Articles
Name | Author | |
---|---|---|
Meet the IntelligentEngine; taking predictive engine maintenance to the next level | James Elliott, Principal Business Architect, Aerospace & Defence, IFS | View article |
Cargolux & TRAX eMOBILITY Q&A | Stephane Kastler, Director of Maintenance & Production, Cargolux | View article |
Vistair brings it all together at Viva Air | Captain David Restrepo, Flight Standards and Training Manager at Viva Air Colombia | View article |
Right person, right qualifications, right place at Lufthansa Technik | Luca Jelic, Training and Quality specialist at Lufthansa Technik’s Base Maintenance Division | Andres del Pino, CEO, StaffNow | Svetla Stoeva, Former Head of Staff Agency at Lufthansa Technik Base Maintenance | View article |
Cargolux & TRAX eMOBILITY Q&A
Author: Stephane Kastler, Director of Maintenance & Production, Cargolux
SubscribeStephane Kastler, Director of Maintenance & Production, Cargolux, takes some time to talk to Aircraft IT about the how & why of their successful implementation of the TRAX eMobility Shop Control App.
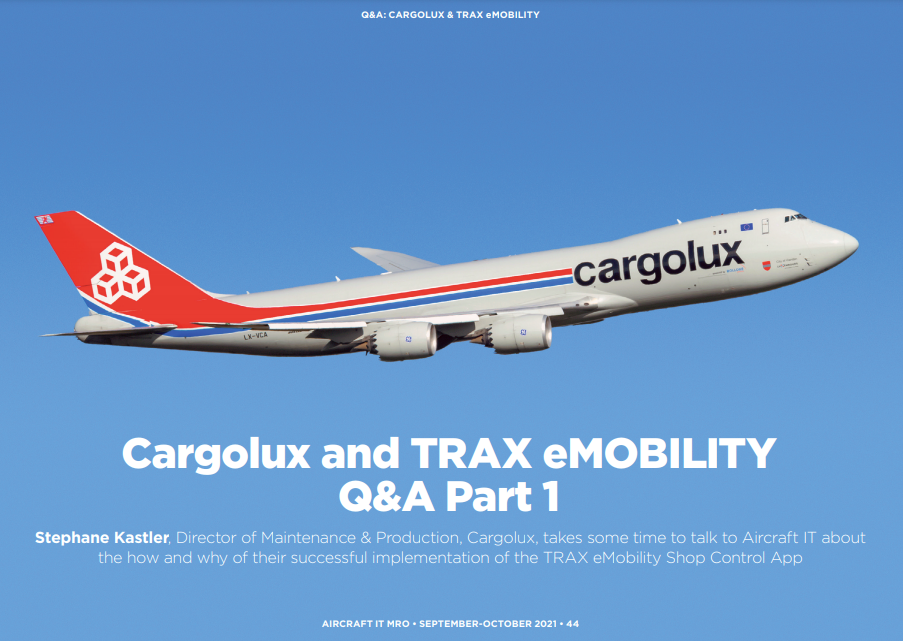
Aircraft IT: Thanks for joining us, Stephane. It’s great to be able to hear how Cargolux has implemented the TRAX eMobility Shop Control application. We have a few questions that we will go through, so let’s get straight on with those.
Can you start by telling us a little bit about your business case for implementing the app and how you’ve seen it maximizing your operation?
Stephane Kastler (SK): Thanks for having me. The shop control app is used in our shop environment. In Cargolux we have 10 back shops which support the airline and the maintenance organization, and their mission is to repair many 747 components for the fleet. At the same time, they also support the hangar and the line operation directly. So that’s what we have grown to in the last few years. Basically we are repairing about 10,000 components per year. It is a lot of components, many of which are needed urgently or are required on an AOG basis. With so many components traveling through the different shops, we need to track them and their progress.
PULL QUOTE: “The more you reduce the working process, the more you make life simple for the shops and for the people who are working on the parts. That is the name of the game, that’s what we are achieving here.”
With the increase of our fleet and the rise in the numbers of components that we are repairing, it has become very clear that we need to have a system which shows us an overall priority and progress tracking status on the parts that we are repairing. That is what the Shop Control app does for us. You can see where we are coming from is a situation where components were coming off wing and in need of repair, and we would just send them to the shop. The shops receive a lot of components and they have to figure out the priorities. The shops have to figure out what needs to be done on the components. This creates a large backlog of parts for them, and with a large backlog comes a lot of issues of space, of priorities with other elements of the organization, etc. That had become a major problem for us. At the same time when you have these ten thousand components which each sometimes require very small action in different shops it starts to be very difficult to know where you stand with all these components. So some time ago we decided that we need to create a system –a process let’s say– which is controlling the inductions of our parts into the shops system. As well, we need to control the induction of parts into our 10 shops, and once the part is inducted into the system, we have to make sure that it has the right priority and that we can track it in real time. That’s basically what the Shop Control project was for. The Shop Control app is giving us a way to decide when the part needs to be sent to the shop for repair, when is it needed, and when it has been released. We can track in real time what is happening to that part and that’s extremely critical. By doing this you manage your parts, you manage your parts ‘in process’, you are reducing your turnaround time, and you are able to take the right decisions and to repair the right part at the right time. That is where the added value is, of course. The turnaround time is immediately linked to the number of parts you need to hold in your stock. So the better we are in turnaround time the better we are supporting the airline.
Aircraft IT: Brilliant, very good. Thank you very much.
So overall how do you think that the maintenance digitization has impacted your profitability?
SK: What we are looking at in Cargolux is to have the best way possible for mechanics to focus on their core job which is to maintain and to repair the airplanes. We are trying to remove non-value-added time away from the work of these mechanics and that is what digitalization is doing for us. It is simplifying our processes and it is also bringing to the mechanics the right information at the right time in a real-time format so that we are able to cut down on some processes which are cumbersome. We are cutting down, for example, white boards which we used to have not too long ago in the different shops. They are now replaced by screens which are displaying real-time information.
That is where the added value is, of course. The turnaround time is immediately linked to the number of parts you need to hold in your stock. So the better we are in turnaround time the better we are supporting the airline.
Digitization is also bringing a lot of aspects which were just not possible before.
A good example is task cards. We still have paper task cards today but soon they will be transferred to digital.
Interestingly, when a mechanic is doing a task and signing off on the paper task card, this process is not controlled.
Somebody may have to come and check if this was the right mechanic with the right skill that has been stamping that task and confirm if he was authorized to do that.
So there are a whole lot of manual processes implied in the background of that manual stamping.
Now that we are working digitally, we are able to control the task card. We issue the task on the iPad and only the mechanic with the right skill and a skill which is not expired can sign off.
The system performs what is in effect an automated QA which is replacing a very cumbersome manual process which was in place up to up to now. It is error free whereas we never managed to get there with a paper process.
Aircraft IT: Very good, yes, that’s great.
So, what has been the response of your employee team to the introduction of this app and the adoption of new technology as part of your efforts to mobilize your maintenance operation?
SK: It has been extremely good. Not only because all technicians see something nice or fancy, but because it is immediately making their life simpler.
They now have access to real-time information so that means that they don’t have to go in the system and look for it or call somebody to look for it.
As well, it is creating data which is providing them an oversight of the situation of their shop or team. They don’t have to go and look at all these components to check the status on a regular of weekly basis. It is on the screen right in front of them and it is always up to date.
We have removed all that manual work of creating the status, which was the case up to now.
This solution also provides good visuals. If the status is bad, it is red. It is going to show red as of the time we decide we need to pay attention to the component.
It provides easy visual management for everybody across the organization to see how we are doing.
So from the technician to the vice president they can come to the shop and see a screen with reds, and know that there might be something that we need to look at today.
Aircraft IT: Can you describe some features they’re using and how they aid your team members and the company?
SK: The shop control app is now implemented in every one of our shops and is used on a daily basis.
The Shop Work Order window displays specific Progress details for the chosen Work Order I will demonstrate the features that they are using on the screen. It is a simple but effective system, and it is also very easy to understand, so it only needs a basic training of a couple of hours.
With a given situation, you click and enter the information and quickly see it. You don’t have to print the task out, you don’t have to print paperwork to sign, and it’s all traced in the system.
It’s efficient, it’s lean, and basically very good.
Aircraft IT: How is the dashboard high level overview such as the shop indicator detail window helping with your managers for following the KPIs?
SK: This is extremely critical. It is very beneficial to have KPIs which are compiled in a live format like this because we come from a situation where we used to manually compile our KPIs.
This was done maybe on a weekly basis, or a monthly basis, so you are already looking at something which is expired. You are looking at what you have been doing in the last week or in the last months and then you look at that and you try to see if you need to take corrective actions.
Now it’s live, it’s in front of you, it’s up to date at any time, and this is extremely valuable because then we can take the actions which are necessary at the earliest point of time. This is extremely critical for a shop environment because the issue of today is the stock shortage in terms of parts needed for tomorrow or the day after.
If you have a component that is dragging in the shop due to a dependency, and if it is not escalated, than this component keeps on being delayed which will ultimately create a stock shortage.
If instead you react a few days in advance of the situation then you are in a much better position and not faced with zero stock.
PULL QUOTE: “What we are looking at in Cargolux is to have the best way possible for mechanics to focus on their core job which is to maintain and to repair the airplanes.”
Aircraft IT: Very good. That’s great thank you.
Did your end users find the training to be helpful and the product to be intuitive and easy to learn?
SK: Yes, definitely. The training was quite short. The user guides are also very easy to understand because basically the app is intuitive, as I’m going to show you online in a minute.
It is state of the art and what you would expect from such a software nowadays. It has a modern feel to it, and you get right to it. It is no questions asked.
We have had very limited feedback or a very limited number of questions put to us because it was just a good implementation.
Aircraft IT: That’s great thank you.
So how would you describe the implementation project support?
SK: The implementation of the project and support from TRAX was great. First of all, what I really appreciated was that they were really open and interested in developing something new. The shop control project that we had at Cargolux was an idea which was already a few years old. We were more or less stuck with the development of the real-time software which was linked to that project because it was a difficult tool to set up. Yet TRAX was really interested in developing an app.
It was quite unbelievable how fast TRAX developers became familiar with the shops, our processes, how all our shops are working, and all aspects of the MRO environment. So it was just a pleasure to work with TRAX on that.
A huge added value of having an app developed by TRAX is that they access the database and pick up the information that is already there and they just make a new tool out of.
Aircraft IT: Very good. That’s great thank you.
Did your end users find the training to be helpful and the product to be intuitive and easy to learn?
SK: Yes, definitely. The training was quite short. The user guides are also very easy to understand because basically the app is intuitive, as I’m going to show you online in a minute.
It is state of the art and what you would expect from such a software nowadays. It has a modern feel to it, and you get right to it. It is no questions asked.
We have had very limited feedback or a very limited number of questions put to us because it was just a good implementation.
Aircraft IT: That’s great thank you.
So how would you describe the implementation project support?
SK: The implementation of the project and support from TRAX was great. First of all, what I really appreciated was that they were really open and interested in developing something new. The shop control project that we had at Cargolux was an idea which was already a few years old. We were more or less stuck with the development of the real-time software which was linked to that project because it was a difficult tool to set up. Yet TRAX was really interested in developing an app.
It was quite unbelievable how fast TRAX developers became familiar with the shops, our processes, how all our shops are working, and all aspects of the MRO environment. So it was just a pleasure to work with TRAX on that.
A huge added value of having an app developed by TRAX is that they access the database and pick up the information that is already there and they just make a new tool out of it.
This is a huge advantage because when you do something in the system in one location then you find it back on the shop control window, it’s just all integrated and that’s what makes the added value of the Shop Control application.
Aircraft IT: Do you see opportunity for further process improvements?
SK: Yes, there is. Right now the Shop Control app is the application which is controlling the flow of work orders or repair orders in our shops. There is already a lot of ideas coming from the shops themselves.
PULL QUOTE: “It was quite unbelievable how fast TRAX developers became familiar with the shops, our processes, how all our shops are working, and all aspects of the MRO environment. So it was just a pleasure to work with TRAX on that.”
One of the two greatest possibilities for improvements is to expand the support to the hangar or to the line. We do repair components in the shop, but we also work on work orders or task cards or projects which are directly linked to the airplanes we have in the hangar, or the airplanes that are on turnarounds on the line. So that would be a first potential improvement.
A second improvement is to continue to build on the Shop Control app and make the process in the shops fully digital, because right now we are at a stage where the management of the shop work orders is digital, but the shop work order itself is still a paper package.
The Shop Control app already has the prime features to make that package digital and that would be a very interesting next improvement.
Aircraft IT: How has the Covid-19 crisis affected your organization and how has this software helped you?
SK: Specifically, at the start of the covid crisis (because now we’re getting accustomed to it, obviously), it was a big shock for us because in the cargo industry there was a dramatic increase of operations.
The cargo airplanes picked up the freight left by the passenger belly market and also, they had to pick up all the PPE for the various countries. So we had a dramatic increase in our operation and at the same time we had a dramatic change of working conditions in all our environments.
The cargo airplanes picked up the freight left by the passenger belly market and also, they had to pick up all the PPE for the various countries. So we had a dramatic increase in our operation and at the same time we had a dramatic change of working conditions in all our environments.
We were affected by quarantine, and we were affected by leaves [vacations] when our employees had to take care of their kids because the schools were closed, etc. So we really had to focus on that.
At our core we had to completely refocus ourselves on just primary operations. For the first six months we did not do any project development or “nice to have” extra things in our duties. We just purely focused on operating and tried to get the airplanes flying. And in that context when you have a software which is supporting you, which is freeing you from doing all this work of analysis such as “where is my part”, “what is the status of my part”, etc., this is invaluable because you just get right to it, get to the point and get your job done. That was clear.
Comments (0)
There are currently no comments about this article.
To post a comment, please login or subscribe.