Articles
Name | Author |
---|
Saving fuel, reducing emissions and a culture of improvement at SpiceJet
Author: Nittin Gulati, Deputy General Manager IT, SpiceJet
SubscribeNittin Gulati, Deputy General Manager IT, SpiceJet shares how the airline has driven quick cost reduction with fuel efficiency.
As the title suggests, the core topics to be covered in this article are cost reduction and fuel efficiency, but before we go into those, a few words about SpiceJet, the airline where it all happened.
SPICEJET
As India’s fastest growing airline, SpiceJet aims to offer a value for money travel experience across its domestic and international network. The airline is also the largest cargo carrier in India with 11 freight aircraft. The group has a focus on growth and, in that context, is constantly looking out for new opportunities for improvement. One landmark achievement has been the induction of 30 aircraft in three weeks in 2019, which is a record. In 2020, because of the strange times, SpiceJet expanded cargo operations and has now become the largest cargo carrier in India.
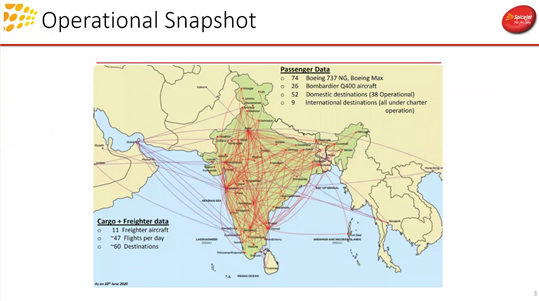
The airline has a strong track record for IT innovation and for wider innovation; whether that be in tooling and the automation of airline processes or working with different airports to move away from legacy software and look for innovative solutions, increasing the efficiency of different airports and different airport processes. The drive for innovation and improvement also extends to the aircraft: SpiceJet has conducted the first BioJet fuel powered flight in India and, in late 2020, launched the first seaplane service in India. SpiceJet’s fleet includes more than 100 aircraft with a mix of Boeing narrow body types from the 737 family and Bombardier Q-400, serving 53 domestic and nine international destinations (figure 1).
The fleet and network are continually growing and will hopefully be boosted by the anticipated return of the Boeing 737 Max to service during 2021.
SAVING COSTS
As a responsible operator, SpiceJet is always alert to cost saving opportunities. Ajay Singh, SpiceJet’s CEO says that, “The focus is clearly on growth and, at the same time, to keep costs lower to ensure we are profitable; and we are quite confident that we will achieve the profitability target.”
Looking at costs, as for any airline, SpiceJet’s biggest cost is on fuel which means there is a constant search for initiatives that can help us to save costs on fuel because that has a direct impact on the bottom line. SpiceJet has established some goals as to what it wants to achieve with a fuel efficiency program. These are the focus areas in terms of primary objectives, and how to ensure that the programs follow best practice.
Data is the first priority in a fuel efficiency program and that data can be useful in training plus the data science team can conduct data modelling; depending on the strength of data gathered, forecasts can be made and patterns identified. It all starts from the very top having the right representation of the data. It is important to gather the correct data on fuel consumption and the real-world parameters contributing to a reliable fuel efficiency analysis. Good quality fuel data will also support better fleet maintenance and better fleet performance. Having collected and analyzed the data, SpiceJet compares planned versus actual parameters and uses best practice compliance to identify the root causes for deviations of actual from planned. It then drives pilot training; using correct data to move towards the adoption and implementation of best practices.
Moving on, I want to share with you the journey SpiceJet took to achieve those goals and how SkyBreathe® helped with that journey.
BUILDING THE FUEL EFFICIENCY PROGRAM
At SpiceJet, a fuel efficiency team was set-up whose first consideration was to acknowledge that there are many stakeholders who are directly or indirectly impacted by the program and fuel management (figure 2)
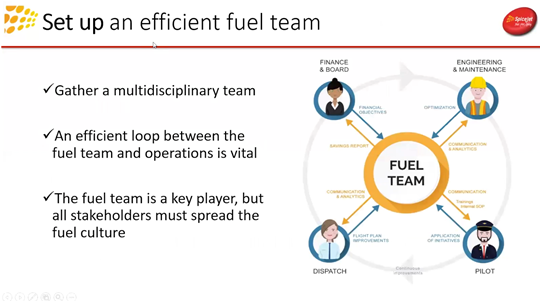
Dispatchers, for example, determine how much fuel will be needed for the flight, pilots are able to add discretionary fuel as they are the ones using it. Finance will be involved negotiating with the different vendors and fuel suppliers plus engineering and maintenance also have a part to play tracking the maintenance of aircraft, which also has an impact on fuel consumption. Then the IT brings it all together, ensures that processes are automated and that data flows smoothly between various systems, etc. For these reasons, we decided that SpiceJet’s fuel efficiency team should be a multi-disciplinary group who can analyze the bigger picture and address it strategically. Also, it was important to have an efficient loop between the fuel team and Operations.
The fuel team is a key player but, given that this is the biggest cost for the organization, stakeholders must also spread the fuel efficiency message throughout all relevant departments. These were the priorities we identified when setting up the team for the fuel efficiency program at SpiceJet, and this was all in place before SkyBreathe was implemented. SpiceJet was already analyzing a lot of data but was facing issues with data integrity and availability. It was at this stage that we decided to work with a partner and it was decided that SkyBreathe offered the best fit.
IMPLEMENTING A FUEL EFFICIENCY SOLUTION
As part of the implementation program, the team devised a Roadmap as to how the program should proceed (figure 3).
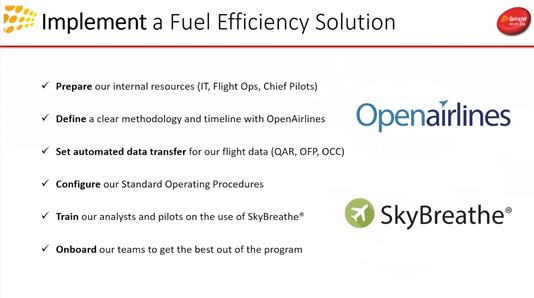
The scope was defined, internal processes were understood, SOPs (Standard Operating Procedures) were created around it and the team made sure that everyone was involved, all the relevant stakeholders were given equal participation and the opportunity to give feedback to ensure that the team was looking at the right picture, getting the right requirements fed in for the implementation. Once SkyBreathe had been set-up, SpiceJets’s fuel analysts were trained to use the tool and were familiarized with the custom reports that SpiceJet had specified for our management.
LOOKING FOR IMPROVEMENTS
Once all that had been implemented, the next step was to ensure the effective use of the tool (figure 4). The view in SpiceJet is that a tool is as good as how it’s used: there is no point in implementing something if you’re not going to use it effectively.
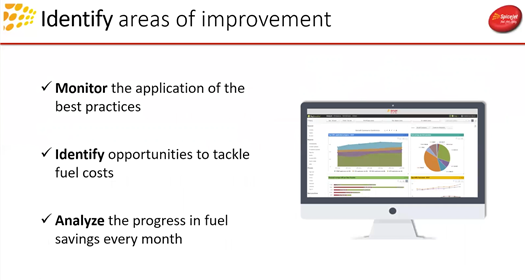
SpiceJet did their governance and put the SOPs into place to ensure continuity, to monitor the data, look for improvements and present the data to all stakeholders, including pilots who are the absolute key to establishing best practices in the airline. What was seen was that pilots were absorbing the new ways and their training, as a consequence of which, we started to see some quick gains and good results within just a few months.
Once SpiceJet was comfortable as to the accuracy and utility of the data, MyFuelCoach mobile Pilot App was made available to all pilots to make it possible for them to track their individual flights. While the App was useful for tracking individual flights, there was also a monthly summary report set up as a performance chart for all pilots to give them a quick overview of how they’re doing, what cost savings they’ve achieved in the past month, information about positive practices and reiterating that they should keep on with them in order to ensure that the program has a major impact on fuel consumption, bringing it down and moving towards best practices.
There is also a monthly forum with Chief Pilots, Senior Dispatchers and other senior stakeholders to monitor what’s happening, how much improvement has been achieved, the state of key performance indicators and even challenges that have been encountered and which can be identified in order accordingly to inform further or revised training to maintain progress in the right direction. Engaging pilots in the fuel efficiency program is a key contributor to achieving further savings.
RESULTS IN THE FIRST SIX MONTHS
This covers the period from mid-September 2019 until mid-March 2020. At the start, SpiceJet had already achieved a good level of cost savings amounting to about US$2.4 million using internal savings programs but there were some issues in terms of data correctness. As soon as SkyBreathe was implemented (figure 5), savings increased by about forty percent…
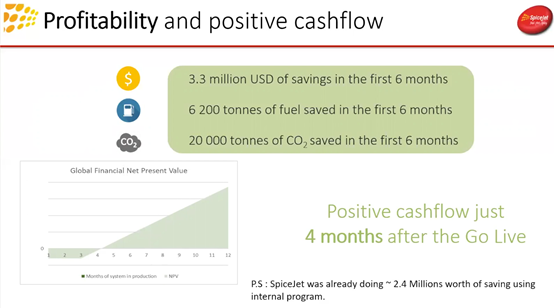
which equated to US$3.3 million, 6,200 tonnes of fuel and 20,000 tonnes of CO2 emissions saved in the first six months. Those are huge numbers but best of all, the data used to determine that could be trusted and presented to pilots to give them an accurate picture of how they are doing, how they are helping the organization and training them.
The ROI (return on investment) was excellent with a full return in just four or five months of the Go-Live which made it a quick win for SpiceJet adopting SkyBreathe and a great ROI to present to senior management as well as adding value to the organization – especially relevant in the past year.
Figure 6 relates to some of the ‘best practices’ at SpiceJet and, in particular, the savings that have been achieved through using them.
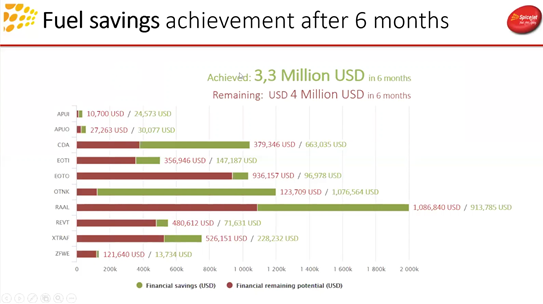
The savings are divided into two groups; first, the remaining potential for saving, the red bars, identified by the tool using SpiceJet’s data with no manual intervention which means that anyone who has access can quickly get this information. SpiceJet’s own achievements, the green bar, are compared to best practices across the sector as well as savings achieved. The potential is still huge in terms of what is still available to be achieved on top of what has already been achieved. Of course, remaining potential will vary according to on-the-ground conditions so that users will not always achieve 100 percent of the potential; but it does offer a pointer to what might still be possible.
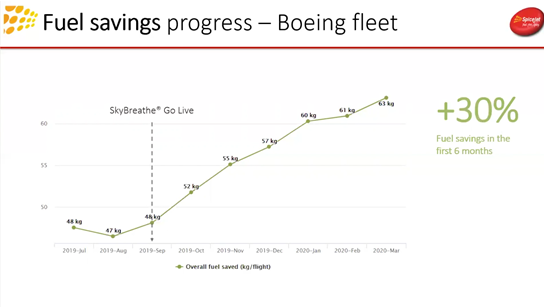
Moving further, figure 7 shows, for SpiceJet’s Boeing fleet, how much fuel was saved per flight. It shows that, at SkyBreathe Go-Live in September 2019, SpiceJet was achieving fuel savings of about 48kg per flight using some best practices that had been set-up internally. With the implementation of SkyBreathe, and correct data being used in the right manner at the right time, a feedback loop was created which resulted in an instant growth in savings in the order of 30 percent of new savings in the first six months.
There were similar numbers for the Q400 fleet (Figure 8), a 25 points improvement in the first six months. The two figures make good viewing for senior management as they show that something that has been implemented is innovative and helping the airline move in the right direction.
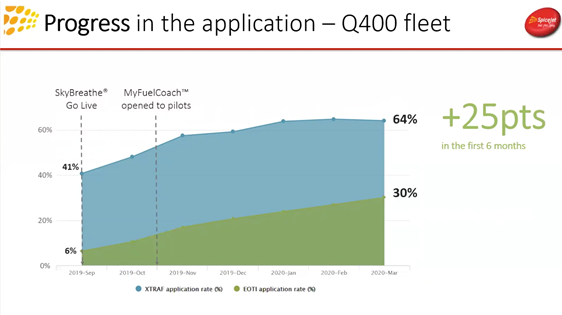
As part of the program, one of the objectives was to train pilots and we did that conscientiously at SpiceJet. Figure 9 shows how confidence in and training with the new solution translated into a reduction in the average extra fuel that pilots carried on a flight.
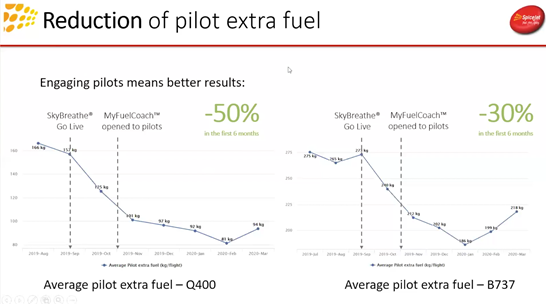
The graph on the right side of the figure was seen to be going down, looking at the data, but then, if you look at February and March 2020, you’ll see that the numbers went up again. That has nothing to do with the tool or how pilots are performing; it’s because, during the month of February there was a regulatory change to the minimum fuel to be carried, which caused the increase. I left it in the presentation to show that, when SkyBreathe went live, the graph came down but there are sometimes changes beyond our control, this time from the regulator, which will impact on fuel. Notwithstanding that, the program is still on the right path towards savings on the average pilot’s extra fuel and, of course, less weight on the aircraft means more fuel savings.
CONCLUSION AND THE WAY FORWARD
SpiceJet was able to achieve a quick ROI with SkyBreathe with a rapid increase in fuel cost savings helping to achieve the business’s goals. Up to the time of writing, there had been no data issues with SkyBreathe and it has helped SpiceJet’s teams to build their confidence in the use of and correctness of the data. It gave the opportunity to engage the airline’s pilots in near-real time with the idea of using data to keep a track on their flights, and that has had a direct impact on fuel saving given that they are the ones who use fuel in the aircraft. It has helped the airline to progress towards the use of best practices. Also, in terms of the implementation, it was, at five months, slightly longer than anticipated: it was planned to finish in three or four months; however, that was slightly delayed in order to get the data out of the legacy systems into SkyBreathe, to ensure the format was correct and the automated prompts were set up so that there would be no need to engage a manual process in order to get the necessary data to SkyBreathe.
The future
Looking forward, there are a number of questions that are routinely asked at SpiceJet. All ASEAN businesses in the sector have taken a hit and gone into survival mode which means focusing on things that have a direct impact on cost savings. The questions asked at SpiceJet every day are ‘how can we save costs and ensure that what we are doing is necessary’… To be honest, in the past six months, many programs have been suspended because they were not deemed to be required at the moment but SkyBreathe has been accepted as being of such importance and relevance and found to be so useful that it has been maintained to ensure that it continues to deliver the savings and helps to build a culture in the airline using the best practices throughout the business. Whether for dispatchers, pilots, trainers, fuel analysts, or the data science team, the culture of continuously using the right data, looking at the right picture and moving in the right direction has become embedded. That’s one program that will be continued given the value already, the potential for future savings.
SpiceJet was interested to identify what other things might be done to save costs, how fuel can be saved which will have a direct impact on operations and the bottom line. Any savings will help in the current COVID dominated climate and even when expansion re-commences and when new routes are introduced, it will be important to retain and build on that efficiency culture during growth. A fuel efficiency program is key to preserving cash, boosting competitiveness and recovering profitability in a very limited timeframe.
SpiceJet will continue with SkyBreathe which is proving an immense help in saving money, reducing fuel consumption and, more importantly, building the right culture throughout the organization, a very important consideration.
Contributor’s Details
Nittin Gulati
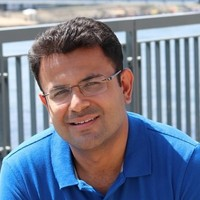
After graduating in Computer Science, in 2012 Nittin joined easyJet as a Software Engineer then Sopra Steria as a to Project Manager. In 2018 he joined SpiceJet as a Project Manager and is currently Deputy General Manager IT. Nittin is an Aviation IT expert, experienced in managing teams and with a passion for the industry. He is also experienced in leading multiple large-scale implementations with quality on time delivery and adding value to the business.
SpiceJet
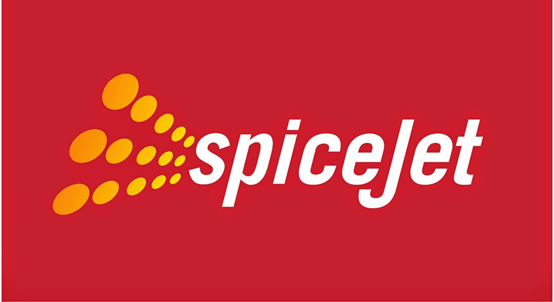
SpiceJet is an Indian low-cost airline and the second largest airline in the country by number of domestic passengers carried. The airline operates 630 daily flights to 64 destinations, including 54 Indian and 15 international destinations from its hubs at Delhi and Hyderabad. The fleet, totaling nearly 120 aircraft (including some freighters) with more than 220 on order, includes Airbus A320 and A330 types, various Boeing 737 models and De Havilland Canada Dash 8 models.
Open Airlines SkyBreathe
OpenAirlines is an international software company based in Toulouse, with offices in Hong Kong, and Miami. It provides consulting and software solutions for airlines flight operations. Since 2006, OpenAirlines has been on a mission to help airlines save 2-5% of their fuel consumption with its innovative eco-flying solution SkyBreathe. The software uses Big Data algorithms and automatically analyses the large amount of available data in flight data recorders to assess flights’ efficiency.
Today, 40 airlines all over the world use OpenAirlines’ software.
Comments (0)
There are currently no comments about this article.
To post a comment, please login or subscribe.