Articles
Name | Author | |
---|---|---|
Future-proofing the Supply Chain | Saravanan Rajarajan S, Associate Director – Aviation Practice, Ramco Systems | View article |
new way of looking at and managing pre-maintenance data Part 1 | Steve Sayers, Director of Technical Publications, FLYdocs | View article |
Paper to Data – Data to Dollars Part 1 | Rob Saunders, Managing Director, Air2MRO | View article |
Case Study: Counting beans and tightening bolts | Kevin Chi-Ming Chen, Senior Vice President, Evergreen Aviation Technologies Corporation (EGAT) | View article |
Case Study: Fleet Technical Management and CAMO | Darmilo Sosa, CEO, Wingbox Aviation | View article |
Paper to Data – Data to Dollars Part 1
Author: Rob Saunders, Managing Director, Air2MRO
SubscribePaper to Data – Data to Dollars Part 1
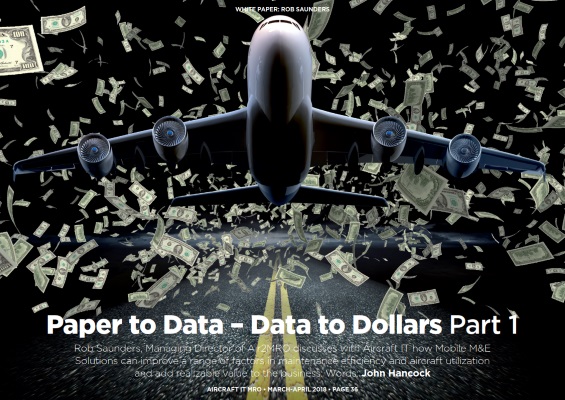
Rob Saunders, Consultant discusses with Aircraft IT how Mobile M&E Solutions can improve a range of factors in maintenance efficiency and aircraft utilization and add realizable value to the business
At Aircraft IT we draw on expertise from across the sector and in that context we arranged to meet Rob Saunders. Rob has contributed to many articles and MRO conferences during his 27 year career with Cathay Pacific. Having left Cathay recently, we asked him, to share his overview of a development area of growing interest in the world of aviation MRO and M&E, mobile solutions: and maybe reflect a little on the advances in that area. But first, why does he consider the topic so important?
“The question,” Rob responded, “is ‘how to generate dollars from the technology available to us? Although the delivery focus is often on the IT element of an improvement project, the business benefit should remain the core objective. Anyone who has presented a business case to the CEO will understand that a safety case or a case with a positive ROI will get a hearing. A case focusing on the IT will likely, and quite rightly, prompt the response, ‘what for?’”
THE STATE OF PLAY
So where does the sector stand today in this respect: what is happening around the industry and where does Rob think we are?
“I can best explain that,” he started, “by citing a project from about five years ago (figure 1) to migrate 35 million paper records into an IT system. There are a small number of specialist systems around, FLYdocs, STREAM, Air Vault, and, to illustrate the magnitude of the problem, if stacked, all the stored paper records for the leading Asian airline fleet in question would result in a Tech Records Tower (as on the right of the figure) higher than the world’s tallest buildings, beside it.
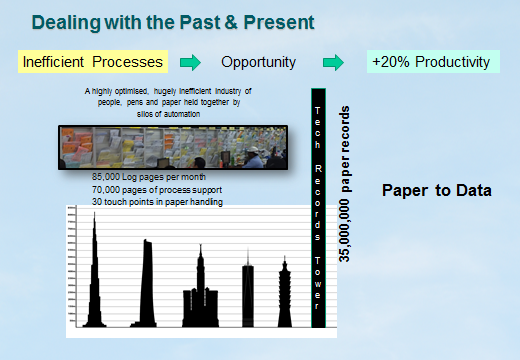
Figure 1
“That was a significant amount of paper, begging the question, what to do with it. It was estimated that if a solution could be found to remove that tower of documents, the airline might expect to generate something like a 20% increase in productivity. However, an important point I’d like to make is, removing the volume of paper is the visual benefit. The actual efficiencies are in retrieval and compilation of compliance information as and when required and, looking forward, the ability to mine all these paper records as data. I believe the solution adopted eventually exceeded the targets. Nevertheless, compared to where the industry could be, aircraft engineering remains a highly optimized, hugely inefficient industry of people, pens and paper held together by silos of automation, often using technology in the forms of Access databases, spreadsheets and interfaces. The industry is at a quite infant stage but there are inroads being made with a lot of initiatives underway that seek to address this issue. If I look back to the ‘80s, we were able to move paper ‘C’ check production plans to a Lotus 123 spreadsheet. 30 years later the spreadsheet is still a major part of many MRO’s toolkit. Fortunately, mobility is the game changer that will see the move to real time production management.
THREE AREAS FOR PAPER TO DATA STRATEGY
That all seemed clear but our next question was to ask how an airline might plan a program to reduce paper. Rob’s response was that any strategy should break the process into distinct areas (figure 2) …
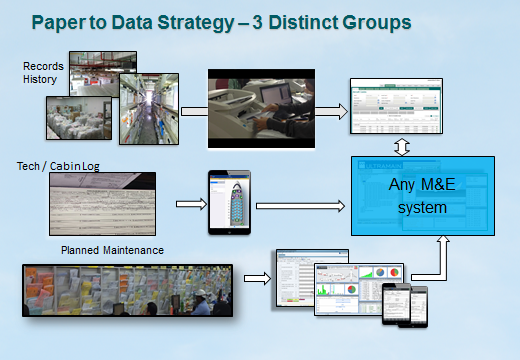
Figure 2
Records history
“Every airline,” he suggested, “has to deal with the records history for many business reasons and very importantly to demonstrate compliance, therefore the legacy of paper that has been handed down and the applications that went with it. Even today, people are still producing paper, scanning it, putting it into electronic systems and saying that’s fixed the problem. In reality, it hasn’t: all that is, is building the problem but managing it. MROs all over the world are still producing paper and many airlines and lessors still require it. For them, the solution is to scan it and hold an electronic rendition of that piece of paper; but that’s not an electronic, digital record, it is just what it is, the rendition of a piece of paper. These are what are being used at the moment; people call them electronic lease returns but they’re not digital data.
“To some extent this is understandable where regulators are not knowledgeable in the subject and therefore reluctant to endorse change. The acceptance of electronic records will happen by attrition. If we look at large fleets with e-Tech log such as Cathy’s A350s where the first sector of the first delivery from TLS (Toulouse) was electronic, it is clear that the precedent is set – there has never been a paper record in the first place. True e-signature of digital work cards is just around the corner with a few software suppliers able to achieve this. As things stand, the paperless operations, and therefore the airline benefits, could be held back while the regulators and others catch up. The alternative is to see paper records produced from electronic data only to be stamped by the QA department. Data to Paper is not quite what we had in mind. That said, there is a lot of work underway in this area with IATA group led by Chris Markou with good engagement from airlines, regulators and lessors.”
That led us to the core issue of planned maintenance and its relationship with documentation on which…
Planned maintenance
“All of what I’ve said so far,” Rob added, “is feeding into the MRO system to support maintenance whether it be forecast or unplanned. But, with a growing trend to outsource, when an airline does not do any of its own maintenance, if you’re trying to justify a system and spend money on it, it may not be seen as the airline’s problem and therefore difficult to justify, ‘why should we pay for that; why doesn’t the MRO invest?’ That’s from the airline side so MROs need to derive their own benefits if they are to make the investment. To illustrate my point I think credit goes to HAECO who, as a pure MRO, have invested in a Mobile Mechanic electronic work card and production control solution that is providing efficiencies in their own processes that translate into ground time savings and the supply of true electronic documents to the airline.
“That’s where things are going and what comes out of this can be fed back into the M&E system as far as compliance is concerned, coming back either as electronic record (perhaps even an electronically signed PDF rendition) into the tech records repository for documents. But, actually, when it’s true electronic, the compliance record could be directly in the M&E system.”
HOW THE NEW ORDER WORKS
While that strategy was clear, the thought that it raised was what the new reality could do for an airline? Rob shared a couple of images to illustrate his response.
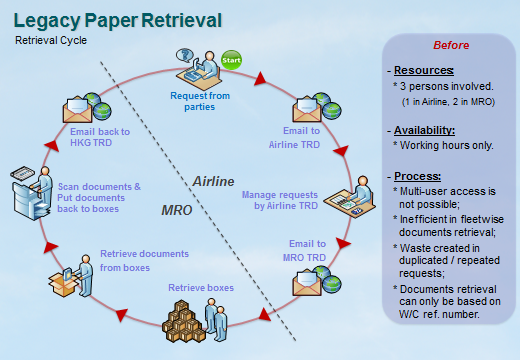
Figure 3
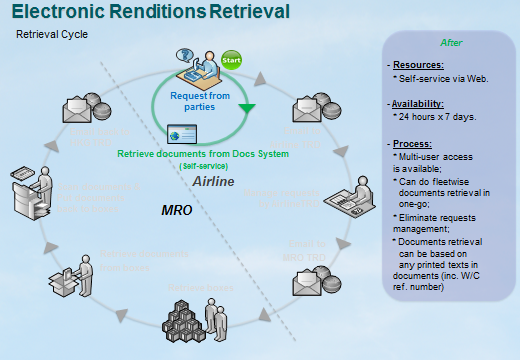
Figure 4
“An analysis,” he showed us, “was done by a Tech Records team after scanning and indexing the paper records. This was simply recovering some document requests from the engineering department, and figures 3 and 4 show the processes that were identified, comparing legacy paper retrieval to electronic renditions retrieval. Between the two, you can see that all of those people in the paper retrieval system have been taken out leaving just the person who needs a document able to retrieve electronic renditions of documents from the docs system by a self-service process. Globally, people can access that data whether they want to look at it whether that’s because they have an AOG (aircraft on ground), they’re doing a lease return or there’s an interest from the lessor. The project also undertook an exercise to compare the old and new retrieval systems in an routine Emergency & Accident exercise situation and for a lease return (figure 5)…
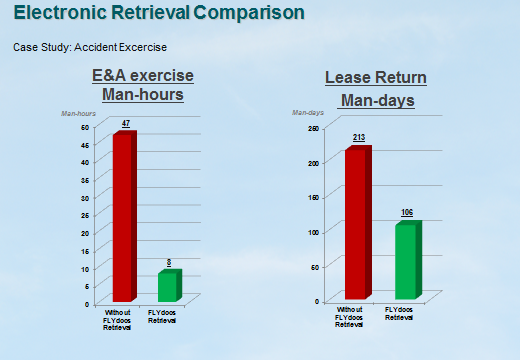
Figure 5
“… where the 47 required man hours to retrieve all the necessary documentation manually was reduced to eight hours when the electronic system was used. More routine and more interesting is that a lease return went from 213 man days to 106 of effort.”
This illustrated improvements to what we do today but Rob also emphasized that, if you can reliably do this then you don’t have to schedule your lease return aircraft into the hangar as you would normally, because you know there is more time to manage it and you know the records are accurate. When it’s possible to start more accurately predicting what components need to be replaced to meet return conditions this can be planned ahead, maybe even on the previous ‘C’ check. In this way airlines and operators can confident that there are no expensive surprises due the lease return process. It is particularly valuable to understand Engine compliance and life from the tech records as getting this wrong for the sake of paperwork availability can be unforgivably expensive.
“All this can be achieved from managing the data, managing the paperwork and having accurate configuration management and accurate data in the M&E system. But it’s an enormous task and that’s where mobility will help maintain this on a continual basis with low effort.”
TECH- AND CABIN-LOG PROCESS
Moving to something more specific, we wanted to look at the TechLog process which will be pretty much the same for all readers.
The paper process
Looking first at the paper process (figure 6)…
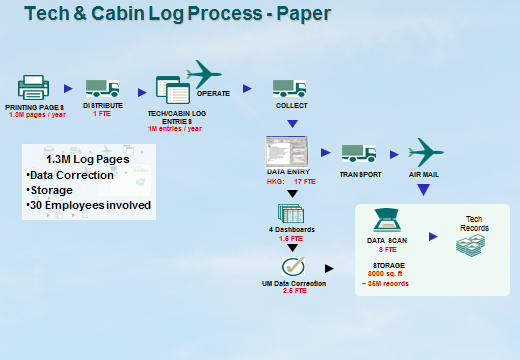
Figure 6
… Rob spelt it out, “With printing, distribution, recording entries on the aircraft, collecting the logs, data entry and, for the back office, dashboards to manage, it occupies a lot of man hours, including correcting data errors from this process, just to keep in compliance, maintaining MELs, part number mistakes and so on. Then it all has to be scanned into a system.”
The paperless process – e-log
In figure 7 you can see the effect of an introduction of e-log in a large airline.
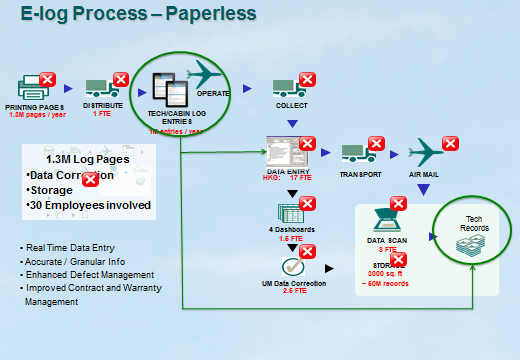
Figure 7
He talked us through the process. “E-log data is inherently accurate because it is driven by pre-determined tasks making it very difficult to make a mistake; the MELs are also accurate because they’re derived from data, selectable against defects. As the figure shows, typically an airline wanting access to tech defects an hour after departure may have 30 employees involved at touch points with probably half of those on data entry.” Airlines with service levels of 12 to 24 hours can reduce data entry staff but will ultimately suffer from defect drive disruption through lack of visibility.
The value of an electronic techlog
He continued the theme, “If fault trees have been built properly, there should be very accurate granular defect information; a key consideration is to have an application where you can build the granularity of what you’re trying to find in the future.”
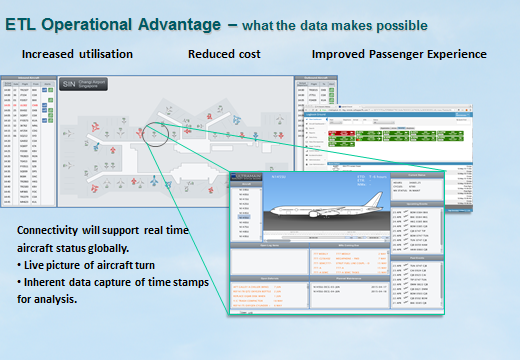
Figure 8
Available aircraft
Figure 8 is an action graphic, in this case using Changi Airport, Singapore, taking an assortment of data to portray where the aircraft is; then if a combination of e-log data and maintenance schedule data is taken, it can be displayed in a graphic that actually shows the aircraft, real-time, in transit. Rob described the benefit. “If you have an e-log that’s delivering real-time updates of what’s happening in the log itself, you can see the aircraft becoming available as work is progressed. Again that’s a productivity improvement but what does it really mean in dollars? For the airline, to know whether there is an aircraft serviceable but not yet released would normally mean calling the MRO and sending someone out to the aircraft. If you have an e-log that’s structured properly to deliver the information you can start to see the status in real-time; so from maintenance control or anywhere in the world, it’s possible to see that this aircraft is serviceable but not released. The flight crew and Ops center can see defects raised and cleared in real-time for much faster decisions. That’s important because aircraft switch and so forth and it can get quite complicated. Plus there is the ability to alert based on the defects that you are reporting if you codify your fault tree on the e-log at source. It’s an effort but it’s then there for everyone, making it possible to prioritize inbound defects and send the engineers to the right person.”
The case for remote sign-off
“With about 30 per cent of transits, there’s no defect found inbound; so, if we change the rules slightly on cabin defects there’s no reason technically why there could not be a remote sign-off. Technical too but let’s walk before we run.” Rob extended the point. “It would be much better to schedule the people to attend aircraft with defects than to schedule them to sign-off an aircraft with nil defects. There’s a lot of opportunity to move forward but realistically it will probably be a while before regulators buy in to that.”
This article will be continued in the next issue of Aircraft IT MRO.
Contributor’s Details
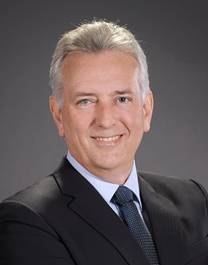
Rob’s career started with British Airways in 1977 then, in 1990, joined Cathay Pacific as a Maintenance Controller where he saw the introduction of the 747-400 and Airbus fleet. In 1994 he managed the Base Maintenance Support team then as Manager of the Maintenance Control Centre in 1997. In 2002 he held the position of Manager Ultramain Program, replacing Cathay’s legacy Engineering IT systems. In 2006 Rob was appointed Manager of Aircraft Engineering with technical responsibility for Cathay and Dragonair’s Boeing and Airbus fleets. As Head of Business Improvement & Lean, he led a team implementing many productivity and compliance related projects. Rob left Cathay Pacific in June 2017 to be a consultant but continues to support the One World engineering group, IATA Paperless Operations and standards and is currently chair of the Boeing /USI eLog user group.
Comments (0)
There are currently no comments about this article.
To post a comment, please login or subscribe.