Articles
Name | Author | |
---|---|---|
Predictive maintenance — beyond the buzzwords | Sander de Bree, Founder & Chief Visionary, EXSYN Aviation Solutions | View article |
Digital twins: improving the way things work and wear | Nadine Etong, Director MRO Product Line, IFS | View article |
Smartwings App helps better manage parts | Petr Barton, Operational Supply Chain Manager, Smartwings | View article |
Looking for a smarter supply chain in MRO: Part 1 | Amol Salaskar, Consulting Business Analyst in Aviation and MRO, IBM | View article |
Smartwings App helps better manage parts
Author: Petr Barton, Operational Supply Chain Manager, Smartwings
SubscribeSmartwings’ App helps better manage parts
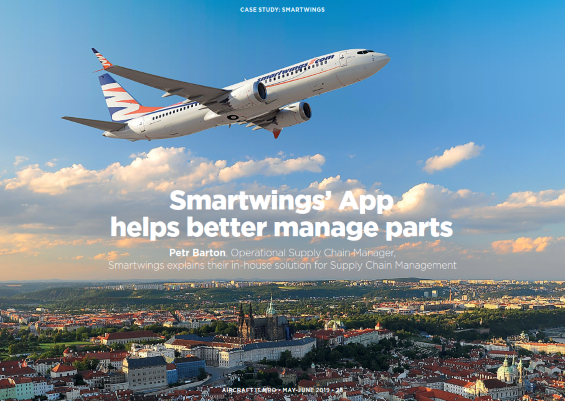
Petr Barton, Operational Supply Chain Manager, Smartwings explains their In-House Solution for Supply Chain Management
Petr Barton, Operational Supply Chain Manager, Smartwings
Supply chain is a critical element in the efficient management of aircraft engineering and MRO and so, in this article, I want to share with readers the story of our in-house supply chain management app that we built and use in Smartwings. But, let me first tell you something about the airline.
ABOUT SMARTWINGS GROUP
There are two brands, Smartwings and Czech Airlines, in the Smartwings Group plus subsidiaries in Hungary, Poland, Slovakia and Germany, operating scheduled flights, charter flights and private flights. In 2018, the group carried ten million passengers from 14 bases across seven countries.
Smartwings
Based at Václav Havel Airport in Prague and the largest airline in the Czech Republic, with a fleet of around 42 aircraft (mainly Boeing 737 variants: -700, -800, -900 and MAX), Smartwings is also one of the fastest growing carriers in Central Europe. It operates to holiday destinations plus dry leases to other airlines as well as scheduled local flights and business charters with a fleet of Cessna 680 business jets.
Czech Airlines
Czech Airlines is the fifth oldest airline still operating in the world with a fleet of 18 aircraft operating scheduled flights. The fleet consists of Airbus A319, A330 as well as ATR 42 and ATR 74 types. The business is 97.74% owned by Smartwings.
AVIATION SUPPLY CHAIN MANAGEMENT APP, MATMen
Smartwings Group in-house solution and app for supply chain management is MATMen and is built in modules.
Stations Parts Management
The first module is Stations Parts Management and the idea behind this module was to reduce the communications between outstations and central stores in Prague, and to reduce the many Excel documents used for material requests, inventories and suchlike. It was developed to deliver complete parts management, to offer a full parts/logistics overview for each station and to manage and cover these functions for each station in one place. MATMen offers an overview of incoming shipments in a window showing all shipments shipped from main base to station: the outstation staff confirms delivery of parts and receives the parts into inventory. The app also shows exchanged parts that need to be returned to the supplier on time. Station staff can create a part request and have an overview of that request to check where parts for planned works are, with the option to search by work orders and the capability to receive the parts into the station inventory. They can also see the inventory and minimum levels in their station and the app offers unserviceable parts management. The main window (figure 1) shows incoming parts as they arrive at the station plus an overview of parts that they need to return to the central stores.
Figure 1
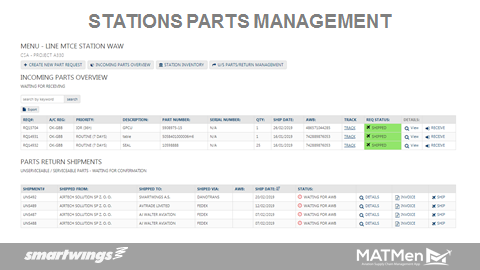
Station Minimum Levels
Part of the Station Management process was for the management of minimum levels so there is a Stations Minimum Levels module (figure 2)…
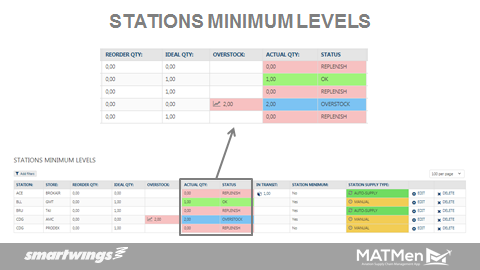
Figure 2
… created for monitoring and administering minimum levels at the stations. Each minimum level has three statuses offering an overview of the quantities of parts at the station, whether there is a need to replenish parts at the station or if some material is overstocked at the station. The minimum level for each station is calculated in real time based on consumption of the material.
For some stations, we have also introduced Automatic Stations Replenishment (figure 3)…
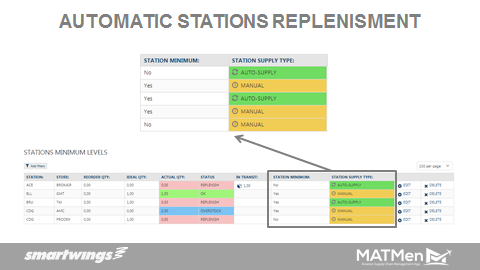
Figure 3
… so that, for each station, it is possible to set an automatic supply process; it means that, when the available quantities fall below the minimum level, the automatic system will generate a replenishment part request and create an automatic shipment for the stores into the stores module.
Parts Master Information
We also created a more detailed Parts Master Information module (figure 4)…
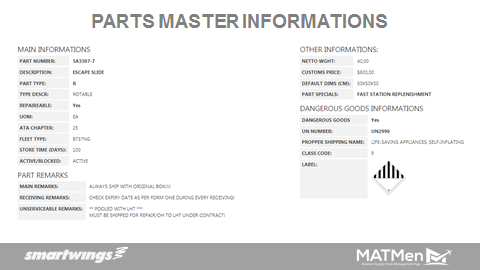
Figure 4
… with better information for every user. Parts Master Information shows details of dangerous goods, default repairs stations, remarks for each step of the material’s progress, default custom price, dimensions and any special information.
Stores Module
Stores module was developed to improve the efficiency of our main store (which was previously not so efficient), to reduce levels of human error and to ship parts without any delay. The storekeeper needs to acknowledge each new shipment from the logistics department that has been created in stores, and wait for confirmation and preparation. During the acknowledgement process the storekeeper or stores manager is able select which shift will prepare the parts in that shipment for effective work planning. After the shipment is prepared the storekeeper confirms that shipment is ready and waiting for shipping /customs clearance. For AOG (aircraft on ground) shipments and if working out of working hours, the stores team are able create, in their module, a new shipment which needs be shipped as soon as possible. This module produces for each shipment:
- A picking ticket;
- A Customs Invoice / Packing Slip; and
- Automatic notification for each outstation about new shipments.
The implementation of this module for daily operations across all of the Smartwings Group has facilitated a large reduction in errors plus all outgoing shipments can be effectively tracked, performance records can be created and shipping costs can be checked. There is a shipments overview with delivery status and proof of delivery for each shipment (figure 5).
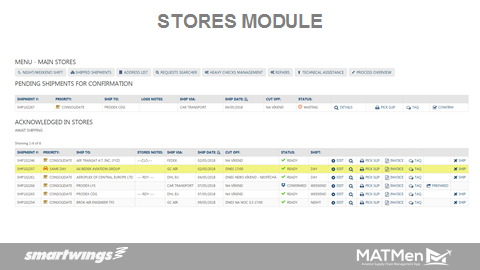
Figure 5
Transport Management
This module was created to monitor cargo transport: it is fully connected into the group’s logistics module. The purpose of the Transport Management module (figure 6) is to monitor actual weight and limits of the cargos. This module also notifies the stores team when a cargo reaches the weight limit for the cargo and it is also used for our cargo transport scheduling.
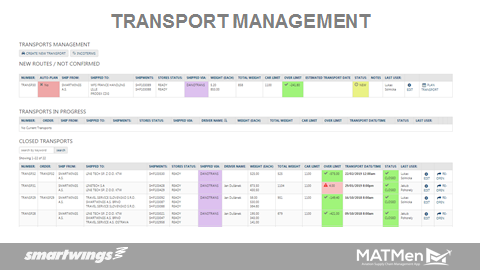
Figure 6
Material Return Management
For the return from different stations of unserviceable materials and serviceable materials that are overstocked, we have this module. It overviews what material is stored on each station and waiting to be returned. The module allows each station to generate shipping documents and easily ship parts back to the main store without any delay or having to wait for information.
Automatic Repair orders
This module was introduced to speed up the shipping process for unserviceable parts to the repair shops. It has automatic repair order generation as per the default setting of the repair stations. For each part number, after receiving the parts at the main base in Prague, the system will automatically generate the repair order to allow the stores team to ship parts immediately without delay or any time spent waiting for the repair manager to create a repair order and send that back to the stores.
C-CHECKS MATERIAL MANAGEMENT
We’ve seen lots of problems with materials requests every year when we’re in the heavy check season. Our heavy maintenance is fully outsourced between MROs in Romania, Hungary and the United Kingdom. With each heavy maintenance check, we have a representative from purchasing department on site. There are hundreds of emails between the MRO, the stores and the purchasing team every day and there were big problems due to the fact that all requests came from the MRO on Excel sheets with many versions. So, our second supply chain challenge was the heavy checks management and the module that was created to handle this improved several processes:
- A reduction from the hundreds of emails that had been generated daily;
- A reduction in the levels of error occurring with materials preparation;
- A single point of communication was created between Smartwings and the MRO;
- All material, requests are now available in one place.
An overview was created for each C-Check to reduce the many Excel sheets that had previously been used. Now, the purchasing people receive a request from the MRO and insert the new material request into this module. They can insert many types of material requests plus any purchase order and any exchange order whether or not the material will come from the main stores. They can also insert the work order details and the work order information, when the part is required and, when the part is shipped from the main base in Prague, the checking information is available immediately in the module.
BENEFITS
Use of the app has reduced email communications because everything is handled through one app. It is also good that we are not waiting for replies but are communicating directly via the app with everything in one place. That has been the main benefit plus we have managed to eliminate many versions of Excel and Word documents – a definite gain in the quality of work.
Currently, the app does not interface with any MRO system but we are thinking about that. In Smartwings we are considering how to achieve a connection for the parts requests and inventory from the current MRO System to MATMen. There is also the possibility that new developments will bring further benefits; for instance predictive maintenance seems to have the potential to further increase the efficiency of automatic supply replenishment.
There are certainly many future opportunities to use MATMen to improve the way that the Smartwings Group handles supply chain in support of more efficient maintenance processes.
Contributor’s Details
Petr Barton
Starting at Smartwings in 2013 as storekeeper, after two years Petr was promoted to team leader of exchange control department and then, in 2016, to Inventory Manager with responsibility for the main store and outstations supply chain. In March 2018 he was appointed Operational Supply Chain Manager to build and manage a new Operational Supply Chain department focusing on outstations’ material management, logistics activities and a 24/7 AOG Desk.
Smartwings
Smartwings Group has two brands, Smartwings and Czech Airlines, plus subsidiaries in Hungary, Poland, Slovakia and Germany, operating scheduled flights, charter flights and private flights. In 2018, the group carried ten million passengers from a total of 14 bases across seven countries with a fleet of around 60 aircraft: Boeing 737 variants: -700, -800, -900 and MAX, plus Cessna 680, Airbus A319 and A330 as well as ATR 42 and ATR 74 types.
Comments (0)
There are currently no comments about this article.
To post a comment, please login or subscribe.