Articles
Name | Author | |
---|---|---|
HOW TECHNOLOGY WORKS: Taking a digital solution to MROs | Israel Revivo, CEO and President, IDMR Solutions Inc | View article |
WHAT IT CAN DO: The secret of a successful MRO IT System upgrade project | James Cornelius, President of ROTA Technology | View article |
CASE STUDY: Maintenance planning at FedEx Express: Today and the future | Roger L. Hutchinson II, Manager TechOps Strategic Mx. Planning, FedEx Express and Elliot Margul, CEO Aerostrat | View article |
CASE STUDY: Chrono Aviation and WAAS benefit with a modern IT solution | Dominic Cayouette, Project Manager, Chrono Aviation and Peter Mortimer, Executive VP Canada, Rusada | View article |
WHITE PAPER: Embracing digital transformation | Adnan Mansur, Head of Digital and Innovation Services, Asia Digital Engineering | View article |
WHITE PAPER: Embracing digital transformation
Author: Adnan Mansur, Head of Digital and Innovation Services, Asia Digital Engineering
Subscribe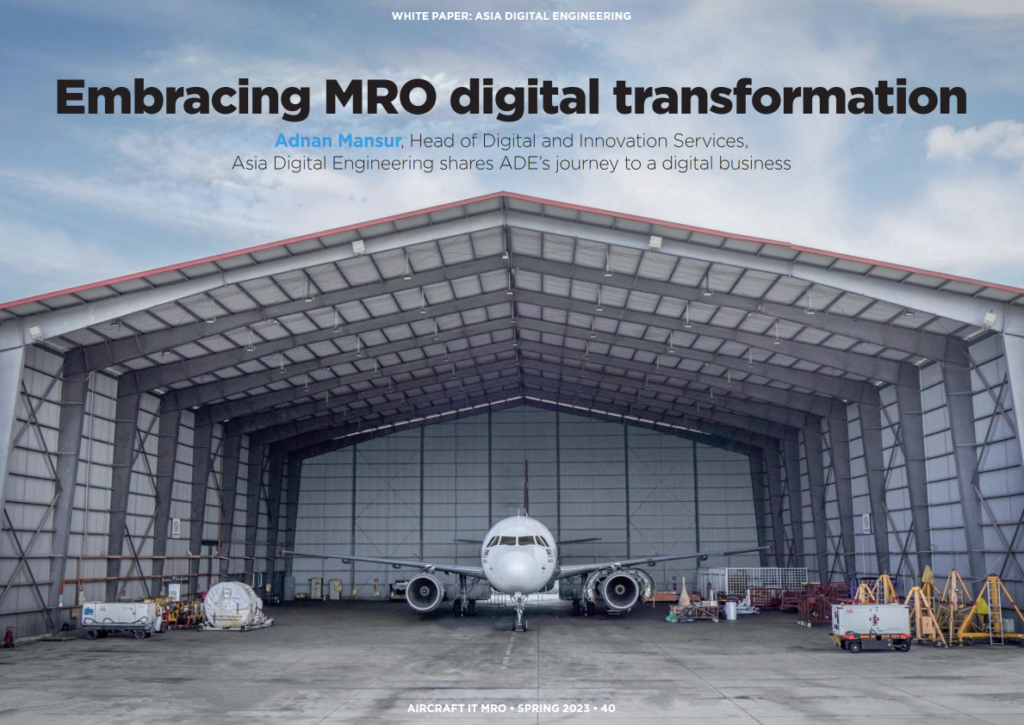
Adnan Mansur, Head of Digital and Innovation Services, Asia Digital Engineering shares ADE’s journey to a digital business
At Asia Digital Engineering (ADE), we have recently undertaken a journey to digital transformation and it is that journey that I’ll be sharing with readers in this article. What is meant by the term digital transformation and why has an MRO business called itself Asia Digital Engineering with no direct reference to aviation or MRO/M&E in the name? And, what is meant by digital transformation? My responsibilities, Digital and Innovation Services, include two core functions which are Software as a Service (SaaS) and Digital as a Service (DaaS). We have found that, while there are plenty of digital solutions on the market, the majority of them do not match the very complex operations in an MRO environment.
DIGITAL TRANSFORMATION
Salesforce defines digital transformation as, “… the process of using digital technologies to create new or modify existing business processes and customer experiences to meet challenging business and market requirements.”
ADE’s had three main reasons for making the transformation (figure 1)
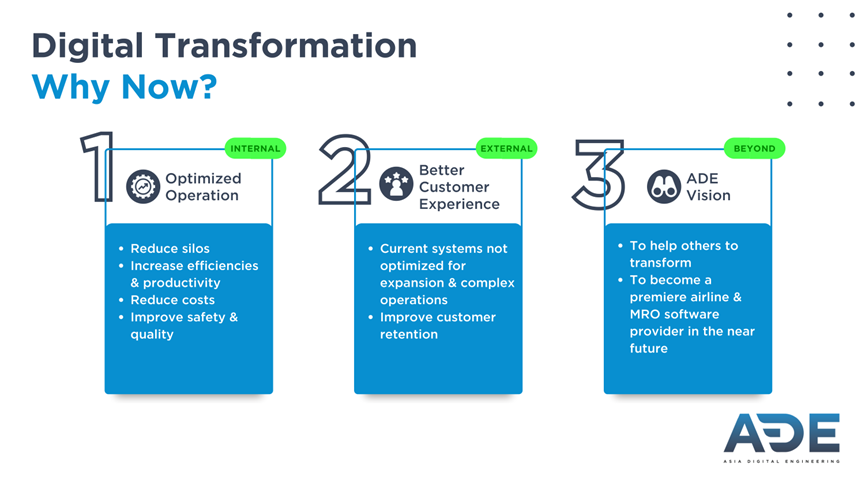
Figure 1
The first reason was to achieve an optimized operation. To reduce or remove silos has become a major objective in many aviation businesses today with the goal to increase efficiencies and productivity as well as use technology to reduce costs. Overall, the plan is to improve safety and enhance quality. These are, of course, internal objectives for ADE, the MRO, and they are why it was decided that digital transformation was the way forward. That said, there is another major reason for digital transformation and that is, how could we use technology to provide a better customer experience?
Now that ADE is no longer part of an airline, as you’ll see later, our market is not limited to what were previously internal customers. We now also work for third-party customers. With that, we have to have a way to manage customers including, how do we use technology to ensure that they return with further business? When this project started, our current systems were not optimized for either expansion or for complex operations to improve customer retention. This is a new mindset for ADE, and we need to educate ourselves to keep in mind that a happy customer makes for a happy business. Technology and data will be harnessed for that purpose.
The third reason is to be able to use what we have and double up reasons one and two to help others to optimize their operations and to help them to better serve their own customers in the future, including providing our own software solutions.
There are some guiding principles for digital transformation which we stand by in ADE. There are a lot of technologies available such as blockchain and artificial intelligence but our principle is that we don’t simply implement technology for the sake of technology, there has to be an appropriate and relevant use-case, otherwise the technology will become a white elephant. We innovate to simplify and solve problems with a practical application of technology: not just because we can.
INTRODUCTION TO ADE
Asia Digital Engineering is an offshoot MRO company and a wholly-owned subsidiary of Capital A Berhad (figure 2).
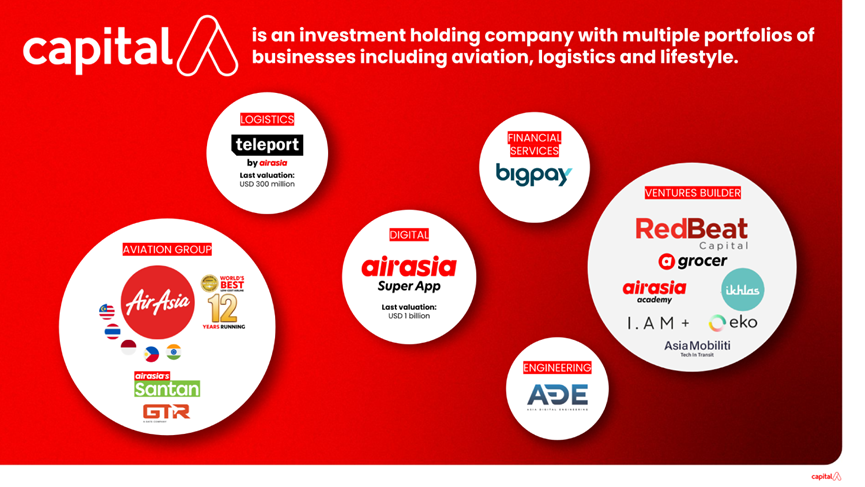
Figure 2
Most of ADE was previously the engineering department in AirAsia, Malaysia. In September 2020, that engineering department was taken out of the AirAsia airline and was constituted as a new entity called Asia Digital Engineering (ADE) as the engineering arm for the group. It was all done in the middle of the pandemic but that probably accelerated our decision to make the change. ADE is based in Kuala Lumpur, from where we offer the full range of maintenance services, primarily in Malaysia today with multiple presence (figure 3).
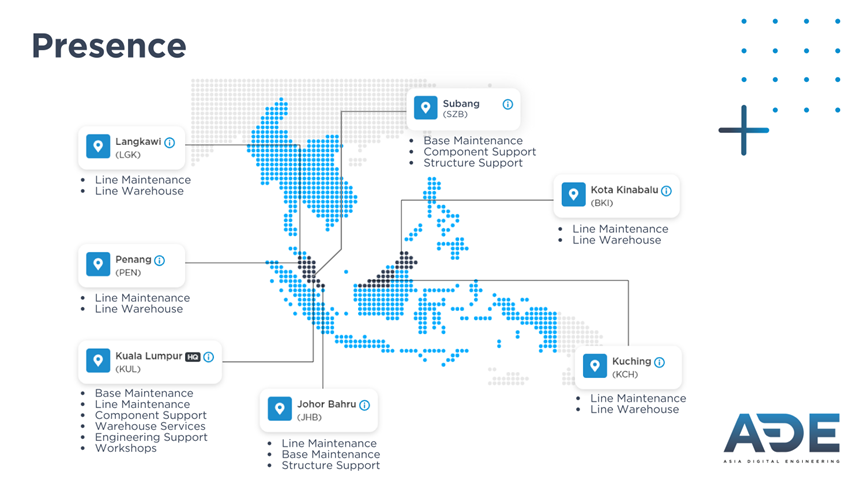
Figure 3
In the future, ADE will be expanding operations to neighboring countries including Thailand, Indonesia and Philippines – all places where we already have engineering capacity.
MRO SERVICES AND DIGITAL SOLUTIONS FROM ADE
We’re always trying to be different from existing MRO businesses, hence the slightly different name. Notwithstanding that, ADE still has the core functionalities and still relies on the maintenance business as a Part 145 MRO (figure 4).
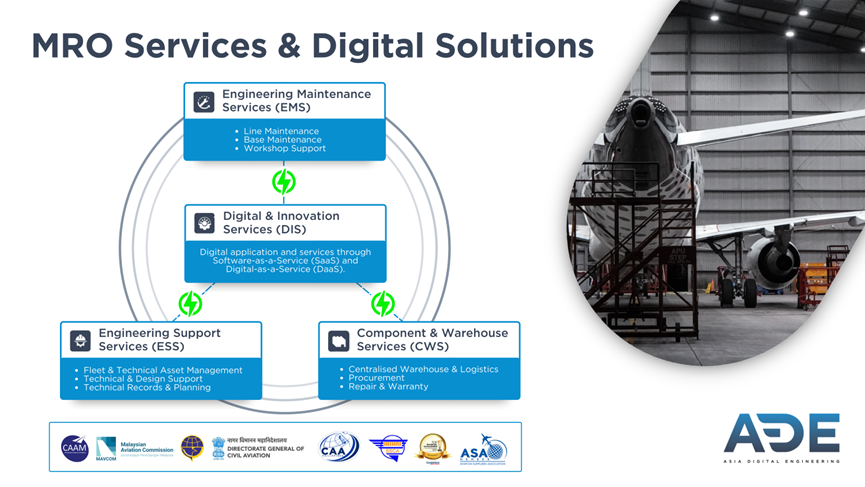
Figure 4
We offer Base maintenance, Line Maintenance and Workshop support and will be adding further capabilities. ADE also offers services on CAMO functions and on asset management, redeliveries and the like. We also have a component warehouse that manages all the assets. So, in the case of any AOGs (Aircraft on Ground), as an MRO, we provide an almost end-to-end solution with digital to glue everything together, to keep our customers flying. We are working towards digitizing MRO operations to optimize resources and deliver efficiency.
Before we look at what ADE has done in the past few months, it will be useful to see the context of what we have been through as an airline engineering department and now as an MRO.
ADE IN THE PAST
The processes in figure 5 will be quite familiar to readers: they are the common processes that MROs deal with every day as part of being an MRO or an airline engineering and maintenance operation.
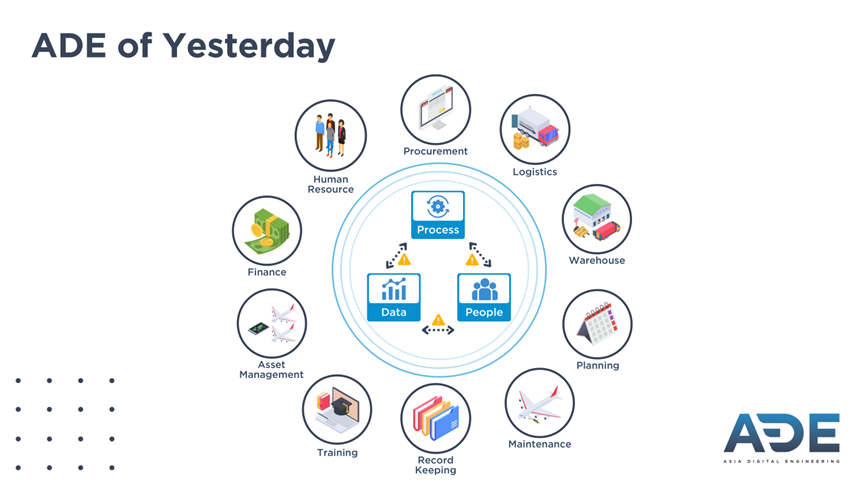
Figure 5
Often, these processes are not connected to each other because, perhaps, of the system that’s being used or, maybe, the data that is available doesn’t allow co-sharing or linking. These are the sort of legacy issues that we had before and that was one of the drivers that we used to re-invent our business. You can see, at the center, ‘Process, Data and People’ which are three key factors in making sure that your processes or your business are working efficiently and close together.
Let’s break down some of those factors in terms of issues that we had before, which will help readers to understand why they drove us to change.
Some of the challenges that we had with data included:
- Data incompleteness because the engineering department in AirAsia still had a lot of paperwork that needed to be managed so, if the data are not all in the system, or even for those that are in the system but don’t flow in real time, that makes decision making quite difficult and, if you want to make any decision, you often find that you’re being reactive rather than proactive.
- As I mentioned, there was a lot of data on paper just flying around in an unstructured form. Today, we all have Cloud storage systems but it means nothing if your data is on paper. So. we’re trying to change that.
- Finally, of course, with data being unstructured and not available in real time, the speed of decision making is also really impacted.
With processes, the challenges included:
- That we relied too much on manual processes. Even though the ERP system was there, sometimes, because of the complexity of the process, the users tended to find their own ways to get the job done, even inventing their own processes. That might also affect data collection on the systems side.
- Also, because of those manual processes, that might hinder collaboration with miscommunication raising communication barriers as part of manual processes.
Last in this list but by no means the least important, people experienced the greatest challenges including:
- Because of those issues that we had before, there was low motivation for people who had to come to work every day and had to deal with the earlier issues; plus, with that low motivation, productivity was also adversely affected.
- Equally, when people are not provided with the correct tools to collaborate, again, the quality and speed of decision making can be impacted.
- Then, with a lack of technical expertise in-house, too many jobs had to be outsourced or dependent on off-the-shelf solutions. So, at ADE, we aim to not be so reliant on off-the-shelf solutions.
ADE OF TODAY AND TOMORROW
What are we going to do in the next five to 10 years? Most important is to change the culture but how can that be achieved? Using technology and data will make that change possible (figure 6).
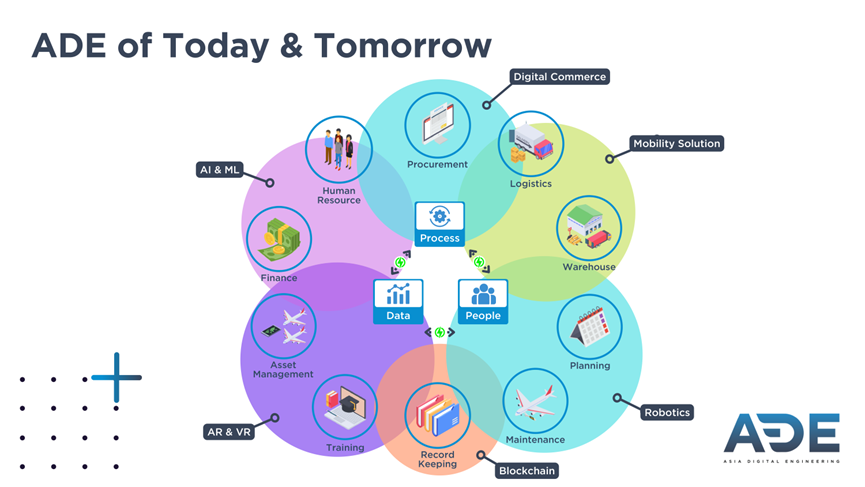
Figure 6
Our plan in the next five to 10 years is to create one connected process rather than siloed separate processes as in figure 5. Technology is the enabler; it’s not the priority, it’s more the glue to keep all of these processes together and to glue process, data and people together. The technologies are shown on the outsides of the areas to emphasize that technology is not the priority and never has been for ADE: it’s more about how to enable the people, the data and the process to work closely together.
Data strategy
Our data strategy follows some lines that will be familiar to readers. First, to improve data completeness. Data completeness is key to being able to make decisions based on full data. Our industry has safety at its heart so having the full data is really important to ensure the best-informed approach and the best safety. We are also aiming to make ADE into a fully paperless operation by either using commercial off-the-shelf solutions or to completely develop in-house. Only by going fully paperless, can we complete our data collection processes. Also, as alluded to above, we aim to improve quality and safety. By having good clean data we’ll be able to ultimately improve quality and safety because, otherwise, there’s always an element of guesswork when the data is all over the place. Again, readers will be able to relate to this issue because the aviation industry can sometimes be quite slow in the adoption of technology and, at ADE, we’ve also been there.
Another part of what we plan to achieve with ADE’s data strategy is to increase operational performance. Once there is good data combined with good technology, the operational performance will improve and, from all of these new processes will come better decision making.
Processes
Once the right tools and improved data are in place it will be possible to minimize redundancies that are often introduced by manual processes and silos. Using technology, can provide more visibility through all departments and processes to avoid having to repeat what others have already done. Redundancies might also affect health and safety, another good reason for good data and good processes as well as reduced redundancies. When improving health and safety in terms of the manpower, there are a lot of use cases in the sector about using robotics and this could eventually help ADE’s workforce to better take care of themselves: for example, avoid lifting heavy weights where that might be better done by robots. That is a use case that would really benefit. Our mantra is not using technology to change but using technology to really help our people. In safety as well, using data and technology can provide alerts such as for an impending lightning strike. If there is technology that can predict that in advance the maintenance team can find shelter before that strike. In most cases, the impending lightning is realized a little too late and it is imperative for us, in the technology sector to reduce these incidents. Minimized redundancies and having good data as well as improving the speed of the data is once result from improved processes.
People
Once we have good processes and good data, people are better motivated which is good because, these days, we need to find ways to retain talent: with the industry booming again, the talent pool is becoming smaller while demand is growing. We need to use data to measure how we can make our people happier. You can measure workload and fatigue using data so that people have the ability to work with us longer and in greater safety. And, of course, we also need to use data and technology to grow people, not just to be in the same roles or processes for the next ten years. We want them to know what they can do efficiently compared to others and, of course, we also want them to be using data. We also want to reward them for their achievements and, in the future, when we have IoT and other technologies we will want to reward our people more fairly.
SUCCESS STORIES
Here are a few success stories that we have already achieved and to show how we are practicing what we preach with some use cases that we can share with readers: there’s more in the pipeline but this is what has already happened.
AEROTRADE™
This one grew from experience and the pain points experienced managing our procurement activities. In early 2021, ADE stared developing its own marketplace: initially just for ourselves to better manage our inventory. However, later we realized, based on the feedback from our partners and customers, that this could be useful for the wider industry (figure 7), so, we have started to invite partners from airlines and MROs, distributors, OEMs and the like, to be part of AEROTRADE™
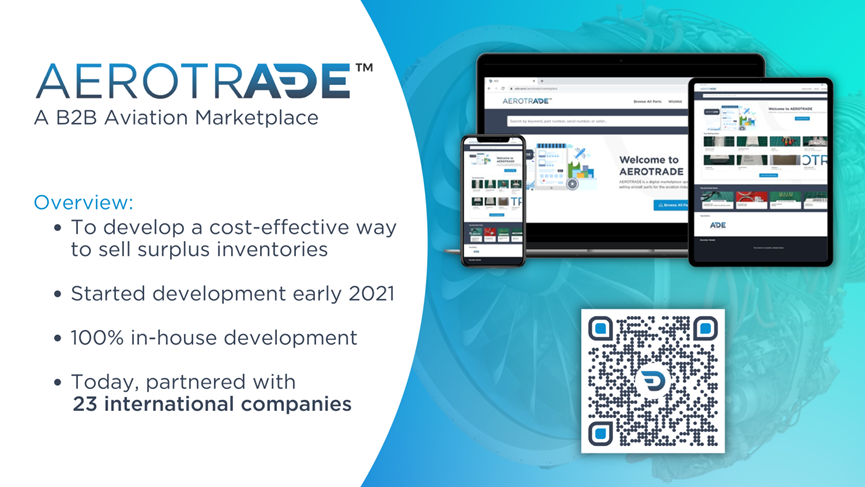
Figure 7
As an in-house parts and materials marketplace, we used our experience from working as part of an airline to develop what we think is a better way to do it and we invite everyone to join and be part of this evolution. At the time of this writing, there are more than 23 international companies who have joined to be part of the AEROTRADE™ ecosystem as well as to better manage their inventories.
CASCADE™
The second use case I would like to share with readers is our in-house developed productivity application, CASCADE™ (figure 8).
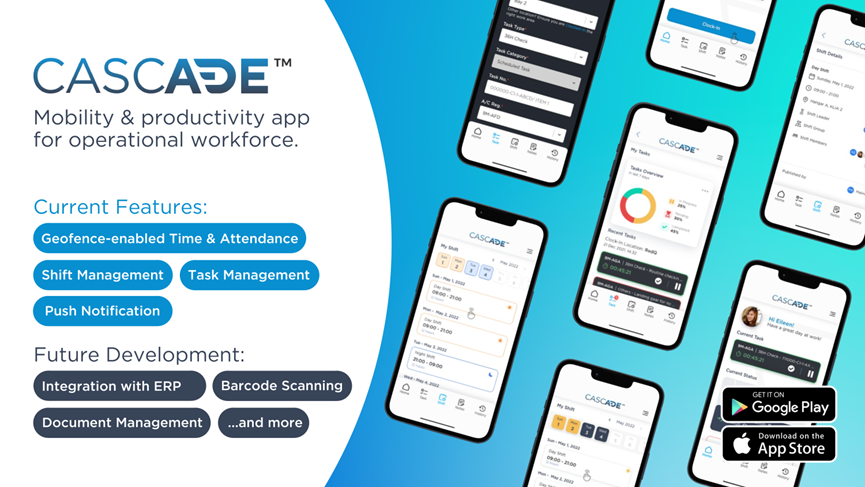
Figure 8
The pain points that inspired this application were managing our people because, as you saw in the map, figure 3, our maintenance people are all over Malaysia at all the major airports, plus, in MRO, the people are the highest cost to manage. Having a Bird’s Eye view of the people and their productivity is very important, so we developed for ourselves a mobile application that people can take on their own device, with which they will be familiar, wherever they are, and start tracking their tasks in order to start measuring everybody’s productivity and reward. This ties back to the previous reference to how we plan to reward people using technology.
You can see now why we have included the ‘Digital’ in ‘Asia Digital Engineering’; it’s because we see ourselves to be not just an MRO and maintenance provider; we also see ourselves to be one of the software providers for the aviation MRO industry.
E-Learning
A final use case that I’d like to share with you, is in terms of training. Because of limitations on movement during Covid, there were a lot of classes that needed to be done using virtual means such as Zoom and Teams which led us to realize that that presented an opportunity for us to further cut costs by building our own recurrent training platform internally which has been approved by our own executive and is now running completely virtually in ADE (figure 9).
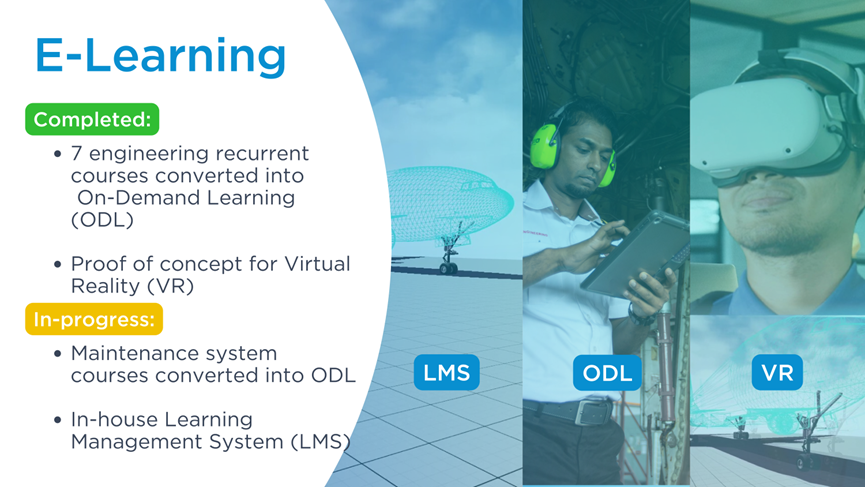
Figure 9
Seven engineering recurrent courses have been re-developed as On-Demand Learning (ODL) programs and we’ve also managed to develop a proof of concept for VR (Virtual reality) training. We think there is a lot of potential for VR, again because of Covid and because, in this very large industry, a lot of people who need to train might not always have access to an aircraft: hence our belief that VR has a bright future in aviation. In MRO, while the majority come from a maintenance background and will have access to aircraft every day, with the business growing so much, there will be people in the company who might not have such ready access to aircraft, people such as software engineers, administrators and more. This VR-based e-Learning will offer them an opportunity to become familiar with the aircraft’s technology and be able to contribute to the work and see themselves as part of the aviation industry.
We are also doing a lot more process developments; this is more for internal systems at the moment but there will be more to come. That’s a brief introduction to ADE’s digital transformation program which, I hope, will inspire some readers to embark on their own program and others to join us as partners on our journey.
Ends…
Contributor’s Details
Adnan Mansur
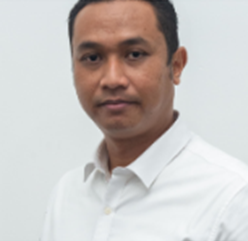
Adnan earned his Bachelor’s in Systems Engineering from the University of Arizona and was involved in managing the aircraft and component diagnostic and analytics as a Warranty & Reliability Manager in AirAsia before being appointed as Digital Project Manager in AirAsia Digital, where today he pioneers the digital transformation in Asia Digital Engineering (ADE) as the Head of the Digital & Innovation Service by adopting new technologies to solve problems in the MRO industry.
Asia Digital Engineering (ADE)
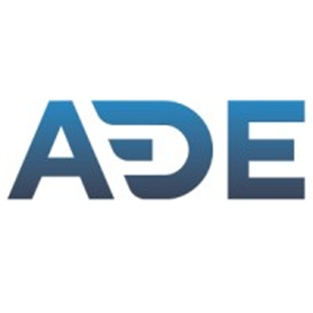
Leveraging the AirAsia’s Engineering Department’s best practices and experience, ADE offers a wide range of aircraft services focused on the Airbus A320, A321 & A330 for engineering maintenance services, component and warehouse services, and engineering support services, as well digital and innovation services. ADE aims to uphold the highest standards in when it comes to professional integrity, quality, reliability, driving greater efficiencies and safety, for all of our customers at all times
Comments (0)
There are currently no comments about this article.
To post a comment, please login or subscribe.