Articles
Name | Author | |
---|---|---|
How I see IT – Improving systems adoption | Allan Bachan VP, Managing Director, MRO Operations, ICF. | View article |
Case Study: Better technology supports better lease returns at Jazz Aviation | John Hensel, Manager Business Services Portfolio, Jazz Aviation | View article |
Case Study: Coopesa goes from effective to efficient | Walter Ching, Director Operations / COO, Coopesa R.L. | View article |
Case Study: Better technology supports better lease returns at Jazz Aviation
Author: John Hensel, Manager Business Services Portfolio, Jazz Aviation
Subscribe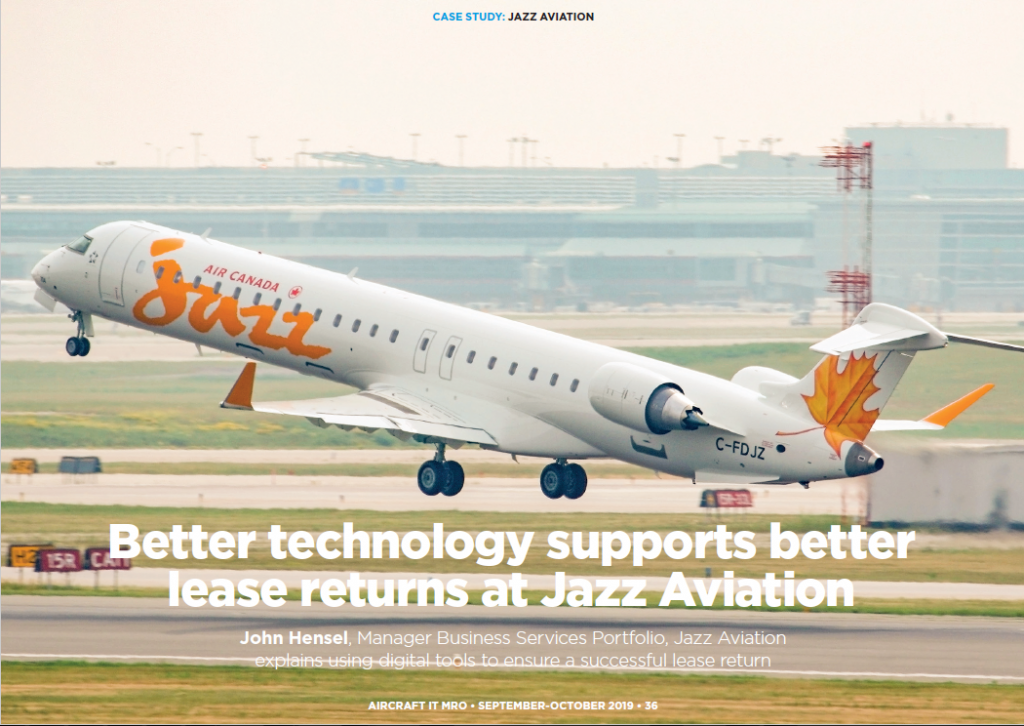
John Hensel, Manager Business Services Portfolio, Jazz Aviation explains using digital tools to ensure a successful lease return
On first reading, it might be that the title will not set pulses racing; but bear with me: lease returns, and especially the benefits of getting them right without many hours of work, is exciting. It’s taken me a while to appreciate that, but now I want to share this project with readers. First, though, I’d like to tell you something about Jazz Airlines.
JAZZ AIRLINES
Jazz has 116 aircraft of which 110 are leased meaning that there is always a big focus on lease returns. The airline serves 78 destinations within Canada and the USA, under the ‘Air Canada Express’ brand, operates 630 daily flights and carried 11.1 million passengers in 2018. As well as looking after Jazz’s fleet, Jazz Technical Services (JTS) also offers third party MRO services.
Jazz has won numerous awards (see below) including for Airline Reliability.
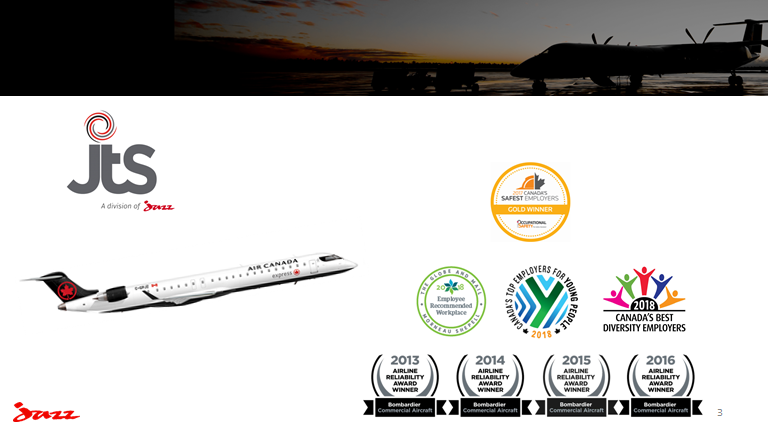
THE BACKGROUND TO DIGITAL LEASE RETURNS
It was as far back as 2009 that Jazz got approval for electronic sign-off for task cards and non-routines. We have one hundred percent approval for Task Cards and Non-Routines from Transport Canada and 92% from our lessors. So it was still necessary to print ADs (Airworthiness Directives), SBs (Service Bulletins) and Structural Deviations… sign them and put them in a box. That brought us down to filing/storing only eight percent of the work we completed in a paper format. That went well; lessors weren’t happy at the beginning but there has been a real shift between then and now. In 2016 Jazz went mobile with Trax eMobility apps. The Trax mobility apps gave the AMEs (Aircraft Maintenance Engineers) the ability to do real time entries with a higher level of detail to the entries quickly by using the voice recognition and camera functionality. That improved the data being received by the lessors. This really got the lessors excited so that, in 2017, they started to ask for all electronic records, which was a surprise to us. We now give them electronic non-routines, task cards, scanned PDFs of the Part Certifications and have been doing that for two years now. But Jazz still had a pile of boxes which, at the end of the lease, we hand over to the lessor who puts them into some other storage area where nobody looks at them.
In 2019, the lessors started to ask Jazz to accept used aircraft with electronic records. At the time of writing, Jazz had accepted three aircraft through that process. Now Jazz has two versions of electronic data. There is the rich data coming out of the system, and there are the scanned PDFs, so there are both smart and dumb documents. The documents coming from the other carrier (the previous lessee) are all PDFs with supporting data, so the receiving lessee doesn’t get all the data.
In that context, Blockchain looks exciting, but it might take a few more years before its use is universal. Although Blockchain is not yet part of the Jazz system, once this current implementation has been successfully accomplished, Blockchain will be the next project. Blockchain will deliver rich data with all the detailed supporting data from the system relevant to an aircraft. This will be useful for operators but will also improve data going back to the lessors, next lessee, and in any new leased aircraft inductions reducing everyone’s risks/costs. Also the further the sector moves from PDFs, the better it will be become for projects like Artificial Intelligence (AI), all that rich data driving improvements/reliability/safety/cost reduction. Meanwhile, that rich data is still needed.
Jazz leases from nine leasing companies and undertakes four to five lease returns each year. To date, all lessors have accepted Jazz’s current process for electronic signoff – including ADs, SBs, Structural Deviations, Modifications and scanned Part Certifications.
So, going back (see above) to 2017, Jazz started talking about improving the process. Over the last couple of years there have been different projects to get the change going. This has led to identifying the keys for a successful lease return (figure1) and what could be automated with the data to make the lease return process seamless and painless. There can typically be three months of pain with all the paper documents required to be organized with the electronic files for the lessor. You end up with two set of data, electronic and paper. So it is not if, it is when the lessors find mismatches between these two set of data the fun starts. They may accept them or they may not.
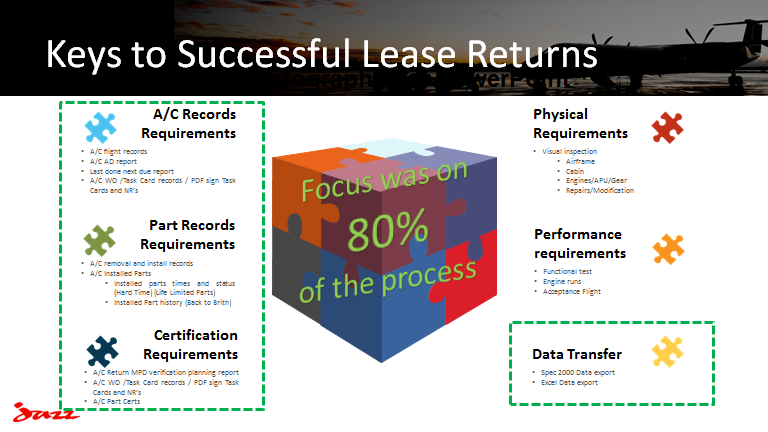
In figure 1, the items in the green squares are where Jazz focuses: Aircraft records, part records, certifications and data transfer. The current process flow at Jazz (figure 2) has been used for about 50 aircraft and it goes through all the steps to do a lease return.
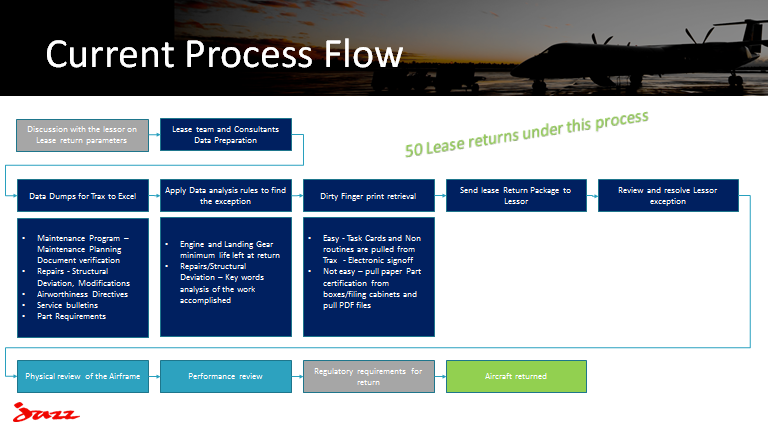
Starting with a data dump from the Trax system to an Excel file, we then analyse that data to find exceptions, then find the paper documents, match them to Excel and then return it to the lessor before reviewing the findings. It’s a three month process.
From this current process flow, a list of targeted improvements was identified. Jazz has worked with Trax on those improvements with a view to launching a new solution in July 2019 – the Trax Aircraft Lease Return Portal. Some of the improvements that are anticipated from this new approach to lease returns include:
- Cost reduction;
- Time savings;
- On time return schedule;
- Less preparation time required;
- Complete record portfolio;
- Improved Lessor Confidence;
- Real time updates;
- Visibility in real time of data problems;
- Improved data quality;
- Reduce printing paper & distribution efforts;
- Increased employee engagement.
This is really a ‘rinse and repeat’ for Jazz as the same process had already been applied to the first part of the data, task cards and non-routines. We are very confident that the savings will be realized and are positive about what will be seen at the end after working with the lessors.
The Trax lease return application has been built with two views: one for the operator and one for the lessor, and covering aircraft, engines and gear. Also built into the application is the automation of the exceptions finding. Where users are looking for missing documents or finding mistakes in the MRB (Maintenance Review Board) program, Jazz wanted to build that all into the application. Then, instead of taking two or three weeks for somebody to analyse that data, it would be known right away what the exceptions are. And when Jazz is talking to a lessor a few months before the return date and is looking to negotiate some things such as percentage of life left in engines and gear at the lease return date, it’s possible to know what is going on within five minutes. The app works in real time as part of Jazz’s core MIS (Maintenance Information System) from Trax.
Some of the functionality that has been put into the application includes:
- Aircraft Lease Dashboard;
- Aircraft Records:
- AD and SB status;
- Modifications/Repairs/Structural Deviations;
- Last Done Next Due Maintenance;
- Images / Files – Work Order/Task Cards/Non-Routines/Part Certification;
- Installed Component Status;
- A/C Times;
- A/C Transactions.
- Lease Compliance Check to the MPD;
- Spec2500 Exports.
These cover typical pieces that you would be looking at for a lease return — Excel files, paper documents — all the things that are collected. One exciting part that has been added into the Lease Return Portal app is the MPD (Maintenance Planning Document) check. Jazz will be able to take the MPD from the manufacturer’s site, load it in, compare it and make sure they are one hundred percent compliant in minutes, or the lessors could do that to give them the confidence in the process. Jazz saves money and the lessor saves money.
DASHBOARDS
Here is a brief review of some of the aircraft records, starting with a high level dashboard (figure 3.1) showing all aircraft, lease returns, and other data.
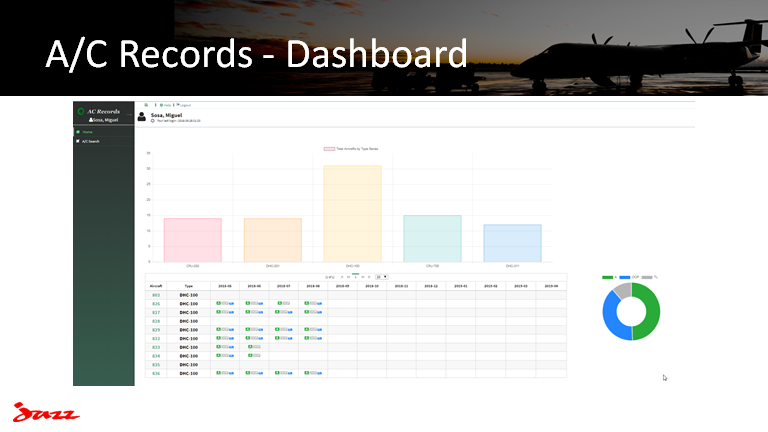
Figure 3.1
Next; here is an idea of how the process is going to work (figure 3.2). Currently engineers sign off task cards and non-routines using the mobile app on their device. The data goes into the main system where a certified PDF is produced, but there is also the rich data available and approval for the electronic sign-off.
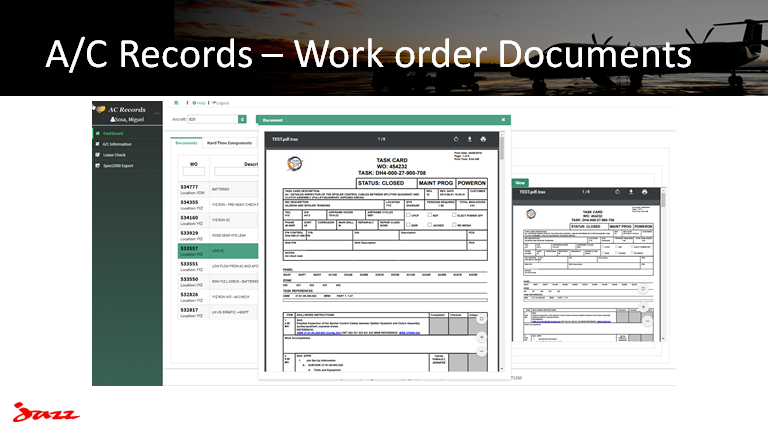
Figure 3.2
When that electronic sign-off happens, that Part Certification, which is scanned up to the part, is issued to the mobile device and added to that certified PDF. So now there are all the pieces to return to the lessor. The task card has been signed off and the Part-Cert is right there. In the system it’s possible to go from a work order to a task card to the data and to see all the pieces there. Plus it is also possible to see the exceptions and address those.
ADs and Service Bulletins (figure 3.3) are key parts of any lease return…
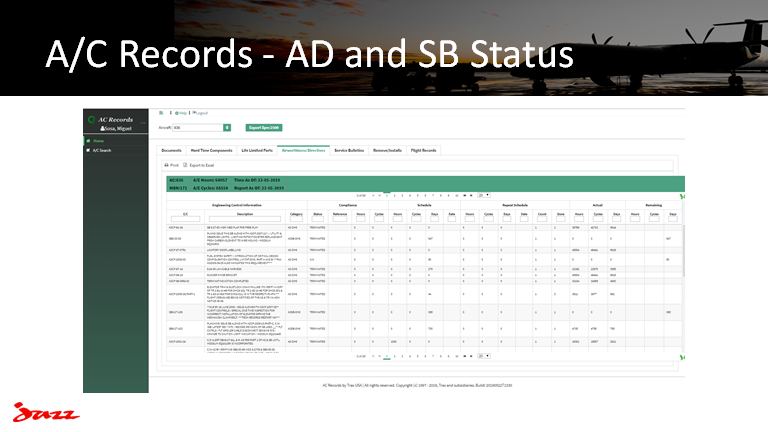
Figure 3.3
… and this dashboard has the same functionality as before with the user able to go to the AD and Service bulletins and see the relevant documentation all in one place.
Hard Time Components and Life Limited Parts dashboard offers the same functionality (figure 3.4).
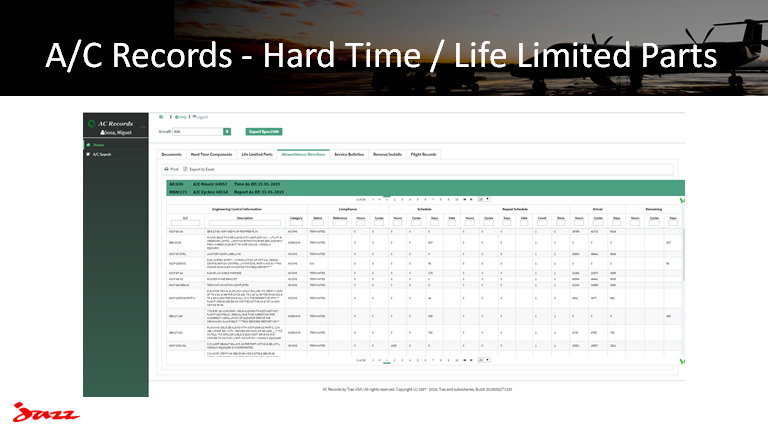
Figure 3.4
All the data is there and users can go in and see the Certifications, all of the Certs or the last ones. All those pieces of data are in the system and in one place where everybody can see it.
Part Transactions (figure 3.5).
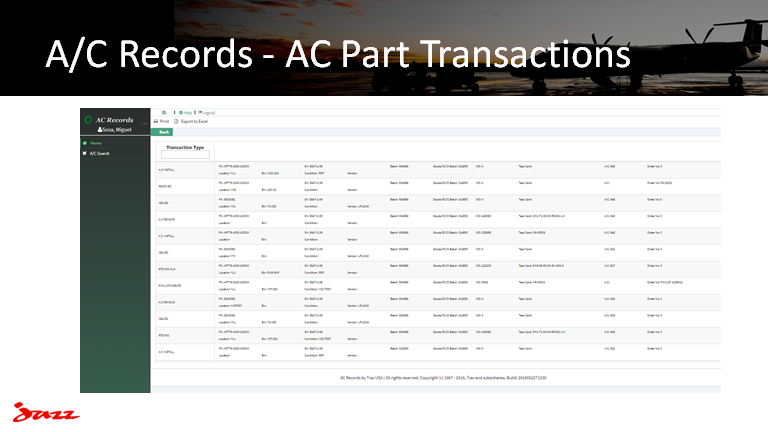
Figure 3.5
The A/C Part Transaction window was added in and would probably have been an Operator view only, i.e. not visible to the lessor, but it was included to help solve some of the issues that were manifesting. It offers a full list of everything that has happened with parts, it is quick and easy to search and, once again, it has that functionality; users can drill down and get all the detailed information from Jazz’s Trax MIS system.
Flight Records (figure 3.6).
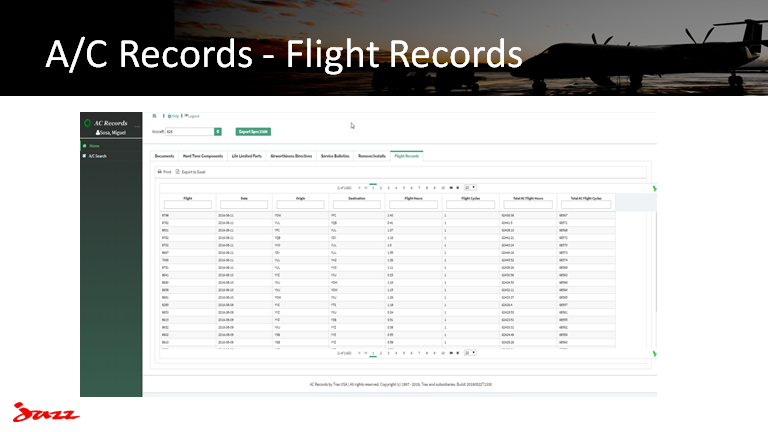
Figure 3.6
Right from the day the aircraft was received into the fleet until the day it is returned: all that data is available.
From the above it can be seen that Jazz organises the data that lessors would be looking for, and probably the most exciting part that wasn’t available with Excel, they also added a full compliance check (figure 3.7)…
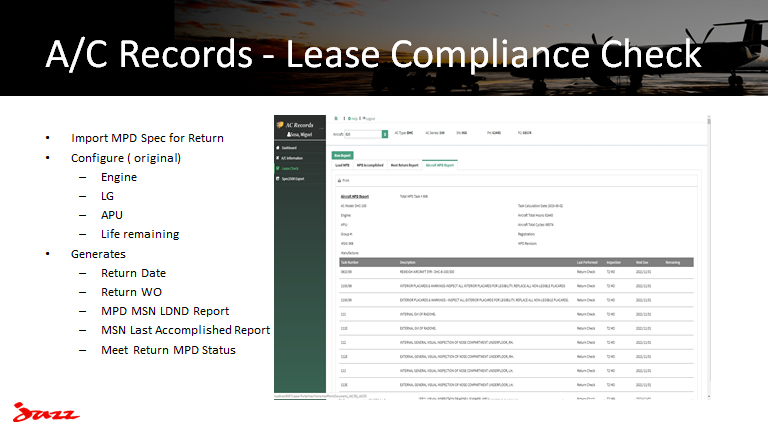
Figure 3.7
… with all those little pieces organized together, it’s possible to quickly manage the lease return, correcting issues real time before the event. With the lessors view they can do there audits…yearly….before the lease return speeding up the process for everyone.
The last part of this solution is the Spec 2000 Export. That is part of what Jazz built here but they wanted to get to the next level. All the lessors say that they will take Spec 2000 but they are not yet ready for it. So that has been built into the system and, at some point, that is how that data is going to be transferred. So there will be those certified PDFs, all the rich data that accompanies those PDFs, and all the details that anybody needs to accept that aircraft.
The process really doesn’t change from figure 2 above, it is just automated (figure 4).
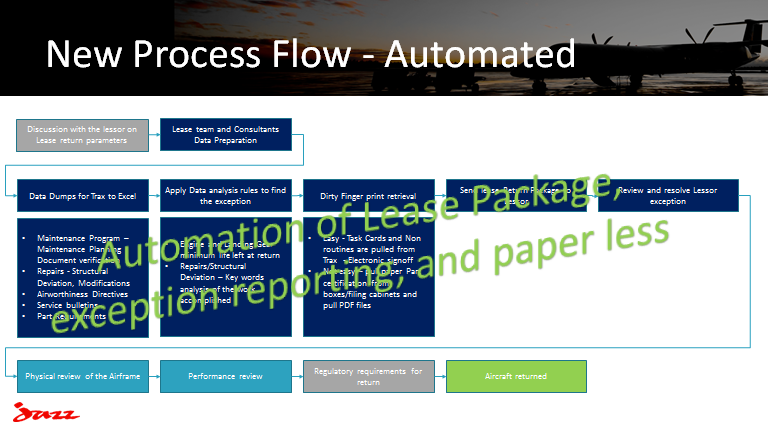
All the pieces have to be done, but when we get to those steps in the process, instead of having to do all the detailed work and make it so that the exceptions can be found, they will already be there, highlighted for resolution. That will be a huge time saver. It will also be useful to explain how Jazz loads the Certifications (figure 5) as part of this process.
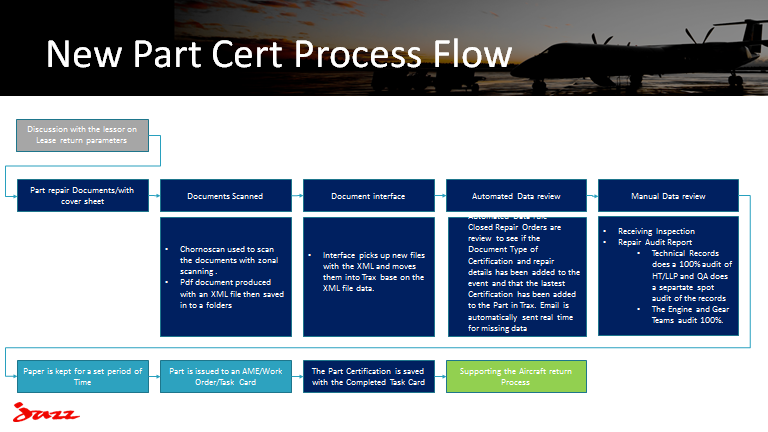
Figure 5
The Certs come into the stores department where the part is received and where they use zone scanning software to scan the part in, then take those documents and put them into the MRO system exactly where they are needed. There is also an option with the mobile device that if there is a single page Cert it can just be scanned and brought into that receiving process. The Part Certs become certified wrapped PDF’s in Trax and become integrated with the Aircraft/part records. Having this detail in the system, connected to all of the supporting data avoids the whole process of collection all of the paper certs and organizing them manually (No more multiple calls and rooting though boxes to find the certs). Now the scanning process is being done and everybody can see them and the data is in the system easily. Jazz is still keeping paper for a while until, probably, mid-2020 and we will probably keep Certs for perhaps three months until everybody is comfortable, and then they won’t be kept at all.
CHANGE MANAGEMENT
As with any of Jazz’s projects, there can be a great set-up, a perfect system but if there is not employee engagement, it will go nowhere. Jazz spends a lot of time on the shop floor making sure that projects are successful, getting feedback, running ‘Lunch and Learn’ events, checking several times a day to make sure that end users are not having problems. And that is done by the whole team: IT, Business Unit experts and whoever is needed to make sure that the project succeeds. There are trainers deployed which adapt their training as issues arise. In fact, this engagement and change management probably accounts for 25 percent of any Jazz Airlines project. Change management is one reason that this project has taken two years after the lessors first declared that they wanted everything electronic, but it is worth the time to get such an important project to work.
BENEFITS
Having implemented the new process, Jazz and Trax undertook a review of the application and, out of that review, were able to identify some clear benefits.
- Aircraft Lease Agreement – No DFP requirement;
- Records Inventory – Reduced paper records (One year of Log books still required);
- Records review – Digital in Trax A/C records portal;
- Discrepancy resolution – performed prior to Lessor review;
- Prepare final records – reports and DFP in Trax A/C records portal;
- Present to Lessor – provide customer access to Trax A/C records portal;
- Final aircraft delivery – signed reports (PDF) printed from Trax A/C records portal.
Having created that record we were very pleased to note the progress that had been made. In one sense, this is another ‘rinse and repeat’ case: we’ve seen it before, it is an easy one.
SAVINGS
This is what everybody wants to know; how much has been saved? Jazz expects to see a 60% to 80% saving on the whole process and that works out to about $100,000 per aircraft in savings. Not only will Jazz save but it will be able to provide better documents to the lessors so that they also can save costs.
- Consultant cost – 60% reduction due to digital records, better audit functions and prior organization;
- Logistics cost – 80% reduced space requirement due to offsite lease return activity;
- Cost of human errors and additional workload – 80% reduction due to better visibility of records exceptions in Trax A/C records portal and nil paper records;
- Additional maintenance and last minute part replacement cost – target at or below 1% additional maintenance and part replacement cost due to better visibility of records exceptions in Trax A/C records portal;
- Cost of additional documents request from vendors – Part certs, BTB trace, AMOC, etc.;
- Aircraft records storage cost – 100% reduction in offsite storage cost.
Notwithstanding the above, the big savings, the real savings are in the manpower. For instance, from having previously had three consultants working on lease returns, the airline will be going down to one. But that isn’t all; there are also the people from the Business Units who have to be diverted to assisting on lease returns. Then the automation that can be done to remove tasks that no longer need to be done. Jazz is now looking at the next lease return and that will be used to identify all the holes that will have to be filled. Also, Jazz is already fifty percent electronic, but for airlines that are currently all paper, the savings will be even greater. We can look at the paper process with task cards and non-routines and that alone amounted to $500,000 a year in savings.
Of course, different leasing companies have
different requirements and it can even be the case that different aircraft from
the same leasing company might be subject to different conditions. But all of
those variations can be built into the system as it applies to each unit. And
hopefully, when increasing numbers of operators are using these types of tools,
any changes by leasing companies will be quickly understood by all of their
lessees. So that is a brief look at how Jazz Airlines has implemented digital
lease returns and all the values that have flowed from this great program.
Contributor’s Details
John Hensel
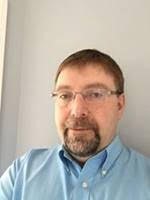
John has worked at Jazz Aviation for over 25 years in Aircraft MTC, Process Improvement/Sigma, and his current position as Director Business Systems Integration. He has worked with Line/Heavy MTC, Manager of Reliability, Manager of CRJ Fleet Management, Manager of MTC Planning, and Manager of MTC Control. He also has overall responsibility for IT systems for the Aircraft Maintenance division.
Jazz Aviation
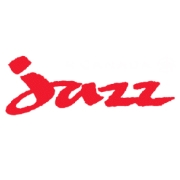
Jazz is a Canadian regional airline with 4,500 employees and a fleet of 116 Bombardier aircraft of various types serving 81 destinations in Canada and the United States. The airline operates approximately 700 Daily Flights carrying 30,000 passengers each day. Over 11.1 million passengers were carried in 2018.
TRAX
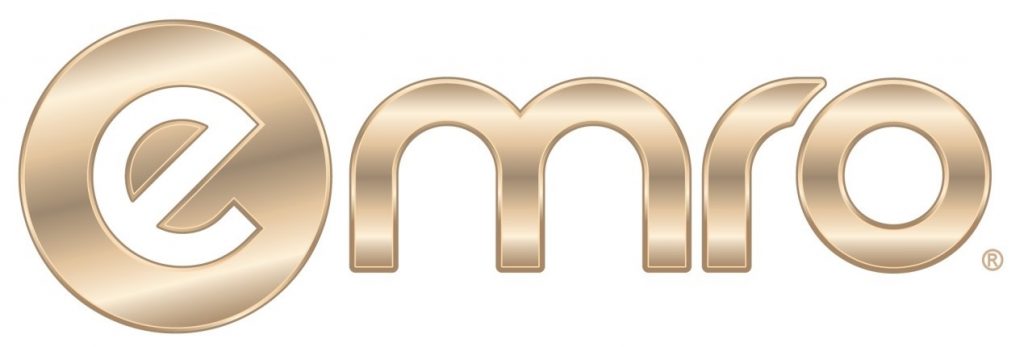
TRAX provides comprehensive software solutions designed to cater to all aspect of aircraft maintenance management. With over 170 customers, TRAX is a global provider of aviation maintenance mobile and cloud products. The eMRO and eMobility products support digital signatures, paperless Workpacks and manuals, RFID-capability for logistics, Biometric security, offline capability for mobile apps, web-based applications and the ability for users to work anywhere with easy access to real-time information.
Comments (0)
There are currently no comments about this article.
To post a comment, please login or subscribe.