Gesine Varfis, Marketing & Early Adopter Program for Maintenance Consulting at APSYS shares some thoughts on digitalization change drivers and change of business models: paperless maintenance, data, augmented analytics and maintenance cost control
The airline industry is in the center of a towering eye wall: data, digital transformation, change of business models and, on top of all that, costing. The pace of digitalization is accelerated by disruptive innovation. Tomorrow’s leaders think out of the box applying different business models as well as customized solutions. Not a leader, happy to follow? Let’s stay with a disruptive picture what it means not to move forward. Digitalization can be compared with confronting a hurricane. Hurricanes can be dangerous because of flooding and because of their destructive powers in moving and destroying objects. The ‘eye of the storm’ is the center. It has little rain or wind, a relatively calm, but moving spot. It is surrounded by the eyewall, a ring of towering thunderstorms where the most severe weather and highest winds occur. Digitalization has moved a long way with maintenance mobility and EFBs becoming standard not the exception anymore. Many airlines have growing operational research centers attached to the Operations Control Center (OCC). Yesterday was driven by business intelligence (BI); tomorrow is driven by predictive and prescriptive; the day after by augmented analytics. Many airlines are in the ‘eye’ of digitalization, they have been driving it. But all are going to face further changes of business models – the eye wall – some of them will be more disruptive than others. Real-time operations costing and economic decisions will be one of the most disruptive changes we are going to face. The objective of this article: to share with readers some ideas to help them prepare for this future.
ABOUT APSYS
Having been in the market for about thirty years, our background is in the fields of safety and security. The business comprises more than 450 people and offers simulation as well as maintenance solutions plus consulting services focused on digitalization. That safety and security capability extends to the design of aircraft and the building of aircraft, taking all data records back to the design stage and ensuring that aircraft produced are safe. More recently, APSYS has moved out of the aerospace area into the broader area of transportation and one of the big drivers in that was to take safety knowledge into other areas to transform them.
Safety is definitely one driver in maintenance and with the new generation of aircraft coming into service that will also extend to cyber-security and data security; Apsys is making sure that the cycle is closed, for fully safe and secure aircraft operations (figure 1). With predictive maintenance on the agenda for airlines the life cycle as well as the capture of data from design to operations gets more and more vital. Apsys believes that the next step after predictive maintenance is to develop prescriptive economics driven business decision support solutions for maintenance. Tomorrow’s operations and maintenance solutions will be real-time data analytics driven and we believe that will require a new generation of maintenance solutions.
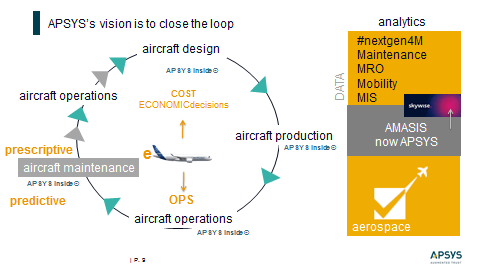
Solutions for (4) M maintenance, MROs, mobility and the maintenance information systems will be data, data processing, data quality and data analytics driven. Our maintenance application is already connected to Skywise and our engagement in maintenance will definitely be driven by data. We currently check out graph relation databases to engage in not only knowing that a part fails but also complementing that information with a recommendation where to replace it in the most economic manner (part availability, least operational impact, at lowest cost…) This is where APSYS’s Lab is working towards innovation and towards artificial intelligence (AI) and we believe in open innovation which means that during our innovation days we invite industry peers to take part, driving data analytics and maintenance.
TECHNICAL PUBLICATIONS AND MAINTENANCE INVOICES
Compared to other industries as well as to airline operations and passenger interaction, Maintenance digitalization lags behind. Complexity, especially in terms of data standardization and an international e-format is a main blocking point. However, with data analytics getting more and more vital and affordable, there is a unique opportunity to define a standard not only applicable for maintenance publication tracking, but that is also able to take predictive and prescriptive maintenance into account. Getting a bit more disruptive, based on one standard and e-format, not only will maintenance track recording get digitalized with all the benefits that will generate, at the same time invoicing with cost driver prediction and economic decisions before the part fails can be taken into account. Real-time costing could be feasible.
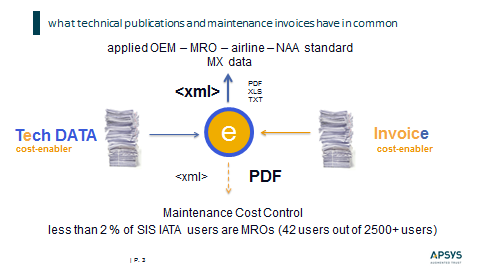
At APSYS, we think the enabler for data analytics is e-standards (figure 2). IATA is engaged in moving the industry to xml e-standard and there are defined IATA chapters that have been applied by OEMs and MROs as well as by airlines and national authorities. IATA also pushed for e-invoicing but, in comparison to overflight charges and fuel, MROs and airlines are hardly applying it. Yet, according to IATA, there are about two percent of MROs and maintenance organizations using paperless invoicing and we think this is something that could be combined into an e-solution. Talking about savings and environment, not having a common e-standard costs millions every year.
Coming back to the storm, as far as digitalization is concerned, we are currently in the eye of the hurricane (figure 3) with, around us, the eye wall and the digital mesh – the network of digitalization, digital trends and what the future holds for digitalization (source: Gartner) such as augmented analytics and augmented reality, which all play into safety and security, cyber security, etc.
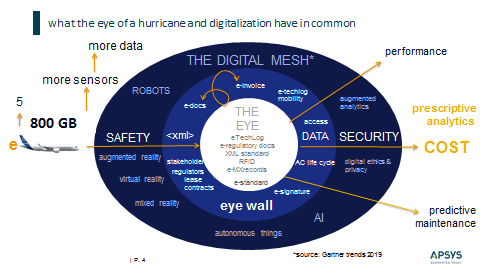
Currently e-standards are determined. One does not have to drive it, nor does one have to implement it. But we are in the middle of the eye. At some point in the future data and standards will be used, if we are not ready for the eyewall in terms of data records digitalization facing the next phase of the storm will be an extremely costly exercise. We also still face e-document problems (e.g. e-signatures). When it comes to aircraft phase in and phase out, if just one party in a chain is not paperless then everything has to go back to paper records. But there will be a time in the future where only paperless aircraft will be accepted (IATA e-ticketing since 2008) getting your documentation and organization ready is vital to survive the next part of the storm.
Getting disruptive again, authorities will have full access to aircraft data. Airworthiness will be automatically checked with indication to the authorities, in case of deviations. Plus, of course, the e-aircraft is operating: readers might not yet be used to the intended extend, but the e-aircraft is already producing lots of data. To our knowledge, an average flight, depending how that is defined, will produce up to 800 gigabytes of data. So, on an average flight, an aircraft like the A350 produces 800 gigabytes of data, albeit that some airlines might only use five gigabytes of that. Data analytics requires design knowledge on algorithms and data, the ones without data will pay a high price to get access to data pools and algorithm intelligence. The ones not having analytics skills incorporated will pay a high price.
e-DATA WHERE ARE WE?
e-invoicing was kicked off pretty early around 2003 (figure 4) 100% e-ticketing was achieved in 2009. For e-invoicing there is an agreed IS-XML file standard format; for e-maintenance and the e-aircraft there are only guidelines. Therefore the target of achieving paperless maintenance in 2020 seems extremely ambitious.
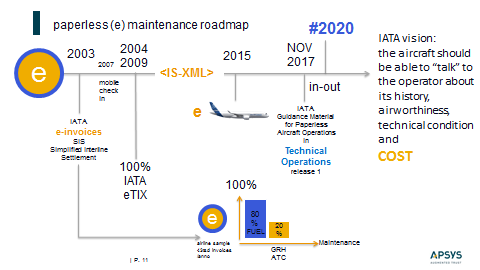
The vision for IATA is not only having paperless maintenance but also to have an aircraft able to ‘talk’ to the operator about what is inside that aircraft in terms of airworthiness, in terms of records, in terms of cost. If we look at fuel, we can say that everybody is more or less ‘e-wise’; fuel efficiency and invoicing are both paperless. However, ground handling and ATC are a different story and then there is maintenance which, as far as digital is concerned, is a blank sheet at the moment and that should not be the case.
Paperless data records are one side of the coin, but authority and manufacturer notifications also need to be taken into the equation. Today SBs (Service Bulletin) are mainly managed manually. The selection of the SB, the identification of the relevant content, the change of the content are all manual procedures including the update of the MIS (Maintenance Information System) and the publishing is again on paper (Figure 5)…
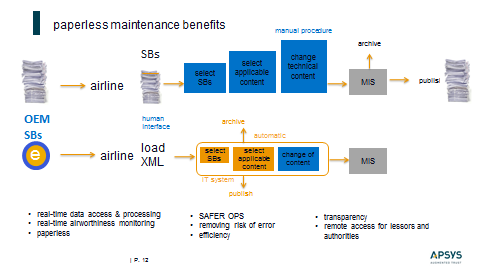
… whereas, applying e-standards to the SB, it is much easier to load the data in one automated stage. Selection is automatic, searches are automatic, and publishing is automatic and paperless. There are solutions available to help with technical publications as well as publication to the MIS, real-time data, access to data, transparency, ensuring that the data is correct.
e-INVOICING – IT CAN BE DONE
What we’ve seen for documentation (above) applies for the e-invoice (figure 6).
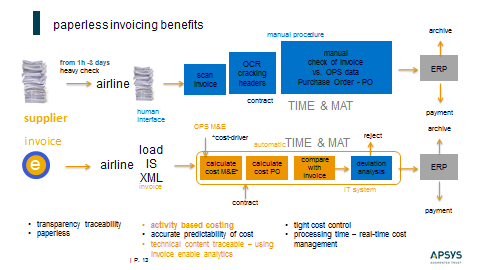
To be disruptive, e-invoicing standards can applied to e-maintenance and, taking it one step further, particular content such as an e-task can be e-performed and e-invoiced. So, why not attach cost to tasks and ATA chapters? SB notes and invoicing have a common paper process. In terms of invoicing the invoice is received and scanned, then the invoice is checked by going through the papers item by item, finding the deviations… we generate 100s of pages per heavy check. However, it’s possible to adopt the e-standard and automatically import the data as well as the cost, based on the items in the invoice. Then it’s possible to calculate the maintenance cost, calculate the purchase orders – the routine stuff – and to do the deviation of routine and non-routine. It’s also possible to complete the deviation analysis and rejection management – there are solutions in the market that will help to support that – ending up in the ERP.
Coming back to the disruptive aspect and its objective: the greatest benefits and values will be achieved when e-standards are not only defined for the technical follow up but for costing at the same time. This means a cost driver based approach: A paperless e-standard for cost, for invoices as well as for publications, bringing it all together is maintenance costing or activity based costing. McKinsey tells us that there will be no traditional cost-cutting programs in the future (figure 7).
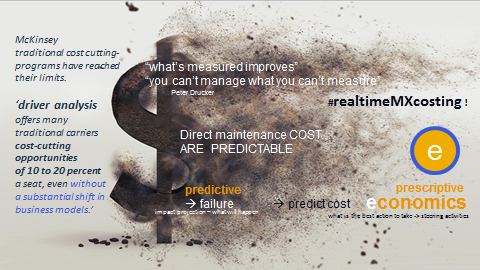
What that means is that traditional cost cutting has been achieved. Tomorrow’s savings will be generated by cost driver analysis. That means we’ll need to know what will be the cost of the engine change, what will be the cost of the removal, what will be the cost of the component as well as the spares, transportation, etc. We will need to know where it is best and cheapest to be performed. Only if we know what drives those costs will we be able to analyze them as well as to measure them and take action. Real-time costing is the prerequisite for ROI (return on investment) related to prescriptive maintenance analytics in the maintenance control center (MCC).
This will change business as usual. The day after tomorrow economic decisions will not be performed in financial control, but in the integrated operations control center (IOCC). An empowered MCC will perform economic decisions… based on predicted failures (predictive maintenance), predicted cost.
Is this philosophy a working solution, how can it be tracked and brought together (figure 8)?
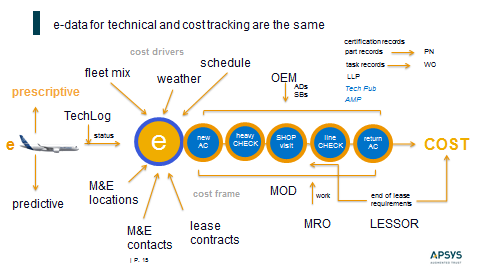
With big data it is feasible. First there is the data from the aircraft. Based on this data and historic data, shared data, we can predict failures, etc. This comes via the TechLog transformed into an e-standard: this transformation is, again, cost and technical content driven. It has to run from receiving the aircraft into the fleet, through health checks, shop visits, line checks and to the return of the aircraft: all cost-driven, all technical publications driven. Again, we strongly believe that what is in the technical part for standards can be easily merged with the costing part.
It’s important to look at the cost drivers (see above) but also at the cost framework; costs are driven, when we are talking about activity costing, via contract content. There is a contract and we know how much time and materials cost will be calculated. Cost and technical tracking is also a relevant feature for aircraft lease and lease return condition management. Today there’s a lot of money lost, often millions of dollars, when returning the aircraft in the wrong condition.
VISIONS FOR THE FUTURE
Let’s start by looking at the vision of IATA and how it might look (figure 9).
Figure 9
First there are cost frame and cost drivers as well as work orders and time as inputs; then, there is the e-tail centric aircraft from which we can go right down to the level of individual components. There will be an e-component and there is a smart tech RFID, which has all the historic data of the aircraft with historic changes and maintenance records on this smart RFID tag. It will also be possible to manage and look at the overhaul caps status which means stating that we cannot exceed this type of cost. This can be done as soon as electronic data is available and, again, it’s the historic data, for maintenance, the actual maintenance status as well as the predictive status, plus deviations and taking costs into account; data analytics driven. We will look at predictive maintenance and economics will be driven by predictive maintenance.
So, how might it look in the future just to look at the vision (figure 9)?
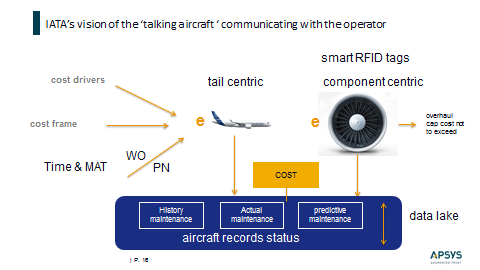
Before shared data lakes were established, the airline and the MRO predicted maintenance cost based on their data available. This is when both faced surprises in terms of calculated cost and predictions. Today the e-aircraft sends its sensor data into data lakes: internal data lakes, group lakes or manufacturer data platforms. In the future both the airline and the MRO will have access to the data. Both will perform again their own analytics in terms of predictive maintenance and costing. This will be a digitalization of the current process. Getting ourselves a bit further out of the box, what if algorithms for predictive maintenance have been agreed and stored in the lake, costing has been contracted so that both technical and cost driver data will be commonly agreed? Eventually, invoice deviation analysis will be a thing of the past, because there will be just one source of OPS data the e-aircraft data, the information of what has been performed plus the costing. Last but not least this is about changing business models and developing a different way of business relations – augmented trust into our business partners. This way ‘trust’ can save millions.
Contracts should be smart contracts integrated in the data lake, to which both parties have access. That means there is automatic calculation of the costing based on the same data, so it will only be necessary, in the future, to talk about deviations, and unexpected work or non-routine work. And, again, it will be a very easy activity-based calculation, time- and material-based. Eventually there will be an app where there will be a deviation analysis for the cost based on the invoice and items within the invoice. The information will all go into the maintenance information system (MIS) and can be changed at a later stage with the ERP. This is predictive maintenance taking into account a new generation of cost analytics.
REAL-TIME COSTING
Still not a real-time costing fan, not convinced that this will be the future? Let’s take an example where real-time costing can really make a difference, where it is taken into the equation. Figure 10 illustrates an easy example.
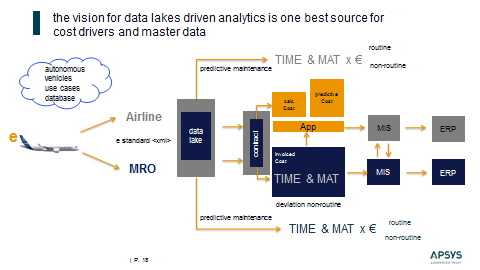
Looking at wear and tear on tires and when we change tires, airlines have performed ‘predictive’ maintenance in Excels before data lake driven big data analytics was on the agenda. We can predict when a tire is due and when to change it. Before taking prediction into account one would wait to change it until a check indicated that it needed to be changed or, worse, when the pilot on his walk around did not accept the aircraft because of the state of the tires. There were AOGs due to tire change, which could be predicted. Today the wear and tear is predicted and the tire is changed before it is due not causing any delay for operations. To perform the right decision, and this is the infancy of prescriptive analytics, is the delay cost. It is important to know when it will happen, what will be the cost involved, what is the best location where the tire can be changed, what is the cheapest location, what is the transportation cost involved… all this was managed in Excel. Now it can be managed in a data analytics solution, taking more aspects and more complexity into account. But, again, this means bringing the maintenance relevant information together with the costing parts to make a decision in the MCC together with the OCC and the IOCC.
PREDICTING THE FUTURE
So, what is the best way to predict the future (figure 12)?
Back to the hurricane picture; we are currently on the verge of moving out of the eye which means we are about to face the digital thunderstorms. We need to innovate; it is not enough simply to say that a good off-the-shelf solution can be adapted; off-the-shelf solutions are a thing of the past. Tomorrow will be driven by start-ups, by innovations, by labs. If one looks at our business environment, many airlines are getting prepared and there are the following functions and positions appearing on corporate organization charts: ‘VP integration and innovation’, ‘VP digital strategy’, ‘VP strategy and innovation’. easyJet now has a CDO or Chief Data Officer whose background is not marketing and airline but is data crunching; and this will also happen to maintenance at some stage.
So, how to address it? The most important part is the data: we need to look at our data, we need to clean our data, we need to clean our records and there have to be skills sets in the environment, in the maintenance, in the OCC and the MCC, capable of doing data processing and analytics to avoid garbage in garbage out. Second is a change of culture: we need to empower people, people need to be able to make decisions and do analytics based on costing. Plus we need a culture of innovation and for ContinuousNEXT – a business strategy suggested by Gartner that urges companies to make change management an integral part of all operations, emphasizing perpetual innovation, integration and delivery. It is considered the next evolutionary phase of digital transformation. Why ContinuousNEXT? We have to ask, when value is created; and it’s not created today. Value is not created when we do post flight analytics and look at the cost of the past. Value is created when we are able to look at tomorrow and the day after tomorrow. So, for all of the time and investment we make, we look more at the past nowadays than we look at the future and this has to change. Also e-standards and cost on an e-level will allow us to look at the future, predict the future and work on the future which is why everybody needs to go ‘e’.
DIFFERENT APPROACHES TO INNOVATION
Looking at innovation, there are different ways to approach it (figure 13).
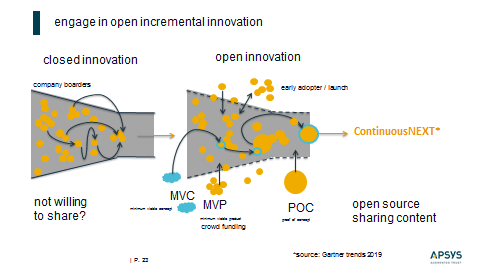
Closed innovation can make a difference, if you have good people. But at Apsys we strongly believe in open innovation, where people from outside helping to move solutions; that becomes open innovation. It’s useful to go outside, to chat about issues, to exchange ideas, to look at multiple viable products and, with that, you might no longer take products off the shelf; you’ll look at a concept, you’ll look to see whether this will fit your solution, you look at minimum viable products and proof of concept. Is there something off-the-shelf with which you can do the job? Minimum viable product is something that is innovatively designed together with the user and their knowledge. We need knowledge of maintenance, we need the knowledge of costing and we need somebody driving change and technology, and digitalization. There are a lot of different features that need to be moved forwards in order to change tomorrow and therefore it is important that everybody joins. So, I’d like to invite you to try open innovation.
Contributor’s Details
Gesine Varfis
Now responsible for Airline and MRO Marketing at APSYS, Gesine worked as CIO and COO advisor for Aeroflot Russian Airlines engaged in the upgrading of Aeroflot’s OPS systems (crew, flight planning, OCC, RMS, HCC, CDM, mobile solutions). Prior to Aeroflot Gesine was engaged as Management Consultant for Lufthansa Consulting with a focus on cost cutting, operational excellence, performance management, Operations Control and Hub Control Center re-engineering, and IT specification, verification and implementation projects.
APSYS
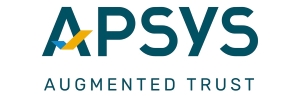
APSYS serves customers worldwide in determining leading risk management standards. Deeply rooted in aerospace engineering, APSYS’s experts are involved throughout the entire lifecycle of an aircraft from design to in-service operations guaranteeing reliable and safe aircraft operations. Driving continuous innovation based on trust, expertise and dedication is the key to success. APSYS.lab is a cornerstone to determine future solutions. APSYS aims to find the right solution based on agile innovation consulting complemented by software solutions with a high level of scientific and technological integration.
To post a comment, please login or subscribe.