Articles
Name | Author | |
---|---|---|
Aviation Maintenance and Covid-19 | Allan Bachan, VP, ICF and Arun Navneethakrishnan, Aviation Solution Adviser, Ramco Systems | View article |
Case Study: Using digital solutions to drive efficiencies at APLUS | Wilfredo E. Regalado, Director Corporate Finance, Strategic Planning and Information Technology, Aviation Partnership Philippines (APLUS) | View article |
Real life essentials in five minute case studies: Recommendations to reduce NFF (No Fault Found) rate | Leandro Correa, Senior Vice President, Seabury Solutions | View article |
Digital processes, e-signatures and ETL/ELB promise better ways of doing business in the post-Covid world | Kirk Strutt, Senior Product Manager, IFS and Dan Dutton, VP, R&D, IFS | View article |
Aircraft IT MRO 2020 survey: COVID-19 and the response of aviation IT developers and vendors | John Hancock, Editor, Aircraft IT MRO | View article |
Aviation Maintenance and Covid-19
Author: Allan Bachan, VP, ICF and Arun Navneethakrishnan, Aviation Solution Adviser, Ramco Systems
Subscribe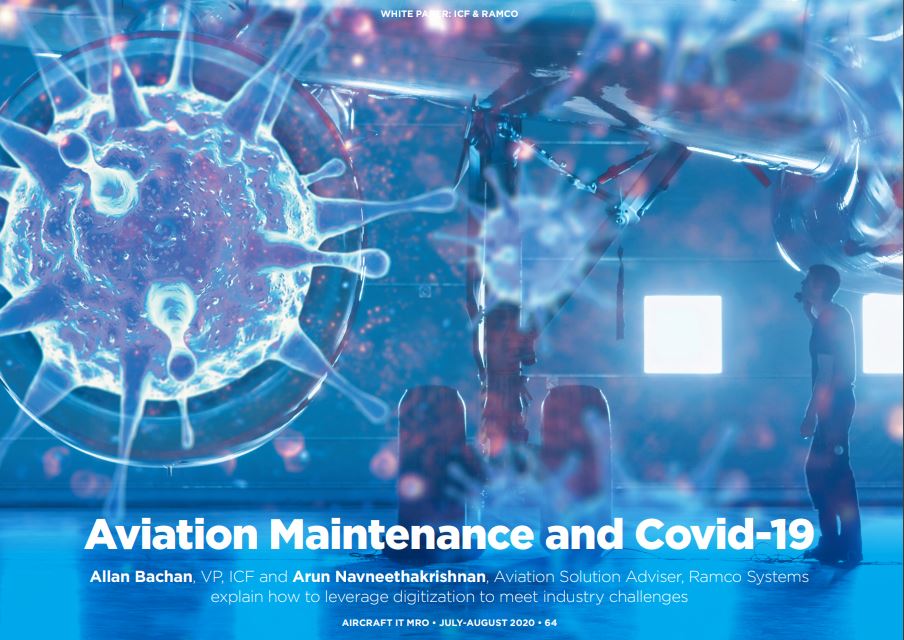
Allan Bachan, VP, ICF and Arun N, Aviation Solution Adviser, Ramco Systems explain how to leverage digitization to meet industry challenges
This article addresses the very real and present challenges facing the aviation industry as a result of the Covid-19 pandemic and will look at some coping strategies. We’ll also consider how maintenance organizations can leverage digital technology to improve process efficiency through a mix of automation, integration and optimization.
CHALLENGES
At the time of writing, the aviation space, including MRO, was mostly at a standstill. As we emerge from the pandemic, how can we use digitalization and modern technologies as a catalyst to help achieve effective advancements for the sector? We’ll consider this issue from three perspectives: people; assets; and money (figure 1).

People
The world’s population is largely confined to their homes. With global border restrictions and business closures, there is really nowhere to go anyway. Also, the airlines that are operating must abide by government and health protocols to maintain medical safety.
Assets
Aircraft make up a large portion of aviation assets most of which , are grounded and/or stored. With the likelihood that markets might not return to pre-Covid levels for two or three years, what will happen to these aircraft? How many will return to service? How will that impact operators and the wider community?
Money
Year on year, March 2020 saw a 52.9 per cent reduction in Revenue Passenger Kilometers. This has contributed to a $314 billion loss across the industry (Figure 1). There is no recovery playbook for this pandemic. No recipe exists which mirrors anything that has happened before. This does not resemble 9/11, SARS, MERS or any other past Black Swan events. History offers little guidance as to how we might recover.
A recent Oliver Wyman forecast (figure 2) projects that in December 2020, when some normalcy might be restored, the total number of aircraft in operation is likely to be many fewer than pre-Covid-19.
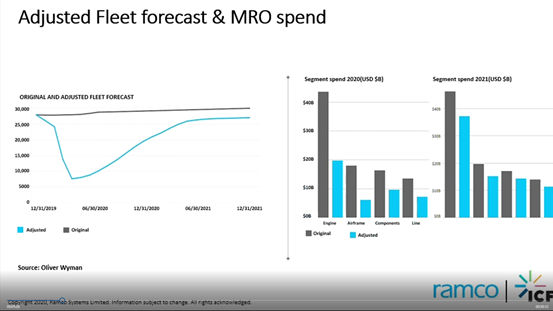
Aircraft maintenance is primarily driven by flight hours and cycles: if aircraft are not active then maintenance demand and MRO spend will be lower. Operators today are delaying and deferring maintenance events into the future. These events, however, can only be pushed so far and some are calendar mandated. Once flying restarts, demand will rise in 2021 but to lower levels than original pre-Covid19 projections across airframe, engines, components and line maintenance. The rise in 2021 will be largely driven by the maintenance events that have been intentionally rescheduled.
COPING STRATEGIES
No doubt, recovery will be complex. There are a number of different paths that airlines, operators, MROs, suppliers and OEMs may follow.
We identify several key coping strategies which are shown in (figure 3).
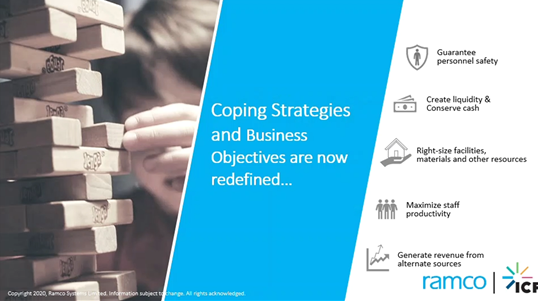
Guarantee of personal safety is first. Everyone has to feel one hundred per cent certain that they will not contract the virus from traveling and that their family will be safe. Each touch point and interface must be safe.
Secondly, generating liquidity and conserving cash is high on everyone’s agenda. This means that investments previously planned are no longer a priority and any expense is scrutinized with the utmost diligence. We also see that facilities have to be right sized along with materials and resources: buildings, spaces and material assets. For example, there is a lot of capital tied up in spare parts. With less aircraft flying, that value can be leveraged to carry the business forward through this trough.
Staff productivity is a key issue. We’ve seen many working from home during the pandemic, but how do you maximize staff productivity in such a situation? There are two schools of thought. People tend to spend more time working when at home especially if the work involves desk-based activities; but then there’s also speculation that if people aren’t out there mingling, if they’re not in a physical as opposed to a virtual community setting, productivity suffers. Sometimes just sharing ideas, communicating with each other can optimize productivity: so, finding ways to maximize staff productivity as we emerge from Covid-19 is key for organizations and how they are adapting or needing to change.
Also, revenue is being generated from alternate sources: we have seen passenger aircraft being flown with seats in and with seats out for cargo operations, especially PPE equipment.
KEY BEHAVIORS:
The above coping strategies are driving key organizational behaviors (figure 4).
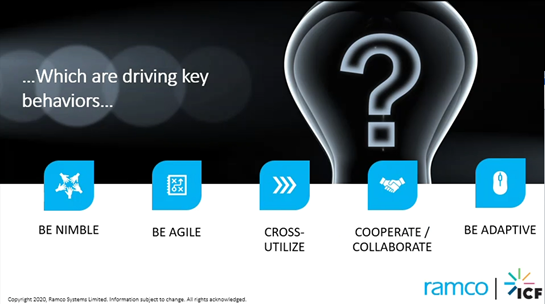
These behaviors, starting from the right, will be familiar throughout different organizations.
- Be adaptive: Coming out of Covid-19 requires everyone to adapt. There is literally no going back to the ‘old way’ since many things around us have changed.
- Cooperate and collaborate: Leveraging the strength of teams, qualitatively and quantitatively, is seen as a core behavior moving forward. No one organization has all of the elements needed for effective progress.
- Cross-utilization: Most organizations will be leaner. More has to be done with less and roles and responsibilities will span the vacant spaces. A more versatile workforce will develop and physical resources will be multi-purposed.
- Be Agile: This is a term that has been bandied about and is popular when speaking to transformation or adoption of technology. Being agile though is not just about ideas and innovation. It also has to apply to strategic and tactical execution; which has been lacking in Aviation MRO IT.
- Be Nimble: This defines how to execute. Some of the largest and most complex airlines in the world are operating decades old MRO IT. That demonstrates that we were not nimble enough even before Covid-19. Acting on change initiatives in a manner which provides quick benefits in a consistent manner is being nimble.
ENABLEMENT
How best can the strategies be achieved consistent with the behaviors? We believe that an integrated Technology and Processes approach along 6 key points should be implemented. These are illustrated in (Figure 5).
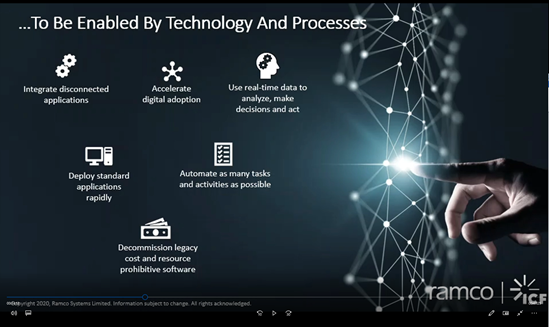
Of necessity will be the re-engineering of business processes.
Redefining all of the tasks which each staff role has to fulfill, taking full cognizance of the revised objectives and behaviors, will be a key action.
For example, having less in-person meetings for distributing work tasks on the front-line in Line Maintenance is not currently practical or safe. Workflow and notifications will therefore become more prominent. To go above just emails for such a task will incorporate all the 6 listed items to realize a workable solution.
Integration is the key; such as having a mobile device integrated into the back-end system. And that also has to occur in a collaborative environment: you might not have all the applications and you have to integrate within the organization and with other outside organizations and services.
It will also be necessary to accelerate digital adoption. This is a huge issue in the context of not being as nimble as we need to be. Using real-time data to analyze, make decisions and act is something we always do in our personal lives today. For instance, would you go to the grocery store when the number of Covid cases within your county or city is increasing? Again, in our professional lives, in the aviation space, who makes decisions on how the aircraft is connected to downline systems and, on seeing on seeing the information that delivers, making good decisions. There’s also deploying standard applications rapidly: we don’t see many long-term projects to get this, new applications have to be up and running as quickly as possible and, of course, they have to be built for purpose; there have to be modular offerings. We foresee a lot of that happening very quickly which, in turn, links back to that nimble requirement we covered earlier.
With constraints around staff and cost, it will be important to automate as many tasks as possible: so, technologies like artificial intelligence (AI), machine learning (ML), will come into play but how do you automate? How do you become, instead of predictive, prescriptive for maintenance? We sometimes explain this as, imagine a mechanic who, on his phone, his own device, can receive instructions as to: ‘where to be, what to be doing and how to do it…’ That’s more prescriptive. So how do we get the applications that support that philosophy? And, of course, it all has to be done in, as far as possible, a touchless environment. Finally, legacy and resource prohibitive software will have to be rapidly decommissioned.
The challenge with all the above is how to do that? We believe that these changes will occur not with wholesale steps (a ‘big bang’) but in small, modular steps and with deploying applications rapidly. This is a holistic approach and these are tenets as to how you’d operate but, moving forward, we see digital transformation using AI and ML as 10 times, not 10 percent, better. It will be massively transformational.
To illustrate all this, we’d like to show you a few use cases with Ramco software to demonstrate what we have covered already focusing on key roles who have direct impact on the aspects covered above like maximizing productivity, using the right skills and materials and, of course, to conserve cash and increase revenue. This will help when actualizing the digitization process. Some of the use cases that we’ll show are in production use with many operators, MROs, business aviation operators and defense agencies, helping them achieve their digital transformation goal.
USE CASES
Use Case 1: Aircraft maintenance Technician (AMT) – Advanced Mobility Access
In our first use case we’ll look at how mechanics and technicians can use software to collaborate virtually with improved productivity while also satisfying regulatory compliance. We’ll use Ramco’s Mechanic Anywhere Mobile App as an example to demonstrate the potential (figure A.1)…
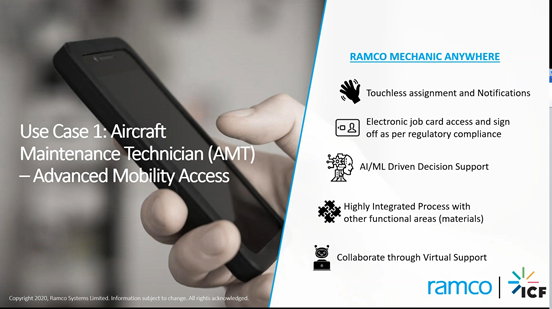
… for performing touchless assignments and instantly notifying the mechanic electronically rather than with a paper document. Mechanics get access to the job card they can also sign it off, all electronically within the mobile app and in accordance with regulatory compliance. Also, machine learning technology will help with decision support where AI is going to play the key role in an automated process, integrated with other functions, like supply chain, for tracking parts availability and getting parts issued using the auto-allocation strategy. Finally we’ll look at collaboration through virtual support for audits, inspections and any clarifications that will need mechanics to be present in person.
So first, touchless assignment and notification (figure A.2.1).
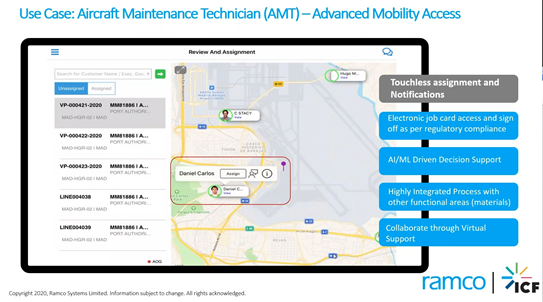
In figure A.2.2, you can see the assignment page in the mobile App that can be used by supervisors to review all the unassigned jobs based on input from the Maintenance Planning Department.
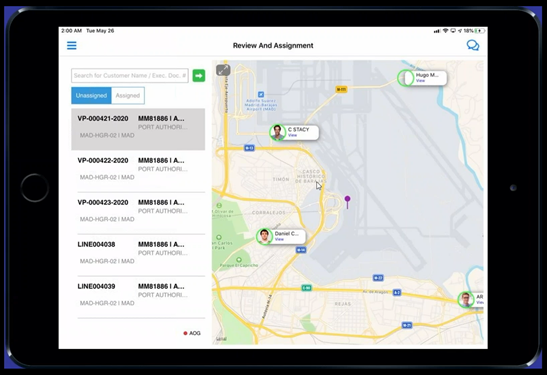
Supervisors can also look at the live availability of all mechanics, and their respective shifts so they can determine which mechanic to pick for the job based on proximity.
If the supervisor wants to assign the job to Daniel (middle left on the screen) he can select Daniel and look at his information, which will come up on screen with his availability and skills: if a mechanic does not have the right skill for the job, the system will not allow the supervisor to allocate that job to that person. In fact, the assignment process could be completely automated using the software scheduling and assignment capability. But, if the supervisor is able to assign the job to Daniel, that can be managed from the screen by clicking the icon. The system will allocate then job to Daniel and send him a notification to his mobile app or smart watch. This is similar to an instant messaging app, avoids any paper handover and provides a complete touchless experience.
After the job has been assigned (figure A.3.1) the mechanic will be granted electronic access to the job card within the mobile app. Ramco’s digital task card feature allows any scanned PDF or OEM task cards to be rendered electronically within the mobile app itself. There is also instant access to the job card information for the mechanic.
In the screen of the mobile app (figure A.3.1)…
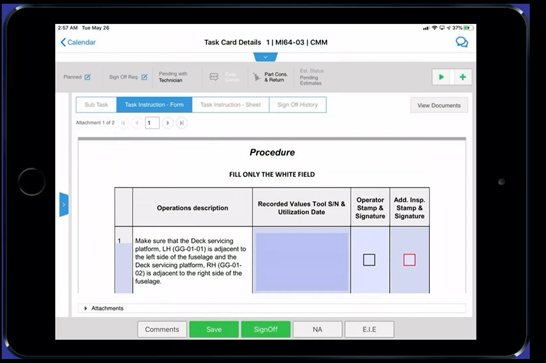
… the mechanic is assigned access to the electronic job card, is able to review the steps and procedures within the job card and then sign-off by just selecting the check box on the job card. On selecting and checking these boxes and providing the sign-off information, the system will provide a dual authentication pop-up as per regulatory requirements for keeping electronic documents. In order for a mechanic to perform an electronic sign-off they’ll need to provide duel authentication with a password and PIN, the system will then electronically sign-off the steps the mechanic has selected.
After sign-off, the system will send an electronic footprint (figure A.3.2) of the signature (green circle 000007) as a digital footprint for any future compliance references.
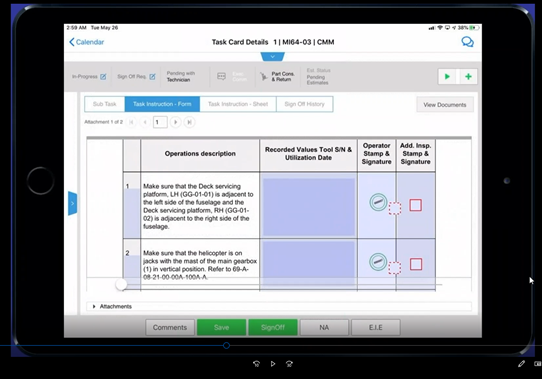
From the same screen, the mechanic can also gain virtual access to any reference documents or even launch an appropriate training video. This will allow the mechanic instant access to reference information without having to visit an engineering or a maintenance room to access training documents.
For discrepancy reporting (figure A.4.1) Ramco’s machine learning powered tool helps mechanics expedite the resolution process by automating the form filling, suggesting the next step, perhaps corrective action, and requesting the required parts.

In the discrepancy screen (A.4.2), when the mechanic starts typing the content, say, ‘dent on the rotor blade’, as the word ‘dent’ is entered, the AI will automatically list probable discrepancies based on the historical data of this aircraft.

The system will not only help fill in the data about this discrepancy but will also suggest corrective action and, again, help in ordering the parts to resolve the discrepancy. This will help to improve mechanics’ productivity where they would otherwise have spent a lot of time filling out the resolution procedure and requesting the parts.
Ramco’s mobile app is highly integrated with other functions such as supply chain where it allows mechanics to request a part and, upon request, it automatically notifies the inventory team (figure A.5.1) and allocates the part from the request
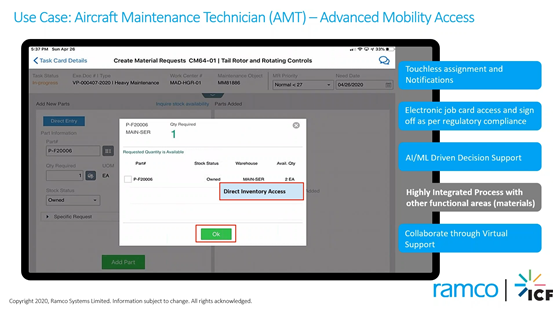
That helps avoid the manual process of communication between mechanics and the inventory team and reduces the time top source parts.
In the screen on figure A.5.2, the mechanic can type the required part details either by part number or just a description –the system provides a smart look-up.
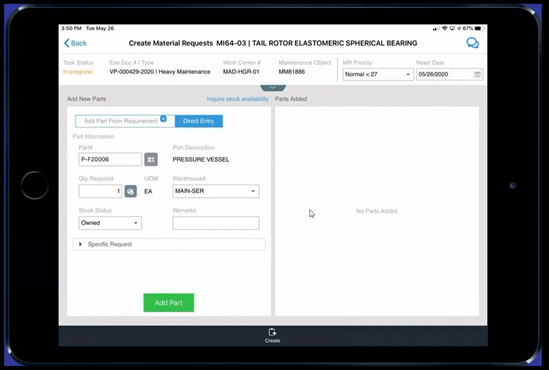
Also, mechanics can track part availability in the inventory from the screen: not only parts in the warehouse, but it can also parts currently on parked aircraft. This will help the mechanic choose whether to use a part from the warehouse or cannibalize an existing aircraft to help conserve cash. If the choice is a part from the warehouse, that can be selected, added to the request and then the request created from the same page. When the request is placed, the system will automatically generate a material request and notify the inventory team. The system will automatically allocate the part for this request and notify the mechanic once the part is available to pick-up from the warehouse.
One of the key challenges that will remain in the Covid-19 situation is to determine how effectively mechanics can manage their work with minimal face-to-face interaction and manual process, while maintaining regulatory compliance. To this end, Ramco offers a Virtual Support feature along with co-browsing capabilities to allow mechanics to interact and share their work in a live mode with their supervisors and colleagues (figure A.6.1).
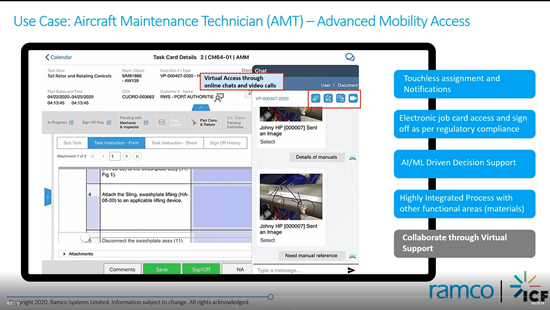
These capabilities can also be used to perform virtual inspections and sign-off by inspectors. This is a trend that readers will have noticed recently in the industry where even regulatory authorities are performing virtual inspections and audits of maintenance facilities due to the pandemic situation where they cannot do an on-site visit.
Let’s say a mechanic wants to review a damage notice while performing a job; they can instantly take a picture from a page in the app and share that information with their supervisor as well as making markings or annotations (figure A.6.2) on top of the image.
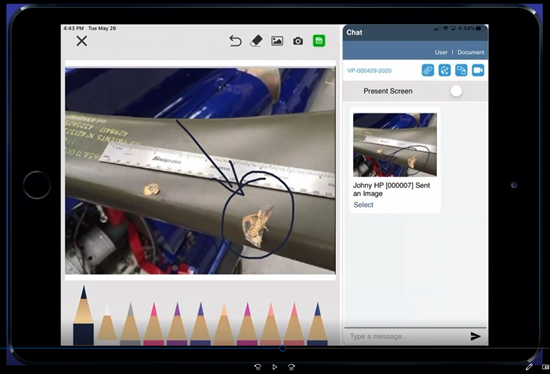
The supervisor can base a recommendation on this information and will receive an instant notification where they can respond within the chat window or, for further investigation, the mechanic can share their page or screen with the and show live details of the work that the mechanic is currently performing, allowing the supervisor to review and even perform a virtual sign-off using the co-browsing capability. Mechanics can even hold a video call with their supervisor and live relay the hangar floor through that video call so that the supervisor can look at the information and then provide a recommendation which will make the communication more effective.
This will help to minimize person to person interaction and help mechanics manage their work efficiently while helping to increase productivity even with the current limited workforce availability. This virtual support platform feature can be extended to any other role in the organization.
Use Case 2: Maintenance Planner – Auto Scheduling and Assignments
In this next use case, we’ll consider how maintenance planners can contribute to digital adoption using technology tools. Maintenance planners play a major role in minimizing cost and that can be better controlled with effective planning tools. With the current Covid-19 situation, planners have to think out of the box to effectively use the available resources and manage the maintenance facilities with very little margin for error. This case shows how a maintenance planner using MRO software can… manage auto scheduling of jobs based on available capacity and daily changing constraints; ensure skill validity to have the right resources appropriate to the job; and manage assignments with no paper hand-off.
Ramco’s advanced planning tool includes (figure B.1) a holistic view of the maintenance forecast along with any dependencies that might impact the turnaround time (TAT) for an aircraft undergoing maintenance.
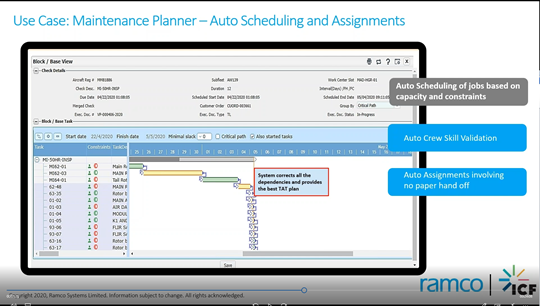
Based on the optimization algorithm, the system can automatically clear constraints or any dependencies that fall under the critical path of the forecast in the figure, allowing the maintenance planner to manage by exceptions which enables a highly automated process and ensures a high level of productivity. The forecast is not only determined based on familiar utilization parameters like flying hours, cycles, seasonal variations, etc. but, with the current situation, the parts on the aircraft should also be taken into consideration. The planning tool considers those parameters to provide the constraint visibility to the planner when, based on that information, the planner can effectively manage the currently operational fleet.
With the current Covid-19 situation, in addition to regular resource constraints, the organization needs to ensure that the pandemic does not spread within the organization (figure B.2.1) which might impact the complete operation.
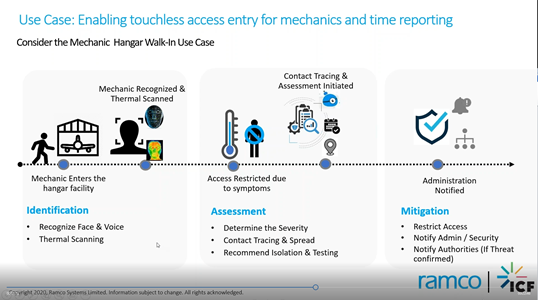
Keeping this aspect in mind, Ramco has introduced a touchless access control system that will scan mechanics for both facial and voice recognition and thermal condition, record their presence, and can be integrated with an existing HR system. The solution restricts access if a mechanic is found to have a temperature outside of a given range and, in case of an asymptomatic but Covid-19 infected individual, the system can identify that by using self-certified questions and chatbot as per the health authority guidelines. Contact tracing can also be enabled by integrating with the mechanics’ calendars to identify the potential contacts that they’ve had in the past, and then help mitigate any further risk. This system can also notify the administration or security, using the workflow engine, to mitigate any risk and take the necessary precautions.
The input from this solution is integrated into the planning tool where the system automatically reschedules and reassigns resources for the forecasted job in light of this constraint. Ramco’s touchless access control system can be deployed as a stand-alone or it could integrate with an existing IT or security system. You can see the system in use at Ramco’s Global office (figure B.2.2) where it is integrated with IoT door sensors and can restrict access in case of elevated temperatures.
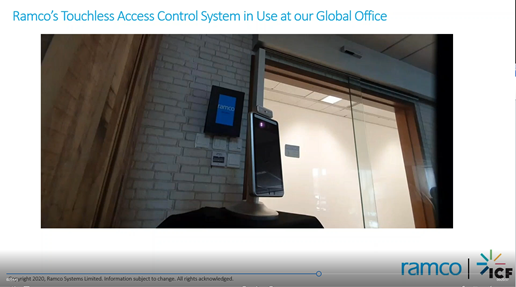
The set-up can be deployed at multiple hangar access points.
With multiple constraints evaluated automatically, the system also validates if the mechanic has the right skill and certification to perform the task and notifies the planner in case of any restriction. The mechanic also gets notified in advance in case they have to get re-certified for a respective skill. This helps to avoid resource non-availability and, in turn, helps save the cost of cancellation.
After the job is assigned, the system automatically notifies the mechanic in their mobile app with electronic job card access (figure B.2.3). This will help minimize the lead time in paper document hand-off and brings process efficiency.
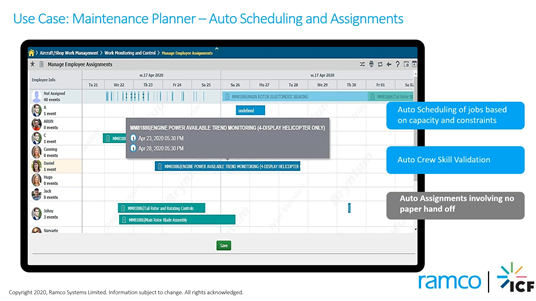
The system also keeps track of actual work done by mechanics and updates the maintenance schedule in real-time.
Use Case 3: Material Planning and Buyer activities
The last use case is about material planning and buyer activities the larger part of cash conservation but still meet the demand for the parts. As more than seventy percent of aircraft are currently parked there are parts that can be cannibalized from those aircraft in order to meet current demand and that will help to conserve cash for the organization. Historical data on demand might be of little or no use to forecast and manage stock in the current situation; planners must continuously work with the maintenance and operations teams on an almost real time basis through planning the parts and determining the best sources for purchases. In the long-term, automating the entire planning and procurement process by EDI connection between customers and suppliers is expected to introduce efficiencies and cost reduction for the purchasing process. In this use case, you will see how materials planners or buyers can get global visibility of inventory across locations and parked aircraft, perform dynamic demand planning and enable frictionless procurement with EDI.
Aircraft currently held in long-term parking (figure C.1.1) have no focus on compliance or near-term plans for reactivation. These aircraft are expected to help with conserving cash as parts might get removed and resold or used to fulfil the demand from the current operational fleet.
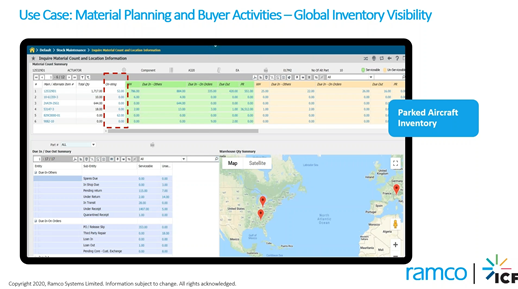
MRO software is expected to provide this global visibility to all the key stakeholders such as inventory planners, warehousing and maintenance teams. As you’ll see on the screen in the figure, visibility is extended to the level of the parts currently attached to parked aircraft as well as the aircraft’s location.
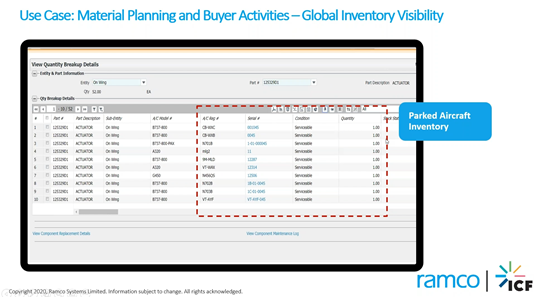
Drilling down further (figure C.1.2), details such as the serial numbers, and other technical parameters like flying hours, cycles and also the quantity are shown to the materials planner. Here, graphical visibility helps the planner to determine the best source to fulfil the demand with the least logistic cost to the organization. With a growing need for consolidation of resources to manage and centralize supply chain activities, assignment of a specific demand to the material planner will help achieve accountability, until the part is acknowledged with proof of delivery. The demand management hub screen in Ramco Assignments can be managed based on predefined groups by supplier or part type. This process can be further automated through the machine learning algorithm based on historical data available.
Based on the demand characteristics like part information, quantity required, location, technical requirements such as certificates, stock availability, inventory and in-transit movements in the warehouse or from suppliers, the planner gets the recommendation automatically from the system to fulfil the demand. In this case, the recommendation to manage the demand offers four sourcing options as can be seen on the screen (figure C.1.3).
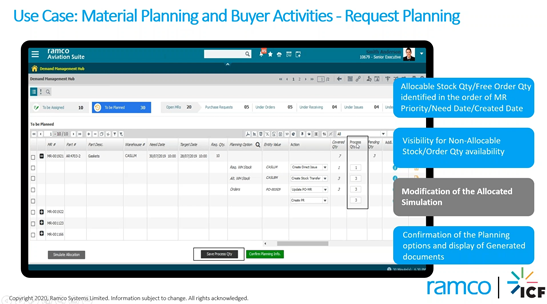
The recommendation parameters can be set based on a target objective. For example, lowest turnaround time in case of AOG (aircraft on ground): demand and lowest cost for replenishment. Planners can also over-ride system recommendations. Ramco Demand Management can also be configured using API (application programming interface) calls to consider the stock availability from the supplier or part traders. In addition, carriers like FedEx will seamlessly provide information on the part movement from pick-up to the delivery along with any delays in this hub.
Automation, not only within the organization but over the larger eco-system, enables the organization to reap the ten times the benefit as opposed 10% incremental benefits. One Ramco customer who is primarily in the part trading business supporting one of the largest MROs in the world, has increased revenue over ten times with very marginal additional cost by automating the standard process, around 70 to 80 percent of the business, and bringing in exception based-only manual interventions. This automation (figure C.1.4) is powered using EDI (electronic data exchange) connectors by partners like AeroExchange where the sale order is issued through the EDI and processed for the demand fulfilment.
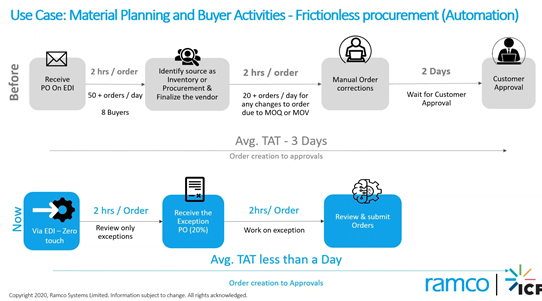
If the decision is to buy then the system can apply the supplier based rule or the machine learning algorithm can initiate the purchase order which gets transmitted to the supplier automatically. Manual approvals are triggered only where the supplier is not in the recommended list or where the price is different from the contracted price.
The entire value chain is automated with the shipping note from the supplier sent to the customer instantly and the status of the shipment transmitted to the customer as well. With 70 per cent of orders automated, the lead time has reduced to minutes for an order with no exceptions and less than a day for an order that requires approval or with some exception. This is considered as a true digital transformation for an organization.
In this time of
uncertainty, digital technologies can help an airline or MRO be agile, nimble
and able to deal; with rapidly changing circumstances and demands. If, at the
same time, they can achieve greater cost effectiveness, that will also be good.
Contributor’s Details
Allan Bachan
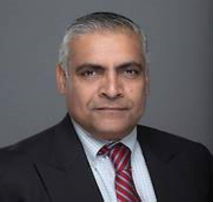
Allan is a Vice President at ICF responsible for MRO Operations and IT practice and he manages the Aircraft Commerce Consulting relationship with ICF. His experience includes managing application design, development, and implementation for strategic clients in the MRO industry using different commercially available MRO IT products. In his career, Allan has fulfilled the following leadership roles: MRO IT practice and technical lead; MRO systems Product Principal; M&E and MRO Solutions Director and Manager of Technical Records, Maintenance Planning and Production Control.
Arun Navneethakrishnan
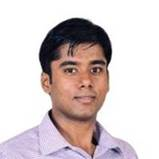
Arun has over 12 years’ experience in business transformation, project management and solution consultancy in maintenance, supply chain, production planning, flight operations and financials for several aviation segments. He has domain and industry knowledge combined with IT expertise. Arun has been with Ramco for over 10 years, involved in several project implementation and product development phases. He heads the solution advisory group in the Americas for new accounts and existing projects and holds a Masters in Aeronautical and Airport management
ICF Aviation
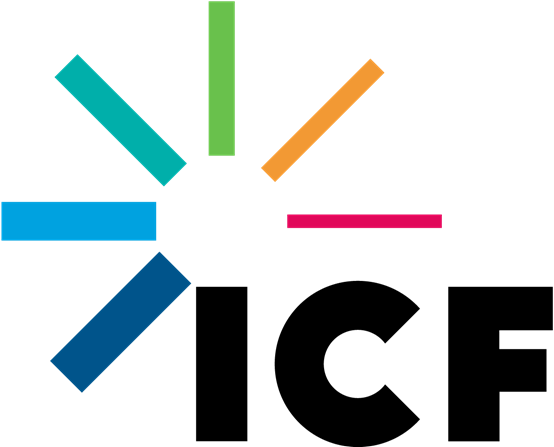
ICF works across the aviation value chain to help clients navigate the complexities and uncertainties of the changing aviation industry. Whether helping airlines and airports reinvent how they engage with customers, assembling the world’s largest leasing transaction, speeding up aircraft turn times and improving on-time performance, or helping an international airport achieve its goal of doubling capacity, ICF has a deep understanding of the forces that can impact our clients’ success in an era of unprecedented change.
Ramco Aviation
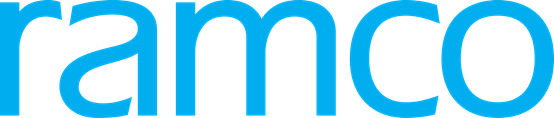
Ramco Aviation software offers Maintenance solutions on cloud and on premise with multi-tenant capability and next-gen mobility, catering to the needs of Airlines, Heli-Operators, MROs and Charter operations. Next-gen mobility solutions for maintenance operations are available through an app ecosystem where MRO supervisors, mechanics, pilots, storekeepers and customers can seamlessly execute critical operations on the go, from anywhere, anytime.
Comments (0)
There are currently no comments about this article.
To post a comment, please login or subscribe.