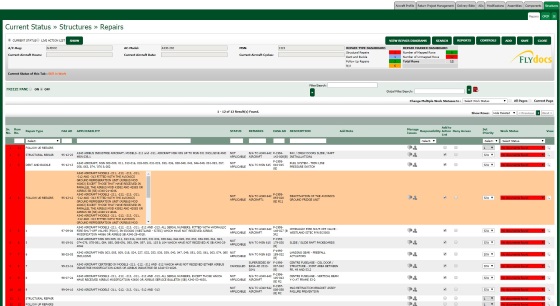
Looking at it from the point of view of the solution with which I’m familiar, the importance of recording repairs and all the subsequent associated supporting documentation in FLYdocs becomes even more critical when some aircraft can remain in service for over 20 years. Imagine trying to find the authorization and record for a repair that could have been carried out some 10 years previously without searching, data linking and data storage capabilities. It once was routine in all airlines and will still be routine in some airlines to spend weeks, sometimes months, trying to validate repairs during the aircraft returns phase. In some cases, repairs could not be validated and the repairs had to be replaced which can be a very expensive process, requiring downtime for the aircraft and the need for specialist manpower requirements.
One of the real breakthroughs in using digital data is the ability to automate the linkages within data sets; this can be within the same manual between similar assembly/disassembly procedures or even across different manuals, for example linking from an AMM Task into the required part within the IPC/IPD or vice versa. This is a real timesaver for engineers, not just because they no longer need to access multiple sets of data, but more importantly it helps to make the decision for the engineer by taking them to the right section of a manual through the hyperlink. Hyperlinking also has been a real enabler for providing data through mobile devices.
CURRENT PROBLEMS WITH DIGITIZED MAINTENANCE DATA
The main OEMs all produce maintenance data sets, (AMMs, IPC/IPDs, Schematics, Wiring Diagrams, SRMs, etc.) and they all author to S1000D Standards but beyond that they format and present the data in differing ways. So, if an Engineer is working for a multi fleet airline, for example operating Airbus and Boeing aircraft, then they will need to be able to access both the OEMs’ applications and software to retrieve the relevant maintenance data they require.
This problem is further exacerbated if the airline or operators are supporting mobile and desktop devices. For example, neither the Airbus or Boeing software works through the same application, i.e. you need duel applications to access data from both OEMs on mobile and desktop devices; furthermore you cannot access Airbus data through Boeing applications or vice versa.
The other issue with OEM digitalized data is online/offline access. For example, the Boeing mobile App only works in an offline mode so the data has to be uploaded to the device, which then creates a potential compliance issue with engineers accessing and using out of date maintenance data. It also creates a large amount of work for areas of the business that support the front-line operations, as this data upload has to be managed on a regular basis. The solving of one problem is the creation of another.
There is one obvious advantage to working offline and that is the Wi-Fi capability can be somewhat challenging at certain airports and maintenance locations and even on some types of aircraft. Although Wi-Fi access for passengers is now a given, getting maintenance data via mobile devices on board aircraft can be very challenging.
The Airbus mobile offering does work in both offline and online modes.
The online option does address the issue of using out of date data and greatly reduces issues of non-compliance, but pushing large data updates across the Wi-Fi can then introduce other problems.
SO TO SUMMARIZE
There is a requirement for multiple OEM software packages to be accessed through one single portal that provides the same ‘look and feel’, whether being viewed through mobile or desktop device. Currently there are no providers offering a single access concept, so at FLYdocs we have seen this as a service offering opportunity and a natural enhancement in developing the pre-maintenance applications as part of the overall platform. It makes sense to expand our solution and service offering to create a new, fully integrated platform that fully covers the entire pre-maintenance sphere of engineering within an airline and MRO. Our current development roadmap sees us deploying a new fully integrated pre-maintenance platform commencing towards the end of 2018, developing to full functionality through to the end of 2019.
Contributor’s Details
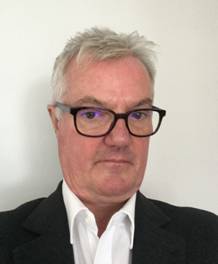
Before joining FLYdocs in 2017 as Director of Technical Publications, Steve’s career spanned 35 years in aviation; 24 years within production of military aircraft with BAE Systems followed by 11 years in commercial aviation with Virgin Atlantic Airways, where he held the role of Information Services Manager. In his current role, Steve is responsible for identifying and developing opportunities to enhance the capability of FLYdocs, for example, by creating, managing and controlling pre-maintenance data and documentation and to provide FLYdocs’ clients with a seamless end to end process for all their documentation needs and requirements.
FLYdocs
FLYdocs is the world’s most advanced aviation data and records management solution provider and global industry leader in managing the lease transfer of aircraft and assets. It provides airlines, lessors, OEMs and MROs with live digital lifecycle compliance information to demonstrate asset airworthiness condition, protect asset value and deliver cost savings. Users include Qantas, Cathay Pacific, Virgin Atlantic, Hawaiian Airline and Willis Lease to name just a few. We have transitioned 200 aircraft on-time in a paperless environment and migrated 400m documents in the last year alone. Currently, we have more than 500 lease returns and audits contracted. But more importantly: FLYdocs has delivered over $140m in cost saving for customers.
Comments (0)
There are currently no comments about this article.
To post a comment, please login or subscribe.