Articles
Name | Author | |
---|---|---|
Case Study: Building innovative route optimizing flight planning platform at Qantas | Mike Riegler, Manager Business Innovation and Support Flight Operations, Qantas | View article |
Solutions In Practice: Safely fixing the pilots’ devices in the cockpit | Alex J Rodrigo, VP/FAA DAR-MFG at Avionics Support Group (ASG) | View article |
Case Study: Big data improves operations and fuel performance at Cebu Pacific | Francesc Torres, Director Operational Support, Cebu Pacific | View article |
Solutions In Practice: Safely fixing the pilots’ devices in the cockpit
Author: Alex J Rodrigo, VP/FAA DAR-MFG at Avionics Support Group (ASG)
Subscribe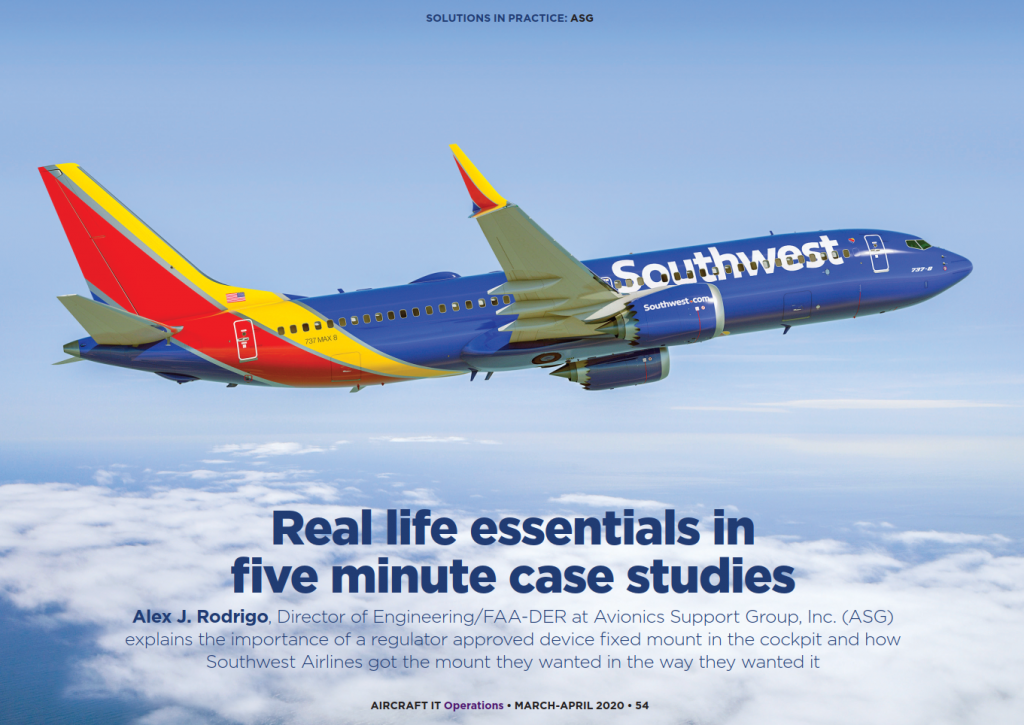
SOLUTIONS IN PRACTICE
The importance of a regulator approved device fixed mount in the cockpit and how Southwest Airlines got the mount they wanted in the way they wanted it
Alex J. Rodrigo, Director of Engineering/FAA-DER at Avionics Support Group, Inc. (ASG) explains about the unsung hero of any fixed device based system used in the cockpit. Without a safe and well-positioned mount, a device will at best be awkward; at worst, a safety issue.
Using a fixed mount for a device in the cockpit
The first reason for using a fixed mount is that most if not all suction cups eventually dry up and fall off the window during flight. A fixed mount solution does not have that problem but provides an approved viewable stowage location for the EFB or PED. An FAA-certified mount fixture will have been evaluated for human factor considerations; plus a fixed EFB mount is not a temporary solution and can be adapted to changing device requirements. Avionics Support Group’s fixed mount or cfMount™ (Constant Friction Mount) provides an FAA-approved solution that can evolve with the airline’s EFB program.
The challenges when mounting an EFB or any device
The main challenge is finding a location that offers maximum pilot visibility without interfering with cockpit controls or egress. The location also has to provide sufficient existing structure to attach the mounting device. Because the mounting solution is under an STC (Supplementary Type Certificate), regulatory compliance has to be accepted by the airworthiness authorities to approve the location of the mount. Concerning the operators, one of the challenges for them is to realize and see the value in a long-term solution vs a cheaper short-term alternative that requires replacement and is not FAA certified or approved.
The considerations for ensuring pilot visibility
Human factor compliance during certification ensures pilot visibility; this considers the field of view which is evaluated in accordance with CFR 14.25.771. It also takes into account the glare and light interference, this is easily accomplished with ASG mounts as users can adjust the view angle and position with one hand due to the constant friction design – no tooling or clumsy levers required. The last thing we consider is egress to ensure no interference from the device in the proposed location.
The considerations and challenges for fixing and positioning mounts in different aircraft types
There are a few challenges to consider. These will include commonality in location and viewing angle, non-interference with pilot controls or egress, available cockpit space to install a fixed mount, multiple STC certifications across different aircraft types and designing a common installation to reduce installation time. Other engineering and use issues include making sure that the mount and device do not block or impede the existing window shade, the donning of the Oxygen mask or steering control.
The history of ASG and the Constant Friction Mount, including the granting of STC in 2005
In 2005, ASG had the opportunity to do the first Class 2 EFB STC on Miami Air’s Boeing 737 fleet: this took around 18 months since it was the first of type. ASG listened to the pilots on how they would use the EFB and their needs, from which we came up with the constant friction mount design. This design was so unique that it also received a US Patent and today it is used worldwide by many airlines. The design is very rugged and reliable and is also adaptable to many configurations.
A case study for Southwest Airlines
Avionics Support Group (ASG) was contracted by Southwest Airlines to generate customized engineering data for the installation of the cfMount™ on a Boeing 737.
Key requirements for this installation, as outlined by Southwest Airlines, were:
- The installation must be able to be performed within less than two hours per window modification.
- Installation kits must be identical for both the Captain and First Officer windows.
- The Standard cfMount™ must be able to receive the quick release system that is integrated into the device cases used by the Pilots.
Based on those requirements, the solutions were:
- Although, in the past the installation kit required that the mechanic performing the modification would have to assemble all hardware, after a revision to the installation data, all structure parts are now shipped from Avionics Support Group (ASG) with preassembly hardware installed.
- The installation of the cfMount™ on the Boeing 737 was designed so that the Captain and First Officer installations were mirror images of one another. To confirm that both installations were located in the same spot on both windows, a drill template was designed. The drill template fixes onto the existing chart holder mounting holes giving the mechanic the ability to drill both windows exactly the same.
- The top plate of the Standard cfMount™ was modified to receive the quick release system of the Pivot case.
The engineering data was customized to capture all the newly added revisions, and installation was performed. All key requirements were achieved and witnessed by both the project engineer and mechanic performing the installation. Southwest has now started successfully performing modifications of the Boeing 737 cfMount™ installation at their window shop.
In summary
Certified mounts provide assurance from the regulatory authorities that the fixed mount solution implemented will be accepted as a long term solution. Uncertified temporary solutions such as Sleeves and Suction Cups run the risk of non-compliance should the regulatory authorities change their current position. This could significantly set back an operator’s future EFB program at the cost of money and, more importantly, time. There also several mounts and Cradles available that are plastic which could be using non-compliant materials, for example, plastics when burned can cause toxic fumes. All ASG products are made of aircraft-grade aluminum and other materials that are not toxic when burned. All ASG mounts, cradles, power supplies, Ethernet adapters and installation kits get delivered with FAA approved installation data and an Airworthiness Approved Tag (8130-3). Avionics Support Group, Inc. (ASG) will continue to develop new products for the EFB market always providing the operator with the highest quality and safety.
Contributor’s Details
Alex J Rodrigo, VP/FAA DAR-MFG at Avionics Support Group (ASG)
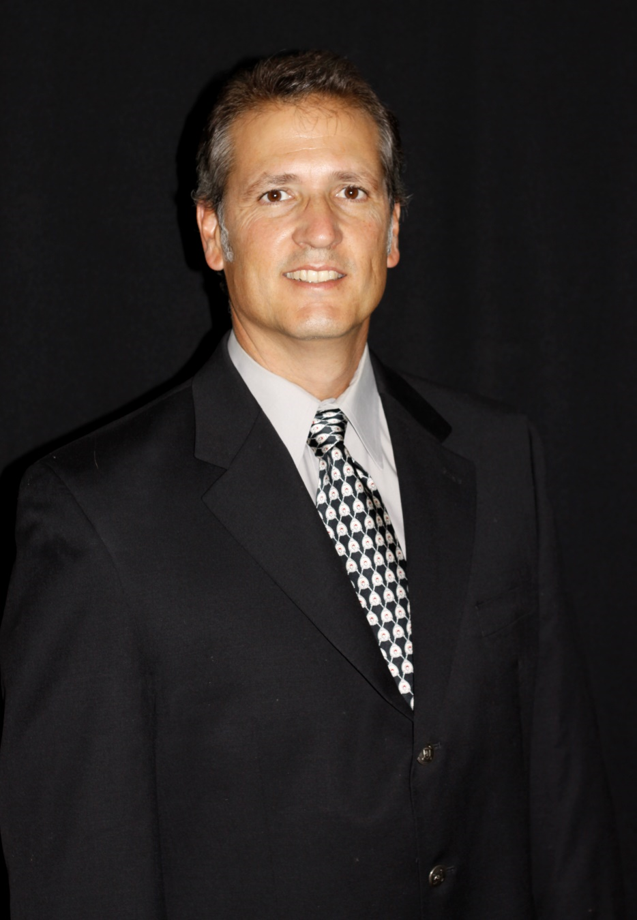
Alex J. Rodrigo is one of the principals and Director of Engineering, and FAA DER for Avionics Support Group, Inc. Alex oversees all aspects of engineering, modifications and associated drawing packages. He also develops all certification data packages and works with the FAA in processing Supplemental Type Certificates. He is a US Navy veteran with a background in Avionics; he later graduated from Florida International University with an Electrical degree.
Comments (0)
There are currently no comments about this article.
To post a comment, please login or subscribe.