Articles
Name | Author | |
---|---|---|
A better view of process in a paperless environment | Neal Reagor, Director Planning and Commercial Services - EAMS | View article |
Column: How I See IT – COVID-19: Impacts and progress | Allan Bachan, VP, Managing Director, MRO Operations, ICF | View article |
Looking into the future at Etihad Airways | Borja Dosal Roiz, Avionics Engineer / CAMO Fleet Management at Etihad Airways | View article |
IATA’s Digital Aircraft Operations Initiative | Iryna Khomenko, Manager, Operational Efficiency, IATA SFO, IATA | View article |
Case Study: MRO IT System Modernization at ATSG. | Paul Harding, Director, Information Technology, Air Transport Services Group | View article |
A better view of process in a paperless environment
Author: Neal Reagor, Director Planning and Commercial Services - EAMS
Subscribe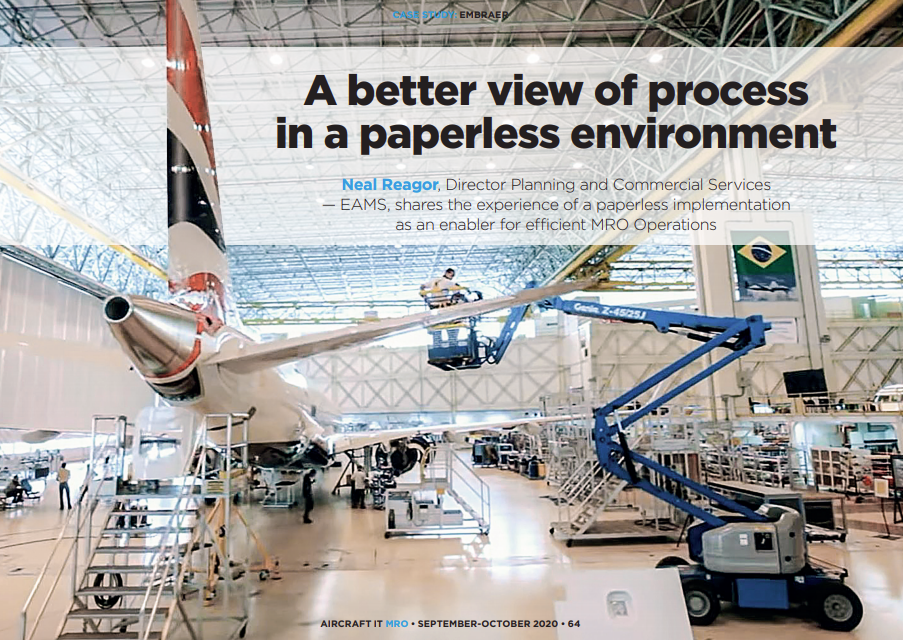
Neal Reagor, Director Planning and Commercial Services – EAMS, shares the experience of a paperless implementation as an enabler for efficient MRO Operations.
Before starting the article proper, I’d like to share a brief history of EAMS (Embraer Aircraft Maintenance Services), prior to looking at what has been changed in terms of paperless and digital developments; then, as importantly, how things are now different and, finally, what EAMS has gained as a result of these changes.
ABOUT EAMS
A wholly owned subsidiary of Embraer since 2002, EAMS was the first Embraer MRO for commercial aircraft in the United States. In 2006, EAMS opened Hangar 2, which was built to support the E-Jets (E170 – E195), and in 2012 opened Hangar 3 to replace the paint area with a dedicated space. In 2013, a temporary hangar was opened, Hangar 4, to provide additional hangar and shop spaces. Today, EAMS provides Aircraft and Component maintenance as well as factory authorized training on the E-Jet from 11 aircraft maintenance bays and with over 400 maintenance technicians.
Where we were
In the period 2014 to 2016, prior to the exercise that is the subject of this article, EAMS was struggling to establish on time delivery performance. The goal was to see 90 percent of jobs delivered on time but the reality was that delivery performance varied between 20 percent on-time deliveries up to more than 90 percent on time (figure 1).
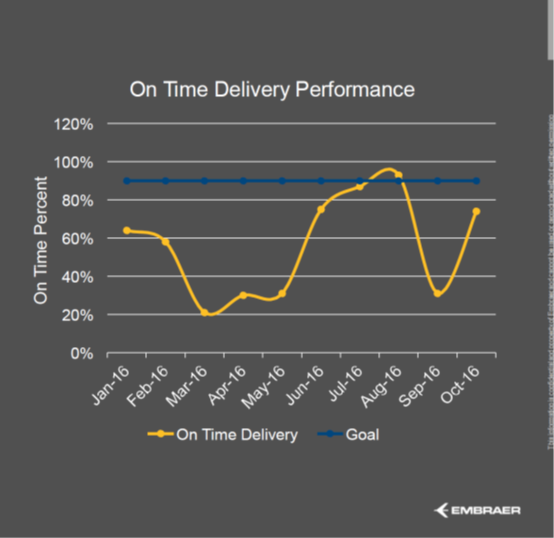
Figure 1
Part of the problem was the volumes of paper involved with, for instance, more than 3,000 pieces of paper generated during a single Heavy Check. Furthermore, this plethora of paper offered no real time visibility of aircraft workflow and meant a lack of data from which to be able to make informed decisions. Everything, stamps, signatures, dates… it was all handwritten on paper.
Also, because workflow was neither straightforward nor visible (figure 2), when paperwork moved to the various locations where it was needed, it was often lost which, even when temporary, meant delays.

Figure 2
There were very large volumes of paperwork in the hangars: each bay would have a board of nearly 500 panels that would have to be opened and closed during the check. Also, they were listed alpha numerically as opposed to by location.
There was much that was not available from that paper-based system and, specifically, there was no real-time data being generated. Hence, there was no live status of aircraft progress; no real time task completion data; no standardized aircraft flow; and the Aircraft Checks’ status was manually populated. It was clear to us that this situation had to change; the question was how and with whom?
CHOOSING A SOLUTION
During Phase I of its value optimization project, EAMS was able to leverage its connection to one of the leading aircraft manufacturers to perform a comprehensive Kaizen A3 exercise analysis of its production processes, information flows, sets of problems and constraints.
Identifying non-value adding activities received special attention. The entire staff was involved in the process from the beginning so all team members would have a clear understanding of the future goals and the contributions expected from each one of them to reach the objectives. Part of the results of this exercise was a detailed list of required improvements.
Multiple key processes were optimized, including re-engineering task card distribution and implementing revised service flows. This type of approach effectively prevented EAMS from looking for software, for the sake of token innovation. Instead, it set the business on the pursuit of a platform and infrastructure, driving the necessary change in its behavior and way of doing business. EAMS needed a proven toolkit that would integrate with the new change management processes.
After evaluating a series of vendors and solutions, EAMS decided EmpowerMX offered the best fit to its goal of becoming an excellency center in commercial aviation MRO and enabling its technical staff to effect change and sustain it. Its selection formed part of the drive, not just to attain better visibility of emerging risks and constraints, but also to open a smooth path to paperless.
Phase II of the project saw EmpowerMX’s MRO Manager© being implemented at EAMS in seamless integration with other solutions already in place as part of the company’s IT portfolio. The two companies worked together to configure the software to meet most of the business requirements defined as part of Phase I, and additional development and customization covered the remainder while keeping in consideration proven and emerging MRO world best-practices.
The software was implemented in waves, gradually increasing the number of bays until the entire facility utilized the new, improved processes and streamlined procedures controlled by real-time data.
WHAT HAS BEEN CHANGED AND HOW IT HAS CHANGED
Starting in 2014, EAMS embarked on a program of process improvement and preparation for the changes that were planned. In 2015 the new paperless and digital solution from EmpowerMX was implemented and the work processes were automated. With the new solution now in place and working, EAMS can look to the future and towards standardized and optimized processes. The whole program was named P3E and stood on four key pillars: People; Culture; Leadership; and Business Efficiency.
Understanding the legacy process
The first step of the project was to analyze and understand the processes within the business and then to identify the issues that would need to be tackled in preparation for implementation of the new solution. A strategy had to be defined and we had to complete our Kaizen objectives. Kaizen is a Japanese business philosophy for continuous improvement of working practices, personal efficiency, etc. It is a commitment that involves all employees from the CEO to the assembly line workers and is applied to all processes. By improving standardized programs and processes, Kaizen aims to eliminate waste. The next stage was, of course, to implement the new solution and then to work to optimize the new process.
The first job was to understand what happened to paperwork within the old processes and to map those processes (figure 3).
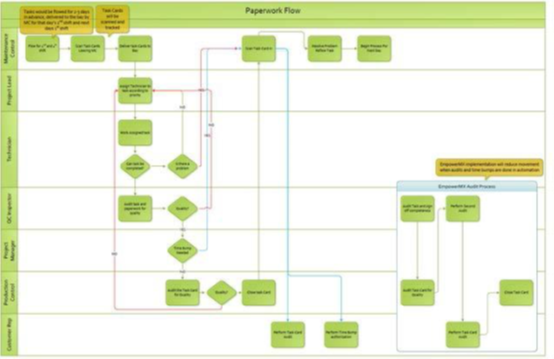
Figure 3
In order to do this effectively, we involved the whole team in the project to ensure that everyone had a stake in the changes; we also encouraged ideas from the team based on the principle that ‘there is no such thing as a bad idea’.
The value of a paperless and digital process
We then considered how the move to a digital and paperless process might benefit the business (figure 4), especially non-routines.
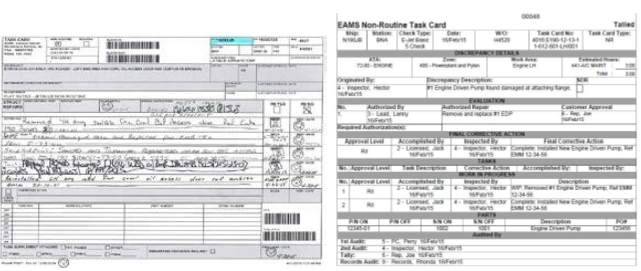
Figure 4
The first clear benefit was the legibility of a digitally produced document as against one on which many different people with different handwriting standards and different pens had made entries; plus the fact that, in a workshop environment, paper picks up dirt which a digital image will not do. Also, date and time stamp entries can be built in to the digitalized process so that they never get missed or incorrectly entered. Perhaps an obvious benefit is that there will be less paperwork on the floor but also the use of electronic signatures will both speed up the processes and ensure that each step in the process is correctly signed off in for the process to continue. Last, but not least, digital notes ensure that nothing is missed and that all notes are always available to technicians in the right place at the touch of a button.
Task Cards
In the legacy system, the flow of task cards around the work environment was complex as seen in figure 2. Moving to a new paperless and digital process reduced the process from 12 steps to just six steps (figure 5)
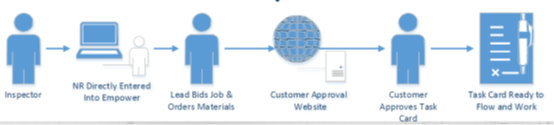
Figure 5
This change offered much better control of task cards in the process. Task card movement has become visible and online customer approvals are possible which can save a lot of time when unexpected issues arise. Because the process is so visible, it’s possible to have increased accountability and, without the need to handle large quantities of paper but with the capability to access documents almost instantly, the time into work has also been improved.
Pre-shift work assignments
With the new paperless digital system, it is easier to arrange work for technicians before their shift commences and to group jobs into executable packages so that technicians can better focus on the job in hand without distractions from all the paper documents that used to be around. It is also easier to flow work out from the project manager to the crew and on to the individual technicians who will be undertaking the work.
Real-time data and maintenance flow
As we’ve already said, the big change is that EAMS is now able to see in real time the progress of each task underway not only for that task itself but also relative to other work in the shop which makes planning and managing processes much easier because planners and managers are better informed about what is happening on the shop floor and informed in real time. The current status of each aircraft in the shop, how far it has moved along in the process; what if any unplanned jobs and non-routines have been revealed and what remains to be done, all that is now available at any time. Also, the major and minor check milestones are all available on the system along with all relevant factual data about the work. Any critical factors that will require customer involvement can be viewed by the customer from the system and, taking a higher level view, planned versus actual labor trends are now plotted to add further value to planning capability.
DATA TO MAKE INFORMED DECISIONS
Decisions are crucial to making progress in a process and (whether they’re right or wrong) in the outcome of that process. Suhail Doshi, CEO of Mixpanel has said, “Most of the world will make decisions by either guessing or using their gut. They will be either lucky or wrong.” That is a very good reason for decisions to be based on as much information as possible. The real-time nature of EAMS’s new solution means that plenty of high quality and relevant decision support information is available when it’s needed.
It’s now easy for managers to check task card and labor/hour progress on any job, and to identify overdue milestones and tasks. Quality indicators are also easily available including reopened, rejected and voided task cards. Non-routine evaluation status can be quickly accessed and, importantly, so can real-time budget process – keeping control of the financial aspect of any work is vital for both EAMS and for its customers. Finally, it’s now possible to compare the planned versus actual labor used in the production process.
Furthermore, because the new solution is digital, reporting is automated (figure 6).
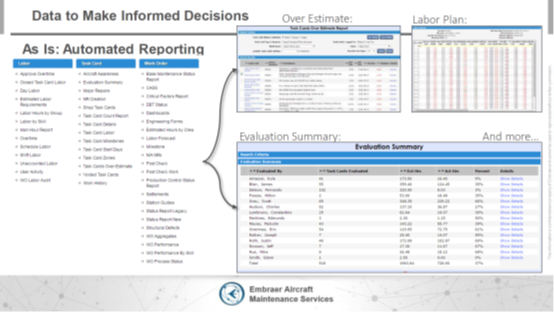
Figure 6
It also makes possible ‘Task card life cycle analyses’ (figure 7) that generates data to improve the execution of task cards and identify bottlenecks. With that information, informed changes can be made to increase mechanics’ hands-on time and decrease overall Check turn time, one task at a time.
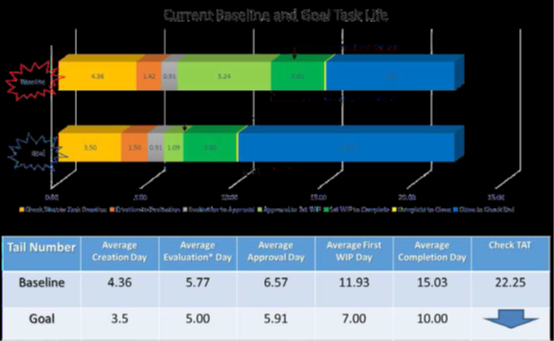
Figure 7
Instant reporting is now available to all departments based on needs. Plus there are other examples of data trends from the new solution. We can spot rework trends and, perhaps, identify any similarities in the cases to minimize reworks. Not only that but we can also spot work stoppages and, again, ask why that has happened plus we are now able to identify incorrectly classified findings. We can capture audit and tally data and all the data now available helps support better shop resource utilization.
THE RESULTS OF THE CHANGE
Since moving to the new paperless digital system, we have found at EAMS that many of our processes and other aspects of the business have improved. Increases in technician efficiency (figure 8) that have been achieved (see above) have also enabled increases in quality (figure 9) and in employee safety (figure 10).
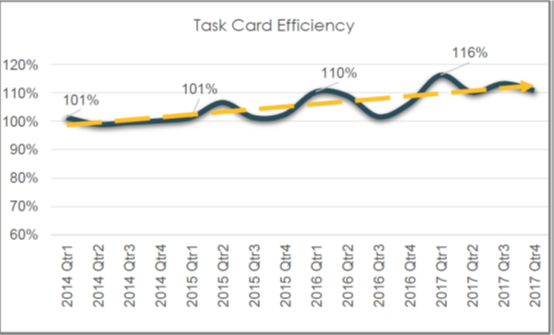
Figure 8
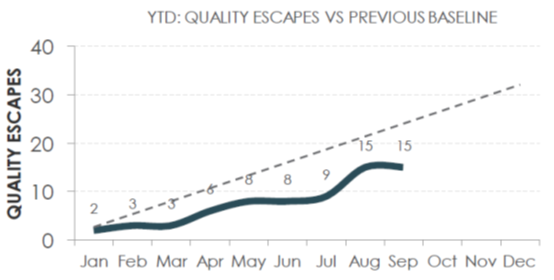
Figure 10
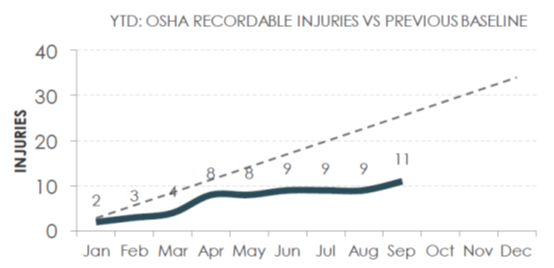
Figure 10
On time deliveries
If you remember, at the beginning of this article, we saw that EAMS was struggling to establish on time delivery performance. The goal was to see 90 percent of jobs delivered on time but the reality was that delivery performance varied between 20 percent on-time deliveries up to more than 90 percent on time (figure 1). I’m very pleased to be able to report that EAMS’s on time delivery performance has stabilized now and at a higher level that our previous but rarely achieved objective with on time deliveries running at around 100 percent for most of the time (figure 11).
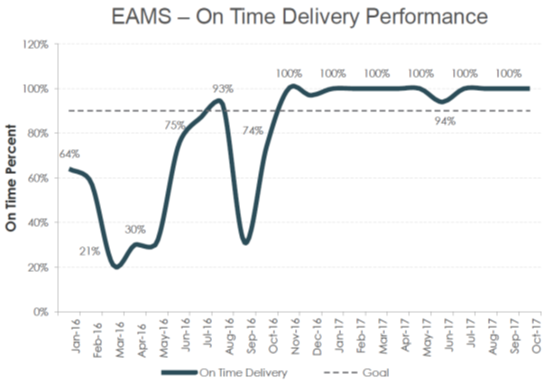
Figure 11
SUMMARY FROM GOING PAPERLESS
Increases in data volumes, organization and availability have greatly enhanced our ability to make quick and accurate business decisions based on factual real-time data. No more guesses or acting on hunches, decisions can be linked to real world events and trends. Also, a better and more defined process means that what happens within the system is properly defined and so requiring few work-arounds or none at all. Finally, we have achieved increased accountability throughout the process with the defined processes highlighting new and previously unknown bottlenecks that were delaying the work but without us really knowing why.
Ends…
Contributor’s Details
EAMS
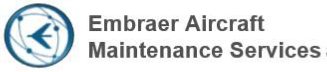
EAMS is the world’s center of excellence for Embraer ERJs and E-Jets heavy maintenance and component repair. EAMS has performed more than 1,400 heavy inspections since 2008. The facility offers 11 hangar bays with more than 500 highly skilled technicians and has more than 2,800 components part numbers on their repair capabilities. EAMS is a Certified Repair Station under a number of regulatory authorities.
EmpowerMX
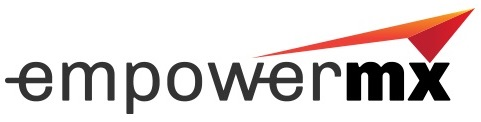
EmpowerMX is a world leader in providing cloud-based intelligent maintenance support for today’s aircraft, with a focus on delivering software solutions supporting the planning, execution and tracking of maintenance in the commercial aviation environment. Since inception, EmpowerMX has evolved into a global operation providing software, services and support to air carriers, MRO’s, OEMs and startup operators. The suite is fully modular so it can be deployed as part of complex IT portfolios to leverage on pre-existing investments, or deployed to cover all the business needs of operators and independent MRO organizations.
Comments (0)
There are currently no comments about this article.
To post a comment, please login or subscribe.