Articles
Name | Author | |
---|---|---|
Case Study: Atlas Air – Paperless, that’s the plan | Andy Genao, Senior Manager, Maintenance Planning, and Michael Henry, Director Maintenance Planning, Atlas Air | View article |
Voice Technology Innovations in MRO | Scott Powell, Senior Manager, Product Marketing, Honeywell | View article |
The changing face of data | Sander de Bree, CEO, EXSYN | View article |
Information: how to get what you need | Bijoy Mechery, CEO, and Brent Heath, Senior Vice President, Seabury Solutions | View article |
Column: How I See IT – The Significance of Telepresence | Paul Saunders, Solution Manager, Flatirons Solutions | View article |
Voice Technology Innovations in MRO
Author: Scott Powell, Senior Manager, Product Marketing, Honeywell
SubscribeVoice Technology Innovations in MRO
Voice Technology: it’s the next big aviation M&E / MRO innovation says Scott Powell, Senior Manager, Product Marketing at Honeywell
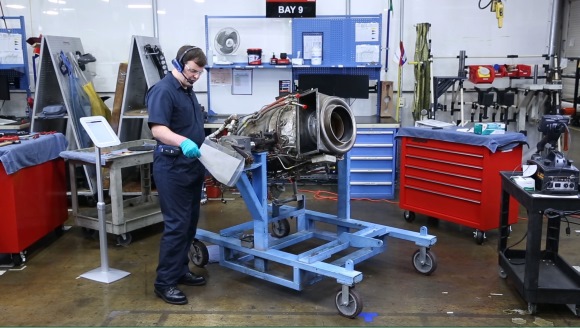
In this article, I’d like to share with readers some of the exciting new technology that is changing the way in which work and processes are conducted in MRO facilities. But to set the context, let me first tell you a little about Honeywell and how Voice based Maintenance and Inspection solutions have emerged as an innovative technology offering.
ABOUT HONEYWELL
Honeywell has a diverse technology offering spanning many markets. Our part of the business is Safety and Productivity Solutions which is responsible for a huge portfolio of products and technologies, including printers, scanners, mobile devices, RFID, and – central to this article – voice technology. The business has a history of innovation through applications of technology outside of traditional markets and verticals. Voice Maintenance and Inspection is an example of this: Vocollect™ voice, traditionally a highly effective distribution center solution, has become an innovative and powerful new technology solution within aerospace facilities to drive process compliance, scale best practices and eliminate wasted time to complete inaccurate data entry
MRO operations at Honeywell Aerospace can be found at more than 40 locations around the world dealing with everything from avionics and APUs to wheels and brakes maintenance. The majority of these are Honeywell products on which we perform maintenance as a service. The process used to maintain and inspect these products is the same as found in most other MRO businesses:
Receive a product → induct it → undertake engine disposition → teardown and wash → analyze the task → undertake staging and assembly → test it then get the final ‘out’ → ship it.
Different companies might use different terminology for these stages depending on the type of product but the steps are easily recognizable across MRO facilities.
PAPERWORK
The challenge with an MRO process today is paperwork. Current documentation methods are heavily paper-based with clipboards, checklists, note-making and, later on, require even more time to transfer that paperwork into the MRO system. Honeywell Aerospace uses SAP to retain its MRO records. On average it will take a mechanic with, for example, an APU induction, four to five hours to complete this process. An hour or more is spent transferring that paperwork into the IT system. There is a significant amount of redundancy as well as painstaking paperwork involved in this process.
EVALUATING TECHNOLOGY OPTIONS
With this in mind, Honeywell Aerospace began to evaluate multiple technology options with a view to improving the process and going paperless. Rather than just eliminating the paper in this process, Honeywell sought to optimize and standardize the current workflows across the 40-plus locations so that the quality of service would be consistent; regardless of whether the technicians had 30 years’ or a few years’ experience. In addition, we didn’t just want a digital version of a paper process. Rather we wanted to reduce the time taken to perform the maintenance workflow tasks, and to explore whether these tasks could be managed by electronic data collection means while still providing a safe working environment for our mechanics. We evaluated a variety of technology options, from head-mounted displays, tablets and smartphones to RFID and, finally, voice recognition technology.
The challenge when using handhelds and smartphones, while useful for certain workflows, is that they are the wrong form factor for a ‘hands busy, eyes busy’ environment. MRO technicians typically wear gloves, work with hand tools, deal with greasy environments, climb onto and under objects, etc., so giving them another handheld device on which they have to stop what they are doing and key in information does not make their job any easier, faster or more accurate. Head-mounted displays are a better fit; they’re wearable and therefore hands free, but when we evaluated them, we found the technology not sufficiently mature to be deployed in an industrial environment due to issues such as low battery life and heat dissipation.
We began to evaluate voice recognition technology as an option. Within Honeywell’s own business we found the solution: Vocollect voice, a voice recognition solution that previously had focused on a quite different market – Vocollect voice is the market-leading solution in use in distribution centers / warehouses for most of the world’s food and beverage distributors. Voice is a hands-free, eyes-free solution that provides work instructions in real time to operators, allowing them to respond directly to the system using voice. This then gets converted into text and sent back to whatever host system is being used.
For the MRO technician, this voice solution allows a step-by-step process guide, real-time data capture and offers a dynamic list of steps to perform, based on a specific product type. All without the need for a clipboard.
VOCOLLECT VOICE TECHNOLOGY FOR MRO
The technology behind this is not new; in fact the Vocollect voice business has been in the supply chain environment for more than twenty-five years, and is used in warehouses and distribution centers by more than a million workers in 60 countries, using 35 languages today. It’s a mature technology, and critically for Honeywell’s customers, voice technology has had a measurable impact on results in the warehouses where it is used, with a roughly 35% productivity improvement and a 20-25% reduction in errors to deliver significant bottom line improvements. Our challenge, and the question we asked of ourselves, was ‘how could we apply voice technology to an MRO operation?’
This short video demonstrates how using Vocollect voice can significantly improve the induction of an APU at the Honeywell Phoenix Sky Harbor MRO facility, where a voice solution has been live since June 2014.
A BETTER WAY OF WORKING
Applying hands free, eyes free voice to MRO is not just about cutting down paperwork and moving to electronic format; it’s a different way of handling documentation. The biggest benefit gained from using voice in MRO is a standard of process compliance across all the locations and technicians using it. With step-by-step guidance, every technician follows the same process without missing a single step. The second benefit is the reduction in documentation time: as technicians move through tasks, the data is captured in real time so that redundant documentation work is now no longer necessary. A third benefit, and a significant one that was not originally anticipated, is the amount of visibility this solution provides: every step and response is time-stamped so that management can see how much time each process step takes, see where the bottlenecks in the MRO process are, and quickly address any slowdowns in any part of the workflow. This also means it is easier to address any issues through additional training and/or process changes.
The results of applying this solution at Honeywell Aerospace are striking: the quality and consistency of service has gone up, overtime costs have been reduced and we now have information from which to continually improve our overall processes and workflows. We have seen a 30 percent reduction in data entry cycle time, a significant improvement in accuracy rates, which resulted in a large saving on the cost of missing parts, and technician training time has been greatly reduced. In detail, the solution has yielded a 39% average time savings across six different engine and part types, has eliminated skipped process steps and ended our dependency on typing / data entry. These were the immediately tangible results, and Honeywell is looking forward to replicating these results across all of our 40 Honeywell Aerospace locations.
HOW THE VOICE M&I SOLUTION WORKS
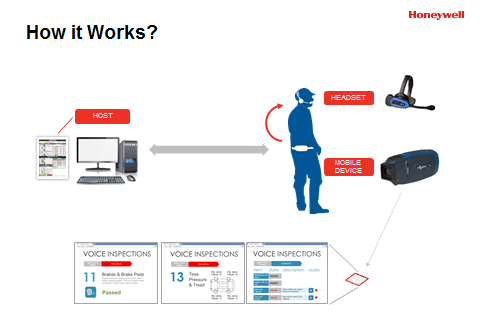
Figure 1
The voice solution works by connecting to the host system (see figure 1), from which the information is converted into a Voice Plan and fed into the A700 mobile device worn by the technician along with an SRX2 Bluetooth Wireless Headset. The mobile device converts the steps into voice instructions, captures the responses from the mechanic, and sends that back into the host system which continues to be the system of record. When there’s a need to see visual information, the system can connect to any screen – a tablet or an existing PC or workstation – to pull out PDF manuals, schematics and images.
IMPLEMENTING VOICE TECHNOLOGY
As a result of this highly successful implementation, we took the decision to expand the solution to multiple locations. By December 2015, ten Honeywell MRO facilities had the voice technology solution deployed for everything from receiving, to induction, to final ‘out’ across Avionics, Wheels and Brakes; indeed, any checklist-based maintenance application. We’ve learned that voice is a clear fit for certain step-by-step processes, but in addition we are investigating other processes such as the analytical or the manufacturing side as these also consist of a lot of back and forth with the E&M system.
The technicians’ verdict
One of the most common questions is how the technicians respond to the solution: do they like it? Do they find their processes easier or more difficult to follow? How do they find the technology? After all, it has completely changed their work processes, replacing the paperwork or smartphones with which they have become familiar. Initially, many technicians were hesitant to adopt it. However, they found the paper-based processes very time-consuming and inefficient, and once they began to use the new technology, they quickly realized that it had significant advantages – and made their working day much easier.
Lessons learned
As the implementations progressed through more Honeywell sites, we gathered data and feedback to drive the solution’s success, including much about the critical change management process. We examined the technicians’ inputs and feedback early on, and gathered the high-performing technicians to advise us on which was the most optimized workflow. With this process the technicians were the ones leading and championing the implementation. Once the decision was made to go live at a site, we conducted classroom and on the shop floor training to ensure that the technicians were comfortable with the technology, and we kept people onsite after go-live to answer questions. After gathering that continuous feedback, we were able to complete time studies about before and after the implementation. These gave tangible, measurable results for Honeywell senior management — including the CEO of Honeywell International — showing the striking effects we’d seen from deploying this technology. The response from senior management was that, based on those results, we should roll it out across the Honeywell MRO organization.
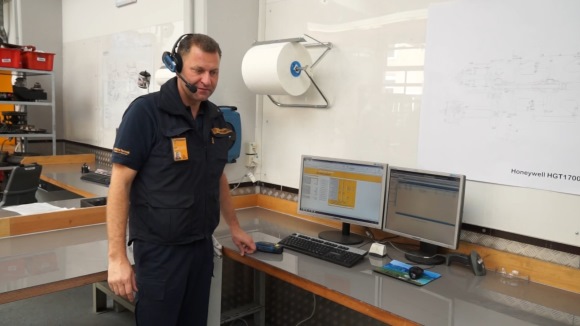
Since then we have successfully implemented Voice M&I technology to numerous MROs including Lufthansa Technik in Germany and the US Government’s Hill Air Force Base. There is a very clear benefit from being able to move directly from paper to voice as the driver of multiple input media (photos, scanning, looking at the display) in the MRO process. The key is to know when voice is the best fit for a particular workflow.
TAKE-AWAYS
Honeywell has learned some important points to remember when considering new applications for a technology. In implementing voice for MRO, we have found that identifying the right technology for the right process is key – tablets and smartphones are a great fit for certain workflows, voice is well suited to some workflows, and different wearable technology is best in others. For voice to be the right fit, a workflow has to have a repeatable structure, the data has to be structured and it has to be a ‘hands busy’ environment – if the workflow does not include these characteristics, then a different device might be a better fit. The change management process is also critical to success and critical to the technicians’ adoption of a new technology and reengineered workflow. Lastly, having clearly defined success criteria allows you to measure success for senior management, and develop a tangible return on investment.
AN AWARD-WINNING SOLUTION
The Voice M&I Solution has proved so successful within the MRO community that it recently won the 2016 Commercial Technologies for Maintenance Activities (CTMA) Technology Competition, which was sponsored by the National Center for Manufacturing Sciences and the Office of the Deputy Assistant Secretary of Defense for Maintenance. The competition was designed to introduce new technologies to the U.S. Department of Defense in an effort to sustain material readiness at reduced costs.
Scott Powell
Scott Powell is a Sr. Manager for Honeywell’s market leading Vocollect voice solutions. Since joining Honeywell in 2012, at the time of Honeywell’s acquisition of
Vocollect, Scott focused on driving different Honeywell Vocollect and software solutions. He is Pragmatic Marketing certified, holds a Masters of Business Administration degree from Villanova University, and a bachelor’s degree in industrial technology from the University of Wisconsin.
Honeywell Aerospace
Honeywell, a diversified technology and manufacturing leader, serving customers worldwide with aerospace products and services, has been a pioneer in aerospace innovation. Thousands of Honeywell Aerospace products and services are found on virtually every commercial, defense and space aircraft worldwide. The Aerospace business unit develops and integrates technologies that span air traffic modernization, flight and runway safety, engines, cockpit and cabin electronics, connectivity, logistics and more that deliver safe, efficient, productive and comfortable transportation-related experiences.
Honeywell Safety & Productivity Solutions
Honeywell Safety & Productivity Solutions provides comprehensive solutions that enhance workplace safety and incident response, improve enterprise and workflow performance, and enable greater product design innovation. Customers rely on Honeywell’s connected solutions to provide real-time safety intelligence to respond to safety threats, increase worker productivity and enrich operational intelligence with data-driven insights that enable smarter business decisions. The company serves customers in aerospace, automotive, commercial building, first responder, field service, healthcare, logistics, manufacturing, oil & gas, power and utilities, medical, retail, supply chain, test & measurement and transportation markets.
Comments (0)
There are currently no comments about this article.
To post a comment, please login or subscribe.