Articles
Name | Author | |
---|---|---|
Column: How I see IT | Allan Bachan, VP, Managing Director, MRO Operations, ICF | Kyle Tuberson, Chief Technology Officer, Public Sector, ICF | View article |
What IT can do | Henrik Ollus, Customer Success Manager, QOCO Systems | View article |
A new MRO IT solution for AISG’s multiple locations | Alejandro Bravo, Sr. VP Production Control & COO, AISG | View article |
Planning for a digital future | James Angus, Commercial Director of the Integrated Vehicle Health Management (IVHM) Centre at Cranfield University and John Maggiore is a senior aerospace leader, executive consultant, and digital transformation expert at Cranfield University IVHM Centre. | View article |
HAECO embarks on an MRO IT upgrade | Teresa Cheung, Assistant General Manager, Centre of Excellence & Cathay Operations, Line Maintenance and Christine Yung, Leader of the AMOS Competence Excellence team, HAECO Hong Kong | View article |
ATR steps-up to a modern MRO IT solution | Patrick Massicot, Head of Airframe & MRO Services, ATR | View article |
A new MRO IT solution for AISG’s multiple locations
Author: Alejandro Bravo, Sr. VP Production Control & COO, AISG
SubscribeAlejandro Bravo, Sr. VP Production Control & COO, AISG shares a complex MRO IT solution upgrade for a geographically dispersed line maintenance business and what helped it to succeed.
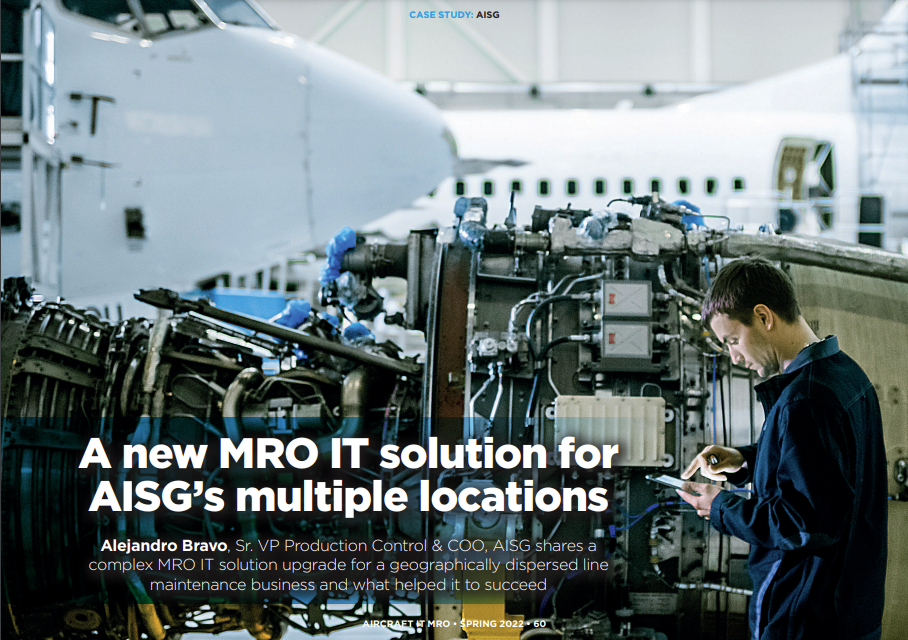
AISG
AISG is a line maintenance services provider and MRO for most of the major airlines in the world. The business started in Cancún in Mexico and there are now 32 stations around Mexico. We service airliners from wide-body to narrow body aircraft across all OEMs and types. The main business is to provide a service for airlines in Mexico but we are now spreading that service to Europe and the Dominican Republic. How the company started was because airlines don’t want to have a technician in every station where their aircraft land to cover only one flight a day. As a result, AISG started offering solutions with one or more technicians on a station who could be trained to be able to serve the aircraft operated by a number of airlines throughout the week or the month which would save them costs as against having their own staff in all of those different locations.
FINDING A NEW SOFTWARE SOLUTION
The need for a new software solution came about because AISG didn’t have a web-based solution; so, we started to look for options among the many available in the sector. We met some of the developers and vendors before coming to the conclusion that Ultramain was the company that offered a better solution for our purposes and, importantly, were willing to help us in the implementation process for the changes.
One of the main goals when we set out on this journey was to have the software or the algorithm with which we could assign flights to technicians. That way, AISG could have a resource planning solution for the future. Ultramain were able to create that with the resource planners to produce a solution that would enable us to know how many technicians we would need during a certain period of time, where they would be needed, for which airline and which aircraft type; that would help us to plan our work better. It was a great solution and represented the biggest challenge faced by Ultramain in meeting AISG’s needs because there are many variables in the requirement. Only Ultramain were willing to undertake this and that was how the project started.
THE ULTRAMAIN SOLUTION CHOSEN
There are more than thirty different applications in the ULTRAMAIN® suite. At the highest level, ULTRAMAIN is a full asset management and logistics system built specifically around aviation. The system has attracted some very large customers such as AISG and Ultramain also shares some customers with AISG. But, specifically in the case of AISG and the line maintenance solution, the problem was something that Ultramain had never really encountered before on the scale that AISG operates. AISG has more than seventy different airline customers, each of which requires different policies and procedures training, plus they have a country certificate and a type rating certificate, the technicians have multiple certificates.
One of the challenges around AISG’s line maintenance service is ‘do we have the right person with the right qualifications at the right time to meet the aircraft?’ There are also associated issues of, who needs more training; how do we make sure that the person there has the right qualifications and that they are not expired; and how do we ensure that the right person is in the city to which the aircraft is going? Added to that are the usual variables around inbound flights, are they on time, and are they on schedule, plus the fleet type that is coming in? That’s what the solution that Ultramain put together had to do. The line maintenance solution for MROs with the optimization to bring all that data together and then present AISG with an option to plan up to sixty days ahead. At the time of writing, we were already planning a month ahead with the new solution.
A key requirement that AISG wanted to have in the system included a modification up to the next level of capability which was already in the ULTRAMAIN system – optimization, crew schedules, certifications. We wanted the ability to create the work schedules automatically, based around when AISG’s customers’ aircraft were coming in. So, the Ultramain system now takes a forecast of the flights that are coming in to the cities served by AISG and looks at the resource requirements to build an optimized work schedule that conforms to the Labor laws in Mexico which vary from city to city with differing regulations about when people can travel to and from work. All of that gets put into the system which then delivers highly optimized schedules to ensure that the technicians needed are not in training, they’re not on a day off or on their holidays or any other leave.
That’s the issue with getting resources to the aircraft. Mobile Mechanic™ (figure 1) is then used to deliver the assignments out to the individuals; they can look, by station, to see what they are assigned to and the work that has been allocated to them.
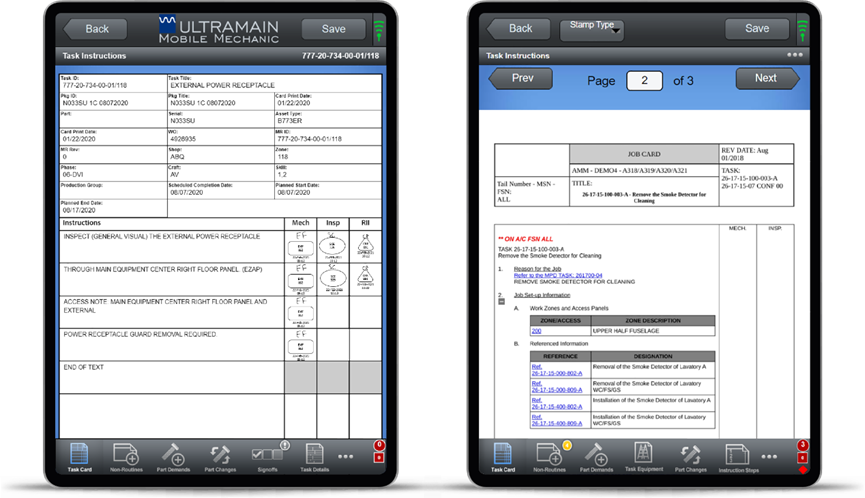
There is also Mobile Inventory™, the ability to scan parts in and out without necessarily needing a traditional barcode reader but using Blue Tooth fobs associate with technicians’ mobile phones which helps to keep the cost of infrastructure down.
HOW THE SOLUTION WORKED FOR AISG
The mobile App has proved to be the most helpful because it frees technicians from the need to go back to the office, sit at a computer and key in all the relevant information about a job. Having it all in a mobile device makes the process really simple with a real-time solution. AISG uses the Mobile Mechanic to register all activities in real time and uses Mobile Inventory to register consumables used. So, if an aircraft is on the ground and the technician decides that it needs oil, he can deliver it from the can but can deduct it from the Mobile Inventory so that, if the inventory is getting low on stock, it can be seen by someone in the office who can order more. That is a very good solution for AISG.
Another module from the software that AISG uses, Labor Optimization (figs 2-4), is also helpful in forecasting future needs, taking into consideration the schedules, the technicians, the aircraft types, the airlines, restrictions from the authorities and the union and permissions from the authorities about each specific aircraft.
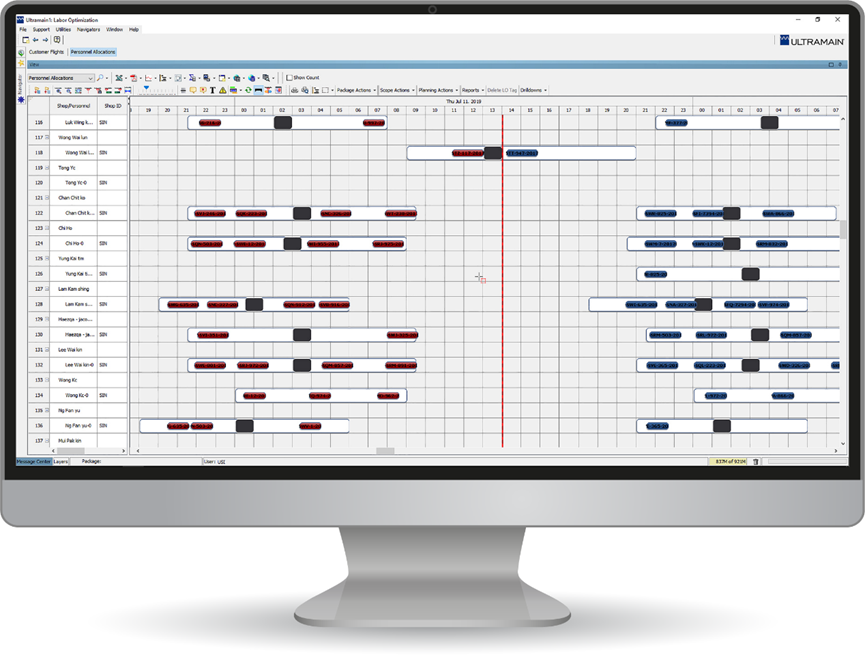
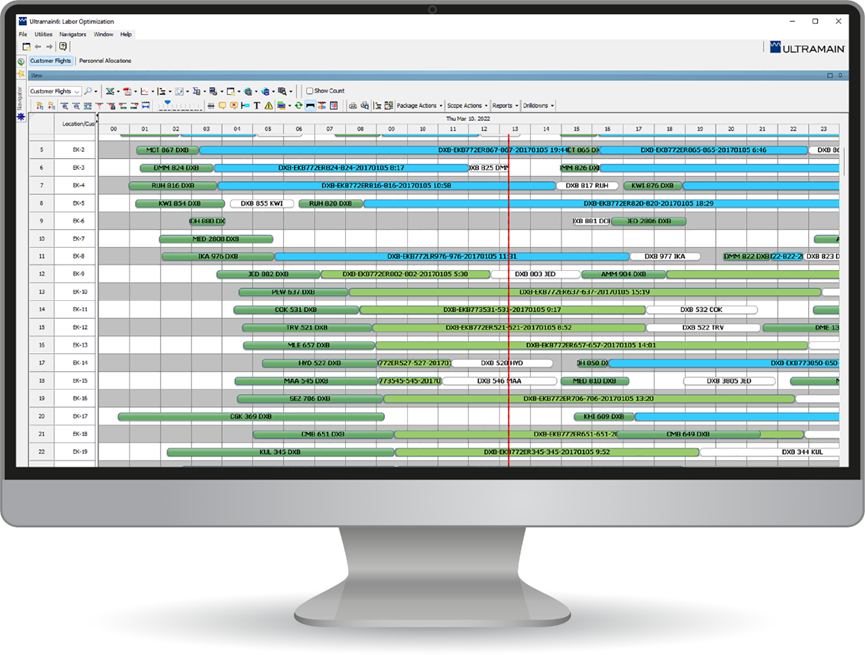
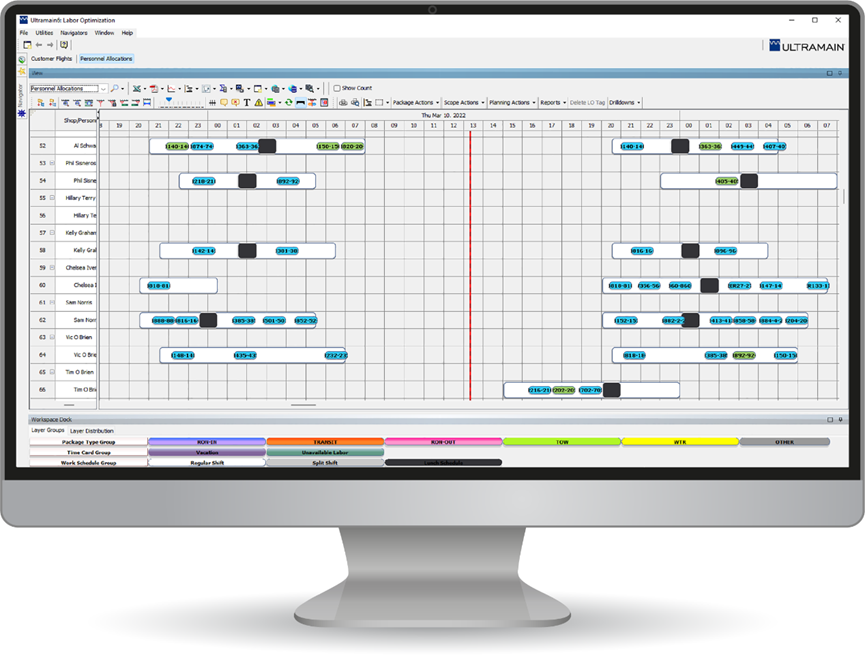
AISG uses Mobile Inventory to make sure that the technician has everything they need to service each flight, it’s also used for audits and, at the time of writing, AISG was starting to use it for managing vehicles. ULTRAMAIN also allows users to track all ground support equipment with full asset management capabilities and AISG is starting to include those in the system.
SELECTION AND IMPLEMENTATION
At AISG, we considered the options available to us in the market as well as recommendations such as from Cathay Pacific Airways and we saw the system working because Cathay is an AISG customer as well as using the ULTRAMAIN solution. We did look at other software but seeing the solution in use with an airline who was also an AISG customer helped a lot with the initial approach from Ultramain which supported the decision to go with them. We were also impressed at their willingness to hep AISG to create a solution for our business model and that was another driver to choose ULTRAMAIN.
On the implementation, we were fortunate to get a recommendation to someone who had worked on a similar implementation with a previous airline. That helped AISG to achieve a better understanding from a consultant who had already used the software. So, that person was brought on to the team and we started the implementation which has taken, from the start, six months at the time of writing and with some further implementation still to do as well as bedding in some of the software to work better for AISG’s specific needs. The implementation was not too smooth at the beginning, given the many variables to be considered as well as there being so many airline customers and scenarios; also, Ultramain had to first learn AISG’s business and then start to program for that. That was the most challenging time and took longer but after that, it started to run smoothly; introducing the solution, starting testing and seeing the system working in about six months. It had been a larger challenge than Ultramain had anticipated, particularly with the full extent of the numbers of variables in the operation and the complexities of getting literally thousands of permutations based on all the data that AISG had. In the second phase, Ultramain assigned a number of its own specialist staff to support the implementation. By working together, we were able to power through.
COVID did come at this time and the impact, as for the whole sector, was mainly on resources because AISG was not able to continue with the planned schedule; we had planned to get more modules in use but resources were compromised. There was not that much available activity to work with to create more scenarios and carry out more tests which meant that those kinds of project were not able to be completed in the time planned.
OTHER CHALLENGES
Because there was not that much activity, the problems faced by the project were reduced and AISG was able to see the different scenarios and solve them because there was sufficient time available; that said, there were actually not that many problems to solve. But we were able to prepare for the next step which is what was underway at the time of writing.
TRAINING
The first approach to training was to train the trainers; that way the Ultramain team could provide the information to key AISG staff. Bearing in mind that there was also a language barrier that could be difficult at times but it was done. First, AISG needed key staff to know the new system and be able to teach and start training other staff. These key staff were then competent to use the system and understand how it works before passing that knowledge on down the line. The approach was, train the trainer in-house and then they could train the station managers and on down to the technicians who would be using the system most.
USING THE ULTRAMAIN SOLUTION AND MODULES
It’s always a challenge to implement a new software system because people get used to doing things in certain ways and, when that changes, they find everything difficult and complicated. There was a learning curve in the early days using the new solution because older mechanics wanted to stay on paper (no technology), and younger mechanics wanted a solution that was more like normal phone apps. However, after they started using it, the mechanics of all ages found the new solution intuitive and a real time saver. It was a challenge for AISG to make the users of the new system believe that this was a system that would create a solution for the future. We still believe that to be the case and, notwithstanding the challenges, the goal is still the same. If AISG can meet eighty percent of our original requirements, that will be a great deal.
GETTING APPROVALS
As has already been stated, there were many variables identified and many challenges that were not apparent at the beginning; those were the drivers that started increasing the complexity of the project. Of course, there was a budget to start with and then it started increasing; but that went well because the owners said ‘this is what we want; this is what we’re going to do’. There were some challenges with the approval but the deal was good, Ultramain understood AISG’s needs and, since this is going to be a long-term relationship, they were willing to help AISG in that.
LESSONS LEARNED
As always with a project on this scale, we learned a few new things along the way. First, we learned that you have to create the scenarios and learn to work with the software managers and project managers to see and decide what is going to be the solution. Having many variables already understood by both parties to the project helps to get to the final decision. Often, in projects such as this, there will be a project team that has a lot of ideas about what they want the future project to be but other than a few key corporate strategies there’s often no-one asking ‘how do we want to do business?’ For the software provider, having the opportunity with the customer to do that is very beneficial and gets the project away from all the independent ideas that a committee tries to push forward after the contract has been signed. Also, with any software vendor, there will always be the limitation of how the software works.
Solutions are all designed to work a certain way. Having an idea of how you want the business to run but then sharing that with and collaborating with the software vendor is the key to success. It ensures that the vendor understands how the client wants their business to be run and the client understands how the software works. Alignment between the vendor and the customer is a very important component in any successful project.
As part of its continual enhancement to the solution and in response to specific requests from AISG, Ultramain was able to make the required adjustments that AISG could see would work for us. There also were some changes to AISG processes to ensure that we got the best from the new software but, in the end, it was mainly a matter of getting used to doing things in a different way. If there is a solution that is going to save the user time, that is not a problem.
Potential customers for new software solutions need to think about how they want to do things in the future, how they want their company to work. Maybe the next step for the future in a project is to think about the affected work force; how old they are and how they will face the changes. The solution needs to be user-friendly. It will be necessary either to change the personnel or change the software. Some will immediately say that the new way is great, some older people might not take to it at first. The good thing in AISG is that our technicians have already been exposed to many different software solutions because our customers use different solutions. Having tested all the software, we came to the conclusion that ULTRAMAIN was the best solution for our company.
BENEFITS, NEXT STEPS AND FUTURE PLANS
AISG is still discovering the benefits as the timescale rolls out. But we already enjoy having real-time information, saving time on all the data that needs to be entered into the system; a job that can now be done on a mobile device. There is also a good system for organizing data to be able to analyze it and to create helpful reports that support planning and inform the business.
The next steps include, as already mentioned, extending the asset management capability to vehicles and ground equipment. Beyond that, the plan will be to integrate invoicing into the solution; have information available in real time and be able to feed the invoicing software system with the information that’s already in Ultramain.
AISG was already, at the time of writing, moving to Ultramain hosting and going fully onto the Cloud. ULTRAMAIN’s next release, called v9.0 Unity, is going to greatly improve the current capabilities with the release of a full browser-based html client. That will give users the ability to create their own user experiences within the software, so it’s not just the dashboards that are available today but it will be ‘build your own dashboards’ and ULTRAMAIN will be taking that to the next step enabling users to really assemble screens any way they want inside ULTRAMAIN and, if there are rough edges in the user experience, they can be trimmed down and made easier to use by users like IASG. Ultramain is always looking to improve optimization, something valued by users such as AISG.
A good thing with Ultramain is that, when other companies join the user population, and bring different problems and requirements with them, and they get solved, AISG and other customer get the benefit of that. Or when there is a different software update or a new function, all users will get that advantage at a reasonable cost. For instance, there was recently, in Asia, a Go-Live with ULTRAMAIN in a similar business to AISG who requested some enhancements and they have all been made available to AISG and others. The software is always evolving, pushed by customer ideas as well as Ultramain’s development process.
Contributor’s Details
Alejandro Bravo
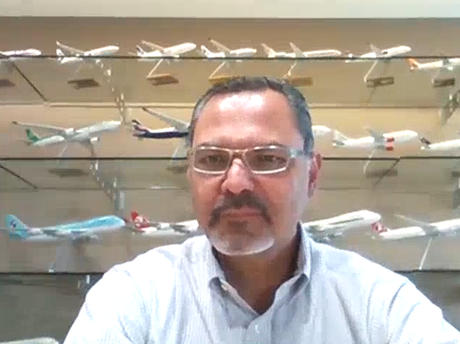
Alejandro has 24 years’ experience in Aviation Management Planning and Production Control. He is currently working at A&P International Services / AISG, as Sr. VP Production Control & COO, providing Line Maintenance services for Worldwide Airlines. His qualifications were earned at Texas Aero Tech, plus he has an MMBA in Management from Anahuac College, Certified A&P AMT by FAA and EASA. His technical training includes narrow and wide body aircraft from both Airbus and Boeing.
AISG
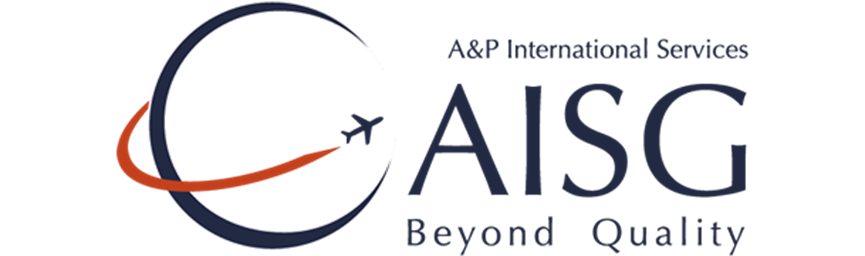
Aviation Integrated Services Group (AISG) is a leading aircraft services company for commercial airlines. Every year the Company performs over 125,000 maintenance operations, serving more than 70 airlines from around the World, at 30 airports in Mexico AISG and its ground engineers hold several aircraft approvals and certifications from airworthiness authorities and airlines from around the world, including: EASA under Part 145, the FAA, and Transport Canada.
ULTRAMAIN

ULTRAMAIN® is the leading paperless M&E / MRO software in the aviation industry. It provides mature maintenance and engineering software designed with and for aviation organizations from around the world. ULTRAMAIN® v9 is industry leading, web-based, paperless M&E / MRO software. The key to efficiently monitoring and managing any major operation is real-time data collection.
Comments (0)
There are currently no comments about this article.
To post a comment, please login or subscribe.