Articles
Name | Author | |
---|---|---|
A question of integrity | Paul Saunders | View article |
Leaving and arriving safely and efficiently | Arno Broes, Partner and Commercial manager, ACFT PERFO | View article |
The problem with implementation | Captain Michael Bryan, Principal, Closed Loop Consulting | View article |
Case Study: Saving Fuel at Condor | Captain Frank Lumnitzer, Head of Fuel-, Environmental- and Air Traffic Management, Condor (Thomas Cook Airlines Group) | View article |
Case Study: Saving Fuel at Condor
Author: Captain Frank Lumnitzer, Head of Fuel-, Environmental- and Air Traffic Management, Condor (Thomas Cook Airlines Group)
SubscribeSaving Fuel at Condor
Captain Frank Lumnitzer, Head of Fuel-, Environmental- and Air Traffic Management at Condor (Thomas Cook Airlines Group) explains how he started and manages the fuel efficiency improvement program at Condor.
Introduction
Fuel costs represent between 30% and 40% of an airline’s total cost; and that’s true at Condor as well. Therefore, even small fuel savings have a huge impact on financial performance. In past years, Condor had implemented several of the ‘obvious and easier’ fuel efficiency improvement initiatives; so, overall we could be proud that Condor was already doing well regarding implementing best practices in fuel conservation. Nevertheless, the management of Condor asked my team to look for more opportunities. We started our enhanced activities in 2011 and have identified further savings opportunities amounting to more than 2.4% of our total fuel bill. So far, the program is progressing well inasmuch as we have already realized more than half of these savings.
We’d like to first share our view concerning how best to start a fuel efficiency improvement program. Then offer an overview of the most common fuel savings initiatives. Finally, we would like to describe what we consider important when identifying fuel savings opportunities and how to best manage fuel savings initiatives.
How to start
We cannot stress it enough – a successful fuel efficiency improvement program is a team effort. The best fuel efficiency expert will fail if working alone and not in a team including people from all relevant areas of the airline. Nevertheless there is no single solution applicable to each airline. The structure and culture of an airline are major elements influencing the ‘right way’.
In our experience the following three ingredients are required to make a successful fuel efficiency program: First the know-how about fuel conservation, then the proper organization including processes, and last but not least good software tools to manage fuel conservation efforts.
Know-how
A lot of good fuel efficiency know-how is already available: the IATA ‘Fuel Book’ (Guidance Material and Best Practices for Fuel and Environmental Management) makes good reading. Additionally, nearly all aircraft manufactures have published documentation describing ways to save fuel. Obviously, your own know-how is still very important, but the bulk of common initiatives have been well documented.
Organization and processes
A fuel efficiency program is only successful if the efforts are led by a strong and empowered team. One requirement before establishing the team is the clear will, mandate, and support from top management to really save fuel. Obviously, no management will object to fuel saving: however, will management support hold if procedures – maybe used for years – need to be adjusted? All fuel efficiency improvement programs will face such issues. Things need to be adjusted in order to save and, as you probably will agree based on your own experience, people can be very ‘creative’ in finding all kinds of reasons why things should not change.
In our experience, the optimal way to convince management, and, eventually, all those involved, is to be able to provide clear data driven facts. Therefore, it is crucial to have full transparency regarding how fuel is used and to be able to clearly show the potential savings.
The usual principles of change management should be followed in order to initiate the change of process and behavior of people. There is a lot of good general advice available on this topic. In the case of Condor, we put the focus on communication with all those involved and on having all areas of the airline represented in our fuel efficiency team.
Software
At Condor the ‘low-hanging fruits’ have already been picked. In order to get more fuel savings, we had to have a better understanding of how we really use our fuel. In the past we have used several Excel spreadsheets. However, the problem was that we had to first spend (or rather waste) our time collecting the required data from all kinds of data sources. After collecting the available data, even more time was wasted in checking the data and either eliminating or fixig wrong data. Anybody having already done such a program probably agrees that this a lot of work. Even more important, if we do not eliminate or fix the wrong data, we potentially make wrong analyses. This can lead to wrong conclusions or even loss of credibility if our analyses turn out to have major errors. An additional complication at Condor is that strong union restrictions prevent Condor from using FDM data.
The good news is that there are a number of fuel efficiency software applications available today. At Condor and the Thomas Cook Group of Airlines, we evaluated several software applications, finally, choosing software from Aviaso Inc.
We would like to have the best possible transparency, therefore, we integrate all the data sources containing data which influence fuel. Obviously, this is not just fuel data, it also includes schedule information, flight-plan information, actual information (such as flight-route information), weight & balance information, etc. We currently collect nearly 1,000 data fields from seven different data sources. On the one side, we integrate data coming from ‘standard’ airline IT systems such as Netline, LIDO, ACARS, or ADS-B. On the other side, we integrate data coming from our in-house/legacy IT systems. The integration of the standard airline IT systems was achieved very quickly, since Aviaso already has standard import adapters for these systems. The integration of the in-house/legacy IT systems was managed by Aviaso together with our own IT specialists.
Fig 1: Condor data sources
Fuel savings initiatives
There are various ways to group fuel savings initiatives. One way is to structure according to the area of responsibility. Another way is to do an analytical grouping. Below you can see the analytical grouping of the initiatives in the areas: flight operations, reduction of aircraft weight, flight planning, reduction.in fuel loading, APU-usage, maintenance, and other.
In the following we just would like to provide an overview of the possible fuel savings initiatives, and don’t want to repeat detailed information that you can find well in other documentation.
Flight operations
This includes initiatives performed during the course of a flight. These initiatives are mainly the responsibility of the flight crew. The flight operations initiatives are:
- Engine-out taxi-out;
- Delayed pushback;
- Take-off thrust setting (improve engine life/maintenance);
- Take-off flap setting;
- Acceleration altitude;
- Climb and cruise (profile and speeds/CI according to flight plan);
- Descent / approach;
- Landing flap setting;
- Idle reverse;
- Engine-out taxi-in;
- Reduced pack operation;
- Various pilot techniques.
A word of caution: risk analyses are important and should be done for all initiatives. However, a comprehensive risk analysis is of particular importance for all flight operations initiatives.
FIG 2: Reduced flaps at landing
Reduction of aircraft weight
This includes initiatives reducing the aircraft weight (dry operating weight). These initiatives are, typically the responsibility of various departments such as Commercial, Ground Operations, and Maintenance.
Obviously, the reduction of even small amounts of aircraft weight will lead to substantial fuel savings over time, say a year. The so-called Cost of Weight factor (CoW) allows calculations to include how much fuel is burned to carry a certain weight (see Aircraft IT volume 1, issue 5 Spring 2012). Accordingly, the CoW can also be used to calculate how much fuel can be saved by reducing by a certain weight. The CoW is essentially a function of the duration of a flight. The longer a flight, the more fuel is burned to carry the weight. The rule of thumb for the CoW is about 3.5% – 4% per hour of flight. For example; in order to carry 100 kg of weight for five hours, about 20 kg of fuel (five hours at 4 kg) is used. However, there are significant differences in the CoW factor depending on aircraft type, types of flights/network, etc. We are using the Aviaso software to exactly calculate the CoW-factor for our operation. This allows us to exactly calculate how much we are saving through reducing the weight.
The reduction of aircraft weight initiatives are:
- Commercial
- Reduce weight of seats, IFE, catering, duty free, newspapers, other contingency/reserve items;
- Diligent cleaning of cabin before every flight;
- Cargo: reduce weight of ULD (unit load devices).
- Ground operations
- Reduce potable water;
- Optimize lavatory servicing.
- Maintenance
- Reduce fly away kits;
- Reduce dust, dirt;
- Use zonal drying;
- Reduce weight of paint;
- Replace items with lighter items (e.g. LED light).
- Flight Operations
- Reduce crew-related weight (e.g. crew-bags, books, maps).
FIG 3: Reduction in aircraft weight: light weight catering equipment
Flight planning
This includes initiatives improving the vertical and lateral flight path, and initiatives regarding the cost index:
- Review flight-planning software and flight-planning process;
- Lateral flight path/route selection;
- Vertical flight path;
- Cost Index;
- Continuous update of routing during flight / mission management.
Condor is working in close cooperation with Air Navigation Service Providers. We are using fuel and trajectory related statistical data out of our fuel management system to evaluate potential improvements and propose such improvements to the Air Navigation Services in order to optimize our flight trajectories.
FIG 4: Lateral and vertical profile
Reduction in fuel loading
This includes initiatives reducing the fuel loading. These are mainly the responsibility of flight planning/dispatch and the flight crew. Overall, there are various ways to reduce fuel loading which eventually mean less fuel is burned since less fuel needs to be carried (see above in the section regarding the Cost of Weight). However, one clear statement has to be made here: whatever reductions are being made regarding the fuel loading, the main criteria is to have the ‘right’ amount of fuel for the safe execution of a flight. Obviously, there is not just one right amount, and in our view, it still needs pilots’ judgment and experience to determine what is ‘right’.
We strongly believe that having the most information regarding a flight is the key to best support the fuel decision of the flight crew. In the case of Condor, we have purposely not made any restrictions regarding the amount of extra fuel (also known as discretionary fuel) that pilots are allowed to take. Our philosophy is rather to provide information to the flight crew that allows them to make well-informed fuel decisions. At Condor, we developed, together with Aviaso, the Fuel Efficiency Flight Briefing functionality and provide pilots with various fuel related information for their upcoming flight. With this approach, we have been able to substantially decrease the amount of extra fuel loaded by flight crews. At the moment we are showing various data from the past 12 months for a city pair including, times, fuel, distances, extra fuel used, etc. The information contains not only average figures but also deviations. Since the fuel efficiency flight briefing is an important enabler and popular among flight crews, we will extend it with further information such as lateral and vertical profiles of the departure and arrival, etc.
Fuel loading can be reduced with the following initiatives:
- Alternate fuel;
- Contingency fuel;
- Additional fuel and company fuel;
- Taxi fuel;
- Final reserve;
- EROPS/ETOPS/LROPS (extended range operations/extended twin engine operations/long range operations) fuel;
- Prevent over-fuelling;
- Pilots’ discretionary/extra fuel.
APU usage
This includes initiatives to reduce APU (auxiliary power unit) usage. Depending on the time of APU usage, these initiatives are the responsibility of the flight crew, ground-ops, or maintenance. Optimization of APU usage can lead to substantial savings. At Condor the first step is, again, greater transparency. In order to determine the potential for improvement, we need to know when the APU was used by the flight crew (e.g. during turn-around) or by ground-ops and maintenance. Results of that analysis have been transferred into an APU/GPU (GPU: ground power unit) availability list provided to flight crews for an optimized decision in APU use.
Maintenance
This includes all the initiatives exclusively available in the maintenance area:
- APM (aircraft performance monitoring);
- Engine washing;
- Aircraft washing;
- Engine: improve SFC (specific fuel consumption);
- APU: improve SFC;
- Aircraft: rigging and regular maintenance;
- Aircraft: modifications;
- Aircraft paint.
Other
This includes all the initiatives in other areas such as:
- Fuel tankering;
- Fuel-efficient tail assignment;
- Optimal CG (center of gravity).
How to realize fuel savings and manage initiatives
Above, we have shown how to start a fuel conservation program and have provided an overview of the typical fuel savings initiatives. In the following, we would like to describe how we realize fuel savings and how we manage the initiatives.
Typically, realizing fuel savings and determining their potential works in a very similar way for all our initiatives. The first step is always to provide transparency. Then we must ensure that the data is of good quality, and eliminate or correct erroneous data. Afterwards, we can use the analytical power of the software with the possibility to look into the data from different points of views (e.g. by fleet, by time, by time of the day, by runway, by airports, etc.). The Aviaso software provides countless ways to group and filter the data and even allows defining powerful user-defined analyses in addition to the many built-in analyses. If needed we can drill-down to see more details or sort and combine the data in various ways. By doing so we can determine if we have a general improvement potential for an initiative, or if an initiative will only bring improvements for e.g. certain airports at certain times of the day etc.
Once we have determined the savings potential we use the DCIM model to manage initiatives:
- Discover: discover and assess the fuel savings potential
- Commit: commit regarding which initiatives to implement
- Implement: implement the selected initiatives
- Monitor: monitor the progress of the implementation and adjust if required.
It is important to set priorities, start with a manageable number of initiatives and successfully implement those initiatives. At Condor we essentially group the initiatives according to the two criteria of fuel-savings potentials and efforts to implement, and naturally work first on those initiatives that have high savings potential and low implementation efforts.
An important factor in the management of the initiatives is the monitoring step. We can only know whether we are on track if we have timely feedback as to whether our initiatives are working or not. In the past we had either no information or only much delayed information. We have now nearly instant monitoring capabilities and essentially know every day how we are doing regarding our initiatives. Should our actual figures be lower than targeted, we can react early and initiate the required adjustments.
FIG 5: savings over time
The real strength of a fuel efficiency tool will be when it can be embedded into rather than bolted on to the existing operations IT infrastructure. That way it becomes accepted as part of the routine of business at all relevant levels in the operation. It took Condor a while to not simply implement another tool but also to make it an accepted and acceptable part of the business through application of user friendly interfaces, by integrating the dashboards into our existing intranet solution and by full integration into the crew portal. Within Condor, that strategy proved correct as the tool is now accepted as the master system for all analytical fuel work within the company.
CAPT. FRANK LUMNITZER
CAPTAIN FRANK LUMNITZER, HEAD OF FUEL-, ENVIRONMENTAL- AND AIR TRAFFIC MANAGEMENTAT CONDOR (THOMAS COOK AIRLINES GROUP)
Frank Lumnitzer started flying in 1994 as a First Officer within the Lufthansa group at Condor Airlines. In 1996 he was appointed Technical Pilot of Condor’s B757/B767 fleet, responsible for operational certification of all Lufthansa fleets for RNAV and was project leader for the development of several RNAV standard instrument procedures. In 2004 Frank was deployed to His Majesty Sultan’s Flight Brunei, and in 2006 was upgraded to commander on B757/B767. Today he is a B757/B767 training captain and member of the senior trainer group. He was appointed Fuel Manager in 2009, responsible for fuel-, environmental- and air traffic management issues. Frank is also chairman or member in Airbus’s FAIR working group, Eurocontrol RNP implementation Support Team, German PBN Implementation Support Team, Expert Group for Active Noise Abatement, and ICAO PBN Task Force & GO Team.
CONDOR
- Founded: 1955
- Headquarters: Frankfurt, Germany
- More than 6.7 million passengers per year
- More than 3,000 employees
- 40 aircraft
- Part of Thomas Cook Airline Group (91 aircraft)
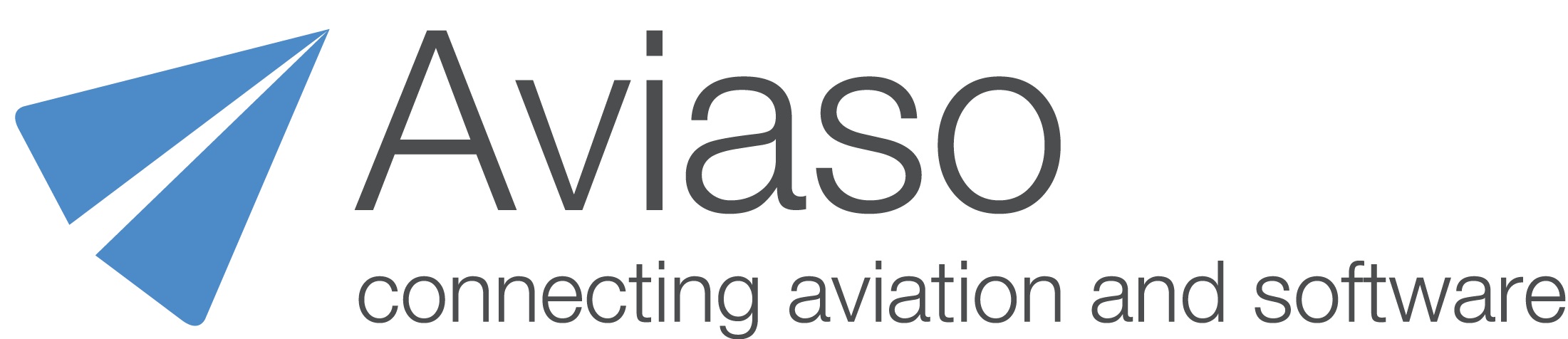
AVIASO/FUEL EFFICIENCY SOFTWARE
- Start software development: 2008
- Airlines using software: 10
- Number of aircraft monitored: over 400
- Modules included: Data collection, data quality
- Assurance, analysis, and communication
- Ready-made data import adapters and automatic
- Data quality checks
- More than 100 analyses and initiatives
Comments (0)
There are currently no comments about this article.
To post a comment, please login or subscribe.